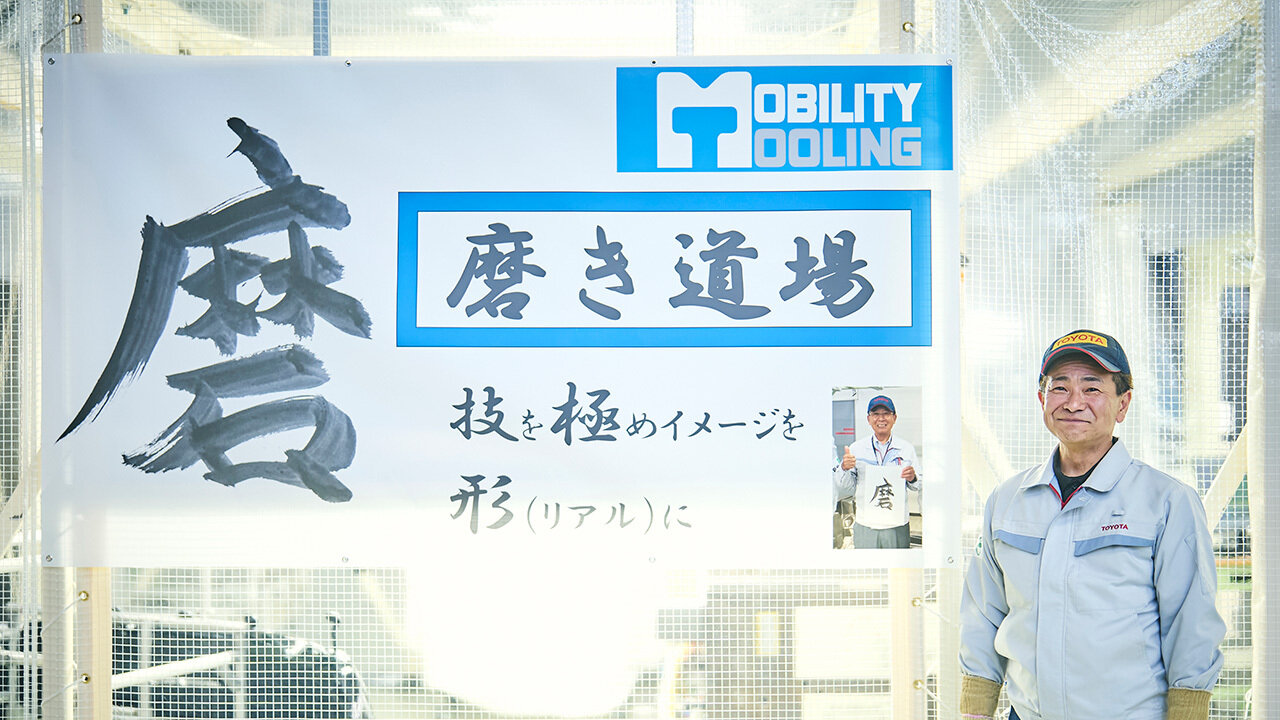
自動車業界を匠の技で支える「職人」特集。第20回は金型を鏡面のように磨き上げ、トヨタ初の塗装レスバンパーを実現した「金型磨きの匠」に話を聞く
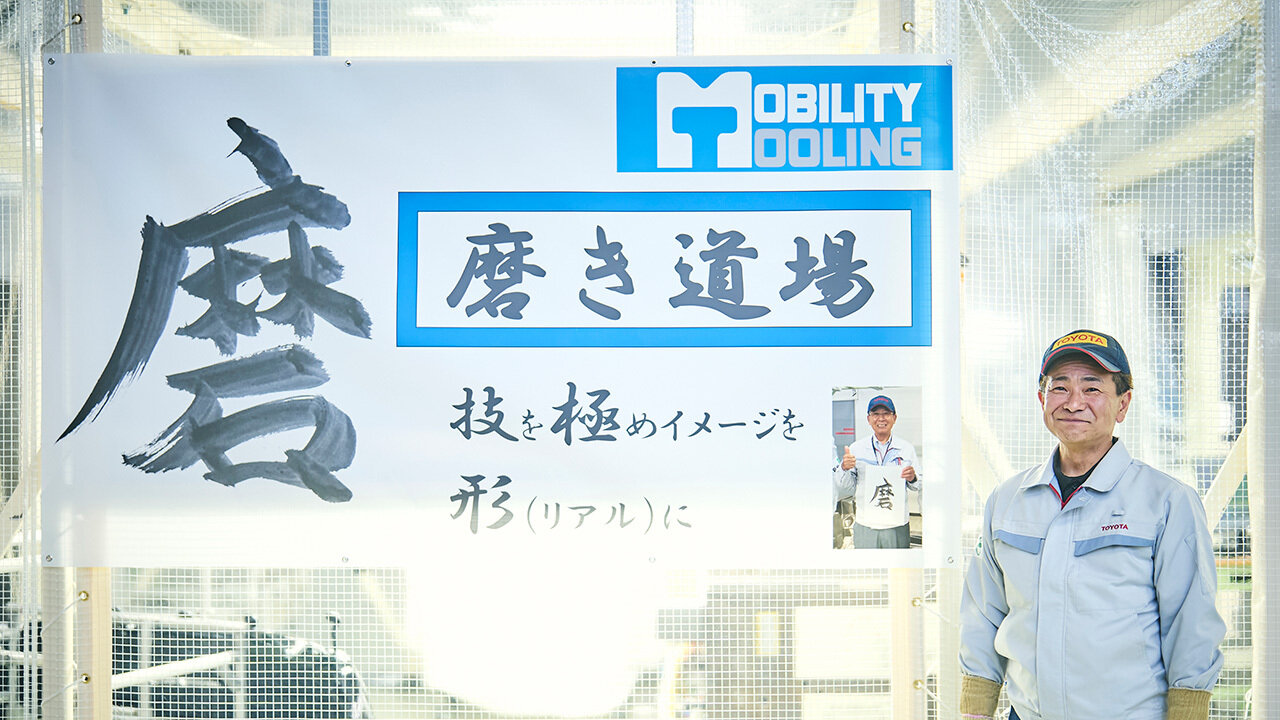
3DプリンターやAIをはじめとするテクノロジーの進化に注目が集まる現代。だが、クルマづくりの現場では今もなお多数の「手仕事」が生かされている。
トヨタイムズでは、自動車業界を匠の技能で支える「職人」にスポットライトを当て、日本の「モノづくり」の真髄に迫る「日本のクルマづくりを支える職人たち」を特集する。
今回は、クラウンスポーツのリアロアバンパーを塗装レス化するため、樹脂成形用金型の表面を鏡面のように磨き上げる技能を極めたモビリティツーリング部の加藤英樹の後編をお届けする。
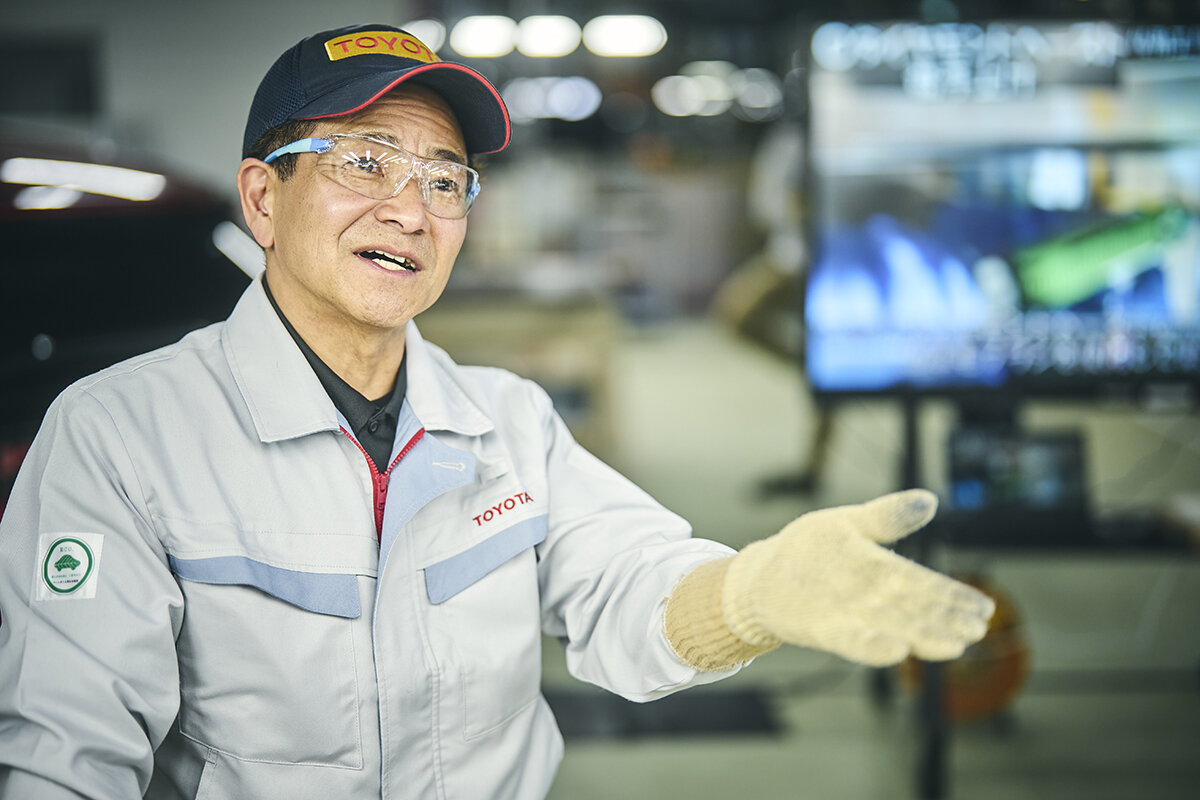
第20回 手作業でキズ一つない鏡面を実現する「金型磨きの匠」加藤英樹
トヨタ自動車モノづくり開発センター モビリティツーリング部 シニアエキスパート
ゼロからの試行錯誤
