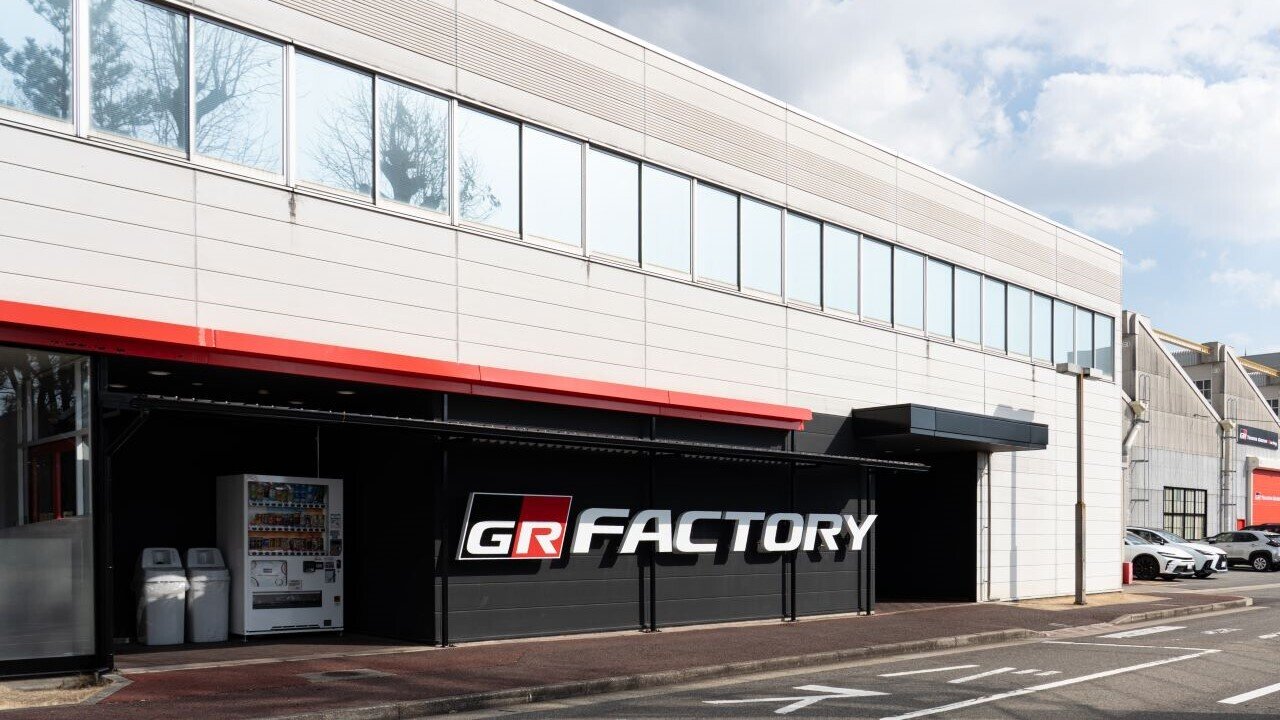
The GR Factory embodies a motorsports-driven approach to making ever-better cars. We shine the light on an area of carmaking filled with passion and dedication for Toyota's sports cars.
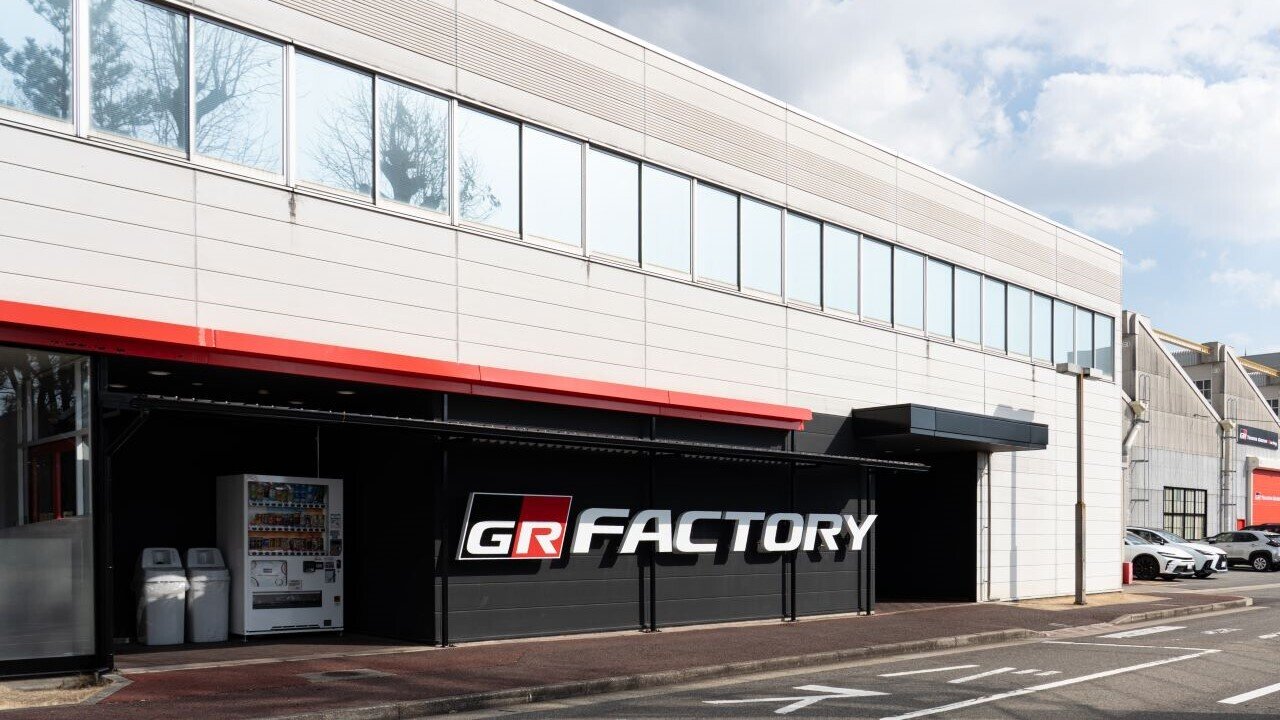
Set up for the launch of the GR Yaris in 2020, the GR Factory is a production line that swiftly adapts its processes as vehicles evolve through knowledge gained from motorsports.
After the line’s latest revamp in January, this article showcases some of the GR Factory’s monozukuri efforts.
Bringing back Toyota’s sports cars
The GR Yaris was the sports car that Chairman Akio Toyoda, aka Morizo, had always wished for.
During the 2000s, a succession of Toyota sports cars ended their production runs: the fourth-generation Supra in 2002, the Altezza in 2005, and the MR-S in 2007.
At the time, the company was pursuing growth through greater sales volumes, especially overseas, with a strategy centered around cars that “sold well and made money.” Sports cars, which were seen as serving only a select group of enthusiasts, had no place in these product plans.
As president, Akio revived the sports car with the 86 (2012) and the GR Supra (2019), yet both models were developed jointly with other companies and not actually produced by Toyota.
Akio Toyoda never let go of his ambition to bring back Toyota’s sports cars.
Making driving more intuitive
Toyota’s past approach to sports cars was to modify production vehicles for racing. It was Morizo who transformed this entrenched mindset.
With the GR Yaris, he turned the idea on its head by creating a car capable of winning races, then turning it into a production model. The plant set up to mass-produce these vehicles was the GR Factory.
