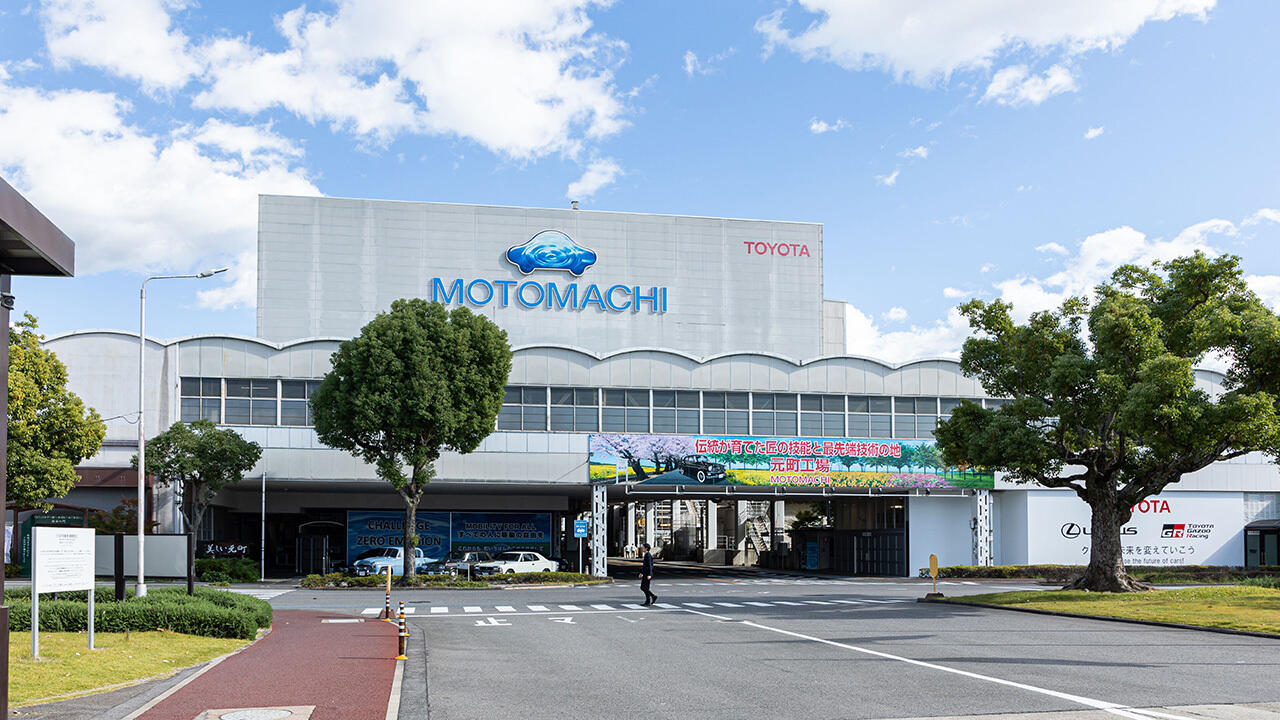
Toyota's Motomachi Plant is embracing an age of diversity by fostering diverse talent. Not satisfied with merely adapting, the plant has set out to be a driver of change.
Skills drive change in monozukuri
The Motomachi Plant is committed to its human-centered multi-pathway approach.
Plant General Manager Miyabe
There is no single method that will allow us to continue producing safe, high-quality, attractive cars forever. We are constantly battling against change,” says General Manager Miyabe. “Simply being able to adapt to change is not enough—we should be able to create change ourselves. The genba that knows the cars and processes so well must continue to be a driver of change.
To see how Motomachi is working to “create change,” let’s look at some of the genba efforts opening up new possibilities in various fields.
In 2022, the TOYOTA GAZOO Racing World Rally Team’s Kalle Rovanperä became, at the age of 22 years and one day, the youngest-ever driver to claim the FIA World Rally Championship (WRC) title.

As a sign of Morizo’s appreciation, and a way to create more excitement around TGR’s WRC efforts, the GR Yaris Kalle Rovanperä Edition was released in a limited run of 100, featuring a three-color body in black, white, and red.
Surprising as it may seem, this coloring is achieved entirely with paint, not decals.
It is the handiwork of the Motomachi Plant’s painting team. First, the entire body is painted white, then masked using stencils so as to leave out the red sections, which are then painted. The elaborate process is finished off by applying the black paint in the same way.
