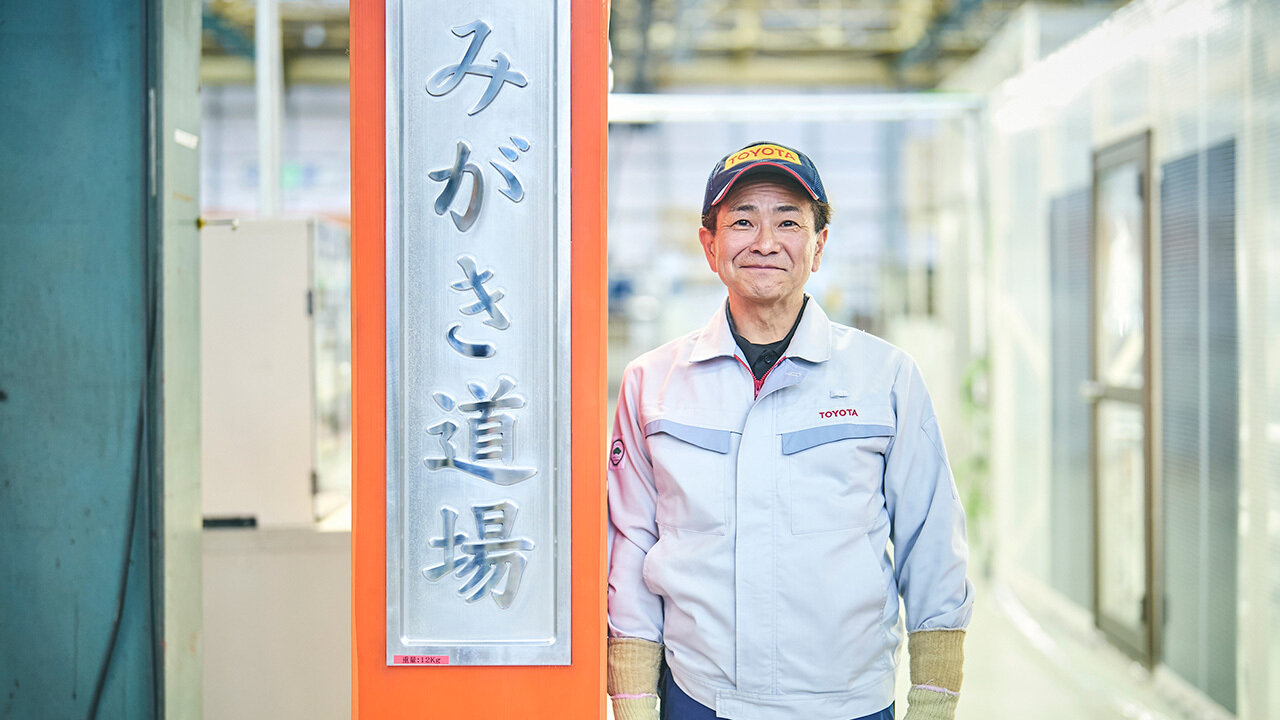
自動車業界を匠の技で支える「職人」特集。第20回は金型を鏡面のように磨き上げ、トヨタ初の塗装レスバンパーを実現した「金型磨きの匠」に話を聞く
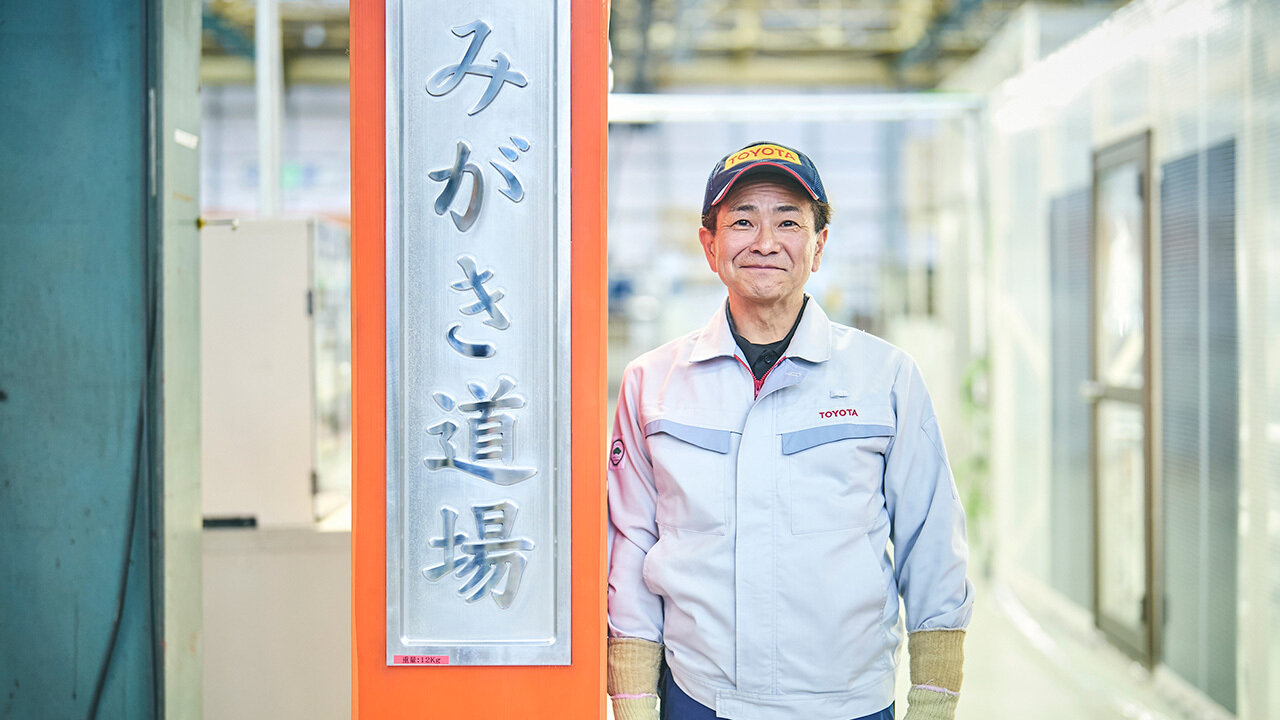
3DプリンターやAIをはじめとするテクノロジーの進化に注目が集まる現代。だが、クルマづくりの現場では今もなお多数の「手仕事」が生かされている。
トヨタイムズでは、自動車業界を匠の技能で支える「職人」にスポットライトを当て、日本の「モノづくり」の真髄に迫る「日本のクルマづくりを支える職人たち」を特集する。
今回は、クラウンスポーツのリアロアバンパーを塗装レス化するため、樹脂成形用金型の表面を鏡面のように磨き上げる技能を極めたモビリティツーリング部の加藤英樹の前編をお届けする。
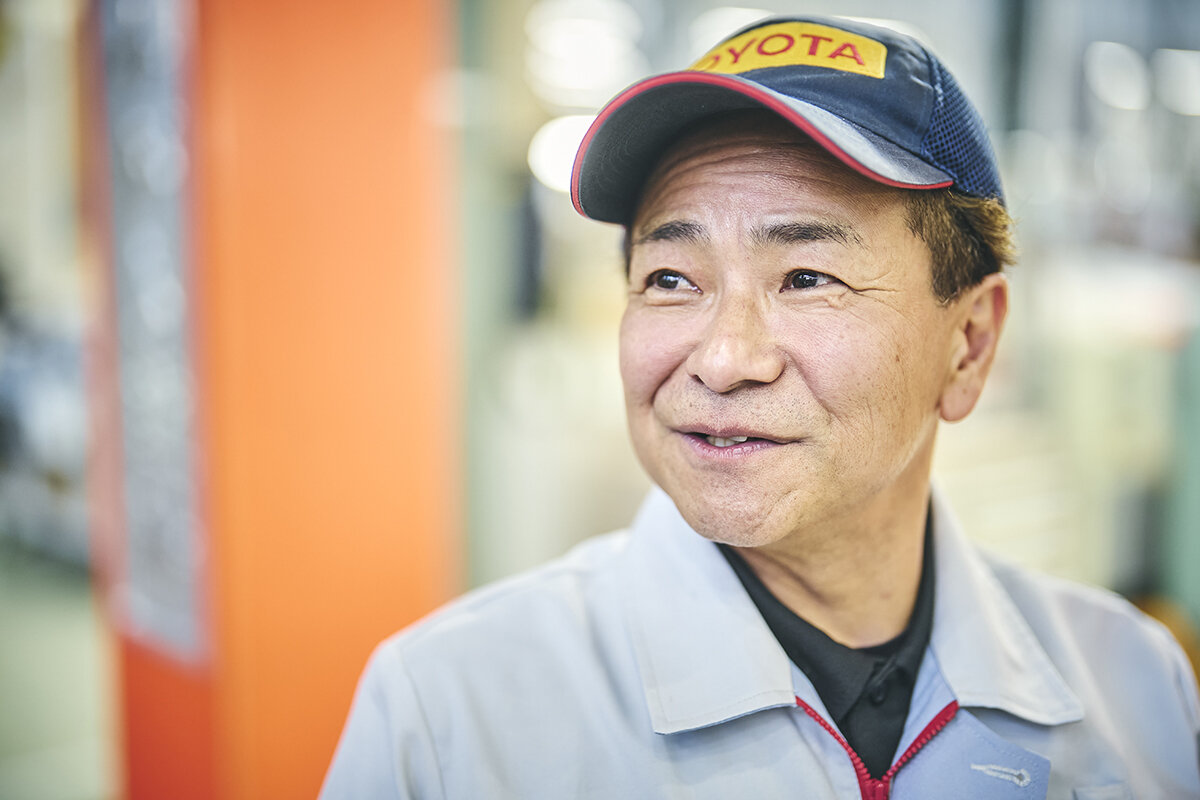
第20回 樹脂成形用金型を手作業で磨き上げる「金型磨きの匠」加藤英樹
トヨタ自動車モノづくり開発センター モビリティツーリング部 シニアエキスパート
40年の経験を経て匠の領域に