前編では金型磨きの匠としての加藤の40年にも及ぶ経歴と塗装レスバンパーへの挑戦について紹介したが、後編では具体的な取り組みと成功までの道のりを追う。
加藤と弟子である竹下千裕は、どのような道具と工程で金型を鏡面にまで磨き上げられるか、ゼロから模索を始めた。
加藤
初めての試みでしたので、適切な方法を見つけるために多くの試行錯誤を重ねました。約1年間にわたり、通常業務の合間を縫ってさまざまな砥石やサンドペーパー、研磨剤を試し、最適な磨き方を探求していきました。
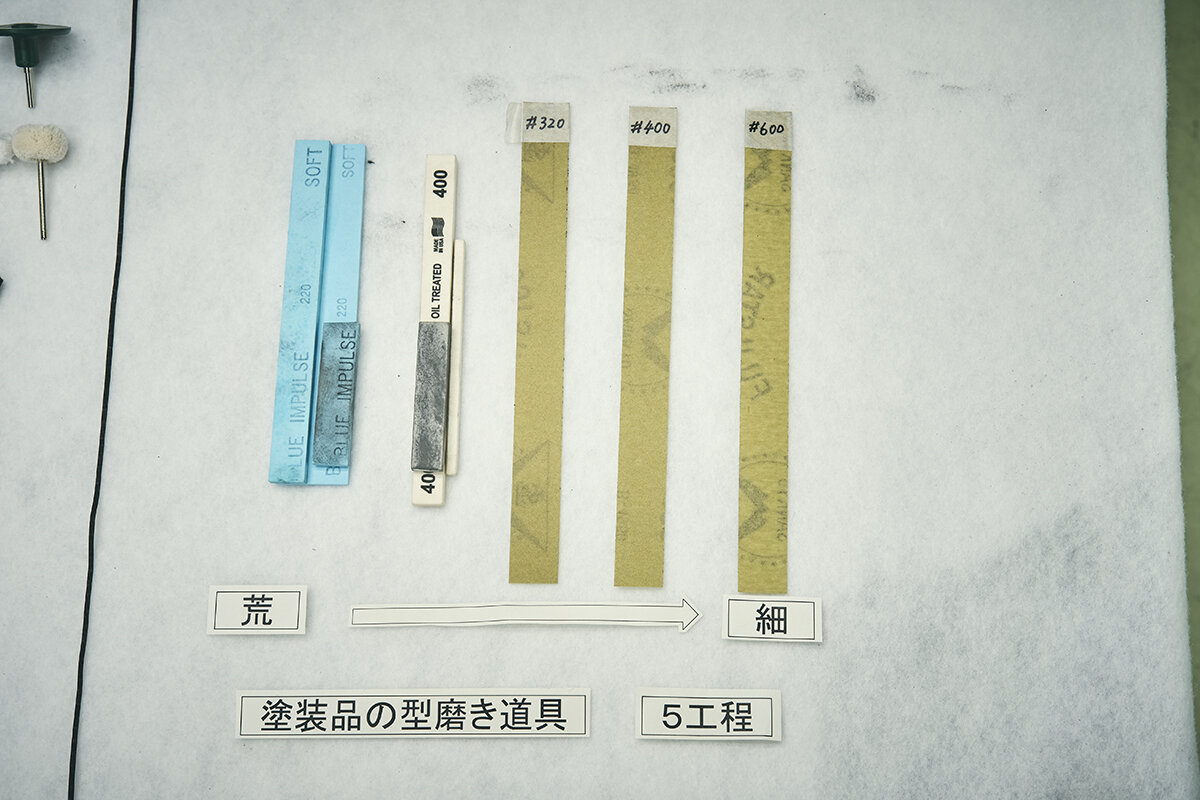
通常の塗装品用の金型は、砥石とサンドペーパー計5種類で5工程の磨きで完成する。しかし、塗装レス用金型の鏡面仕上げには、最終的に砥石7種類、サンドペーパー4種類、研磨用のダイヤモンドペースト3種類を使った14工程が必要だと分かった。
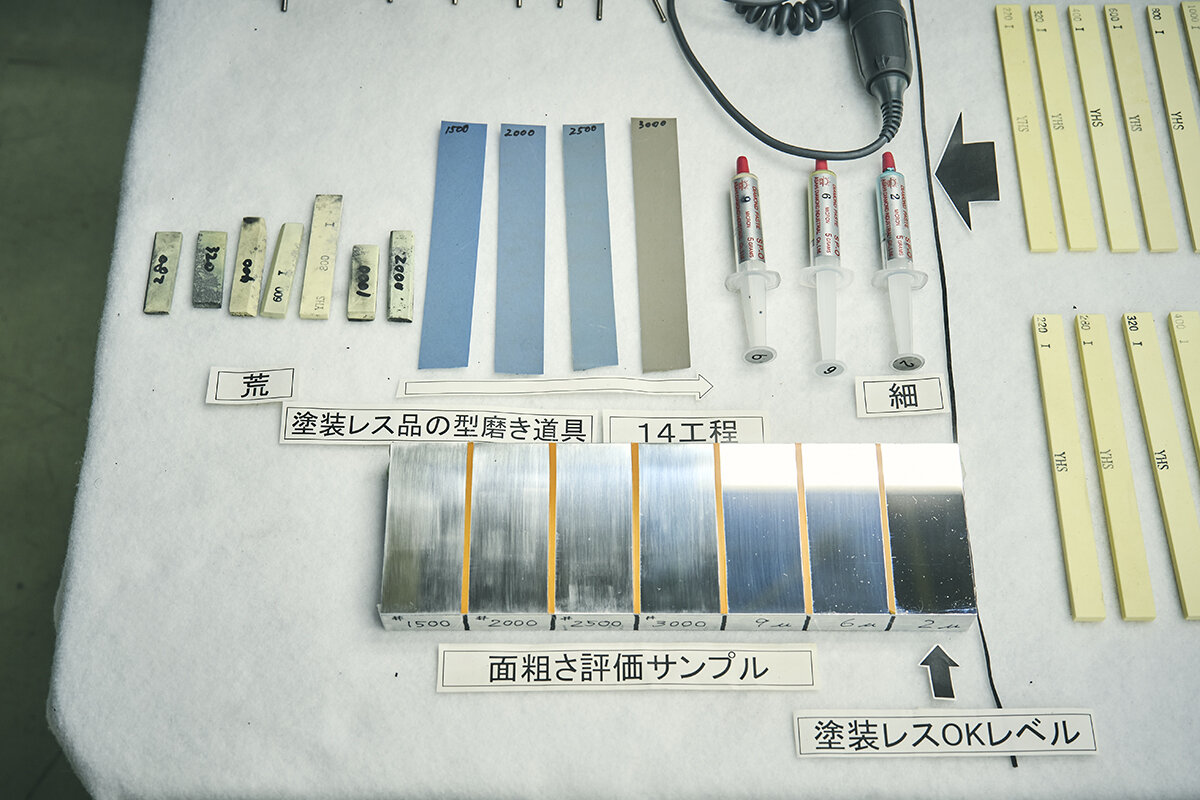
道具と工程を決めた後も問題は続いた。試行錯誤を半年ほど続けた頃、加工した金型に無数の小さな穴が見つかったのだ。これは素材自体の問題だった。
加藤
