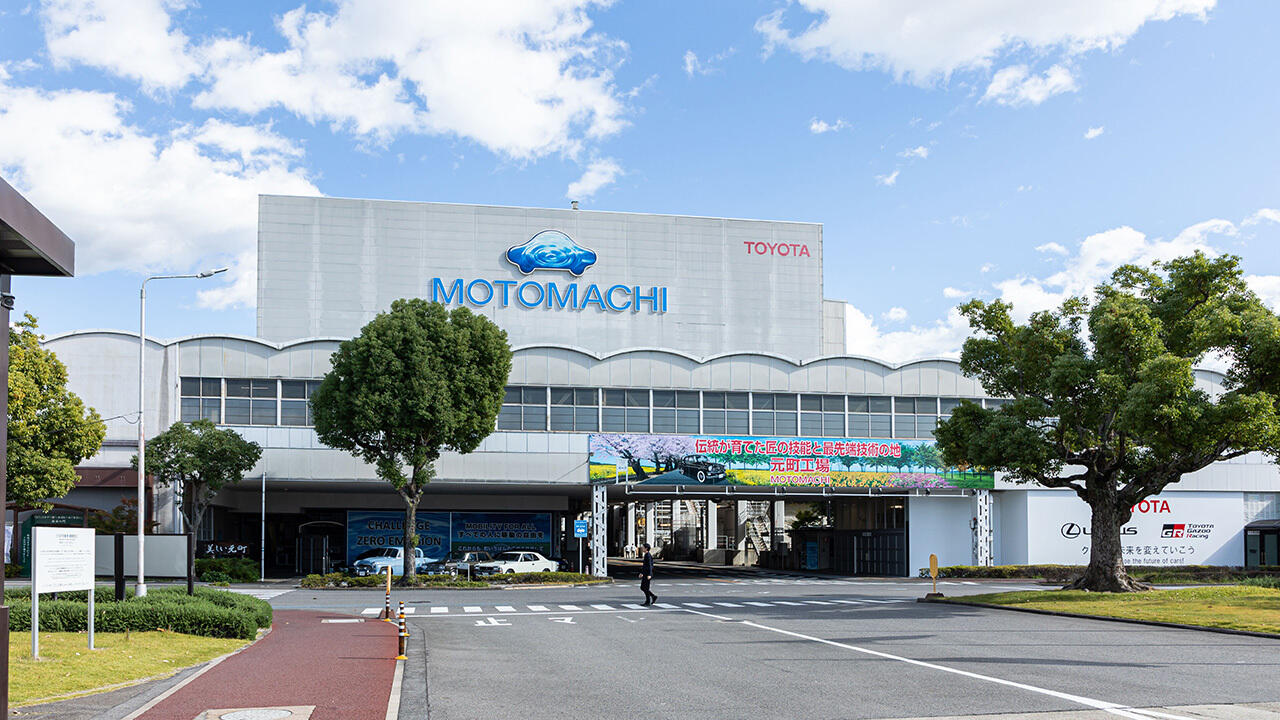
多様化の時代に、多様な人づくりで立ち向かう元町工場。変化に対応するだけで終わらせない、変化をつくりだす挑戦を追った。
モノづくりに技能で変化をつくりだす
「『人中心』のマルチパスウェイ」の実現に向き合い続ける元町工場。宮部工場長は言う。
宮部工場長
「安全で、高品質で、魅力あるクルマを未来永劫つくり続けられる方法なんてありません。常に変化との戦いです。変化に対応する力だけでは不十分。自ら変化をつくりだせる力が重要になる。工程やクルマをよく知る現場が自分たちの手で変化させ続けることが必要です」
ここからは、「変化をつくりだす」ため、さまざまな領域で可能性を切り開く現場を取り上げていく。