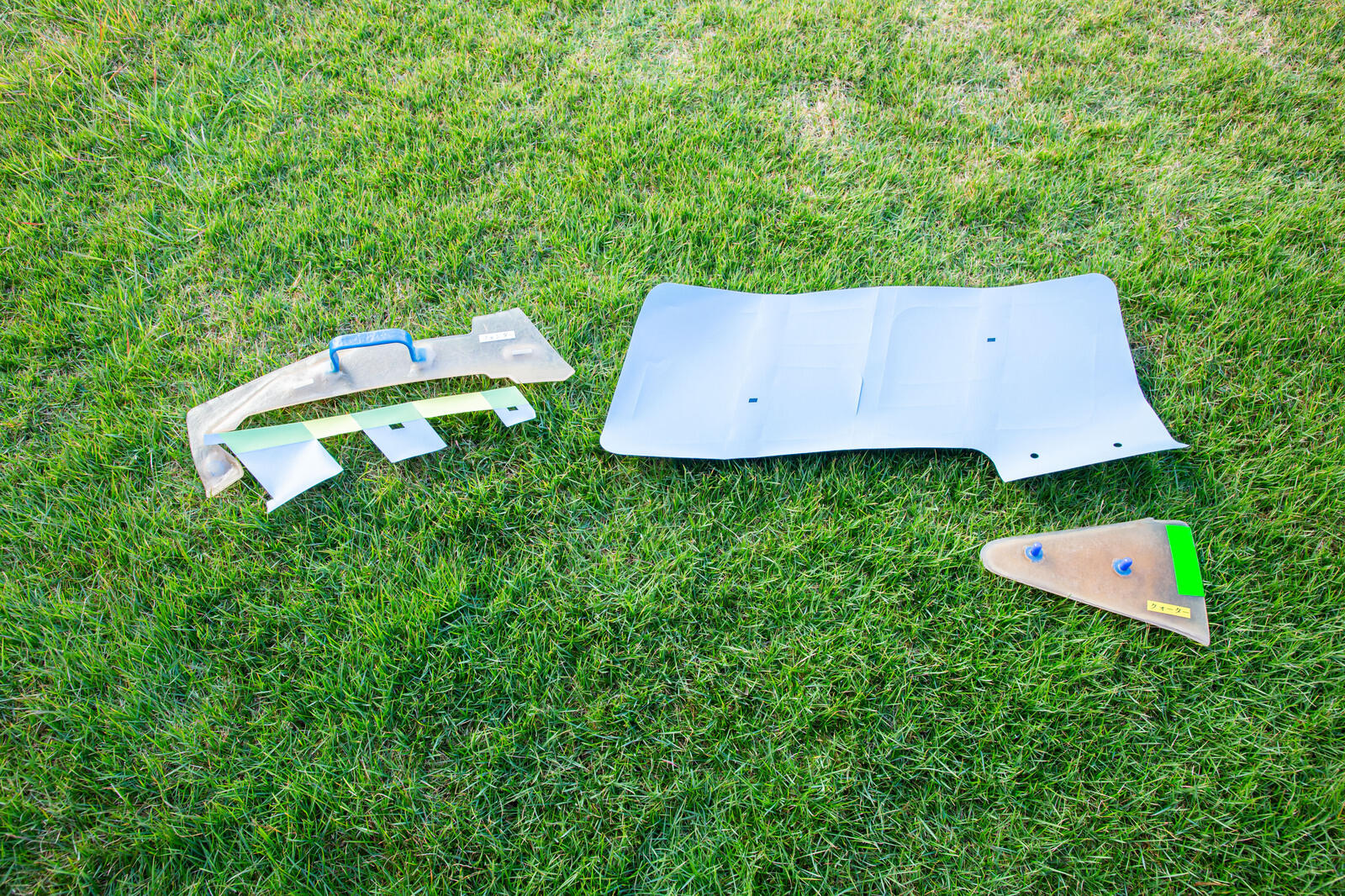
To complicate matters further, body panels and bumpers were painted separately before being assembled, which meant that these steps had to be closely coordinated and adjusted to the millimeter to avoid misalignment.
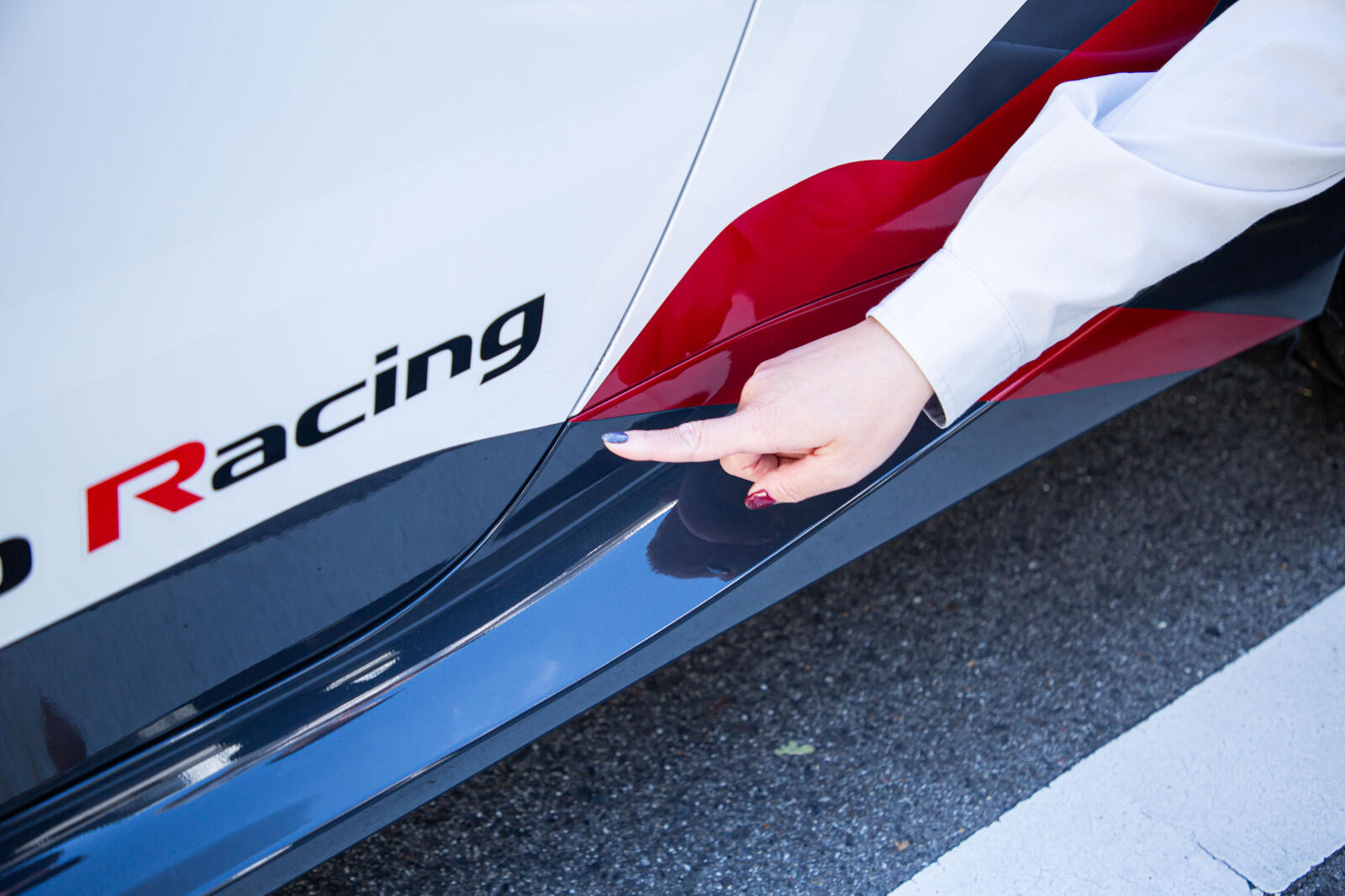
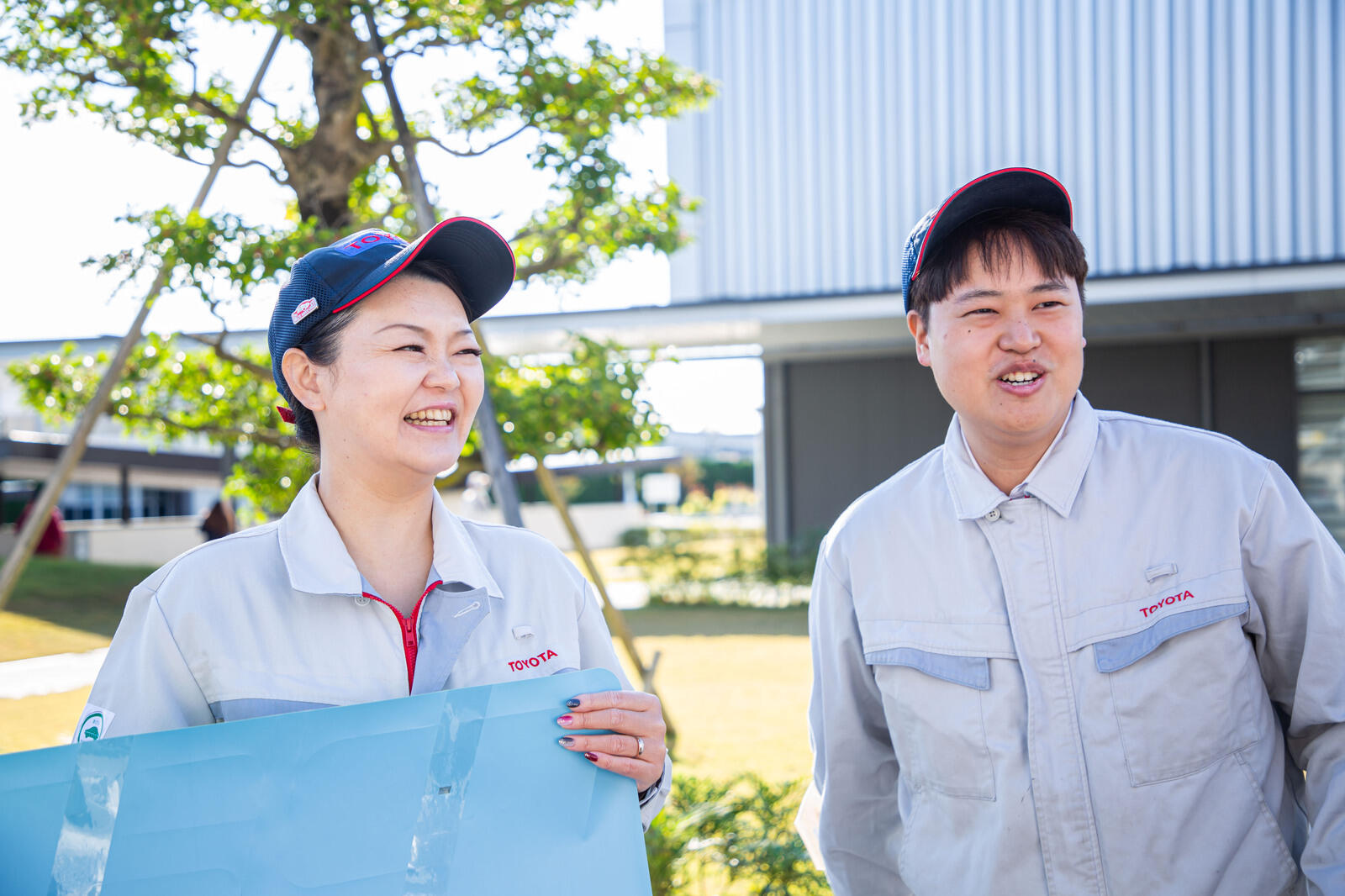
This sophisticated paint job was made possible by expertise and skills built up at the Motomachi Plant in the course of producing police cars and two-tone finishes for passenger cars.
Having tested their skills in uncharted territory, the two team members we spoke to were brimming with confidence for further challenges.
The pursuit of change is also being taken up by Motomachi’s welders, as profiled in our previous article. They too are venturing into a new frontier, moving from steel to aluminum.
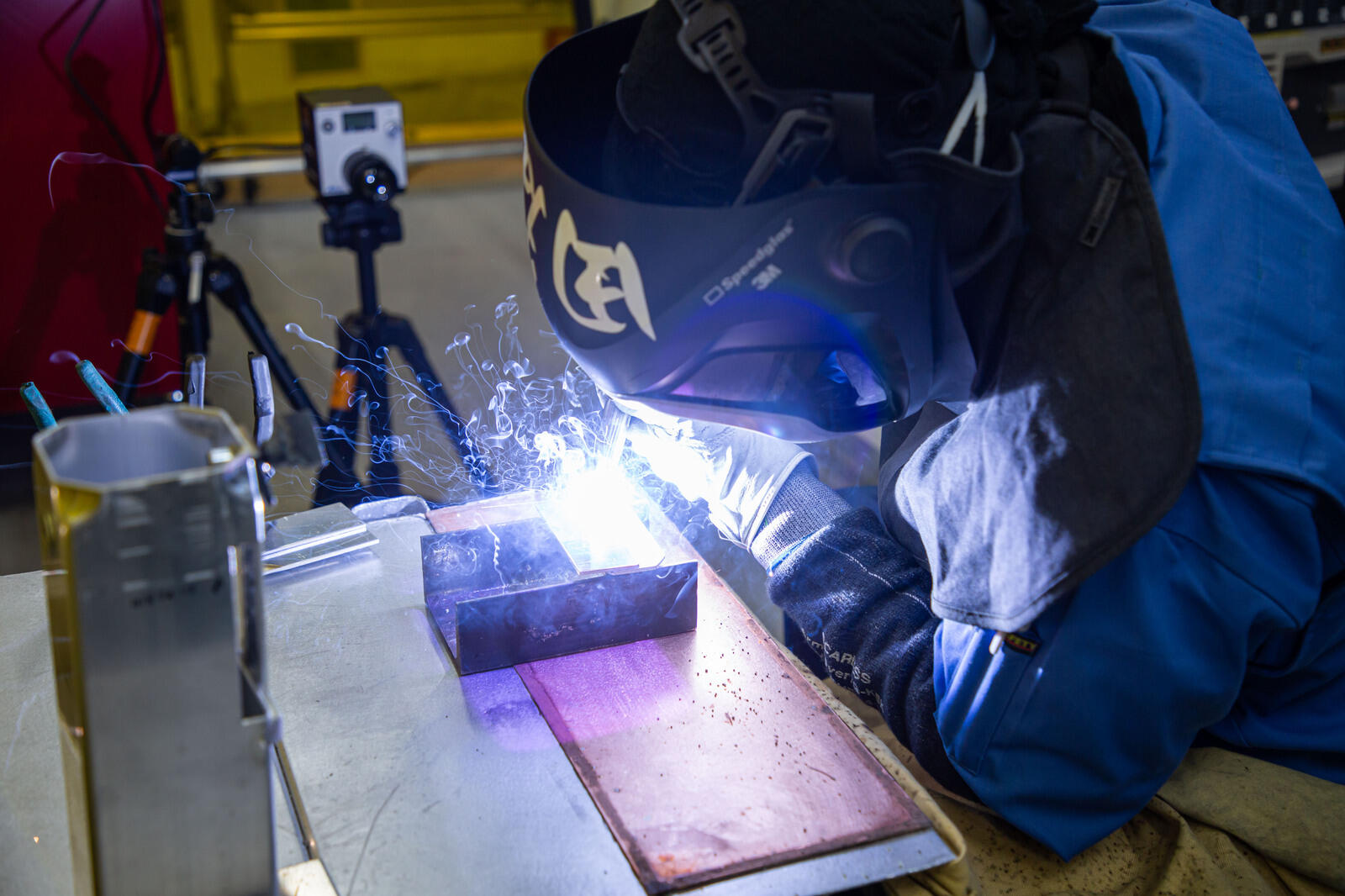
Lightweight and rust-resistant aluminum has become widely used for hoods, doors, and other automotive parts, but it is regarded as a difficult metal to weld.
For instance, to overcome aluminum’s tendency to form an oxide layer that interferes with welding, a right-handed technician must move the welding machine from right to left as they work.
However, this puts the welding area in a blind spot, obscured by the hands or welding machine.
Yasunobu Takasaki, Chief Expert, Carbon Section, Body Manufacturing Division
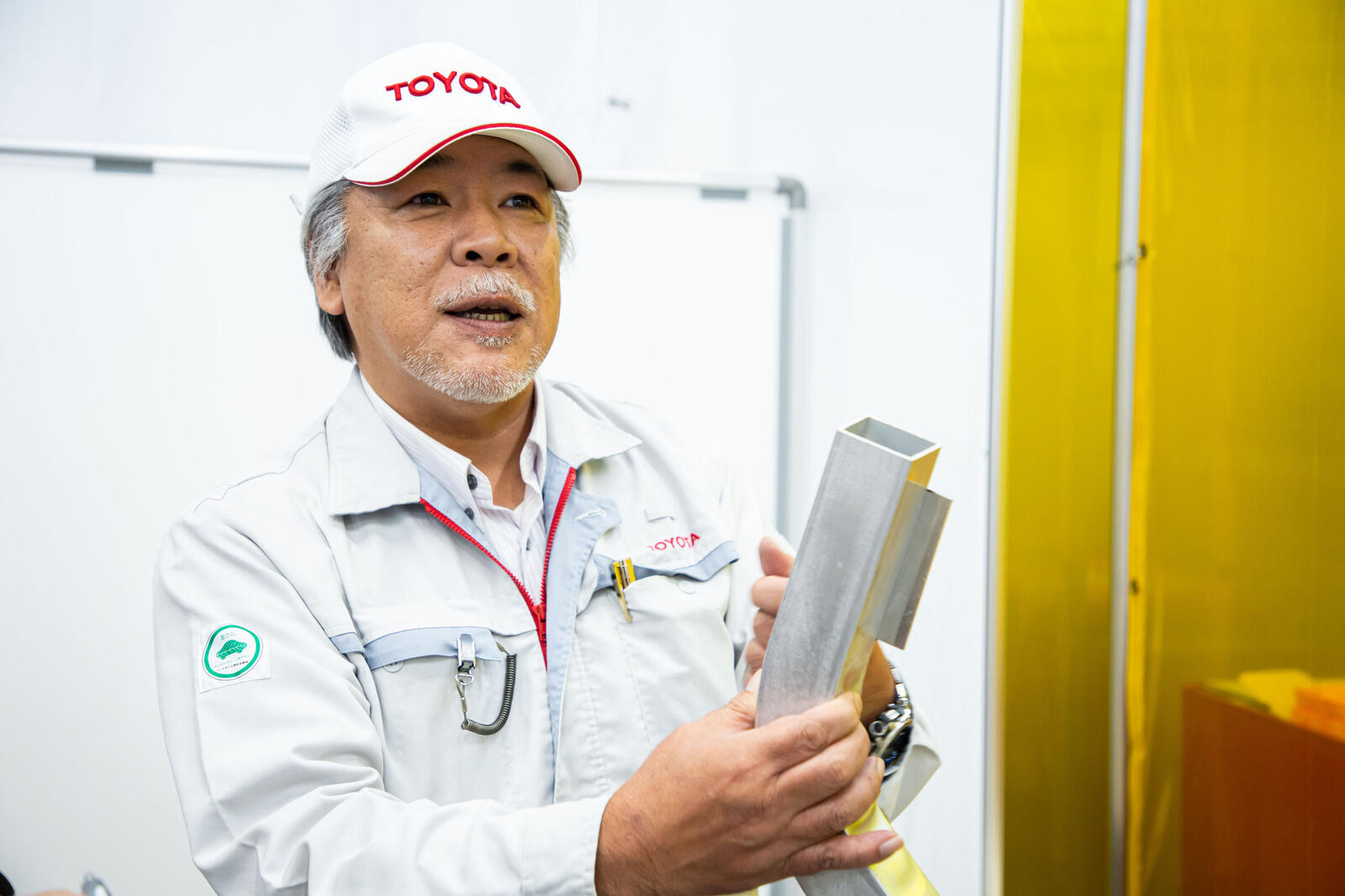
A major difference from steel is that with aluminum, the bead is hard to see until the job is finished. Creating a good weld without being able to visually check the finish relies on feel and intuition.