磨きの技術と工程がほぼ確立したところで、金型表面に微細な穴が多数形成されていることに気づきました。素材の組織から微小な粒子が剥がれ落ちるためなのですが、どのような方法を試しても除去できません。道具もステップもほぼ見えてきた段階でこの問題が発生したため、プロジェクト自体の継続が危ぶまれました。半年かけてきた成果が一瞬にして覆されるような状況でした。
竹下
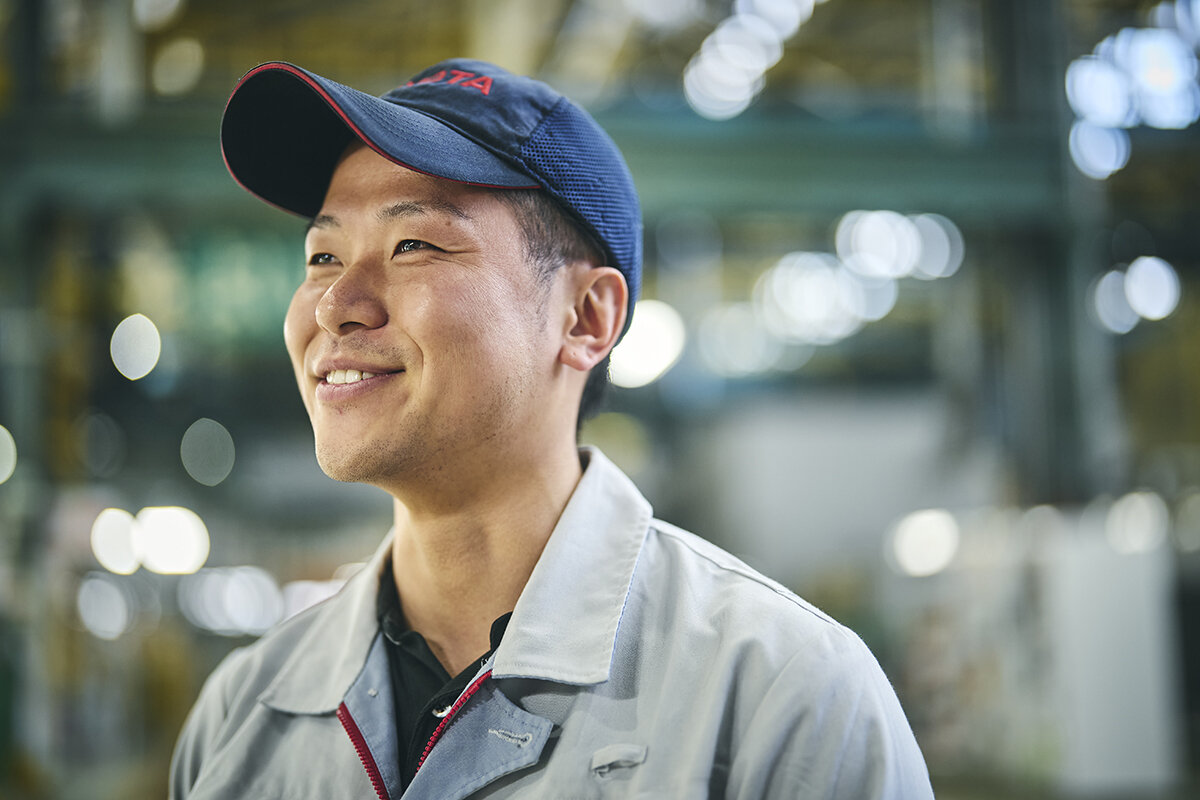
この問題に直面した時は、本当に困難な壁に突き当たったと感じました。せっかく確立してきた工程が使えなくなるのではないかと心配しました。
このような穴が生じる原因は金型材料の製造過程にあった。鍛造過程で高温の金属を圧縮する際、空気中の窒素などの異物が微量に混入し、それが窒化鉄として固まるのだという。通常はそれほど問題にならないが、鏡面レベルまで磨くと、その部分が剥がれ落ちて穴になってしまう。
この問題を解決するため、より硬度が高く、不純物の少ない鋼材が必要だと分かった。ここで塗装レスバンパーのプロジェクトを推進した製品化製造技術部(当時)の新田翼が新たな材料探しに奔走した。
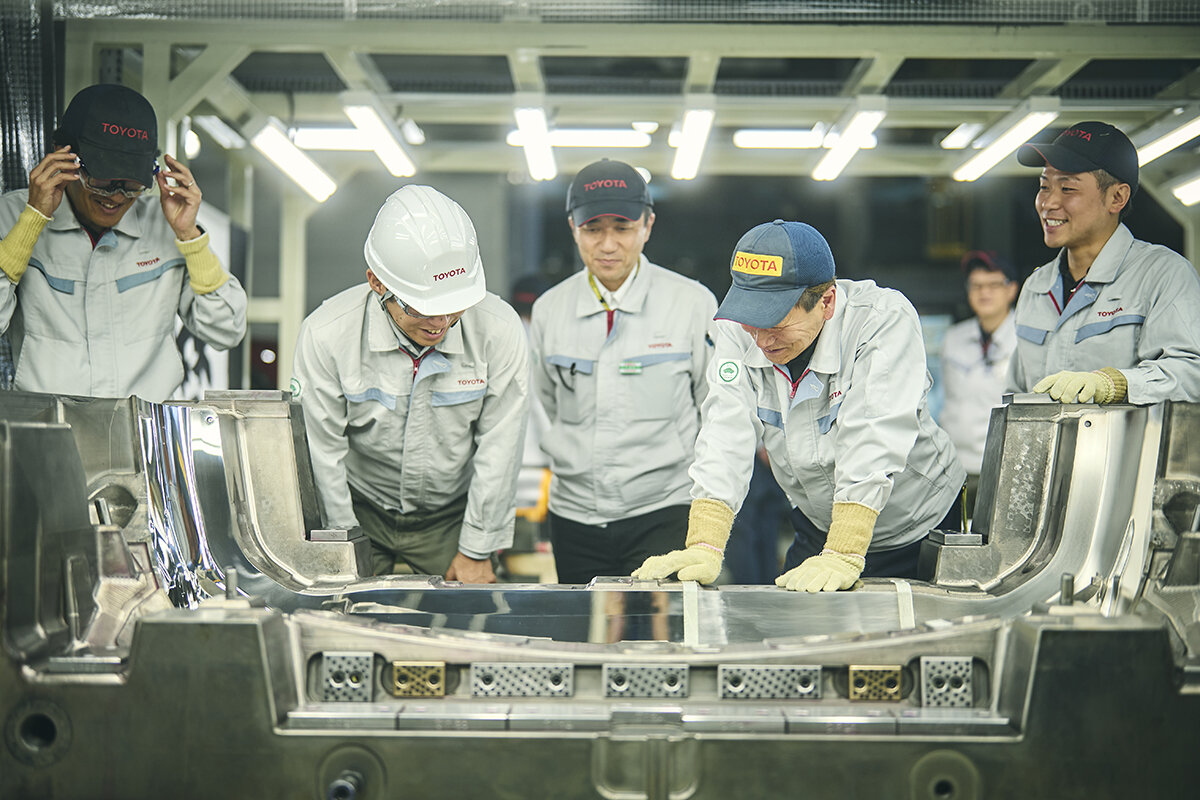
真空環境下で鍛造された特殊鋼材なら、不純物の混入が少なく理想的だが、バンパー用の大型金型に対応できるサイズのものは日本国内では入手困難だった。新田はさまざまなルートを通じて調査を重ね、ついに海外で適切な大きさの鋼材を見つけ出すことに成功した。