Here, you won’t find any of the conveyor belts or hangers seen on mass-production lines for regular cars.
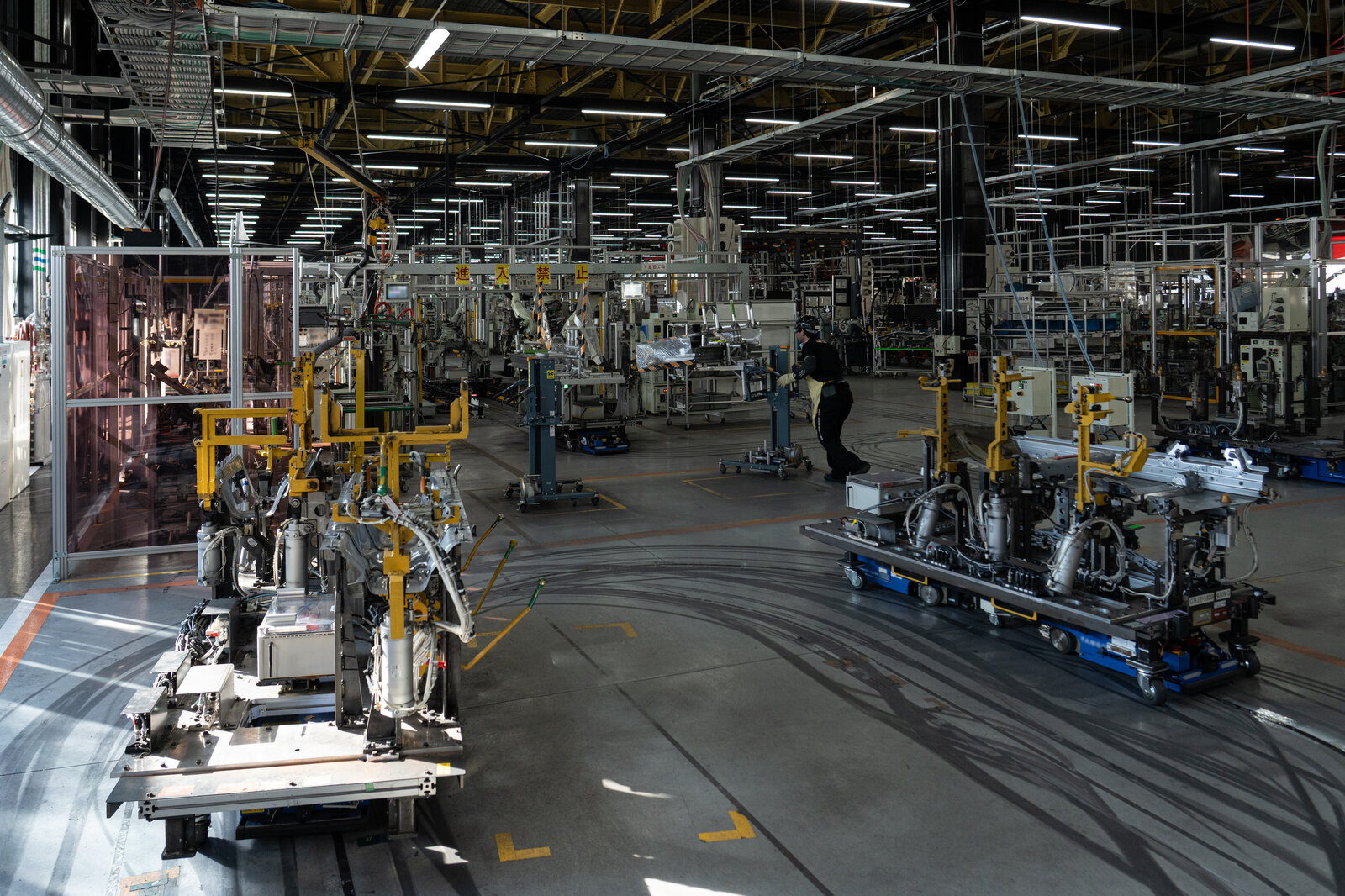
The GR Factory employs a “cell production” style where individual workers or small teams are responsible for multiple processes, with cars being moved between cells by automated guided vehicles (AGVs). This format allows the plant to introduce the latest technologies and respond flexibly to changes in models and volumes. It enables the low-volume, agile production that sports cars require, with the motorsports genba and factory floor collaborating closely on carmaking.
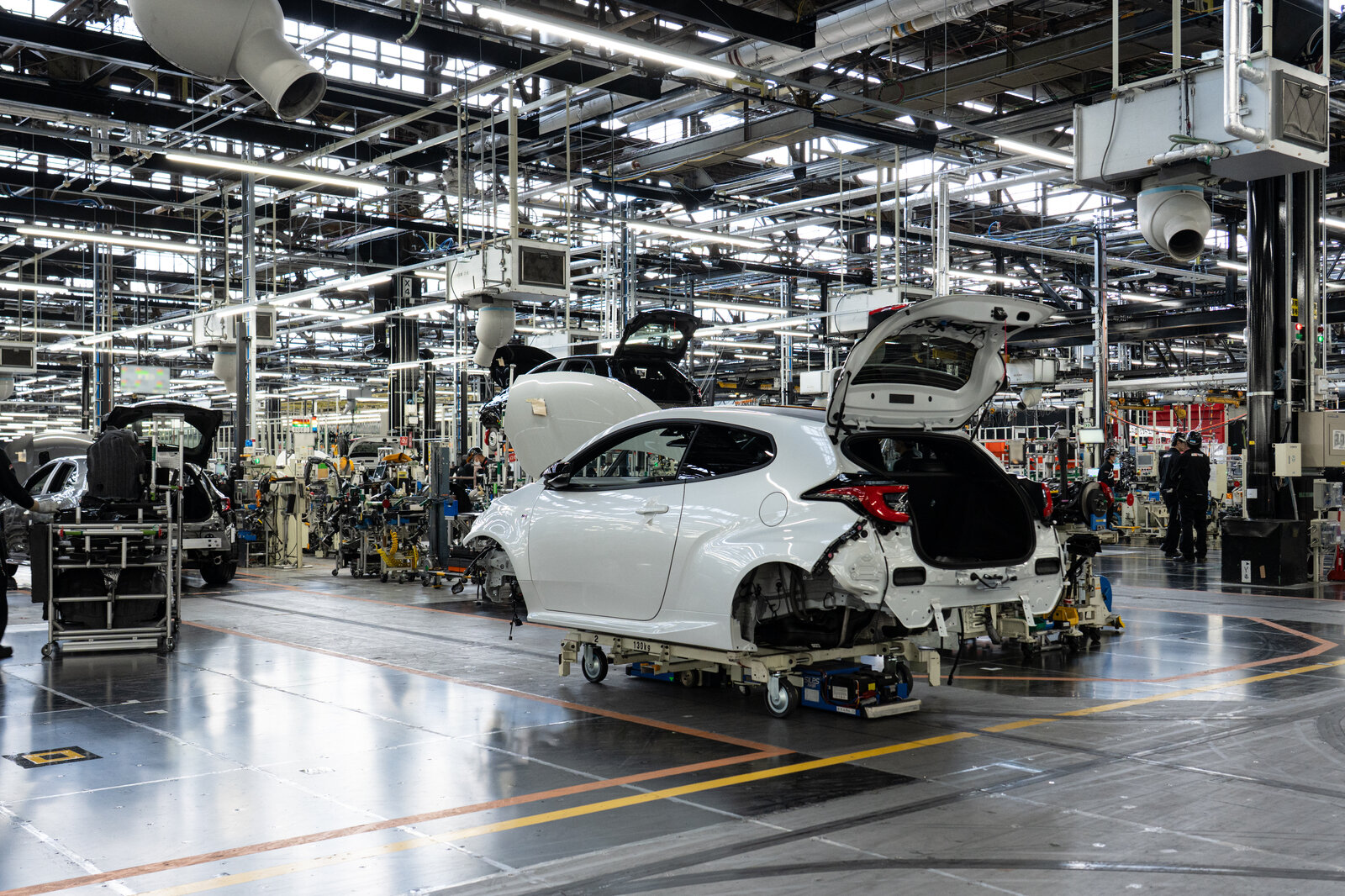
What sets the GR Factory apart is the quality of the finished products, with cars rolling off the line ready to hit the circuit at full throttle.