愛知県豊田市の貞宝工場。クルマのボディやバンパーなどをつくるための金型を設計・製作する拠点の一つだ。工場内の一角に置かれたクラウンスポーツのリアロアバンパー用の金型(試作時のもの)は、まるで鏡のように表面が磨き上げられている。
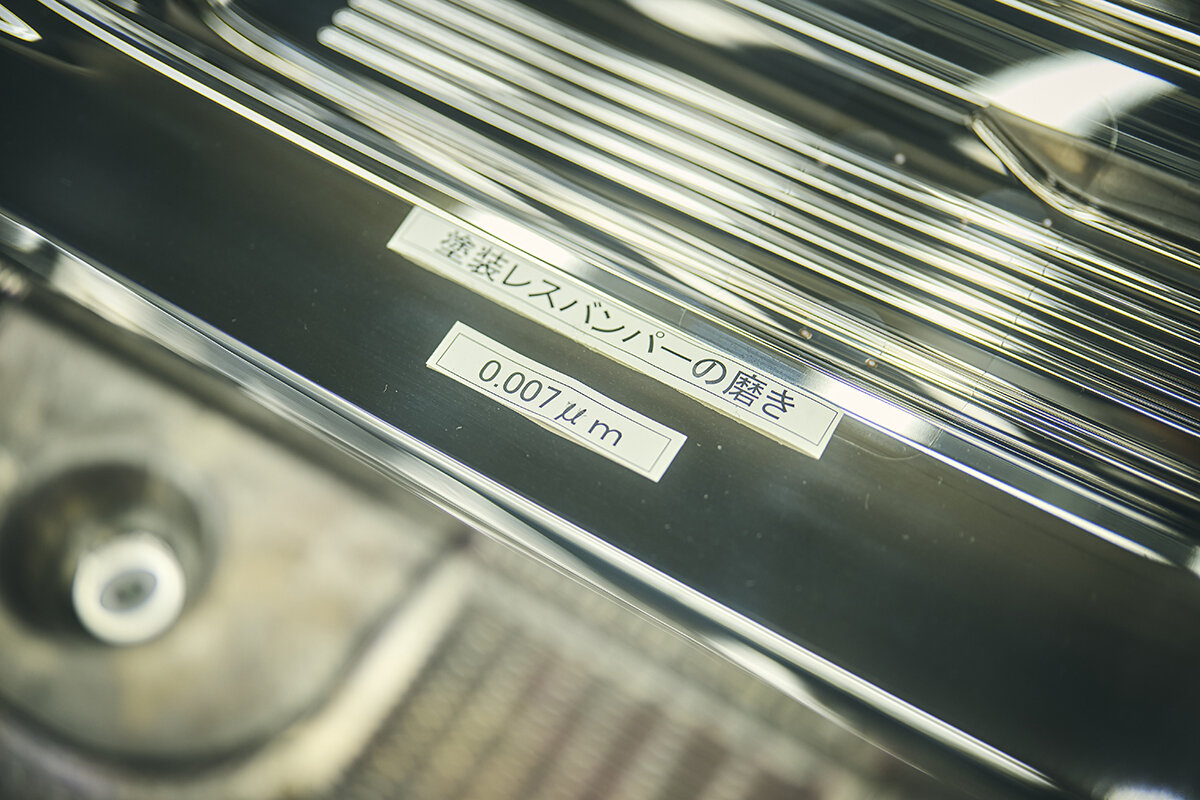
金型とは、樹脂や金属などの材料を成形するための型のことだ。鋼材を鋳造もしくは鍛造してつくられた金型素材を、まず切削機械でデータに忠実な形に削り出す。その後、表面を砥石やサンドペーパーで丁寧に磨き上げる。この最後の磨き工程を手作業で極めた匠が、加藤英樹である。
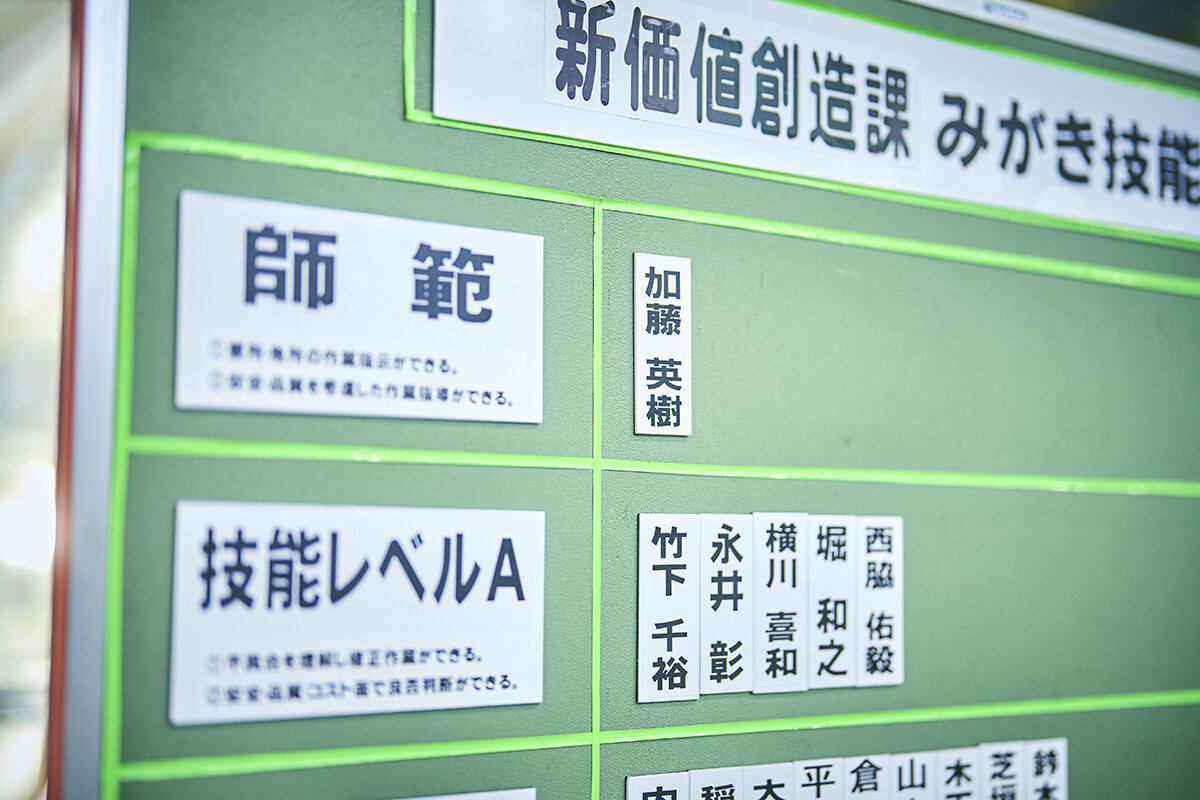
加藤が籍を置く新価値創造課の磨き技能レベルでは、加藤は最高位の「師範」に位置する。匠とも呼ばれるその領域に到達するには、30年以上の経験が必要だという。
現在57歳の加藤は、幼い頃からモノづくりの才能を示していた。岐阜県中津川市の出身で、子どもの頃からプラモデル作りに熱中していたという。
加藤
クルマ好きでしたね。小学校の頃からプラモデルづくりが好きで、トヨタ2000GTは特に思い出に残っています。