新田
日本国内では適切なサイズの材料が見つからず、さまざまな国の鋼材メーカーを調査しました。ようやく見つけた鋼材によって、加藤さんの卓越した技能を金型に正確に反映させることが可能になりました。
鏡面磨きと漆黒の美の追求
適切な鋼材を得て再スタートした加藤と竹下は、リアロアバンパー用の金型を磨き上げた。その作業には総計で約800時間を要した。
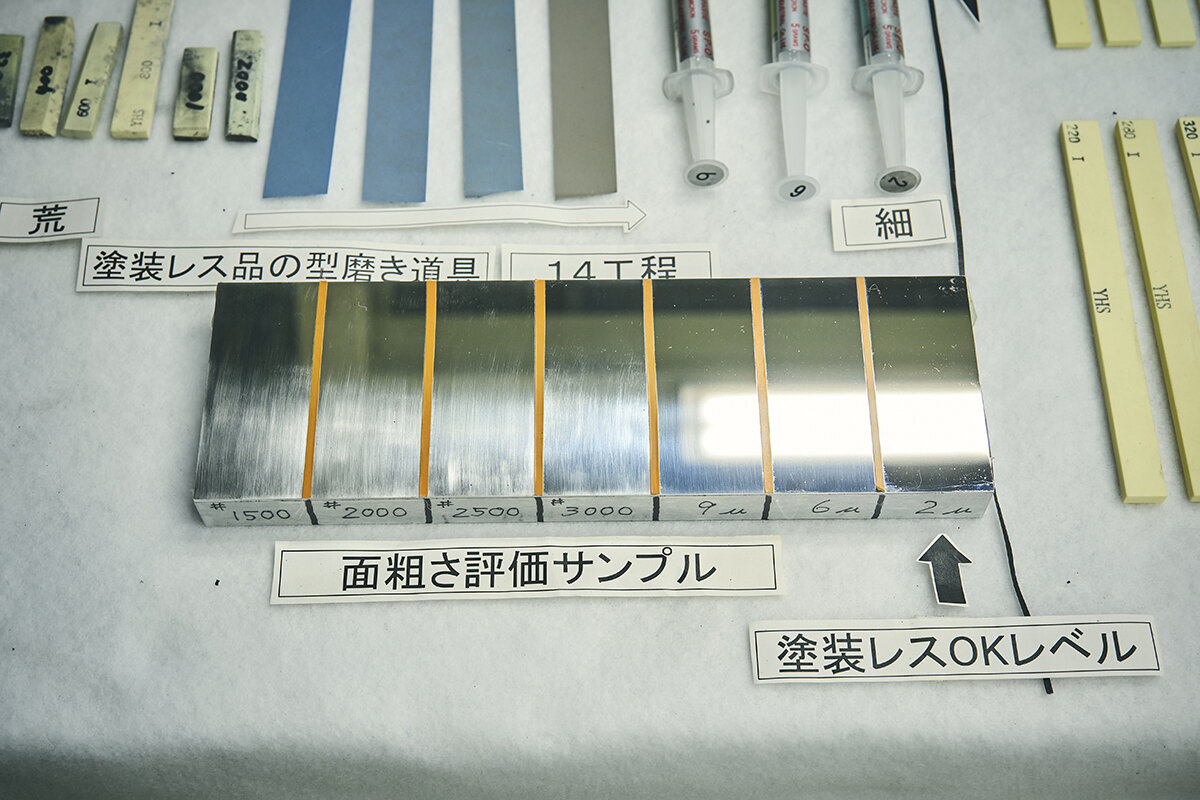
加藤
最も時間を要するのは最初の砥石による下地作りです。この工程が不完全だと、後の工程でどれだけ丁寧に磨いても理想の仕上がりは得られません。基礎となる下地作りに全工程の半分以上の時間を費やしました。
800時間にも及ぶ磨き作業では、肉体的な負担も大きな課題だった。特に砥石を手でつまんで磨く作業は、指や手首に大きな負担がかかる。
竹下
つまんで長時間磨くと、どんどん指先が痛くなってきたり、力も入らなくなってきます。そこで握りやすく力の入れやすいホルダーを開発しました。市販品では理想の角度のものが見つからず、3Dデータを作成し、社内の3Dプリンターで製作しました。