For example, to steer in the desired direction when required, without being thrown off balance, a car must have a highly rigid body that won’t readily deform as force is applied.
Let’s look at some of the specifics. The first step in body fabrication involves welding the underbody (the vehicle’s substructure, including everything from the front framework to the trunk floor). A 3.995-meter-long GR Yaris uses roughly 35 meters of structural welding material—10 meters more than a regular Yaris.
Next, to ensure each component is assembled into the correct position, the main body (the superstructure that forms a vehicle’s basic framework) is initially spot-welded* together and then reinforced. This is another example of the GR Factory’s unique attention to detail.
*Spot welding: a method in which metals are joined together by passing an electric current through a specific point.
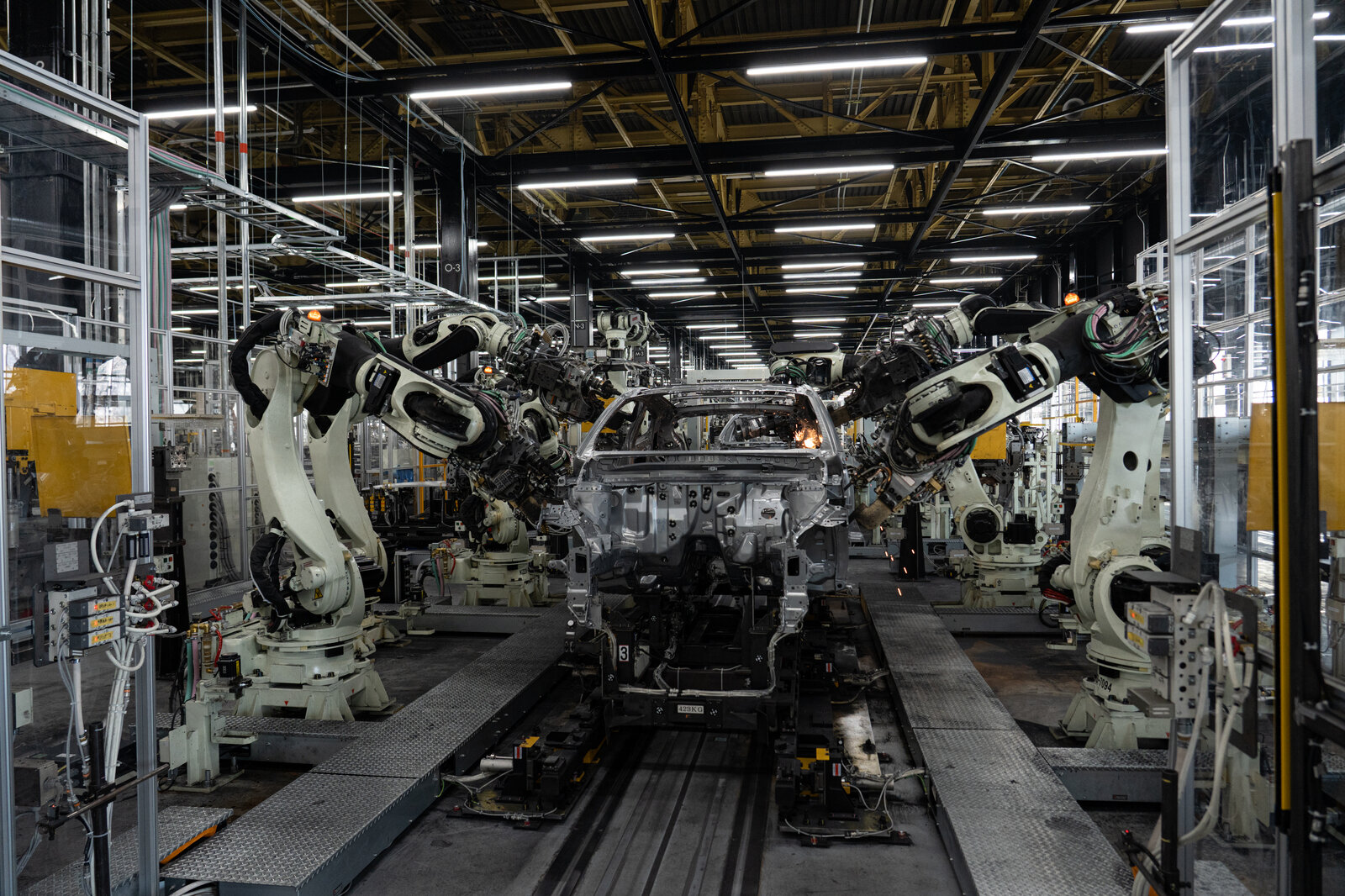
To create a body rigid enough to handle circuit driving, the number of welding points was increased from around 3,700 in the regular Yaris to some 4,500 in the GR version. With feedback from professional drivers, the production team added more points in areas where stronger bonding was deemed necessary.