中学卒業後、地元の担任教師からの勧めもあり、トヨタ工業高等学園(現 トヨタ工業学園)への進学を決めた。
加藤
当時の担任の先生が「こういう学校があるけどどうだ」と勧めてくれたんです。最初は軽い気持ちでしたが、給料をもらいながら勉強もできて、将来は自動車会社に就職できるという点に魅力を感じました。
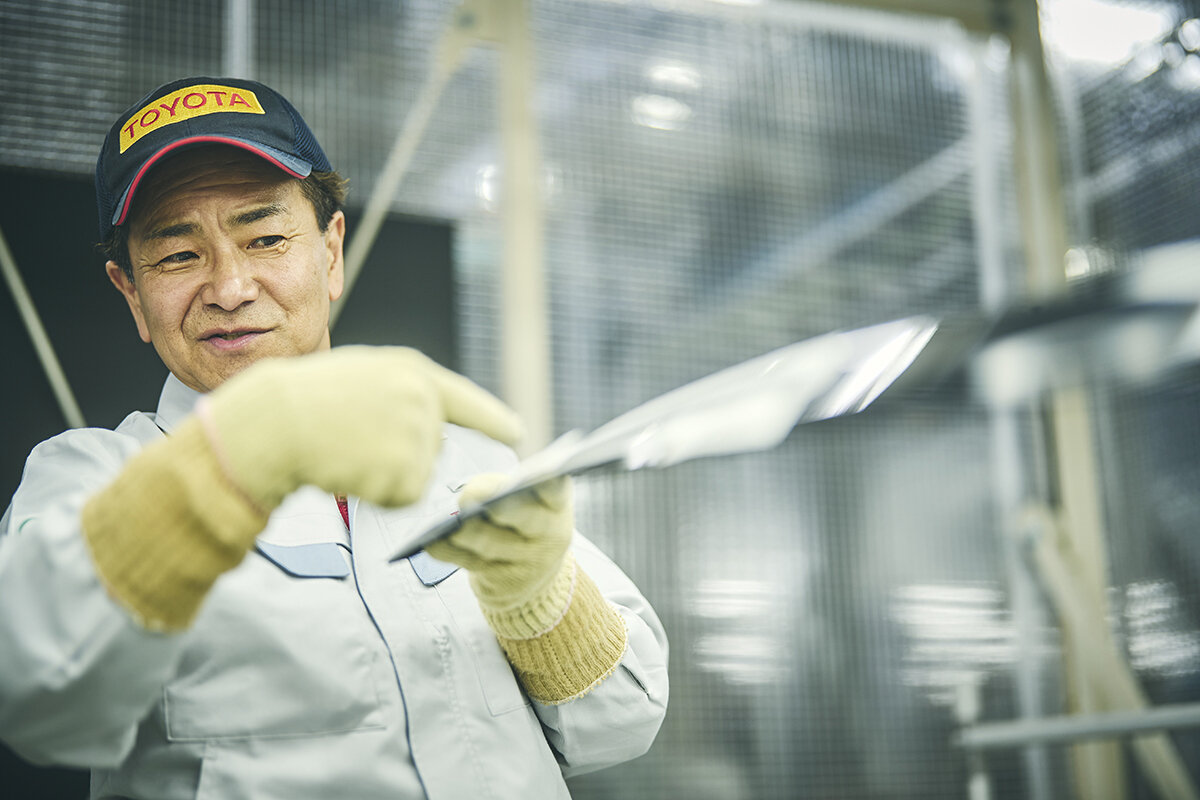
16歳の時から学園生として学びながら、1986年にトヨタ自動車に入社。入社後は樹脂型の仕上げ組み付けを担当することになった。当時は機械加工の精度も現在のようには高くなく、ほとんどの工程を手作業で形状を作り上げる必要があった。
入社当初、加藤はクルマづくりの現場について、想像していたものとの差に驚いたという。
加藤
入社前はクルマそのものに関わる仕事をするのだと思っていました。ところが実際の現場では鉄の塊を削ったり、重量物をクレーンで運んだりする作業が主でした。製造現場にはクルマが一台も見当たらず、想像していた仕事とは異なる印象を受けました。
しかし、先輩たちの仕事ぶりを見るうちに、金型磨きの世界に引き込まれていった。
加藤