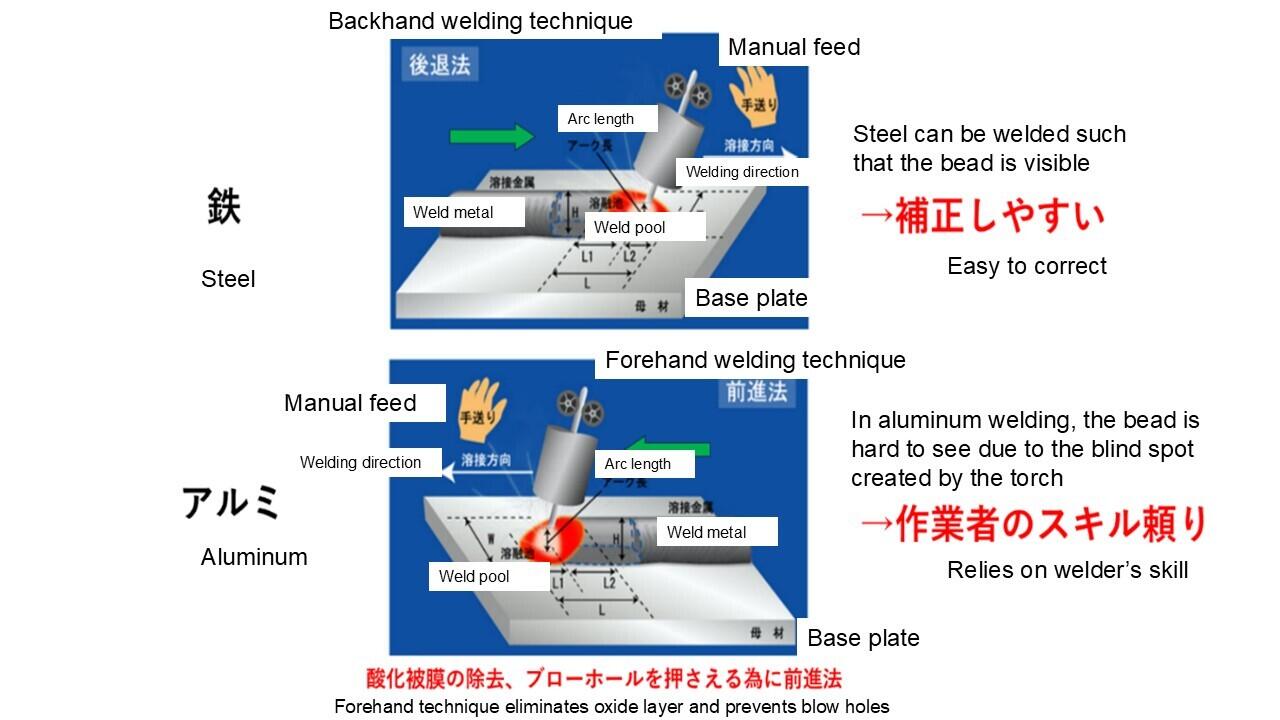
Motion capture is proving useful in learning the necessary skills.
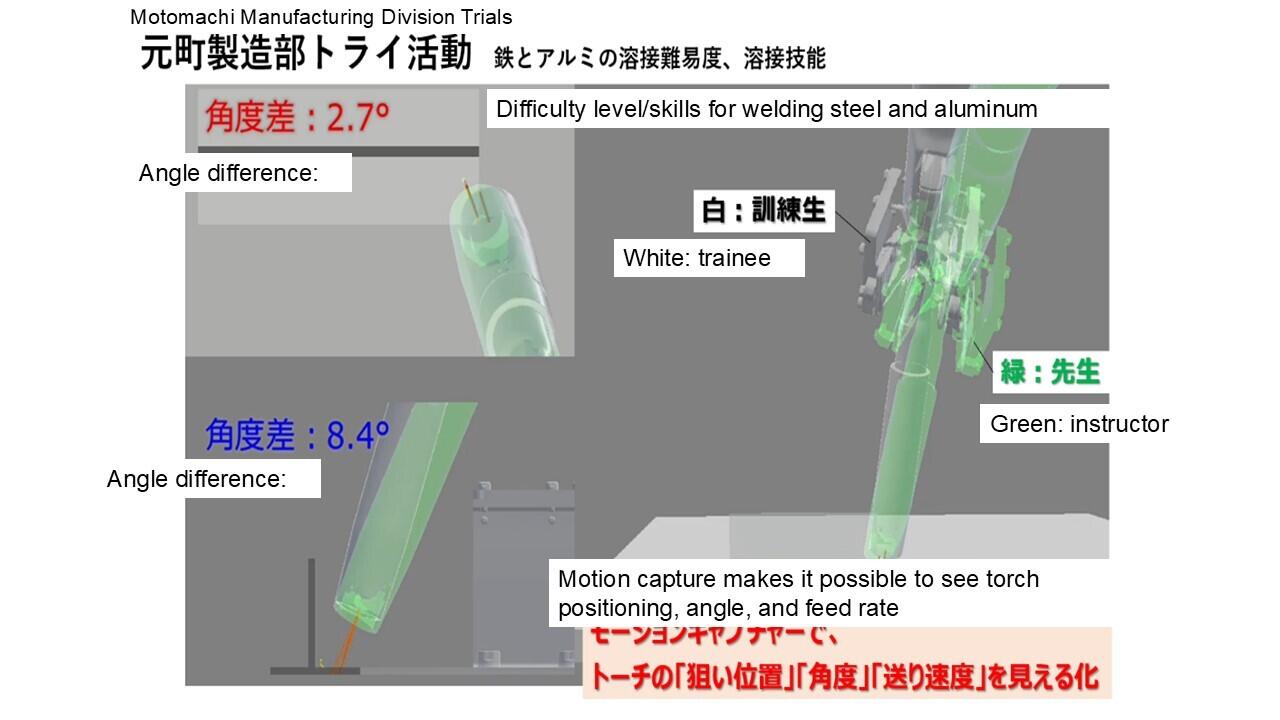
Welds performed by both instructor and student are filmed and reproduced in three dimensions, allowing them to visually verify subtle differences in movement, such as angle and positioning.
This approach has cut the required training time from four months to two. Whereas previously the only way was to compare the differences between finished pieces, digital technology has powered an evolution in how skills are acquired.
The Motomachi Plant’s determination to drive change can also be seen in the area of carbon, which is used in the GR Yaris roof and other parts to reduce weight.
Light and strong carbon parts are made by cutting sheets consisting of 3,000 to 12,000 interwoven carbon fibers with a carbide blade, manually affixing them to a mold in the required thickness and curing with resin.
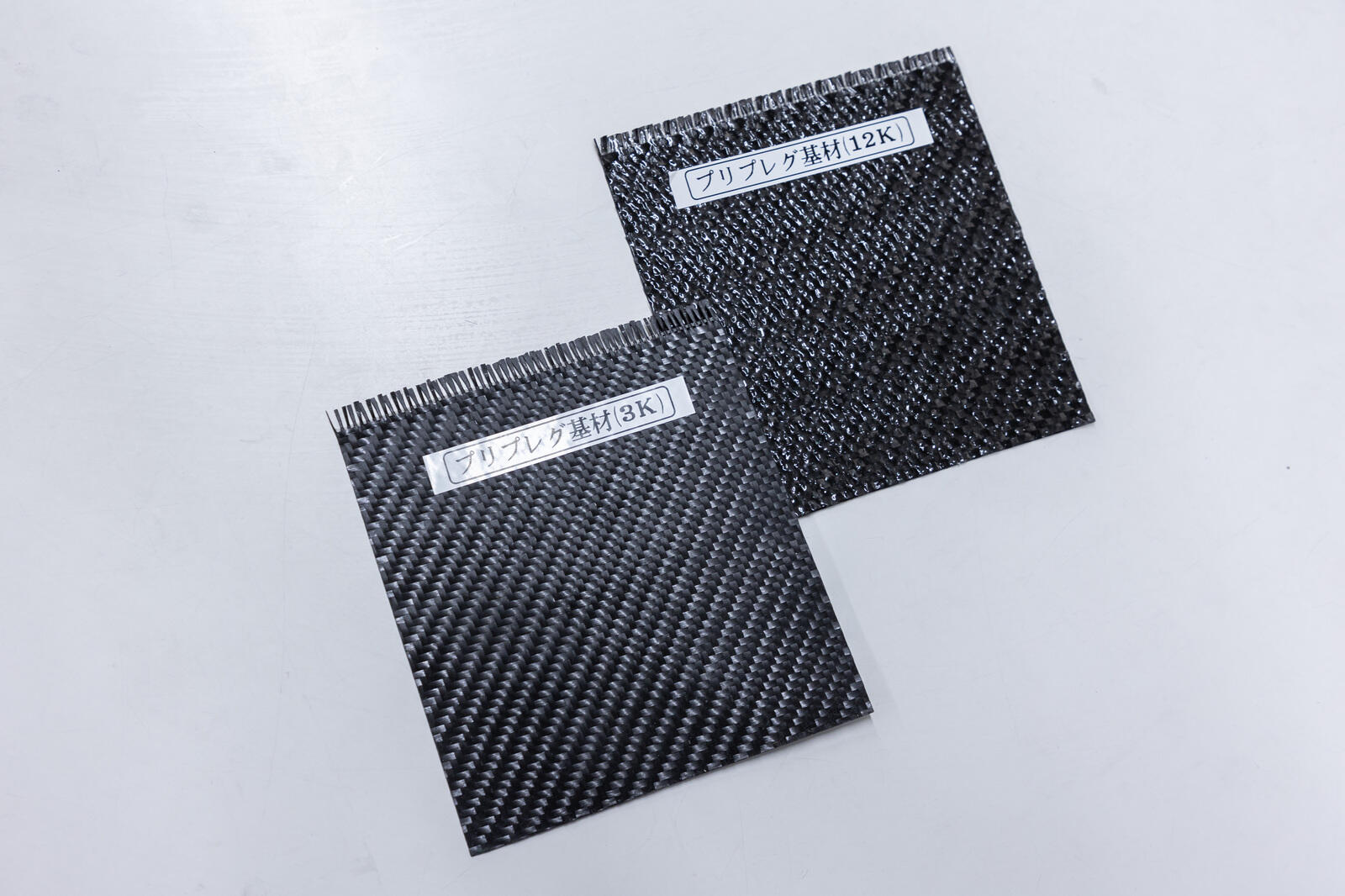
As part of the process, sheets impregnated with resin are affixed to complex molds. Since human hands are able to handle depths and fine indentations that cannot be reached by machines, this artisan skill has continued to be passed down.