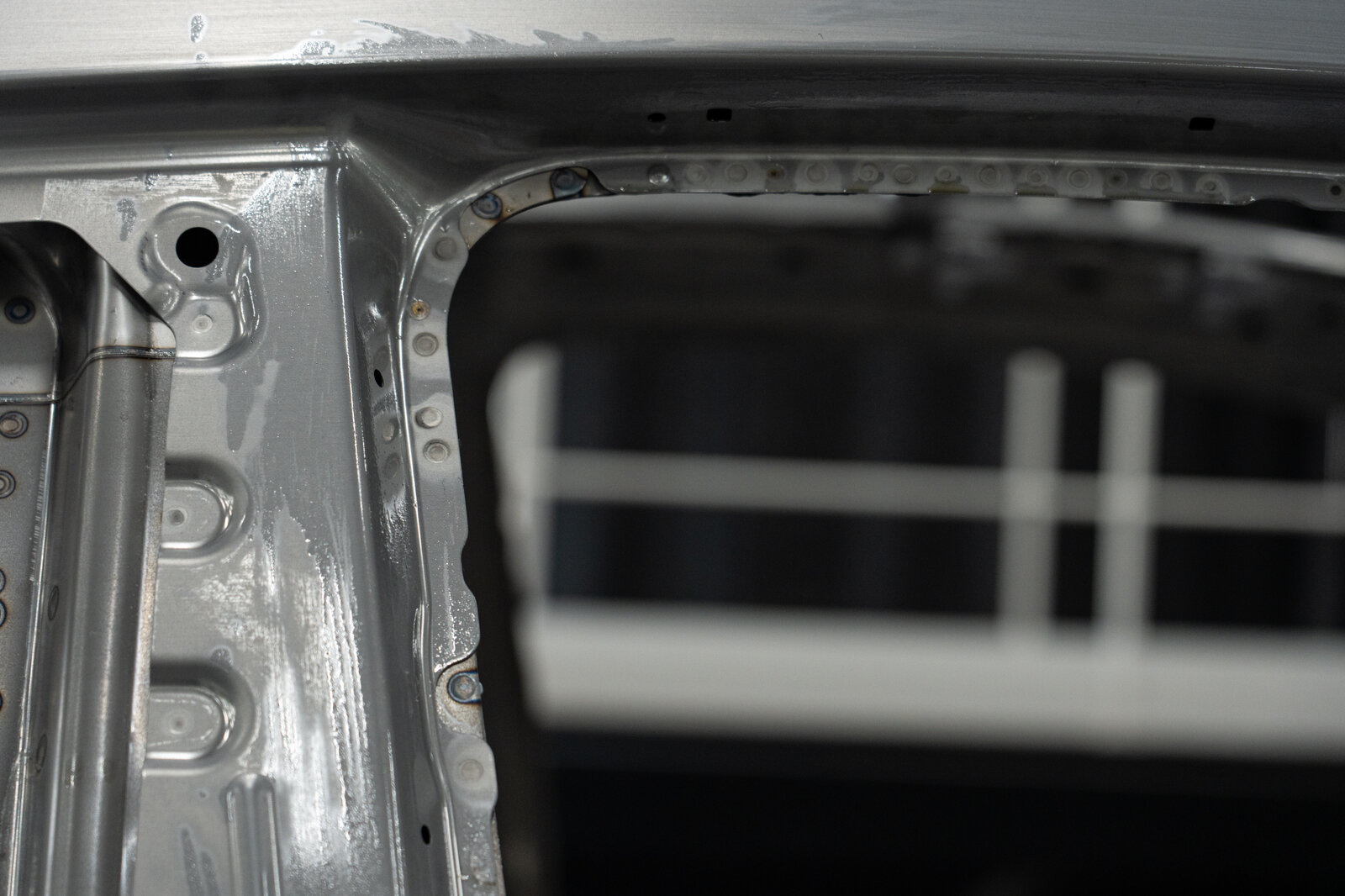
After going through this process, the GR Yaris bodies are rust-proofed. Some are then sent to Finland, where they end up as Rally2 vehicles. The fact that the GR Yaris’s skeleton is virtually the same as the Rally2 shows how Toyota overturned convention by making production models out of race-winning cars.
The body production process ends with a precision inspection, where the finished frame is checked against blueprints. Even among all of the GR Factory’s meticulous work, this step deserves special attention.
Every manufactured product will contain variations within a set tolerance range. However, even minor deviations that pose no problems in a production car can have a big impact on results in racing, where vehicles are pushed to the limits of performance.
To minimize such variations, three-dimensional measurements accurate to tenths of a millimeter are used to capture the misalignment of bolt holes for attaching suspension components to the body.
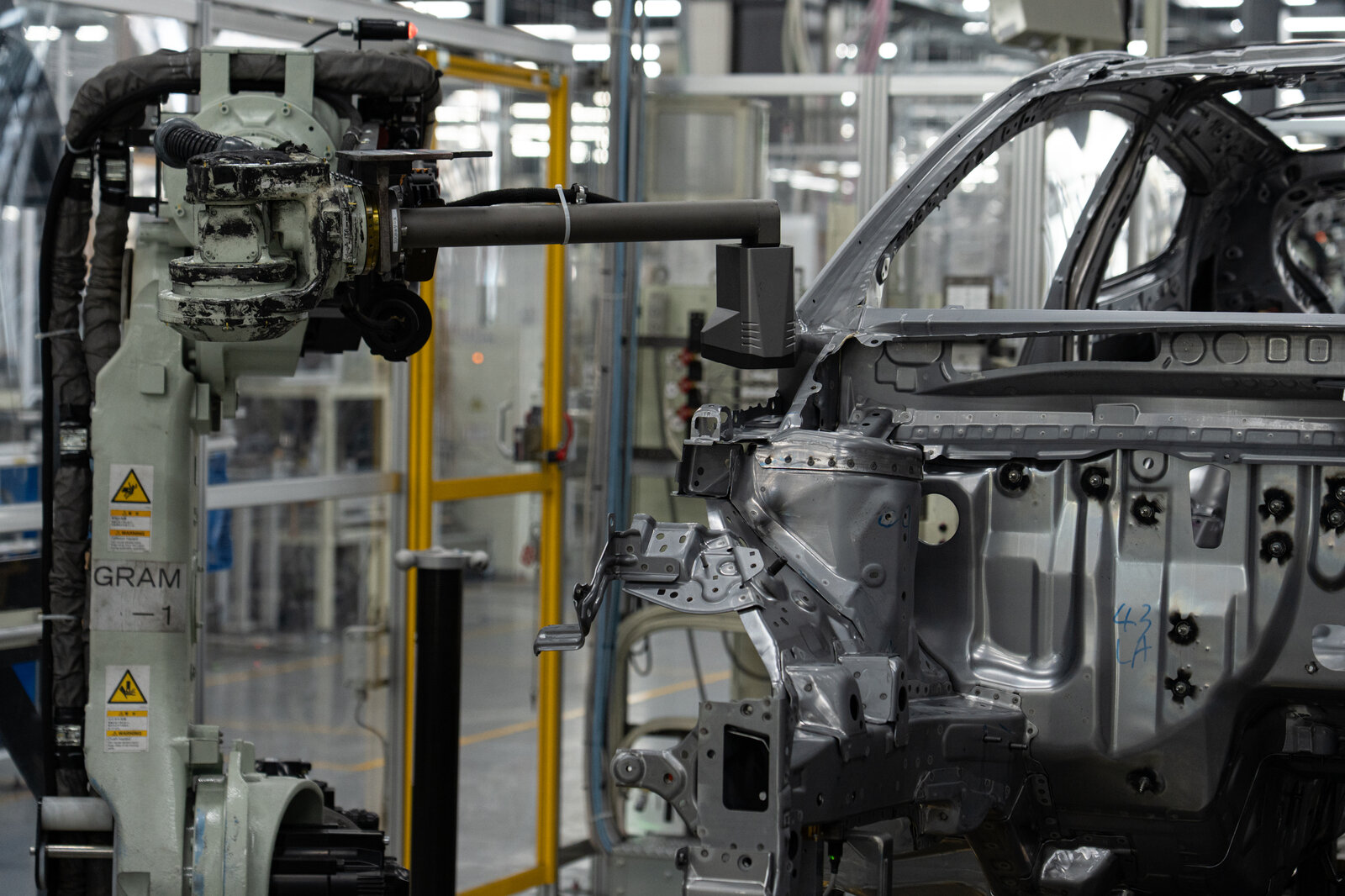
Measurement data is sent to a specialized analysis system, which selects the assembly parts that best compensate for any misalignments, ensuring that the finished body comes as close as possible to the intended design values.