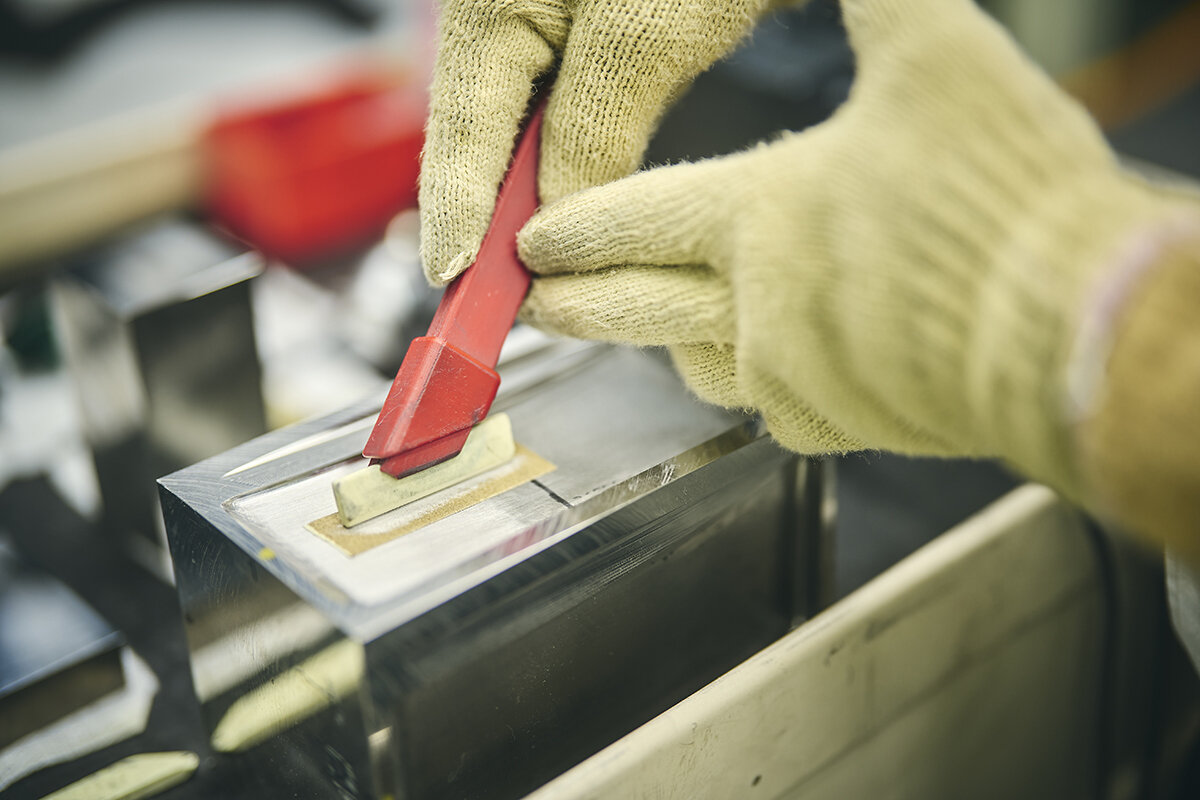
鏡面磨きならではの新たな課題も見えてきた。通常の塗装部品であれば気にならない微細な磨きむらが、鏡面仕上げでは光の反射に影響する。特に、塗装レス樹脂部品の「L値」(漆黒度を表す指標で、数値が小さいほど深い黒を意味する)を高めるためには、金型表面の微細な凹凸を極限まで減らす必要があった。
加藤
鏡面磨きでは、真っ平らに見える面でも、実は微細な凹凸があることがあります。サンドペーパーでの磨き作業では、塗装品なら無造作に擦っても問題ありませんが、鏡面磨きでは同じ力で均一に磨くという繊細な作業が求められます。力の入れ方にムラがあると、表面に微細な凹凸ができ、それが樹脂部品のL値に影響するのです。
金型を使って最初に成形したリアロアバンパーは、目標のL値に達しなかったという。
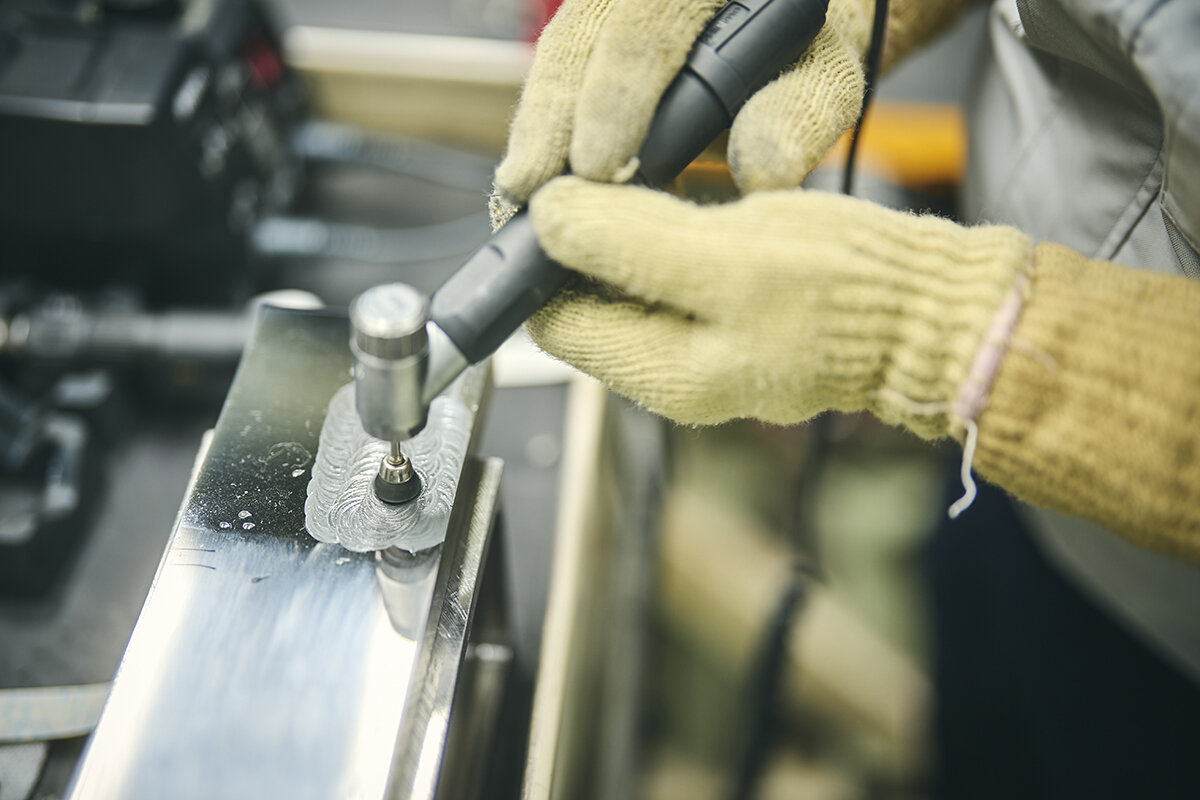
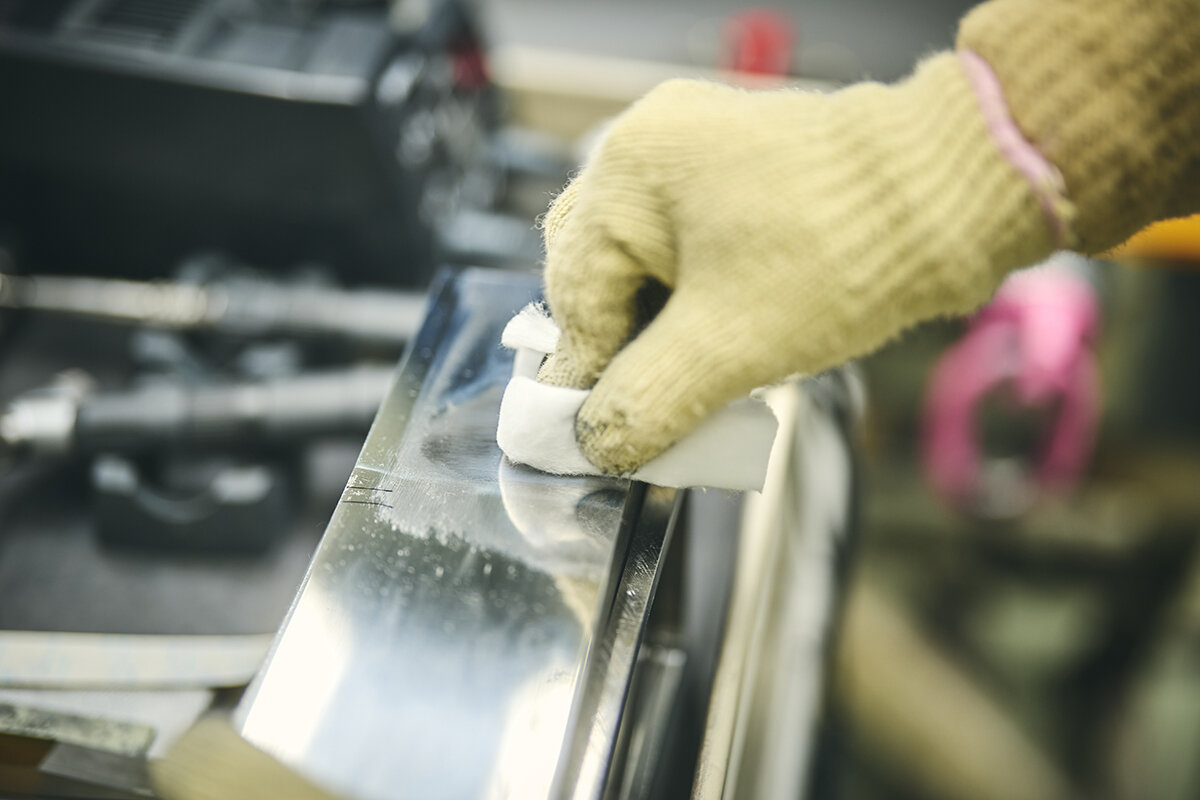
加藤
「これでいいだろう」と思えるまで磨き上げた金型で成形したところ、黒さが足りないとの評価でした。鏡面磨きでは、最初の工程で付いた微細な傷がその後の工程でも影響します。より高品質な仕上がりを目指すには、最初の工程に戻る必要があります。