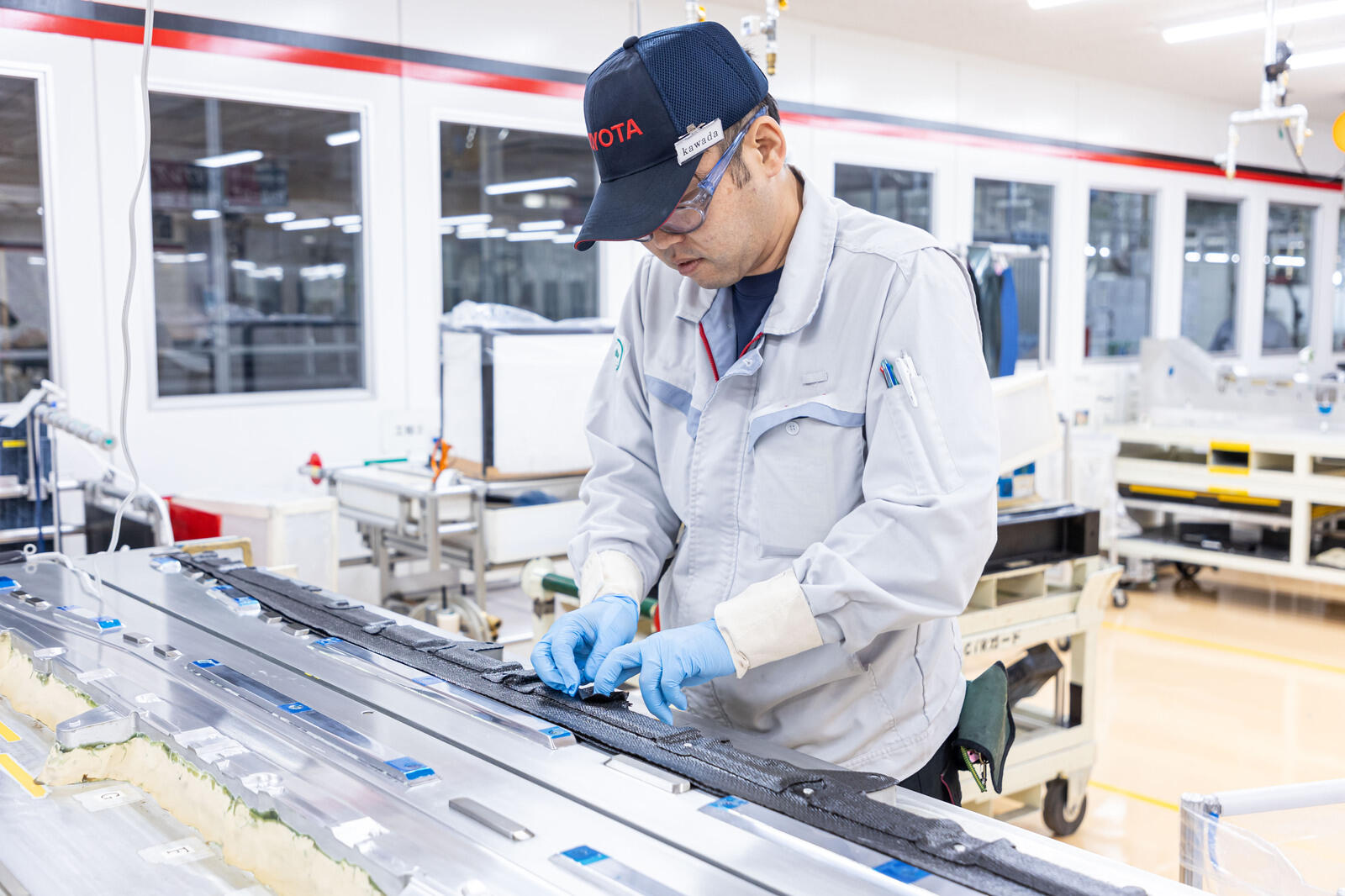
Motomachi is the only Toyota plant that employs carbon in exterior parts. In addition to cars, such parts are also used in racing wheelchairs, boats, and other products.
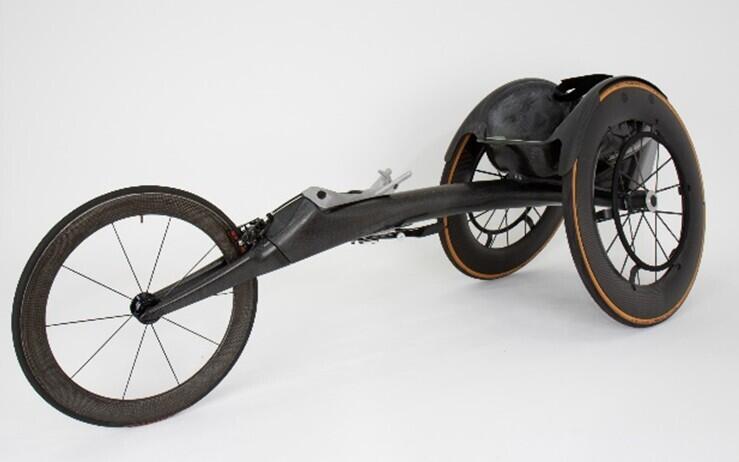
Toyota is working to reduce the material’s weight even further to make it suitable for various mobility applications. To drive this evolution, the company is incorporating complex techniques, such as inserting bags inside the mold once the sheets are in place, then inflating them to create hollow items. The challenge to expand the potential of mobility continues.
Takashi Hirata, Manager, Exterior Parts Engineering Department, Surface Finishing & Plastics Manufacturing Engineering Division, Takaoka Plant, Carbon Parts Group
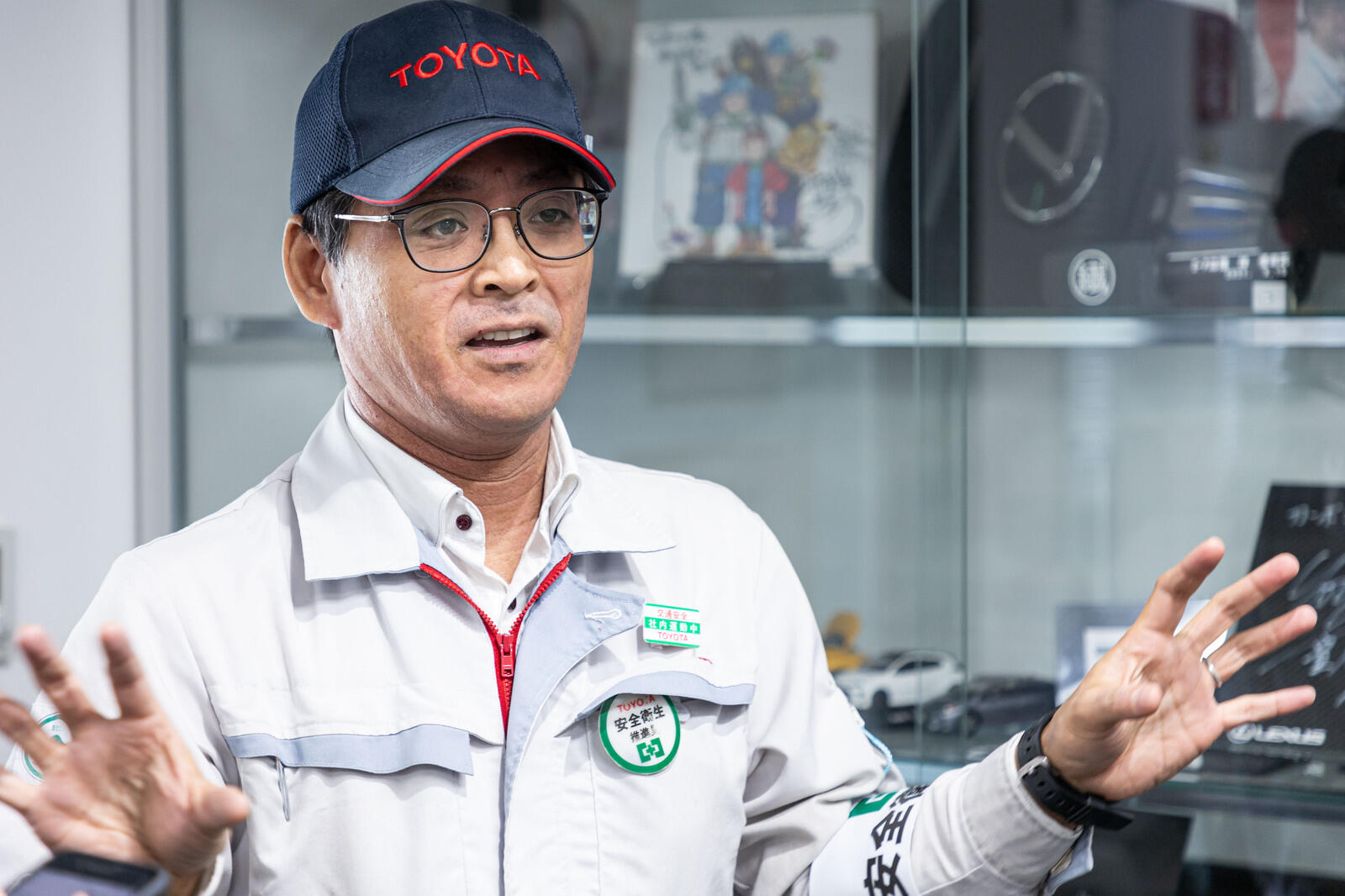
Carbon fiber was developed in Japan. However, we have very few companies mass-producing it, and an incredibly small number engaged in downstream processes. If we throw in the towel here, Japan will lose its technological advantage, so we are doing this out of a determination to protect Japanese monozukuri.
Technology drives change in decarbonization
In keeping with the philosophy of the Toyota Production System, the company’s genba workers constantly strive to shorten lead times and achieve cost reductions through innovation and ingenuity.
While adapting to the electrification shift, Motomachi is also seeking to drive change by overhauling existing work practices and organizational structures.
Shinji Asano, Manager, Machinery Maintenance Section, Machining Division
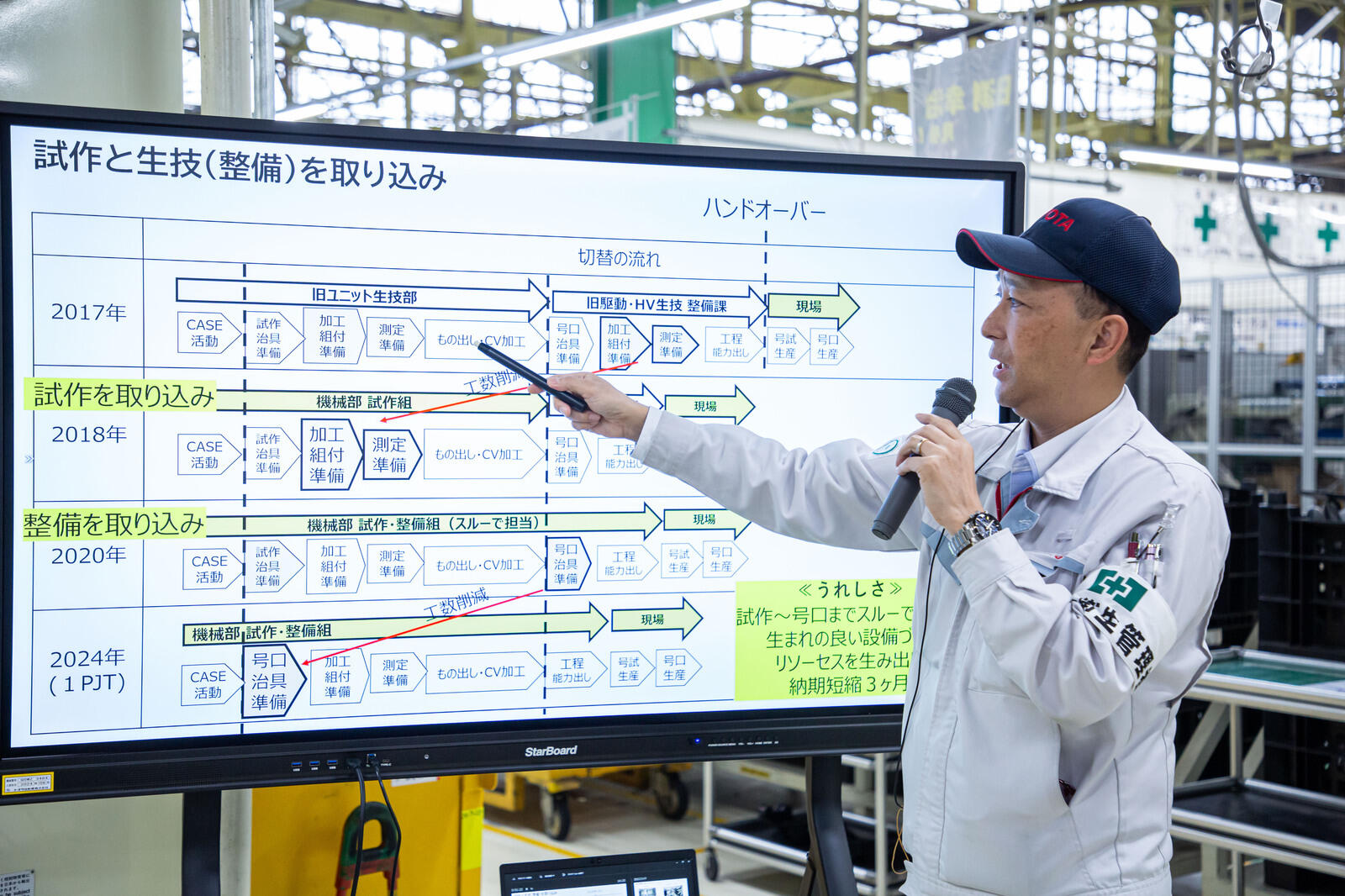
In the past, the production of suspension components was divided up, with the Prototype Division handling the product development stage, Manufacturing Engineering planning the production line process, and Machining taking over once the mass-production line was set up. Since 2018, however, prototyping has been incorporated into the Machining Division, which has also received around twenty employees from Manufacturing Engineering. The structure has been transformed so that one unit can consistently handle the entire process, from the prototype stage to mass production.