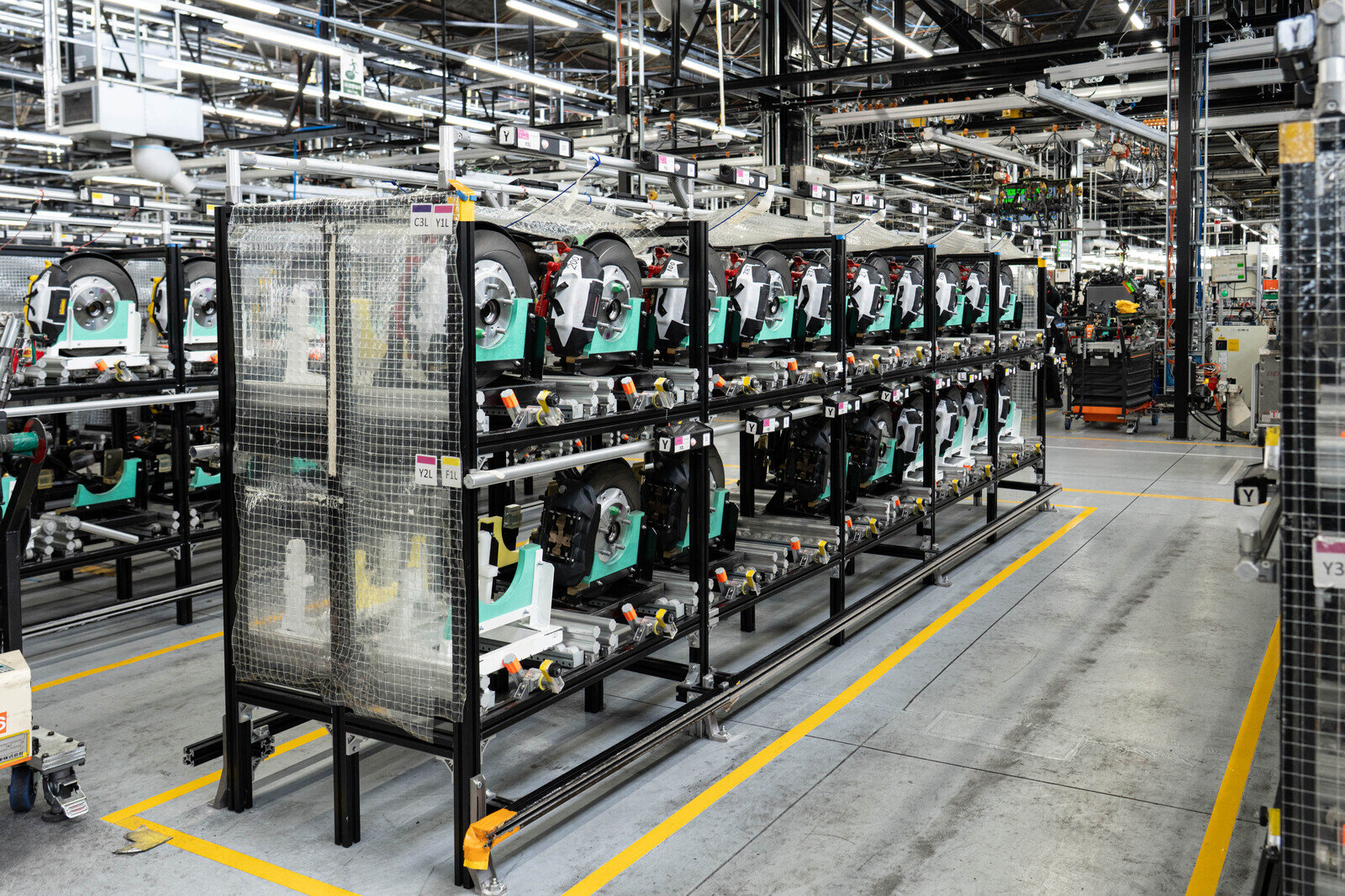
On a standard mass-production line, workers mount suspension components by lifting them up to the vehicle body as it hangs overhead.
At the GR Factory, however, the suspension system is set up precisely on a level floor and the body is brought down on top, exactly as in motorsports.
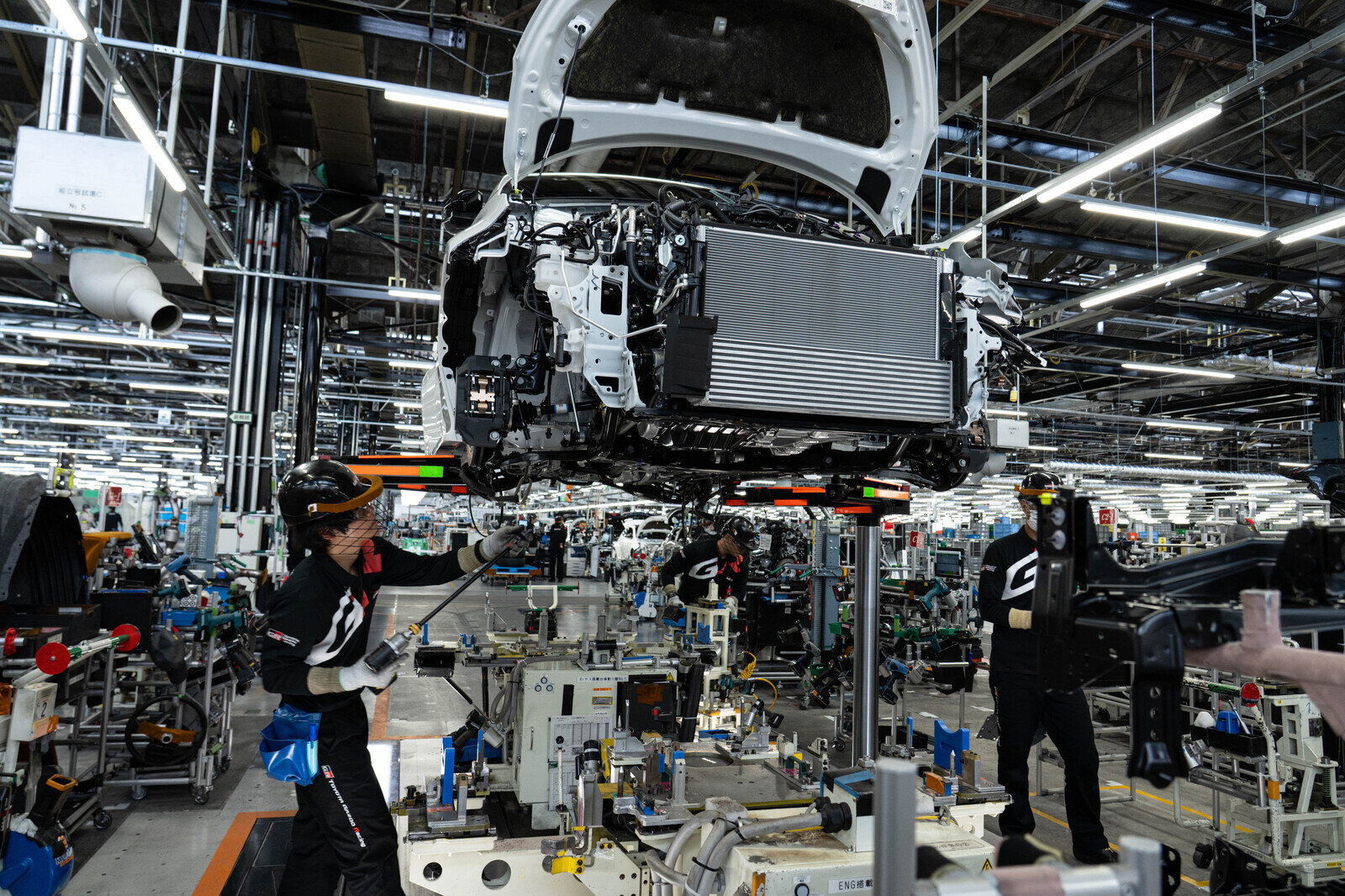
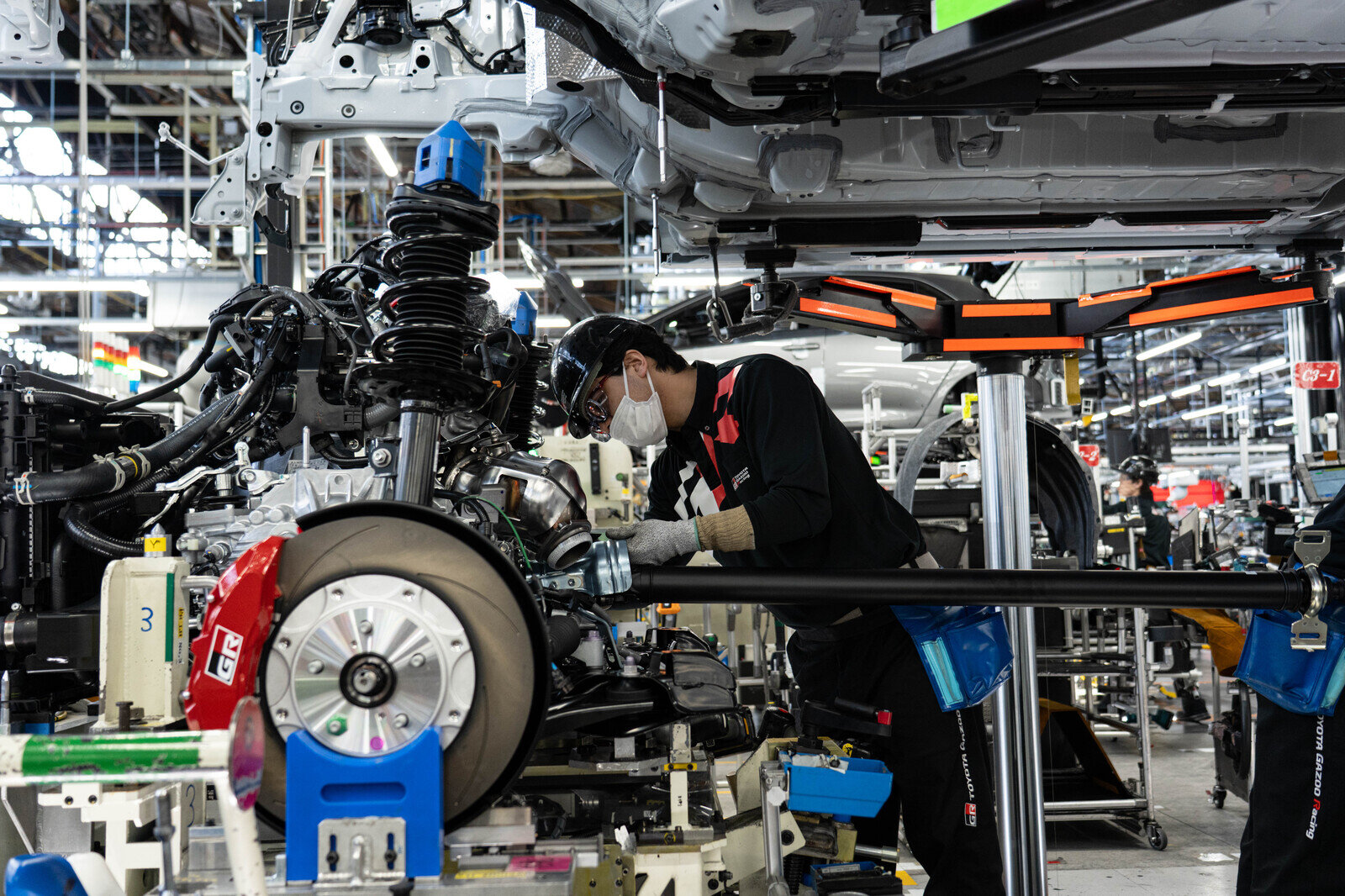
Making the body stationary creates a stable work environment. What’s more, working with the body’s weight leads to a more secure assembly and greater precision.