先輩方の仕事の仕上がりに惹かれました。溶接や仕上げ、磨きの技術はどれも見事なものでした。当時は技術を親身に教えてもらうことは難しく、先輩の作業を注意深く観察して学ぶしかありませんでした。どうすれば同じ技術を身につけられるか、その方法を模索するようになりました。
当時の職人文化では「自分の技は自分で磨け」という考え方が主流だった。加藤は先輩の仕事を注意深く観察し、その技を少しずつ自分のものにしていった。そんな中、25歳頃に印象深い経験をしたという。
加藤
フロントグリルの金型加工をミスしてしまい、どうしても機械加工ではやり直しが効かないような状態になってしまったのです。そこで手加工ですべての形状を作り込みました。グリルの格子の一番奥の細かい意匠まで、1カ月くらいかけて仕上げました。
こうした金型に向き合い続けた日々が彼の技術を一段と高めることになった。
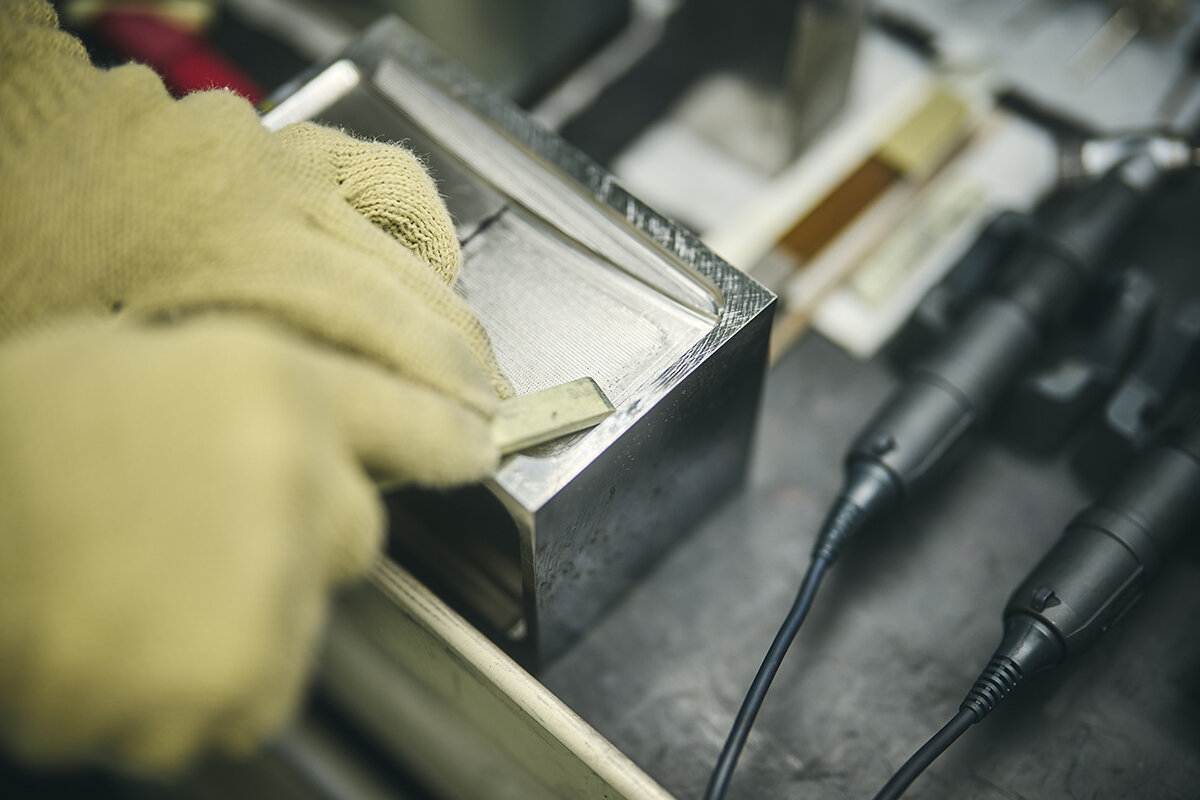
加藤
そのときは上司にも褒めていただき、そこから私は『磨きが上手いじゃないか』という評判も上がって、海外出張にも行かせてもらえるようになりました。