The expansion of responsibilities has spurred personnel development and efficiency improvements, with the free-up resources being allocated to electrification.
Against this backdrop, in 2022 the Machining Division established a battery pack production line for Toyota’s first genuine BEV. Manager Daien Yamada, who oversees the line, told us about his team’s tireless kaizen efforts.
Daien Yamada, Manager, EV Unit Section, Machining Division
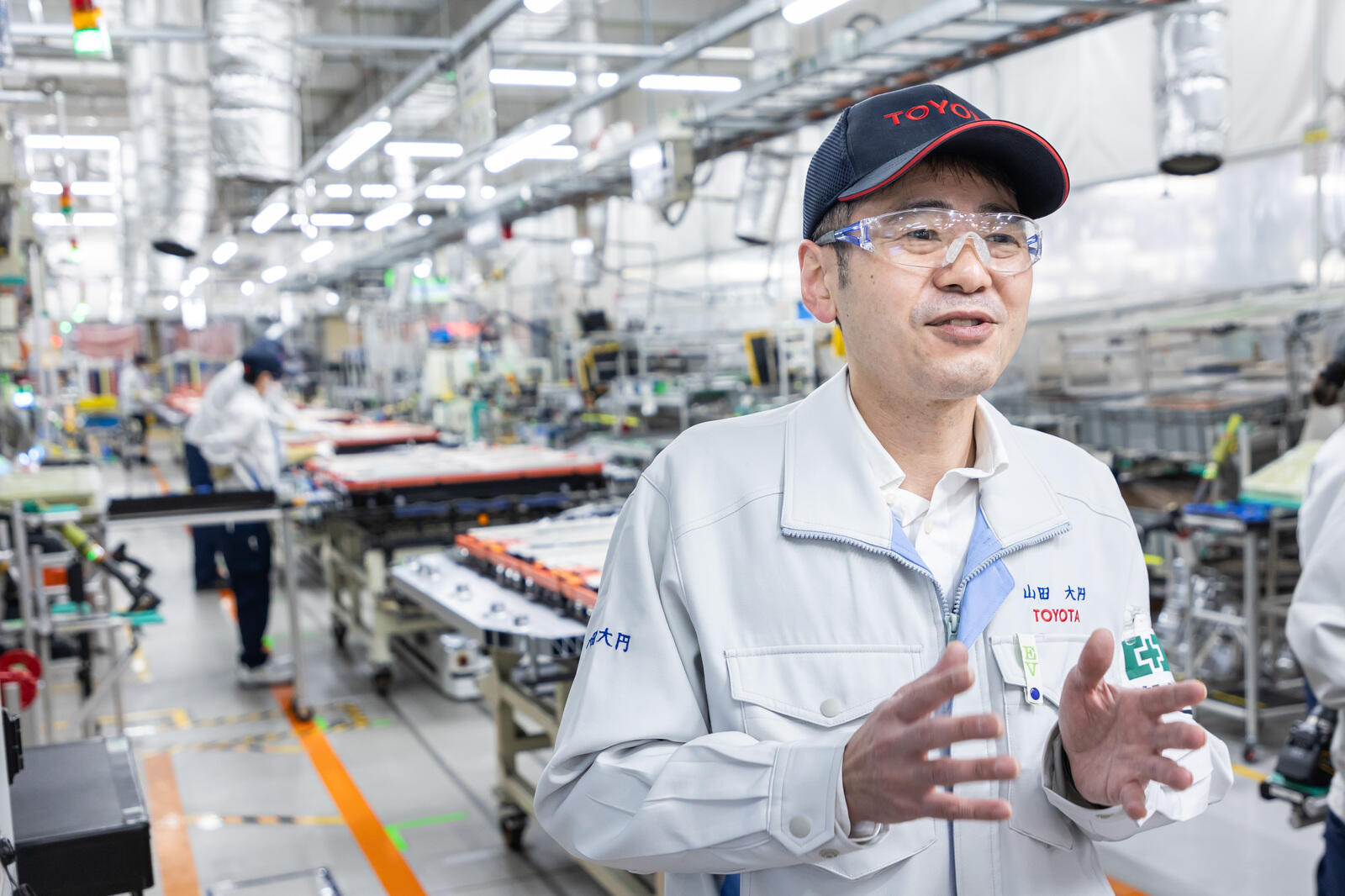
If the connectors linked to the battery are not firmly attached, they can come loose while driving, rendering the car unable to move. This was not easy to pick up in inspections, meaning it might not be remedied before moving on to the next step.
Seeking to put an end to this problem, we devised this inspection jig.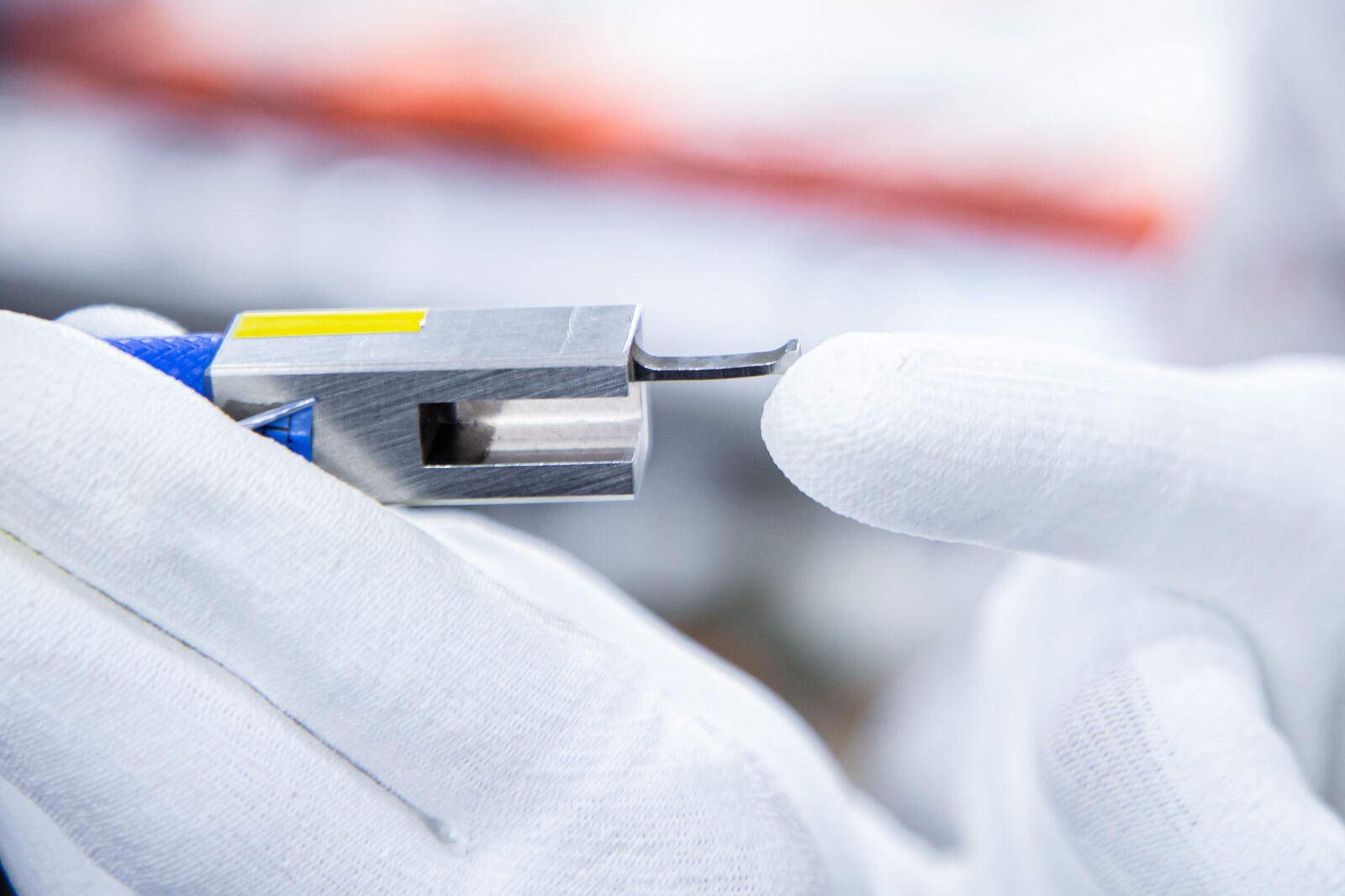
Although the design is incredibly simple, when inserted into a connector that is not properly attached, it will catch and cannot be pulled out.