Racing driver Hiroaki Ishiura is involved in discussions from the vehicle planning stage, providing honest feedback that bolsters GR’s carmaking. “The work looks no different from what we normally see in a racing garage,” he says. “Even if you make millimeter-level adjustments at the development stage, you need to replicate that in the production stage to ensure that customers receive cars with the same precision. I’m really grateful that the plant makes this possible.”
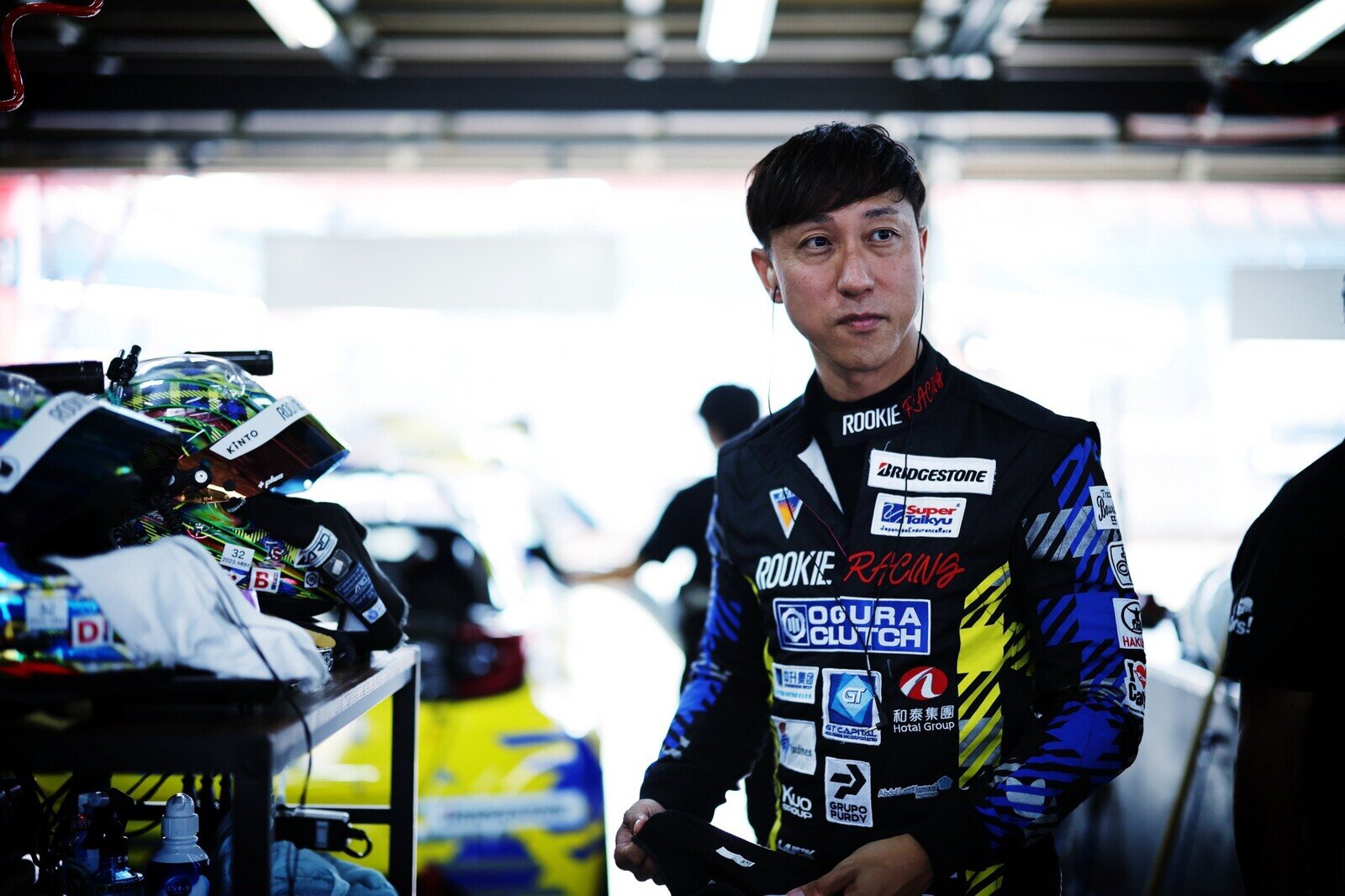
Every vehicle that leaves the GR Factory is also put through its paces on the test course. They are evaluated by 16 inspectors who are trained and certified in driving assessment skills.