この作業を4回繰り返しました。さらに、サンドペーパー後の最終仕上げにフェルト製のディスクを用い、微細なキズを磨いていきました。フェルト製ディスクでは回転による傷を軽減するため、同じ力で均一に磨くことを心がけ、最後にはコットン素材で手磨きを行いました。このような工程の見直しを繰り返して、ようやく目標のL値を達成できました。
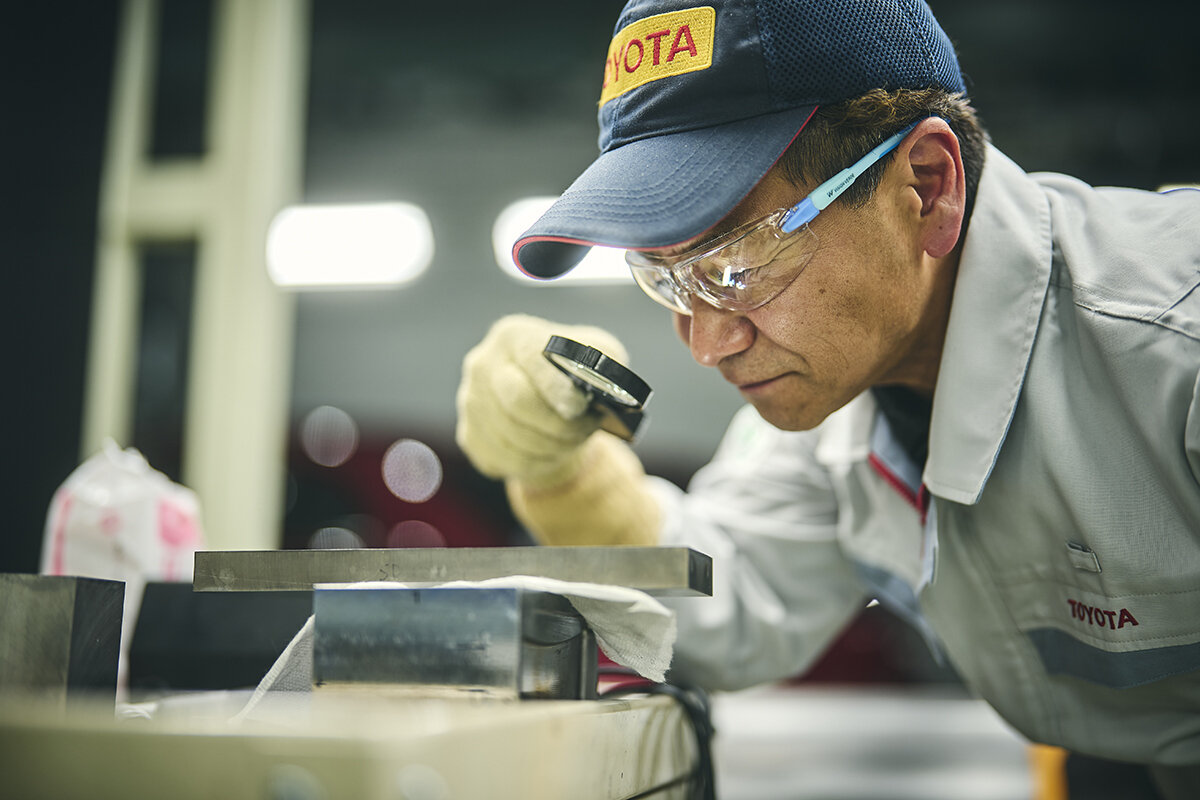
塗装レスバンパーの誕生
幾度もの試行錯誤の末、クラウンスポーツの生産開始3カ月前、ようやく塗装レスリアロアバンパーの実用化が決定した。
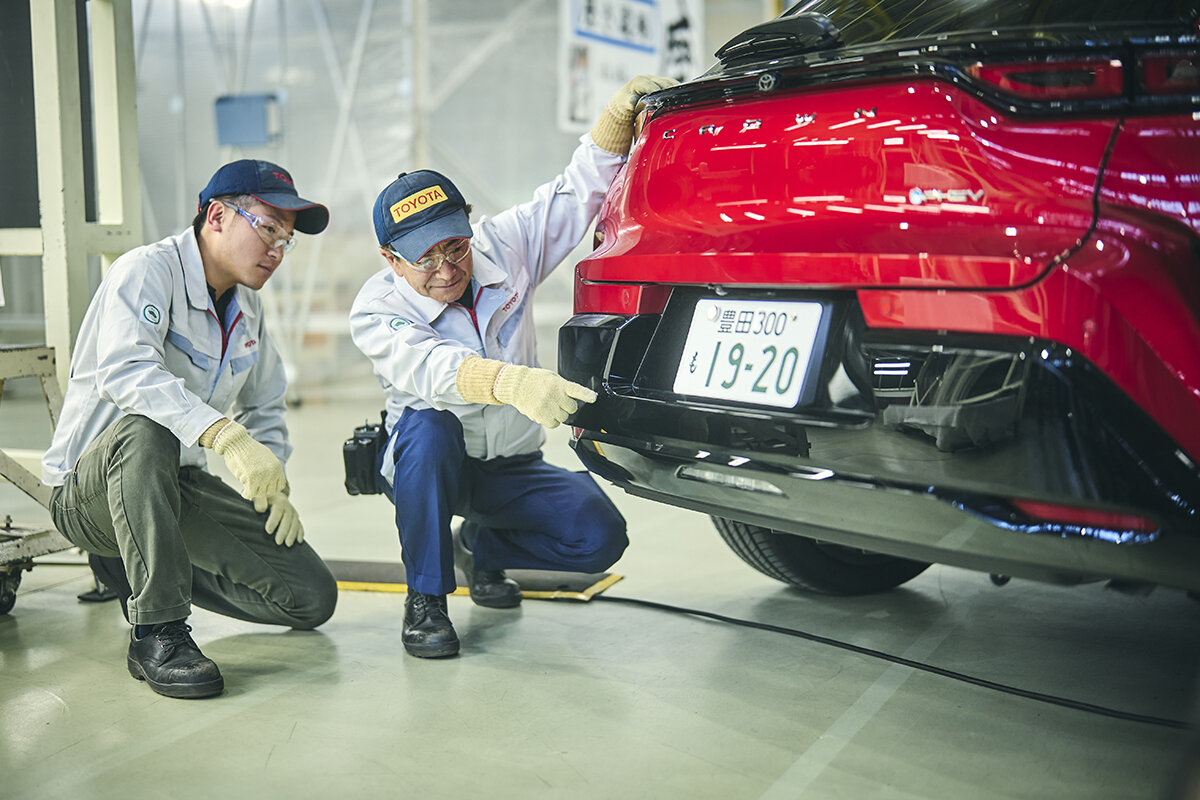
この成果は加藤と竹下の匠の技だけでなく、最適な鋼材を見つけ出した新田、型の設計を担当したモビリティツーリング部のエンジニアである豊田敏彦など、多くの技術者との協働で実現した。
ちなみに、塗装レス用の樹脂材料は光沢感を出すために通常の樹脂よりも固く、流れにくいという特性がある。豊田は樹脂が金型の隅々まで行き渡るよう、樹脂の流入口の数を増やし、また樹脂から出るガスを逃がすための工夫を施した。
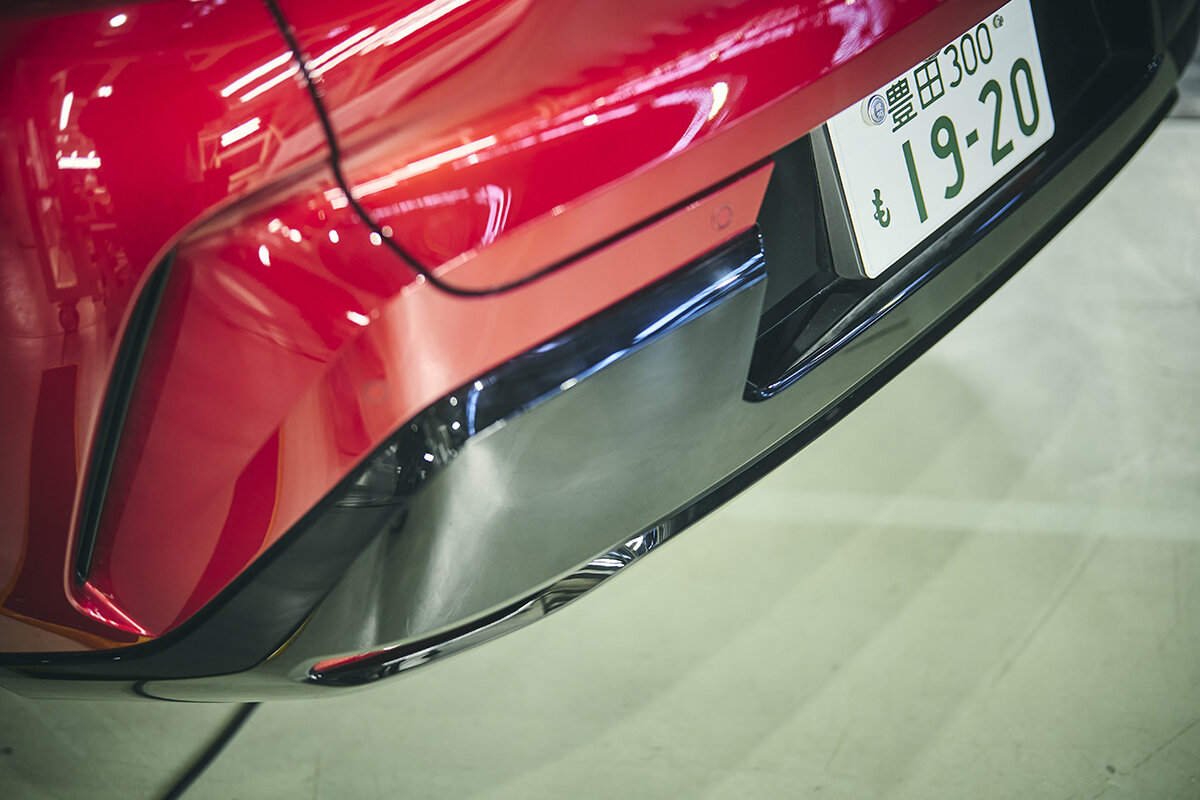