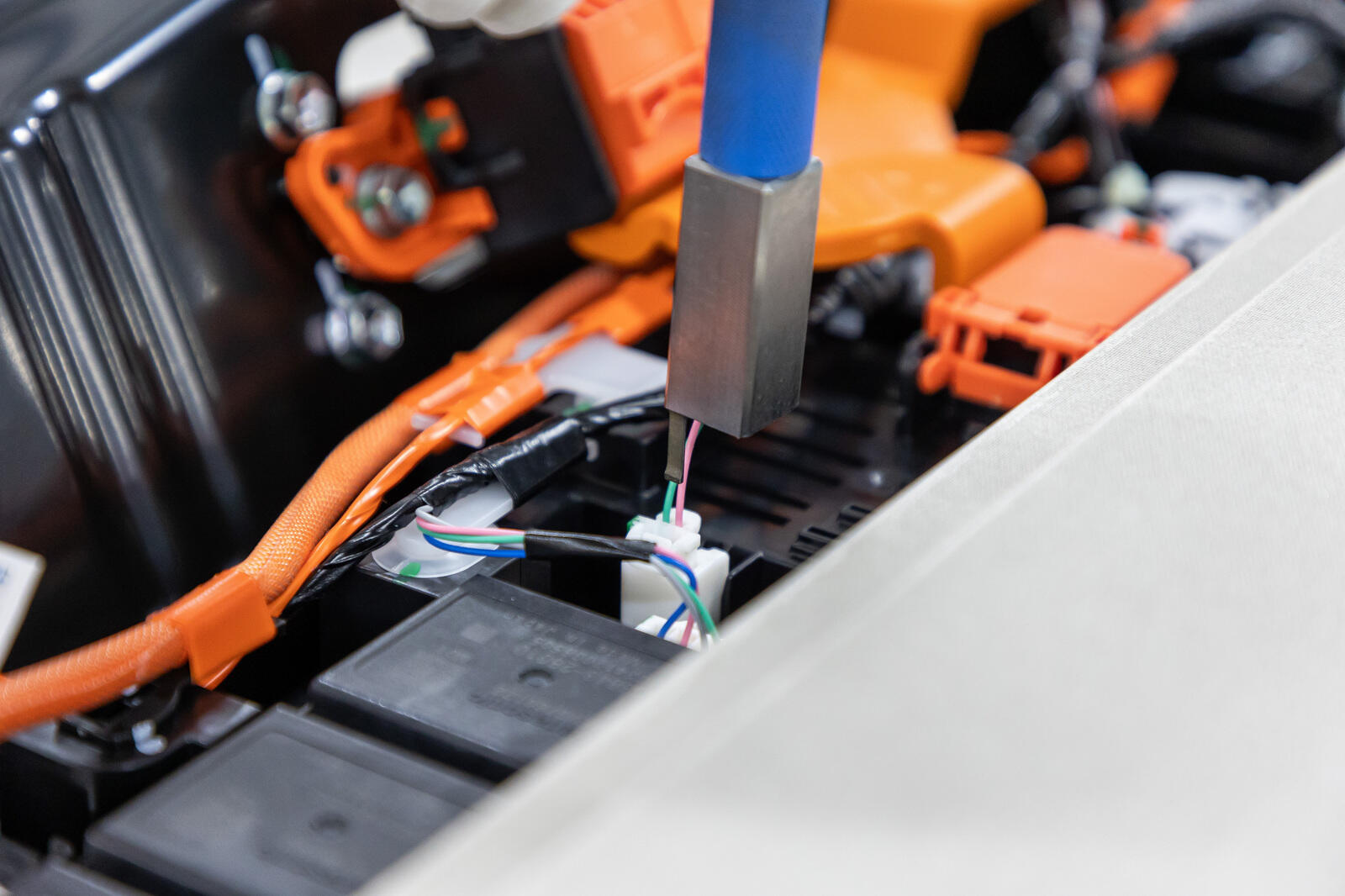
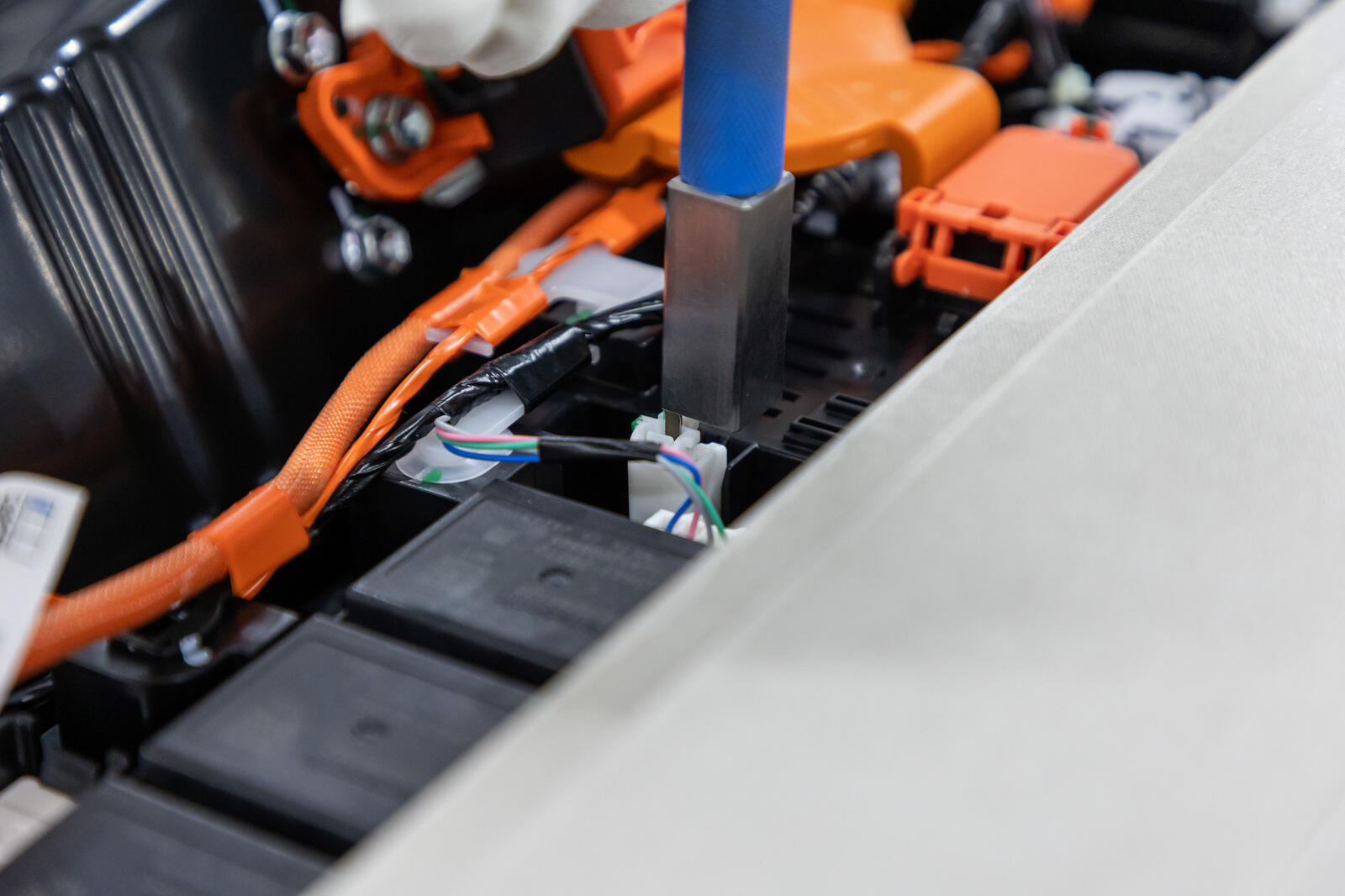
Even when faced with the new challenges of the electrification era, the plant’s operations are underpinned by genba expertise and ingenuity cultivated over many years. Motomachi is creating change by harnessing Toyota’s company-wide monozukuri prowess.
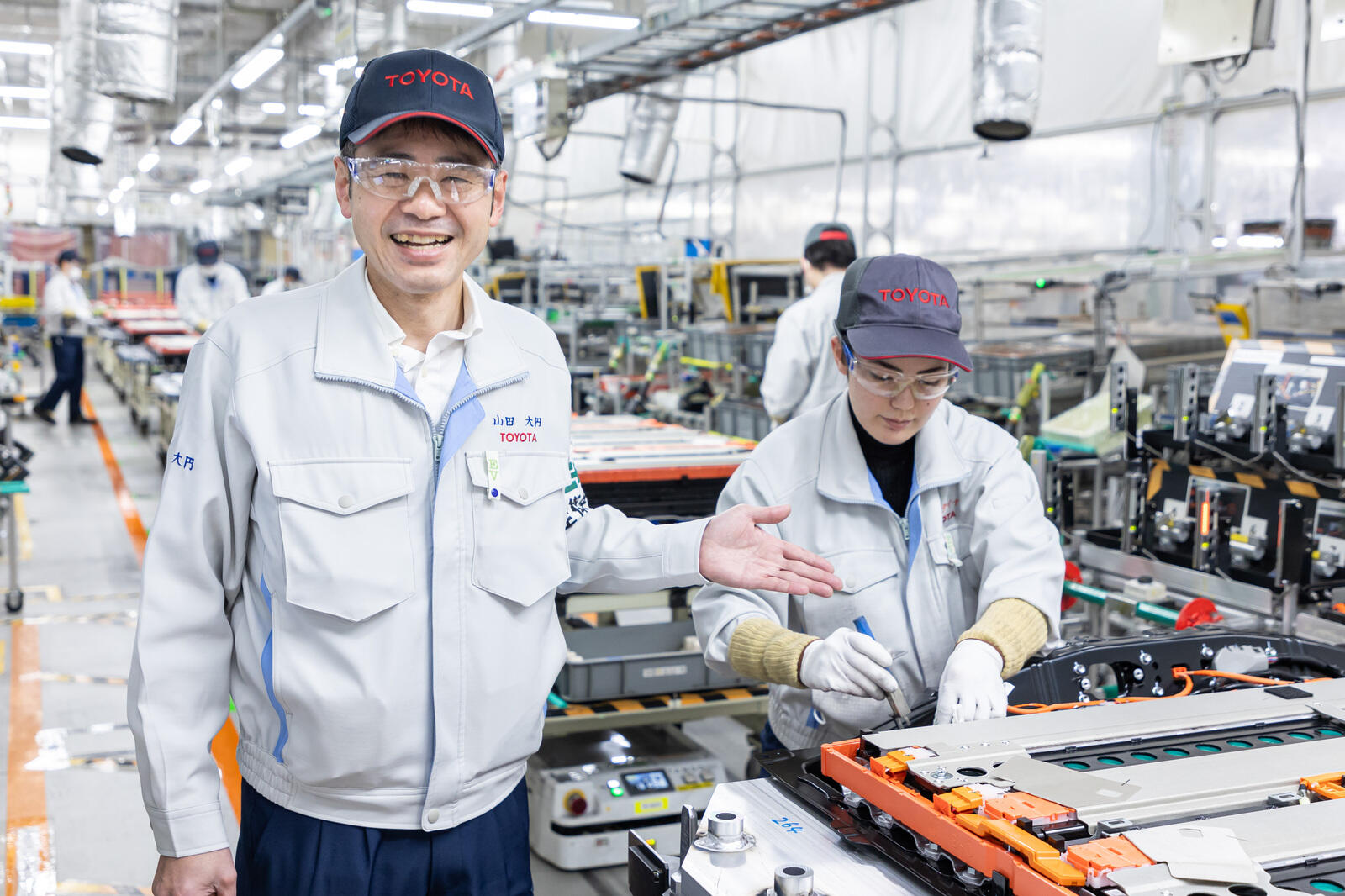
While the efforts showcased so far have been aimed at creating change within the Motomachi Plant, some teams are also taking on the challenge of spreading change to the wider world.
Forklifts are a ubiquitous presence within the plant. In 2016, Motomachi began converting these gasoline-powered machines to fuel cells (FC), and today 167 forklifts—42% of the total—run on hydrogen*.
*In collaboration with Chita City and Toho Gas, the hydrogen used for fuel is produced from biogas-derived city gas.
Other trials using hydrogen are also being conducted in various locations. One example is the drying furnaces that form part of the battery pack line we mentioned earlier.
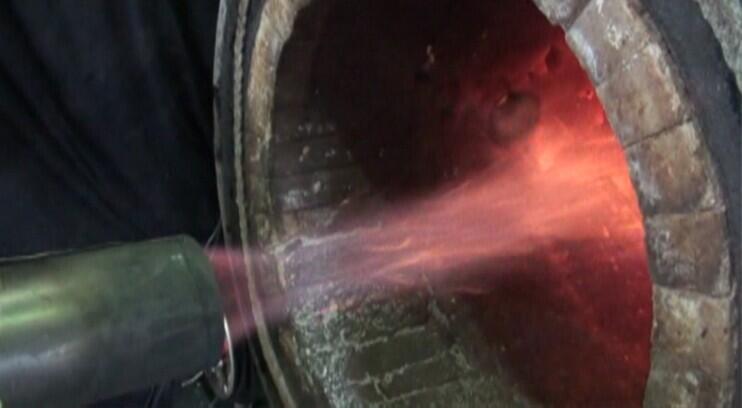
This is the first time that hydrogen has been used as a burner fuel in a mass-production process. This hydrogen is produced through water electrolysis powered by sunlight, with city gas making up any shortfalls in supply. Toyota is exploring ways to establish a stable hydrogen supply, as it works to decarbonize production processes.