加藤のキャリアにおいて、国際的な経験は重要な位置を占めている。北米、英国、南アフリカ、中国など世界各国の生産拠点で、樹脂型の整備や不具合修理のための出張を経験してきた。2016年には中国へ短期出向し、樹脂型の現地調達化支援として人財育成にも携わった。
加藤
海外では頼れる先輩も同僚もおらず、すべてを自分の判断と技術で解決しなければなりませんでした。特に現地の成形工場には専用の加工機械がないため、すべて手作業での対応が求められました。そのような状況で任された仕事を完遂できたことが、技術者として更なる自信となりました。
また海外での指導では、まず一緒に作業をしながら重要なポイントを示すようにしました。ローカルスタッフは基本的な作業はできるものの、細部まで理解していないことが多い。そこで実際にやらせてみることで理解度を確認し、必要な技術を伝えていきました。
塗装レスバンパーへの挑戦
2020年頃、トヨタはカーボンニュートラル社会実現の一環として塗装レスの大型部品開発に着手した。塗装工程は工場のエネルギー使用量の40〜50%を占め、そのほとんどが乾燥工程で使われていた。また、塗装からは多くの廃棄物も出るため、環境負荷低減とコスト削減の両面から重要な取り組みだった。
製品化製造技術部(当時)の新田翼から、クラウンスポーツのリアロアバンパーを塗装レスにするプロジェクトの相談を受けた加藤は、弟子の竹下千裕とともに、前例のない挑戦に取り組むことになった。
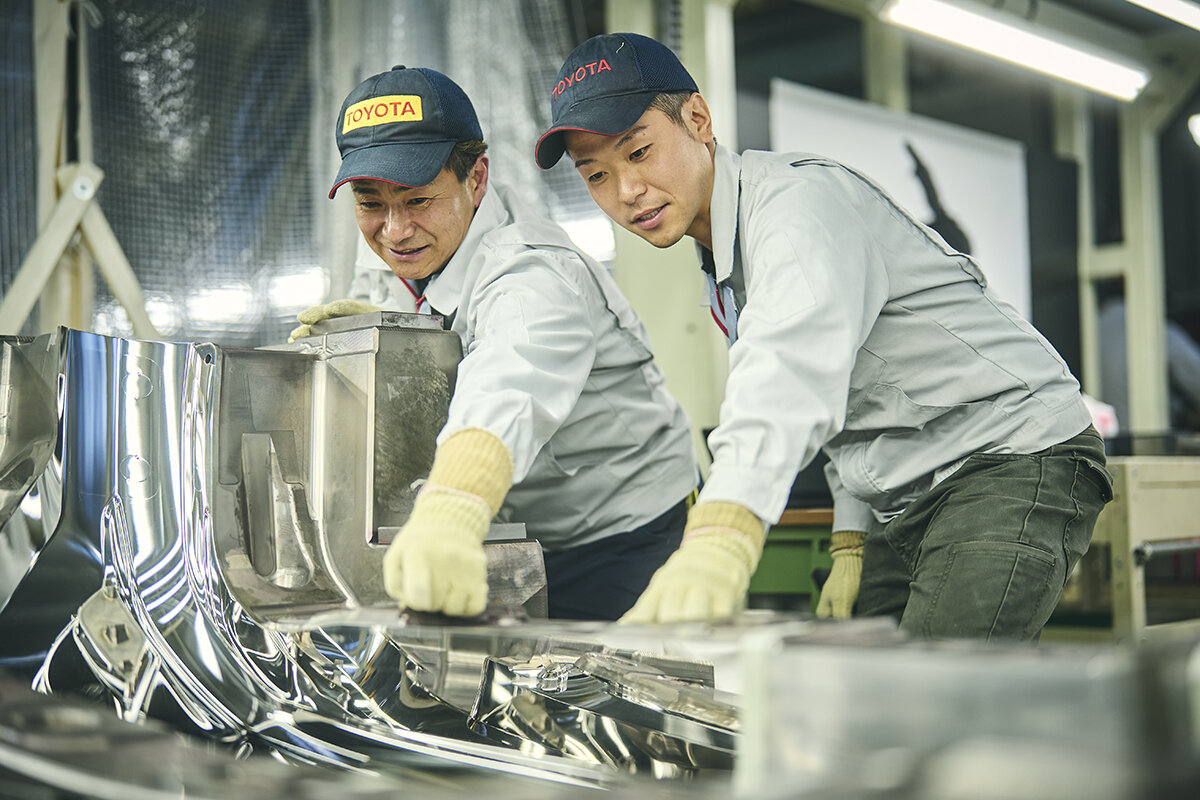
竹下は2013年に入社し、技能レベルA級(師範の一つ下のランク)まで成長した若手である。
塗装レス技術自体は新しいものではなく、Bピラーやガーニッシュなど比較的小さな部品ではすでに実用化されていた。しかし、リアロアバンパーのような大型部品への適用は前例がなかった。大きな部品では、表面の均一性を保つことが難しく、わずかな歪みや傷が目立ちやすいからだ。
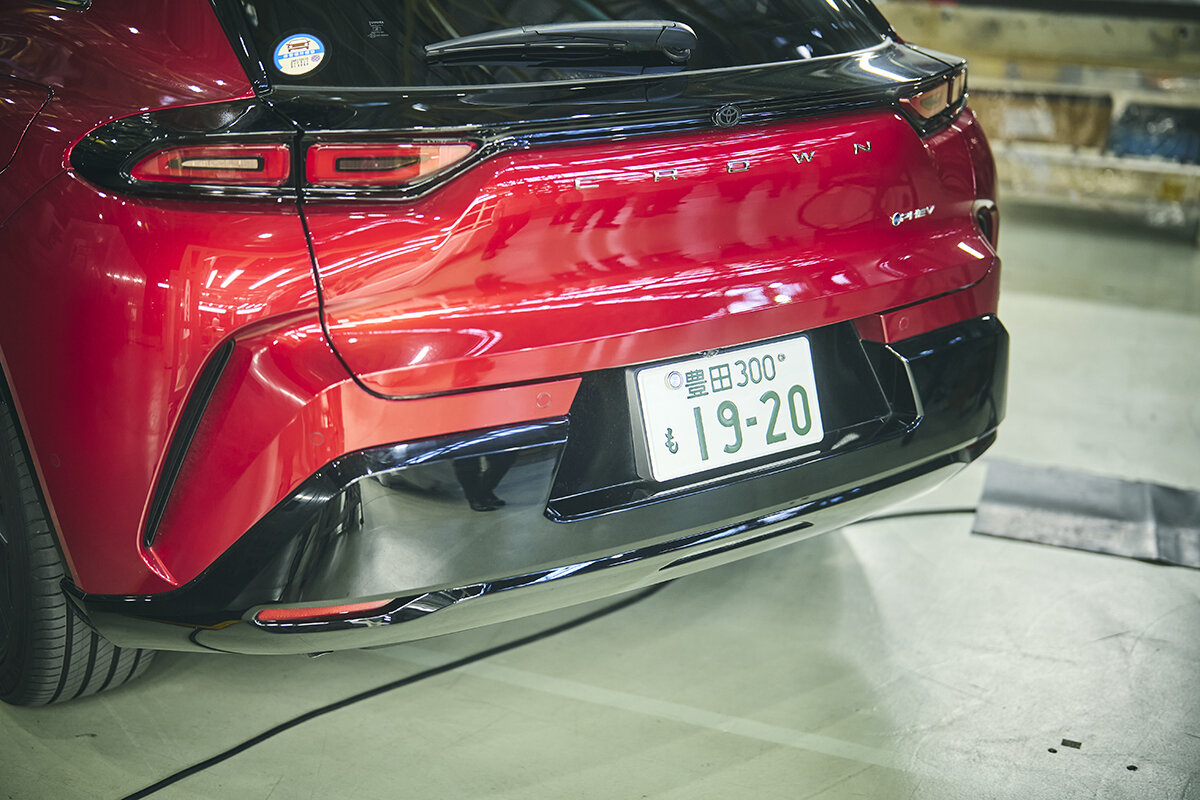
また、金型のサイズが大きくなるほど、適切な材料の入手や磨きの工程も難しくなる。一方で、大型部品を塗装レス化することで、より多くのCO2排出量とコストを低減できるというメリットがある。
加藤が極めた金型磨きの技能の中でも、最も難しいのはデザイナーが描いた通りの形状を金型に正確に作り込むことだ。どんなに金型の表面を美しく磨いても、形状が正確でなければ製品として成立しない。
加藤