加藤の上司であるモビリティツーリング部の嶋方克好は、環境負荷低減だけでない塗装レス部品ならではのメリットを強調する。
嶋方
まず見た目の美しさについてですが、一般的に柚肌といわれる塗装特有の微かなムラ凹凸がなく、光の反射が自然で滑らかな外観を実現できます。また、塗装レス部品の大きな利点の一つは補修のしやすさです。通常の塗装部品は傷がついた場合、該当箇所の塗装を剥がして再塗装する必要がありますが、塗装レス部品は材料自体が着色されているため、傷ついた部分を磨くだけで元の状態に戻すことができます。市販のコンパウンドで簡単に修復できるのも大きな特徴です。
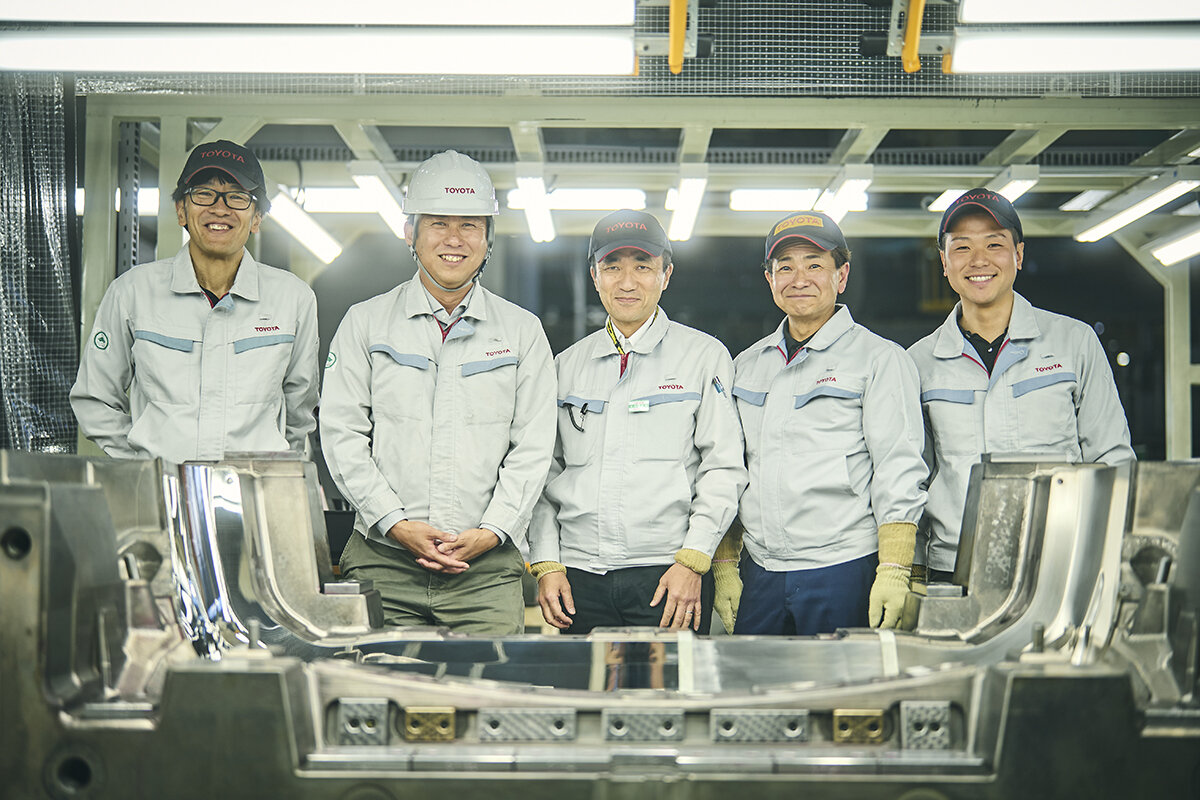
技能伝承が使命
加藤は現在、自らの技能を若い世代に伝えることに力を注いでいる。
加藤
技術の継承は私の重要な使命だと考えています。この分野の匠を一人でも多く育成することで、より多くの高品質な製品を生み出すことができます。限られた人数での作業では対応できる範囲に限界がありますが、同じ技術を持つ人材が増えれば、より広範な製品開発に貢献できます。
現在、鏡面磨きができる職人は5人まで増えており、さらに2人ほど増やすことを目指している。