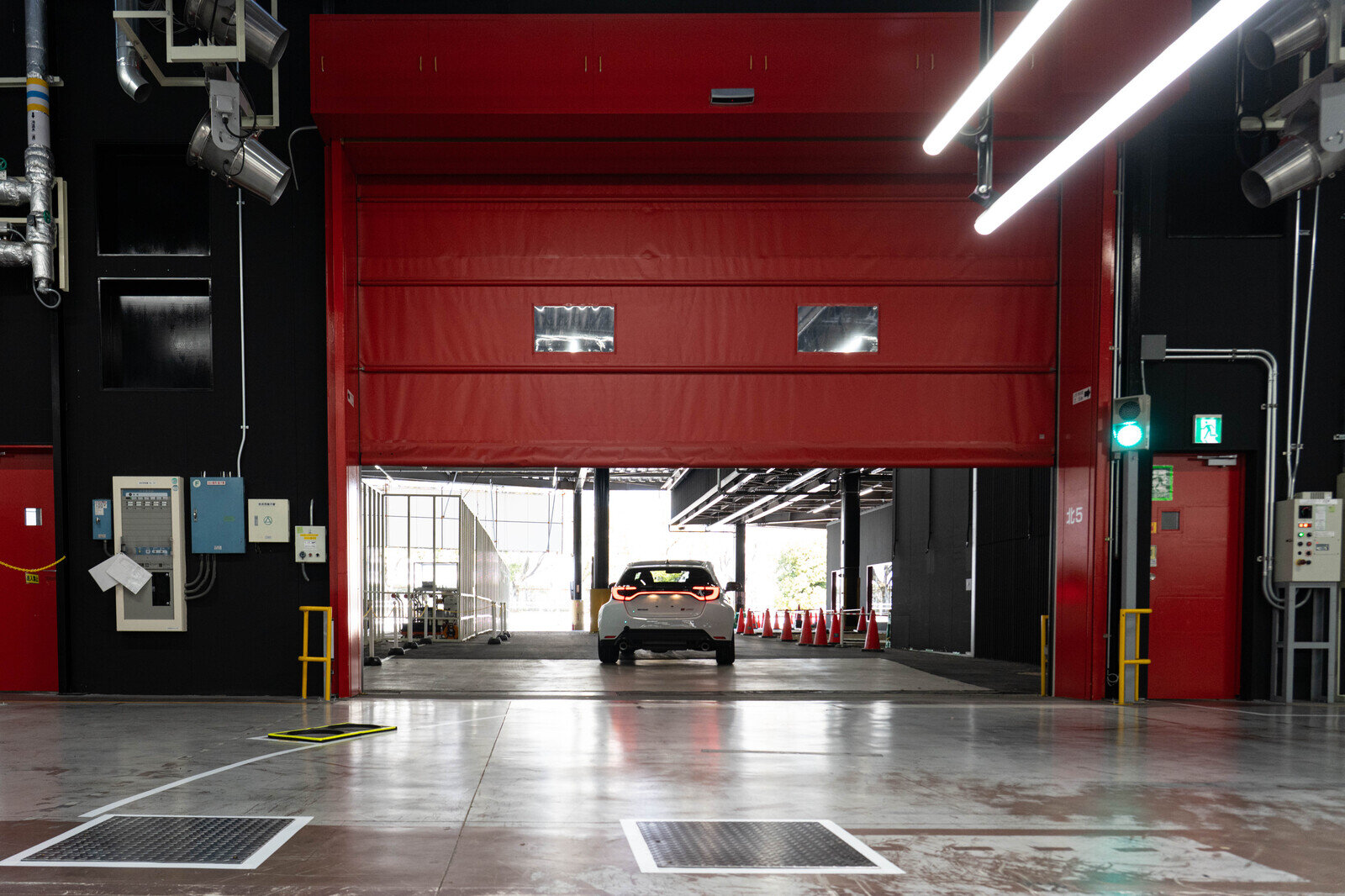
Ishiura himself supervises the assessment criteria, which comprise 14 items including straight-line stability at 120km/h, handling stability* during lane changes, and behavior and noise when braking. All of the results are recorded to provide feedback for development and production.
*Handling stability: a vehicle’s ability to remain stable while driving, stopping, and turning.
Cars that pass these final checks are duly delivered to customers.
This approach to monozukuri, which gives careful attention to every vehicle that passes down the line, results in cars that have a distinct GR feel in the way they drive, turn, and stop.
Chief Engineer Naohiko Saito, who oversaw the development of the GR Yaris, explains:
Chief Engineer Saito
We are able to provide customers with cars that offer the exact same performance as those created by our master driver Morizo and professional drivers Hiroaki Ishiura and Kazuya Oshima. The feedback these drivers provide spurs constant improvement.
I think the GR Factory is a unique kind of place that didn’t really exist at Toyota until now.
GR’s never-ending challenge
Being different from the typical mass-production line, the GR Factory’s style of monozukuri also contributes greatly to developing personnel.
Motomachi Plant General Manager Yoshihisa Miyabe describes the continuous growth among his employees.
Plant General Manager Miyabe
On the manufacturing side, we not only continue to evolve through feedback from motorsports but we also accumulate data on every car produced day to day.
For example, in our selection of parts for assembly, we track changes in the algorithm for both left-right and front-rear balance. While there is no solution for the variations in manufactured products, we are searching for ways to further lessen their impact. Building on the vast amounts of information that only the genba can provide, our team is constantly making improvements and advances that lead to ever-better performance on the road.