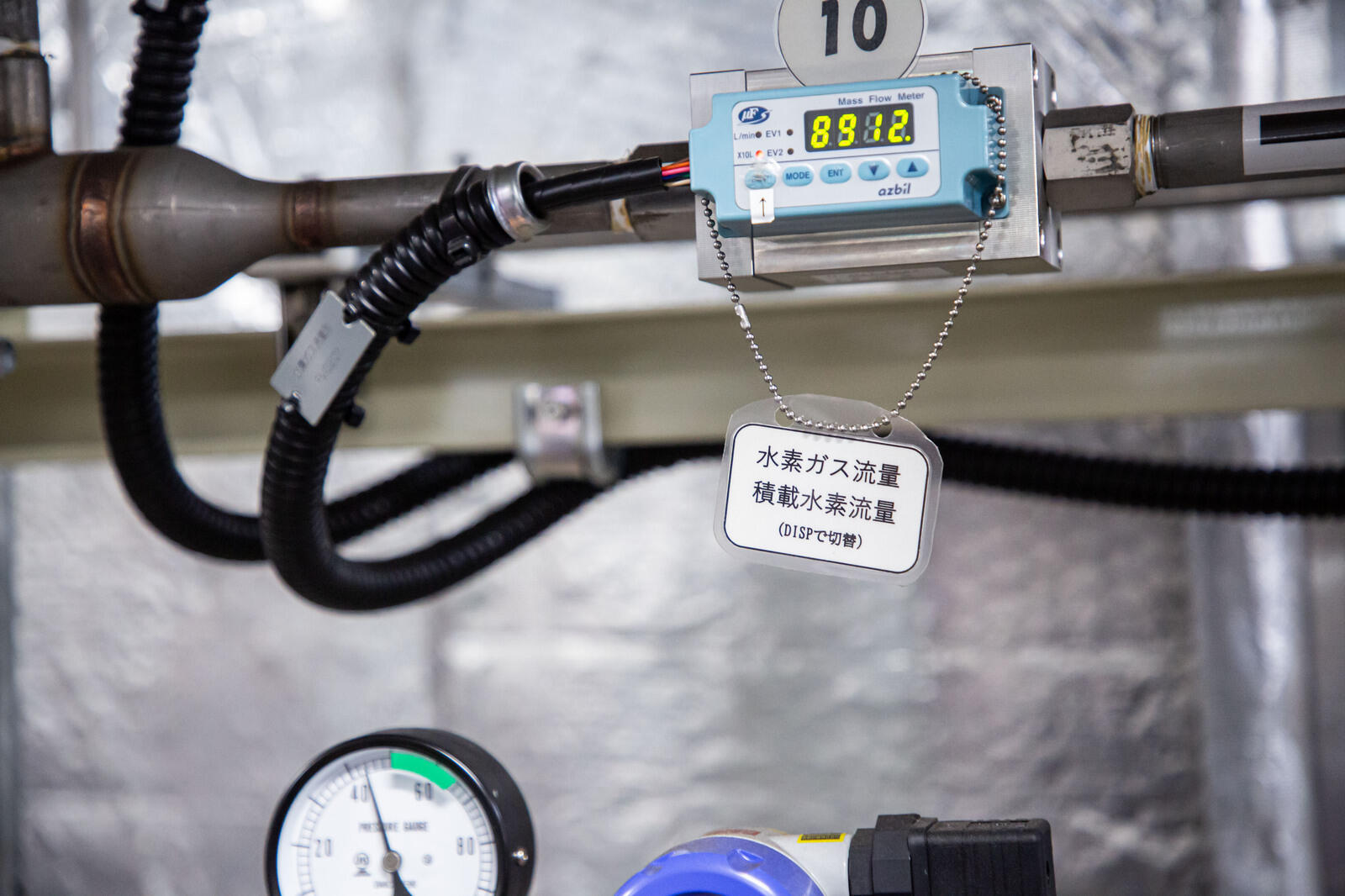
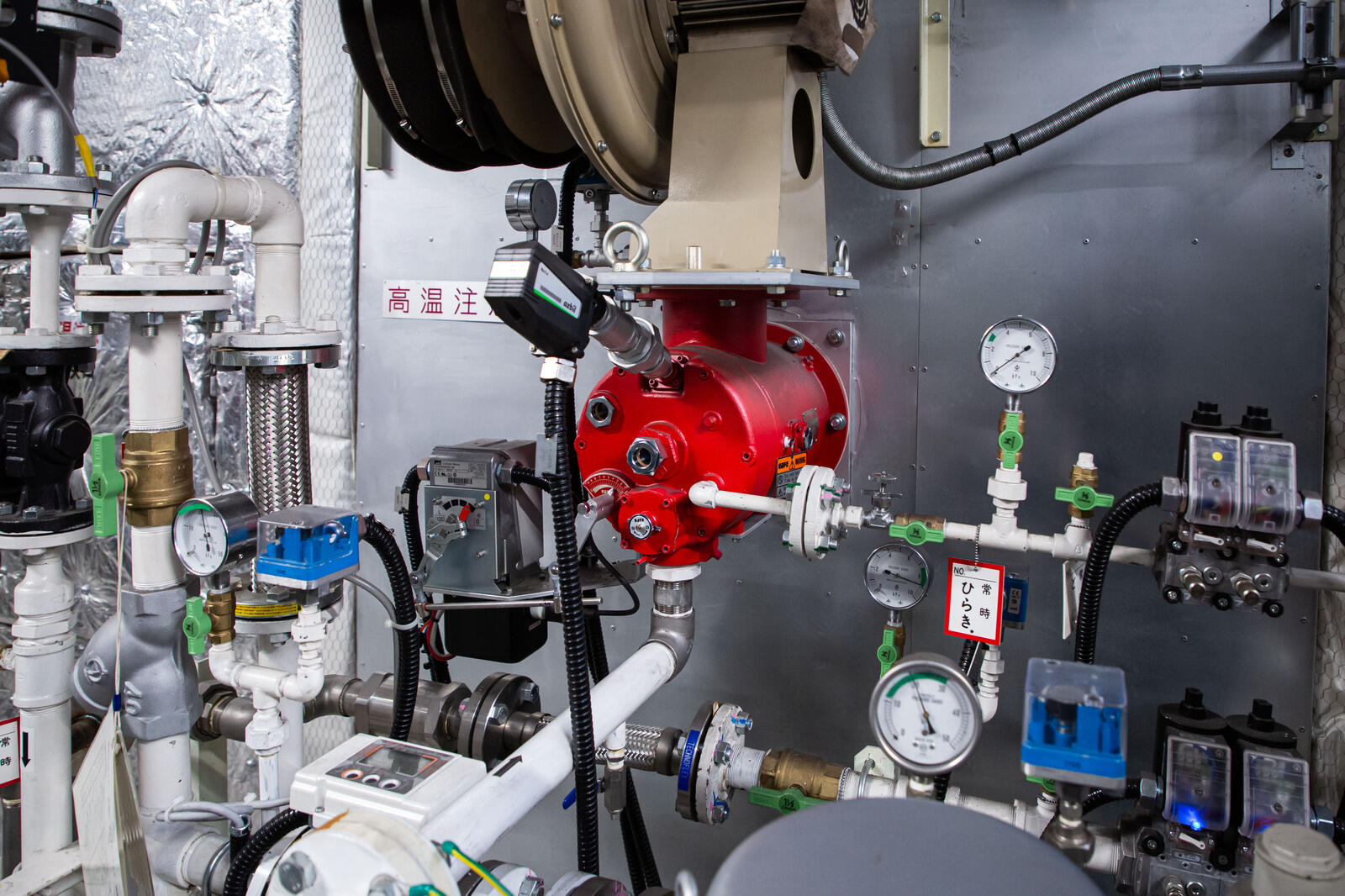
The company is also eagerly pursuing efforts to reduce the operating costs of hydrogen stations.
Hydrogen refueling equipment includes parts, such as nozzles and hoses, that experience wear and tear. Since these components should be replaced after a certain time period or number of uses, reducing the frequency of replacement naturally brings cost benefits.
At the Motomachi Plant, Toyota is testing how long such parts can last under real-world usage conditions, providing valuable data. For each component, the team is exploring whether there is scope to update replacement standards and searching for ways to extend service life.
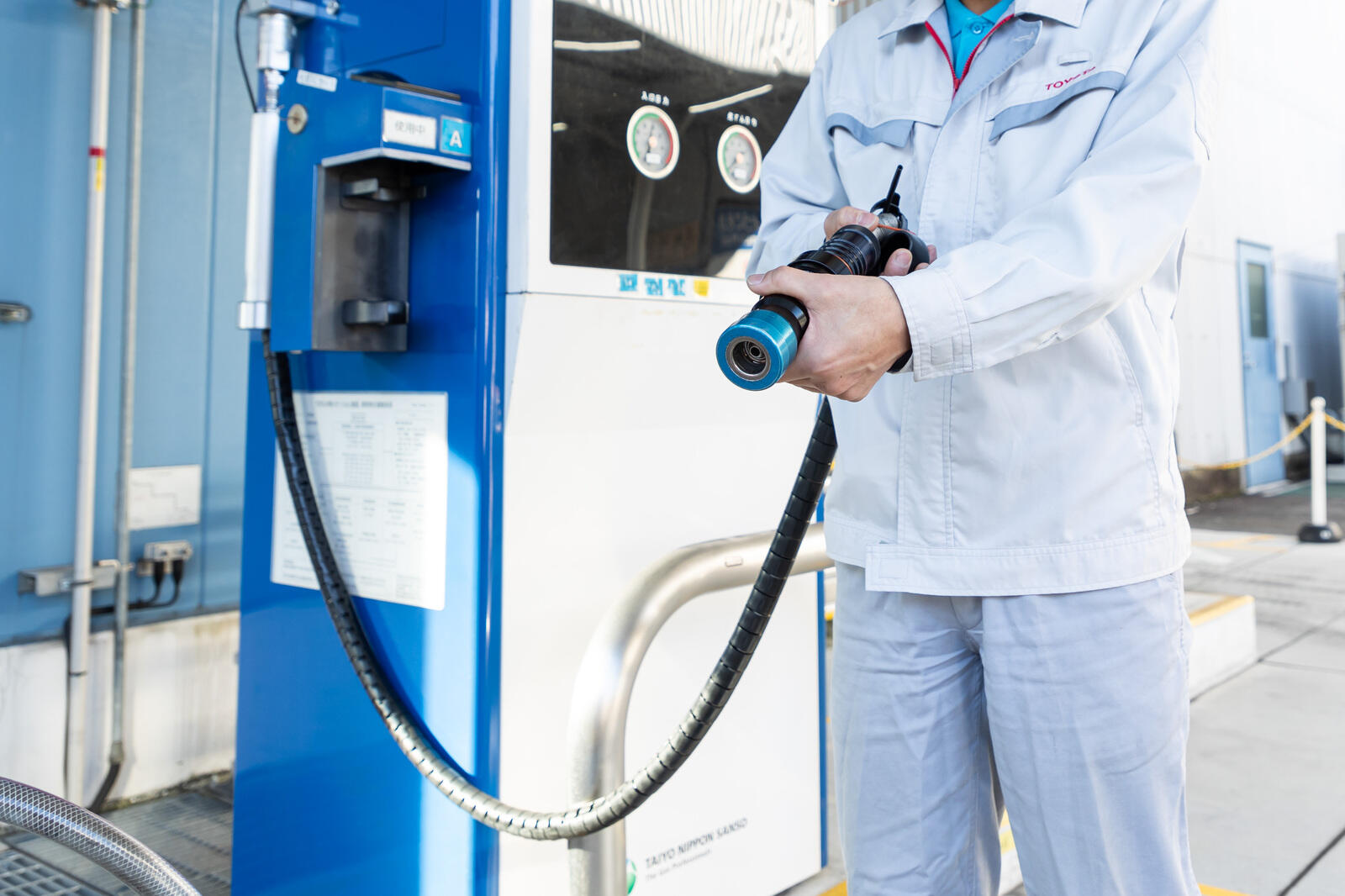
Shogo Hokushin, who manages Facility Management Group No.1 at the plant’s Facilities Engineering Department, explained the reasoning behind such experiments.