私たちの仕事の本質は、デザイナーが考案した形状を金型に忠実に再現することです。まず金型の3Dデータを詳細に分析し、形状を頭の中でイメージします。次に指先の感覚を使って、金型表面の微細な凹凸を把握し、必要な部分を砥石で精確に削り出していきます。
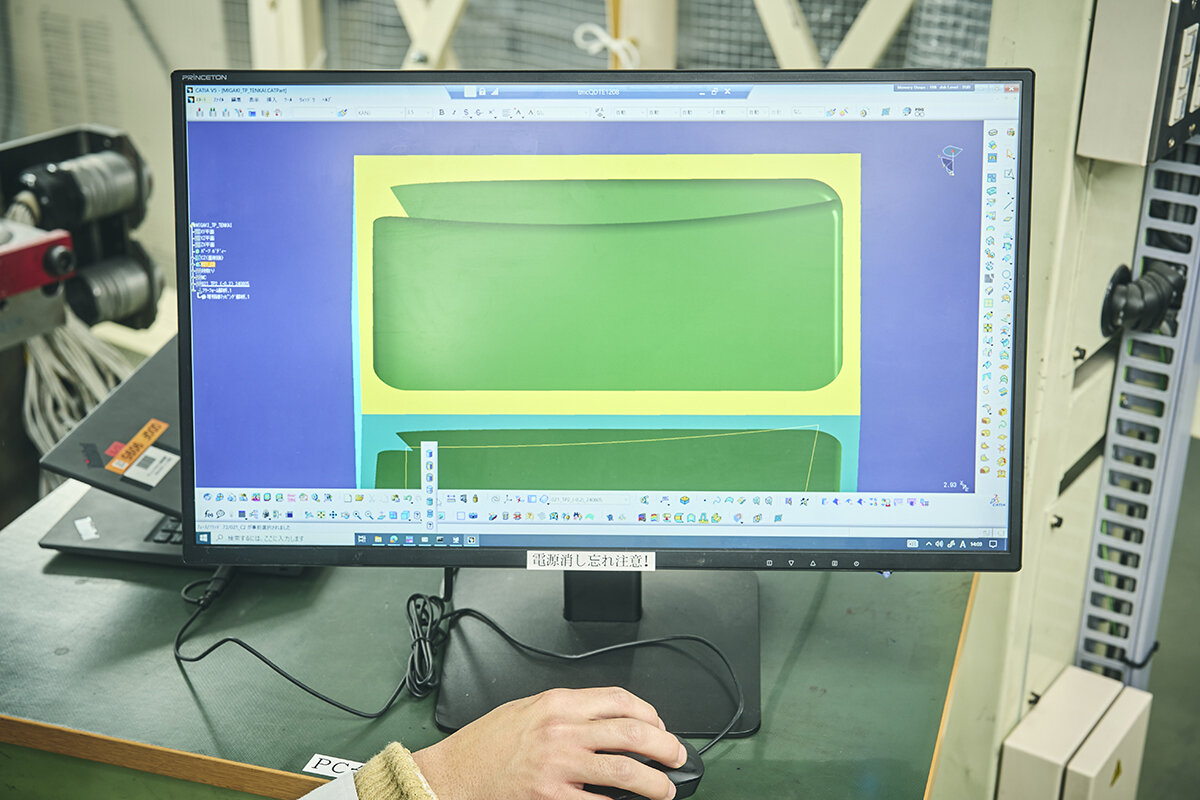
特に大型部品では、形状の正確さと表面の美しさを両立させることが極めて難しい。加藤は続ける。
加藤
大きな部品になればなるほど、磨き上げることと形状を再現することは相反する課題になります。磨けば磨くほど表面は美しくなりますが、同時に形状が崩れるリスクも高まります。一箇所だけ少し凹んでしまったり、エッジが丸くなったりすると、デザイナーの意図した形状から外れてしまう。私たちの仕事は、デザイナーが思い描いた形を一切損なうことなく具現化しながら、同時に完璧な鏡面に仕上げることなのです。
この技能を言葉で説明するのは非常に難しい。加藤は形状を確認する際、軍手を着用している。
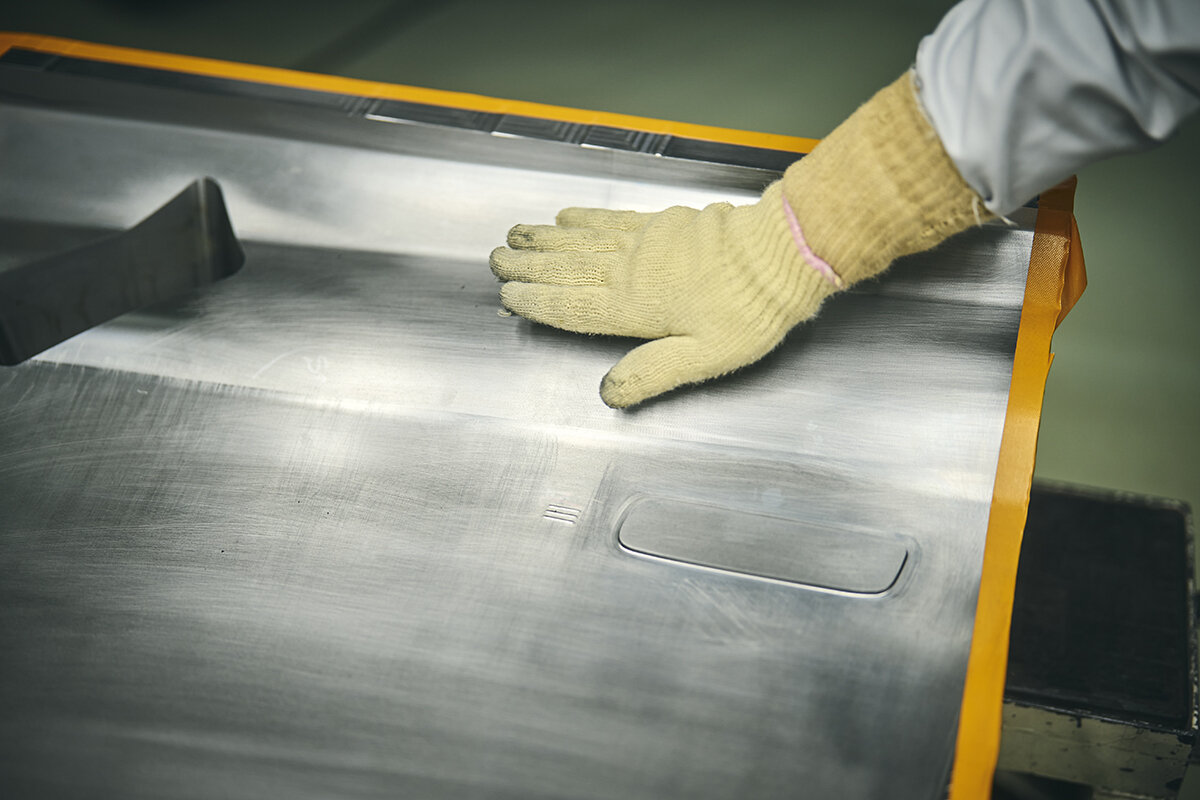
加藤
金型の凹凸を見るときは素手ではなく、軍手をつけたまま行います。指と型の間に軍手という薄いクッションがあることで、滑りがよく、段差を感じ取りやすくなります。