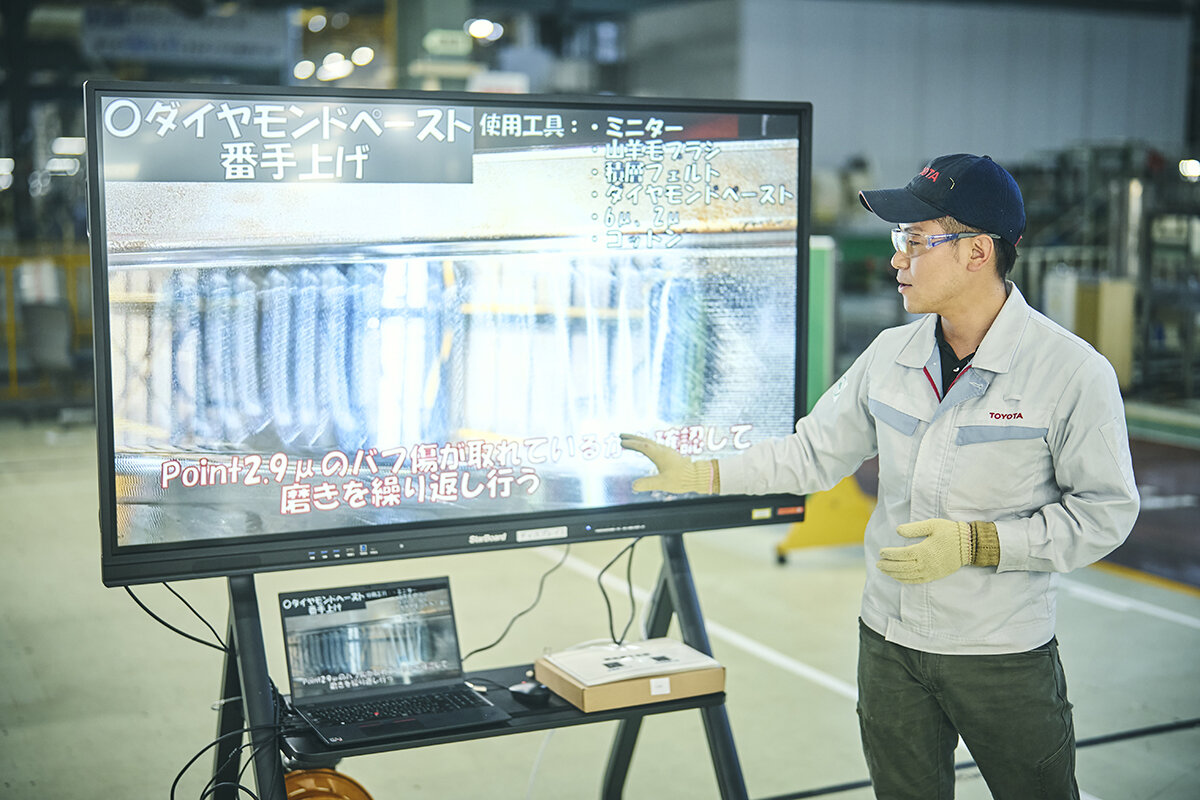
竹下は、匠の技を映像で記録することで技能伝承を効率化する取り組みも行っている。
竹下
匠の技能を伝承する際の課題は、言葉だけでは技術の微妙なニュアンスを伝えることが難しい点です。そこで作業の様子を動画撮影し、各工程の重要ポイントにコメントを追加したレクチャー動画を制作しました。若手技術者が作業のイメージを事前に掴めるようになり、技術習得の効率が向上しました。
クラウンスポーツのリアロアバンパーで実現された塗装レス技術は、今後さらに広がる見込みだ。現在は黒色のパーツに限られているが、白色へのチャレンジも計画されているという。
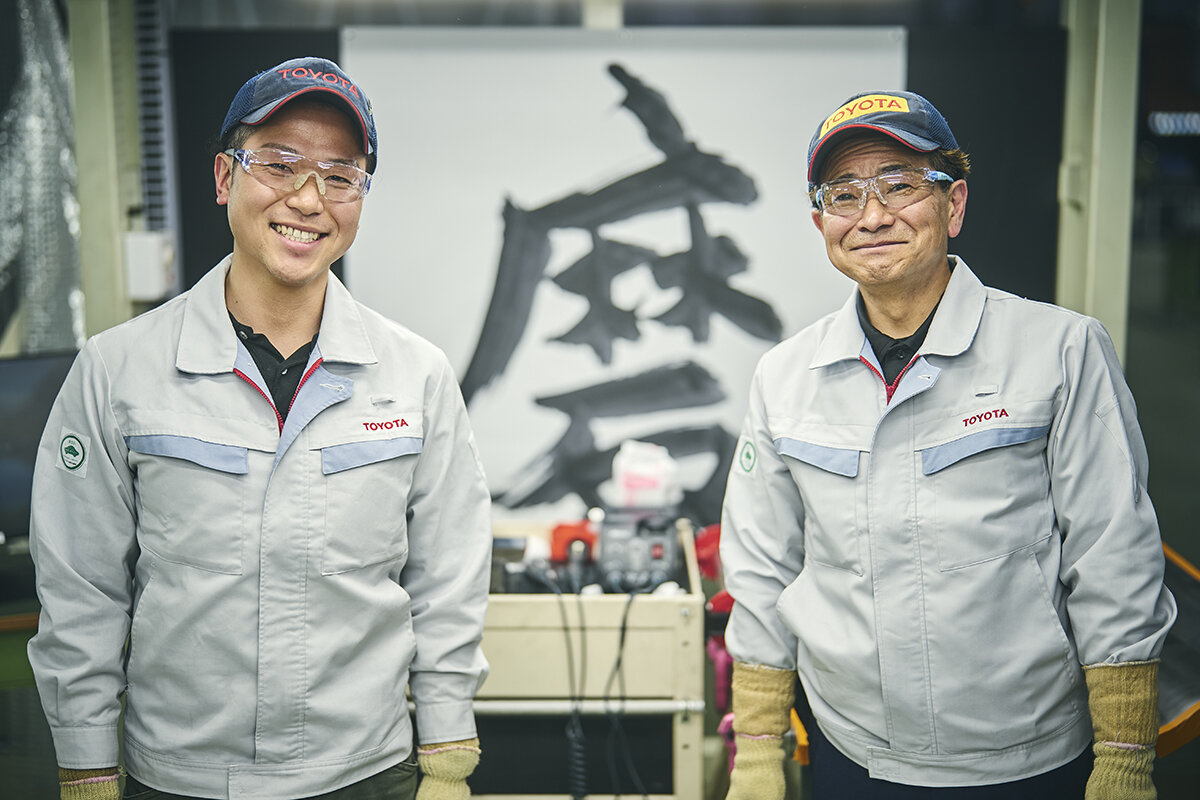
金型一筋40年のキャリアによって培われた加藤の匠の技と指の感覚は、テクノロジーが進化する現代においても、機械では代替できない価値を持っている。その繊細な技が一つのバンパーを通して、環境に優しいクルマづくりに貢献している。カーボンニュートラル時代の自動車製造において、匠の技が重要性を増している好例といえるだろう。加藤の技と後進育成への情熱は、今後も目には見えないところで私たちの未来のモビリティを支えていくことだろう。