Shogo Hokushin, Group Manager, Facility Management Group No.1, Facilities Engineering Department, Plant & Environmental Engineering Division
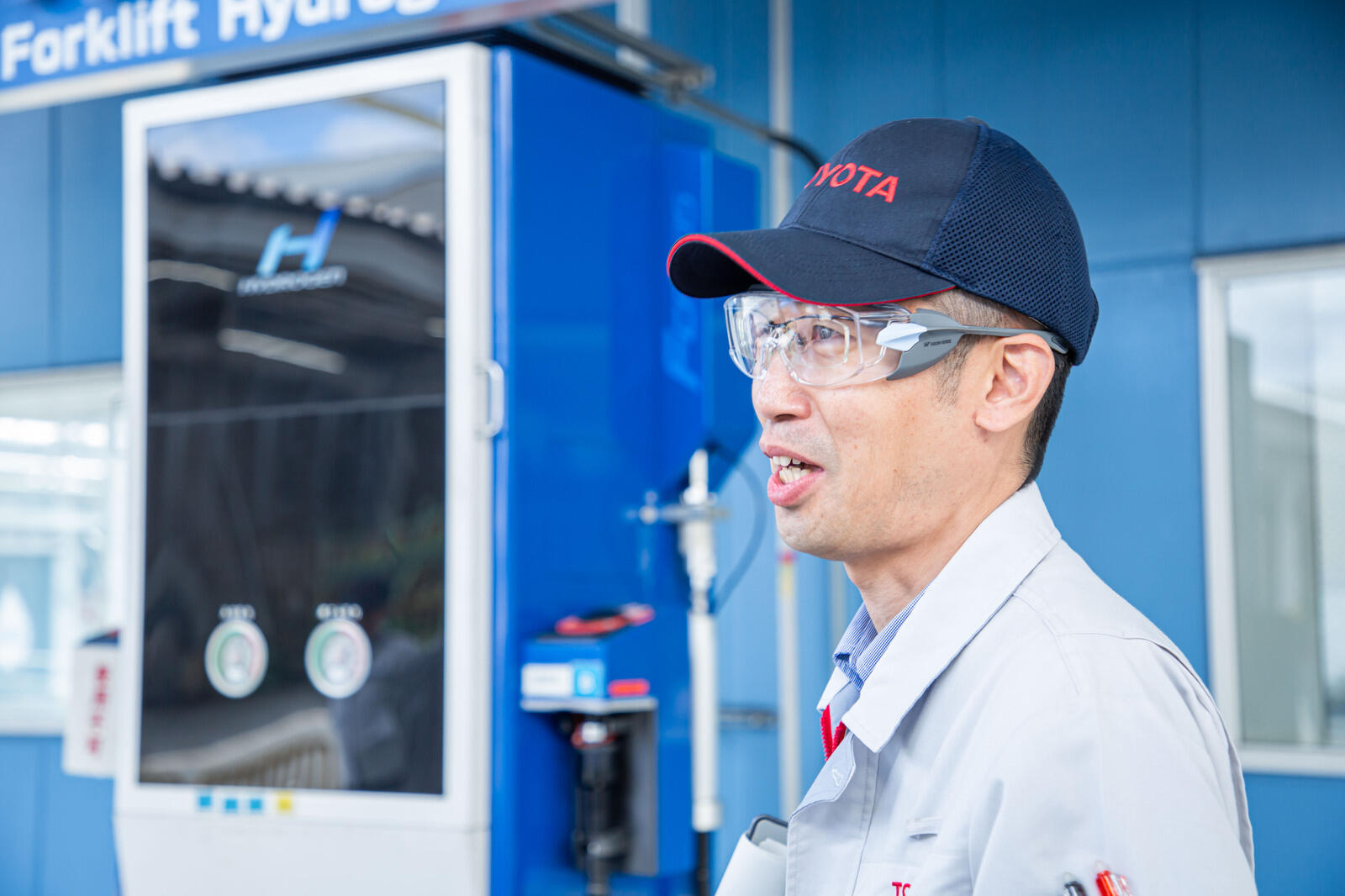
No matter how much we improve the reliability of equipment within Toyota’s plants, that alone will not create a hydrogen society.
Hydrogen stations around Japan are struggling to reduce costs. We hope that incorporating the knowledge we gain here will help lower their operating costs.
By looking beyond Toyota and teaming up with other companies, we hope to accelerate our efforts to expand hydrogen use and pursue carbon neutrality.
With gratitude
In the 65 years since construction was completed, the Motomachi Plant has refused to be swallowed up by the changing times. We asked General Manager Miyabe about the resolve that continues to pulse through the plant today.
Plant General Manager Miyabe
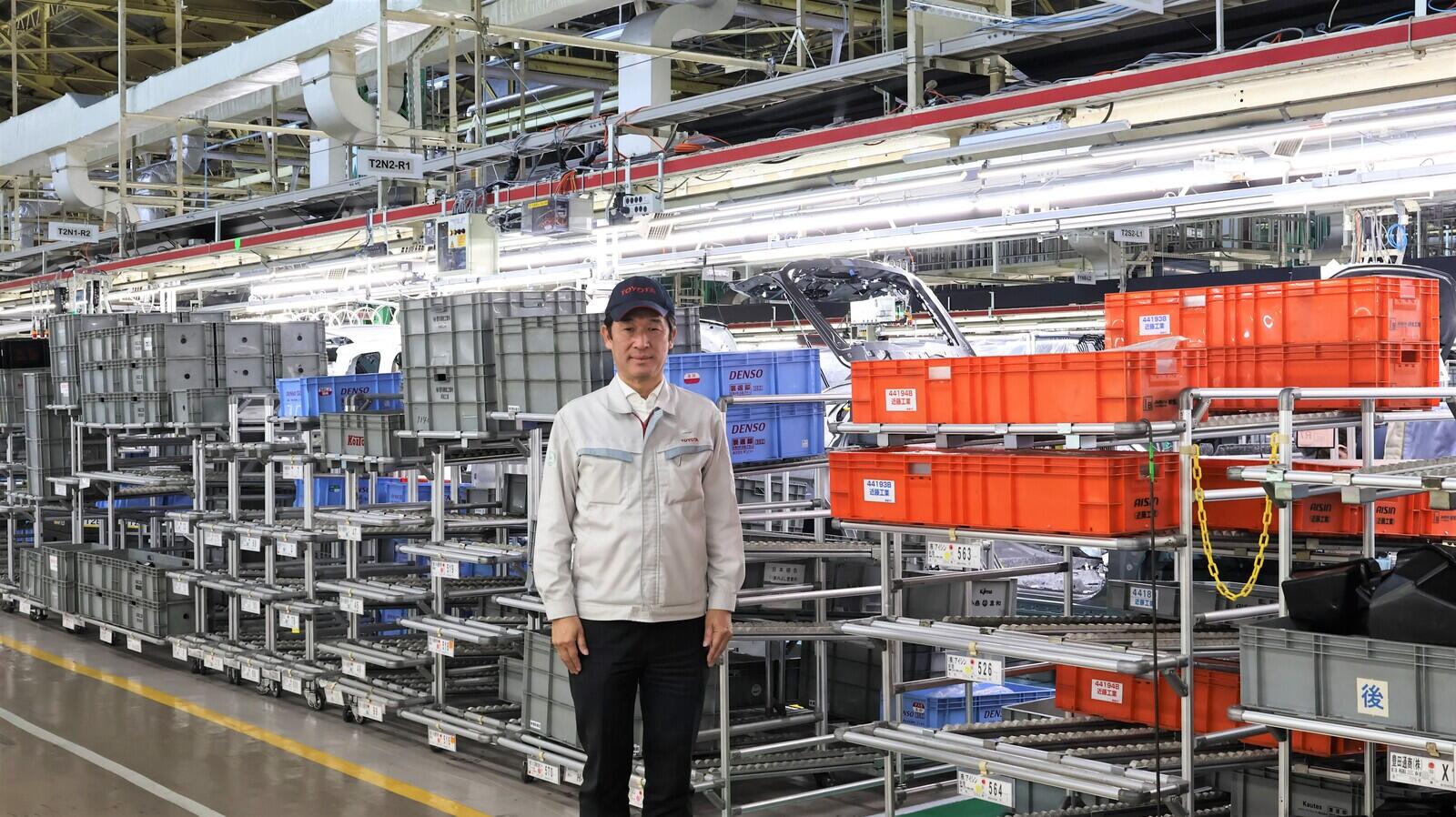
Including things like nuts and bolts, an assembly plant takes in some 3,000 different parts for a single car model.
Despite having worked at Toyota for many years, even now I still find parts crates sporting the names of suppliers that I have never seen before.
These suppliers continue to deliver the parts we need, when we need them, in the quantity we need.
It really drives home how we are sustained by an auto industry of 5.5 million people.
The Motomachi Plant’s first general manager was Honorary Chairman Shoichiro Toyoda. A few days after his passing in February 2023, the car transporting the Honorary Chairman’s casket stopped at the Motomachi Plant, giving many employees the opportunity to bid farewell.
A card from Honorary Chairman Shoichiro is displayed in the plant’s offices, bearing the word “gratitude” written in his own hand.
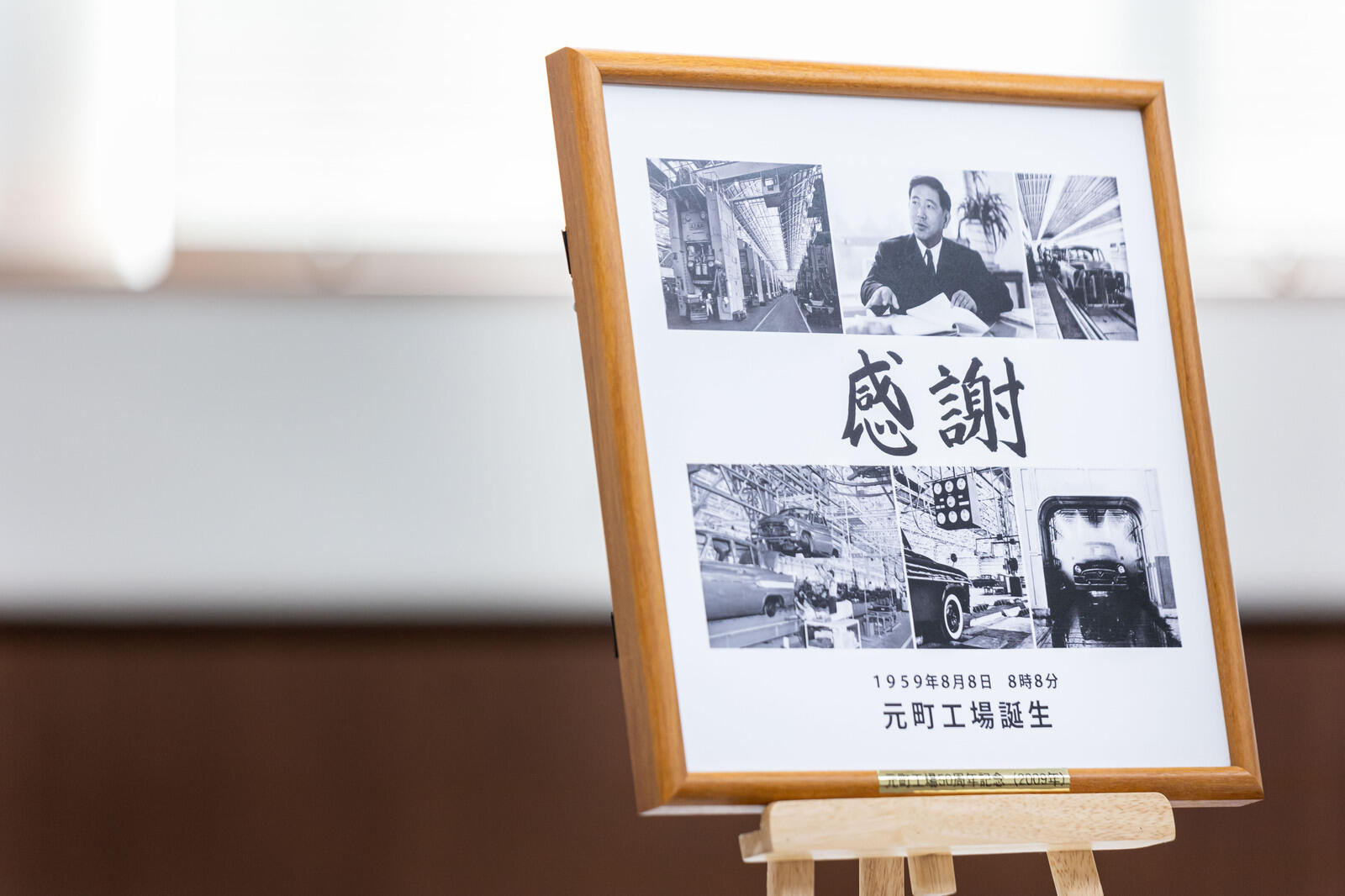
The Motomachi Plant was established with remarkable speed, starting operations just 11 months after construction began.
Behind this feat, however, was the support of many stakeholders, including the local government, which moved quickly to secure the land, and the building contractors who worked day and night to get the job done.
As the chair of the construction committee, perhaps Honorary Chairman Shoichiro recognized this more than anyone. Looking at that framed document, Miyabe’s thoughts moved beyond the plant’s 65-year history to the future.
Plant General Manager Miyabe
Shoichiro Toyoda left us with the word “gratitude”—gratitude for not just the company’s employees, but all of our stakeholders.
At the Motomachi Plan, we must embrace that sentiment and continue to move forward as a collective that emphasizes speed and takes on new challenges. Our generation must carry on the commitment made by those who came before us.
Inspired by the pioneers who spurred the plant’s creation and growth, Miyabe’s words revealed a determination to ensure that Motomachi’s bold, enterprising spirit lives on.