加藤の指は、5ミクロン(0.005mm)程度の微細な凹凸まで感じ取ることができる。この優れた感覚を駆使して、デザイナーの意図通りの形状を金型に作り込んでいくのだ。磨きの工程では、さらに2ミクロン程度の微細な傷まで磨き上げることになる。
通常の塗装部品の場合、金型表面に多少の磨き筋があっても塗装で隠れるため問題にならない。しかし塗装レスにすると、金型の表面形状がそのまま部品に転写されるため、金型をキズ一つない鏡面のように磨き上げる必要があるのだ。
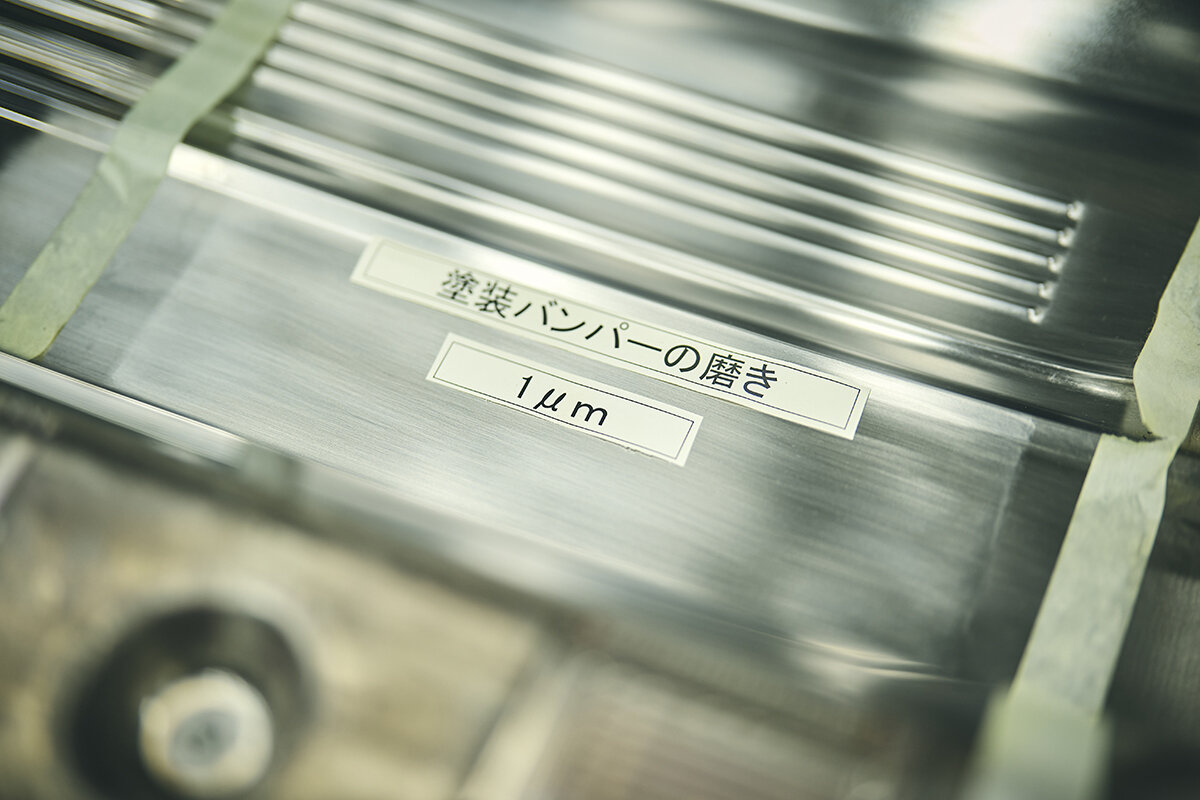
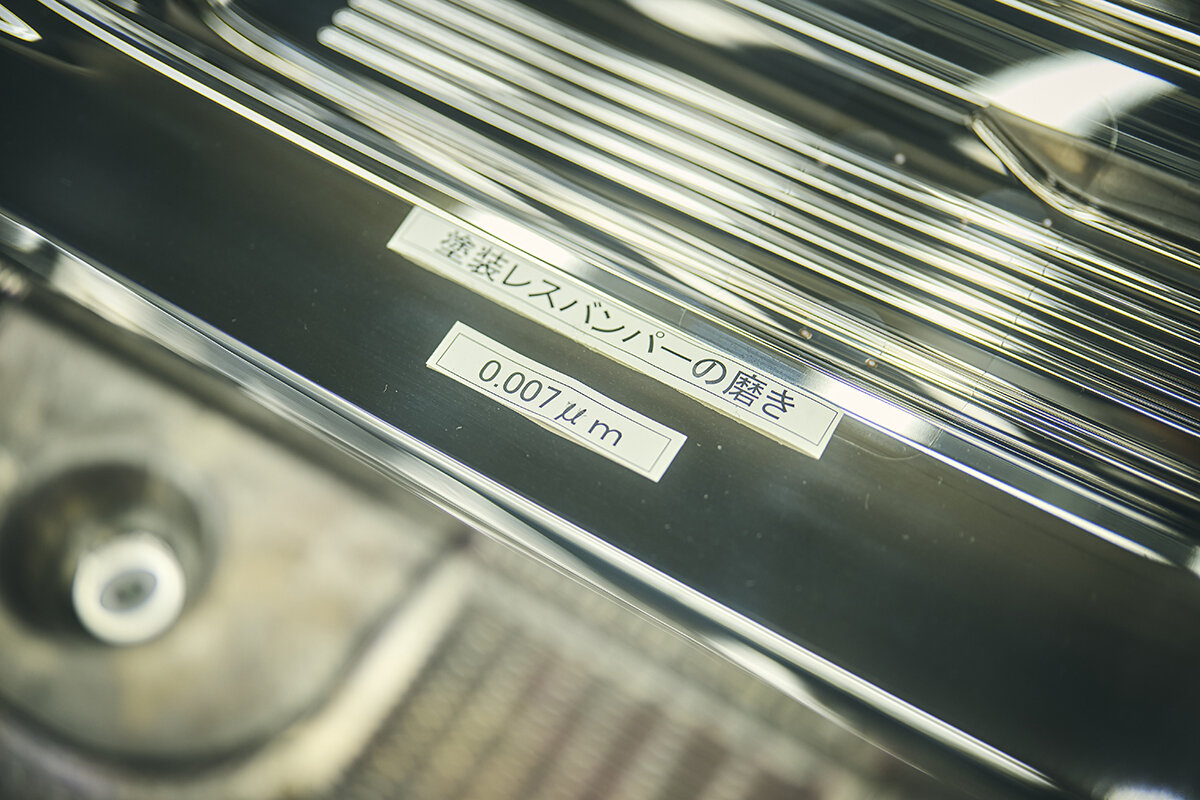
加藤
塗装レスバンパーを実現するには、鋳造型ではなく鍛造型を採用しました。鋳造型の場合、溶けた金属を流し込んで固める過程で微細な鋳巣が発生します。一方、鍛造型は金属をプレスして作るため、そのような巣がなく、加工後も滑らかな表面を実現できます。
後編では、塗装レスバンパー実現への壁となった金型素材の問題、800時間に及ぶ鏡面磨きの取り組み、そして次世代への技の伝承についてお伝えする。