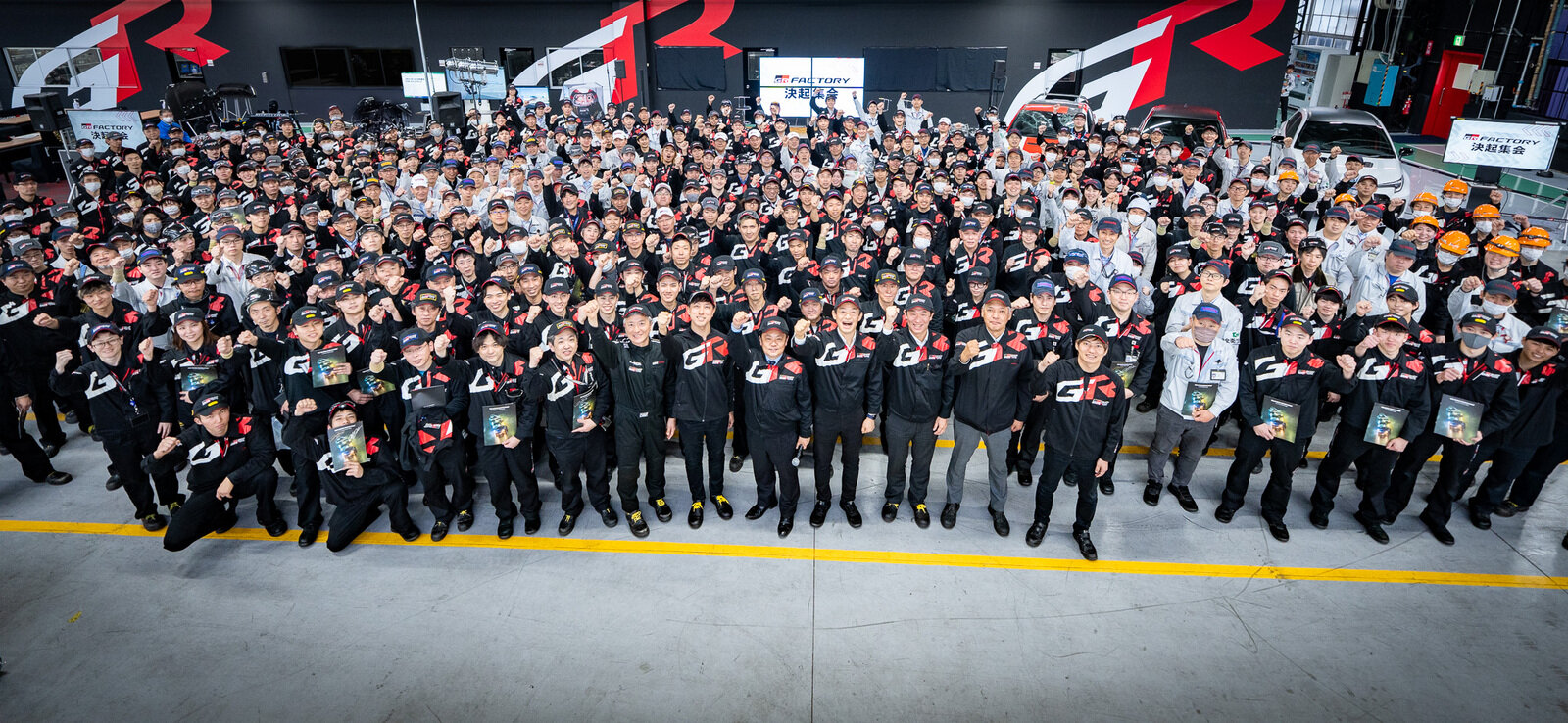
We have always been good at driving constant improvements and evolution in safety, quality, and productivity.
At the GR Factory, however, it is not only the cars that are evolving, as we continue to hone our skills to make ever-better cars and ever-better driving experiences.
From April 18, 2025, the GR Factory has also begun offering plant tours for GR Yaris and GR Corolla owners.
Information about these tours is distributed to eligible MyTOYOTA (website) and MyTOYOTA+ (app) accounts.
GR Company President Tomoya Takahashi describes the GR Factory as “a place where we can lead the company with pioneering challenges, figuring out how to make new improvements and transform our plants to enable ever-better carmaking.”
We hope you will have an opportunity to see this one-of-a-kind line that made Morizo’s wishes come true.
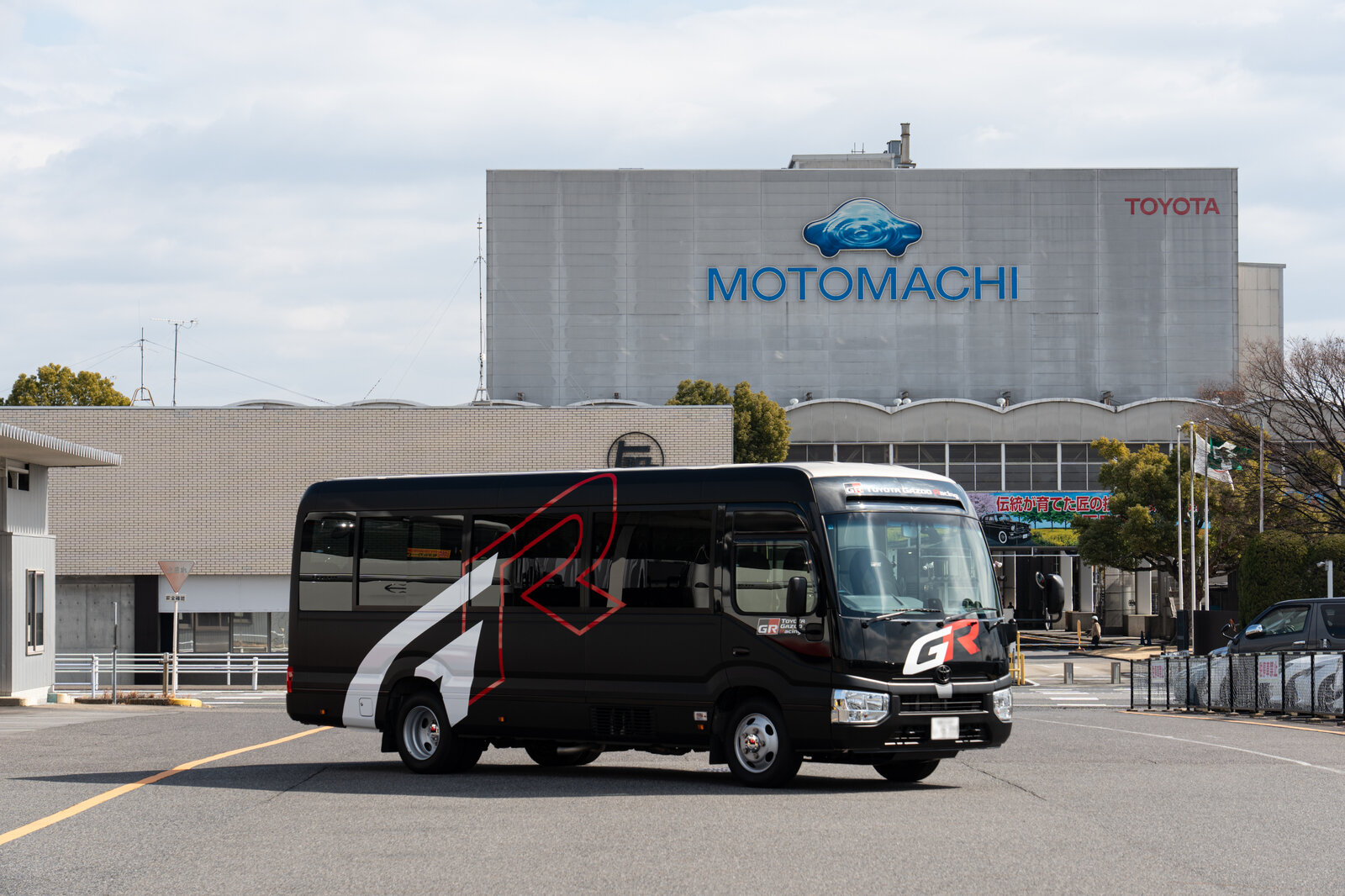