2022年、WRC(FIA世界ラリー選手権)史上最年少記録となる22歳と1日でドライバーズチャンピオンに輝いたのが、TOYOTA GAZOO Racing World Rally Teamのカッレ・ロバンペラ選手。
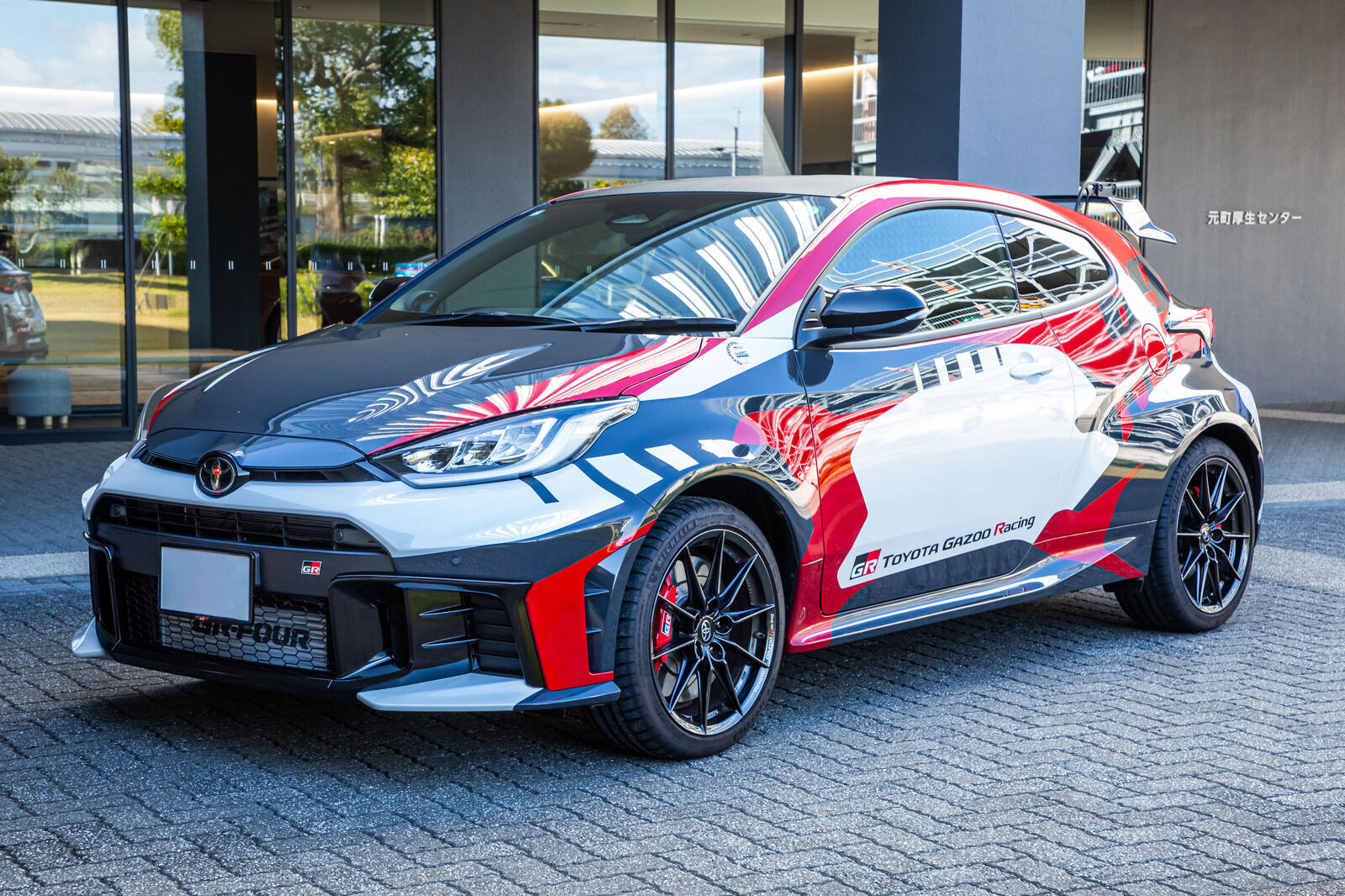
選手への感謝とTGRによるWRCの取り組みを盛り上げたいというモリゾウの想いから限定100台で売り出されたGR Yaris Kalle Rovanperä Editionは、赤・黒・白の3色のカラーリングが特徴的な一台だ。
驚かれるかもしれないが、実はこのカラーリング、すべてステッカーではなく塗装で仕上げられている。
手がけたのは元町工場の塗装チーム。まず全体を白で塗装し、その上から、スキージと呼ばれる型を使って、赤くしたい部分を残してマスキングし、塗装をかける。最後に黒で同様の塗装を施して仕上げるなど、非常に手が込んでいる。
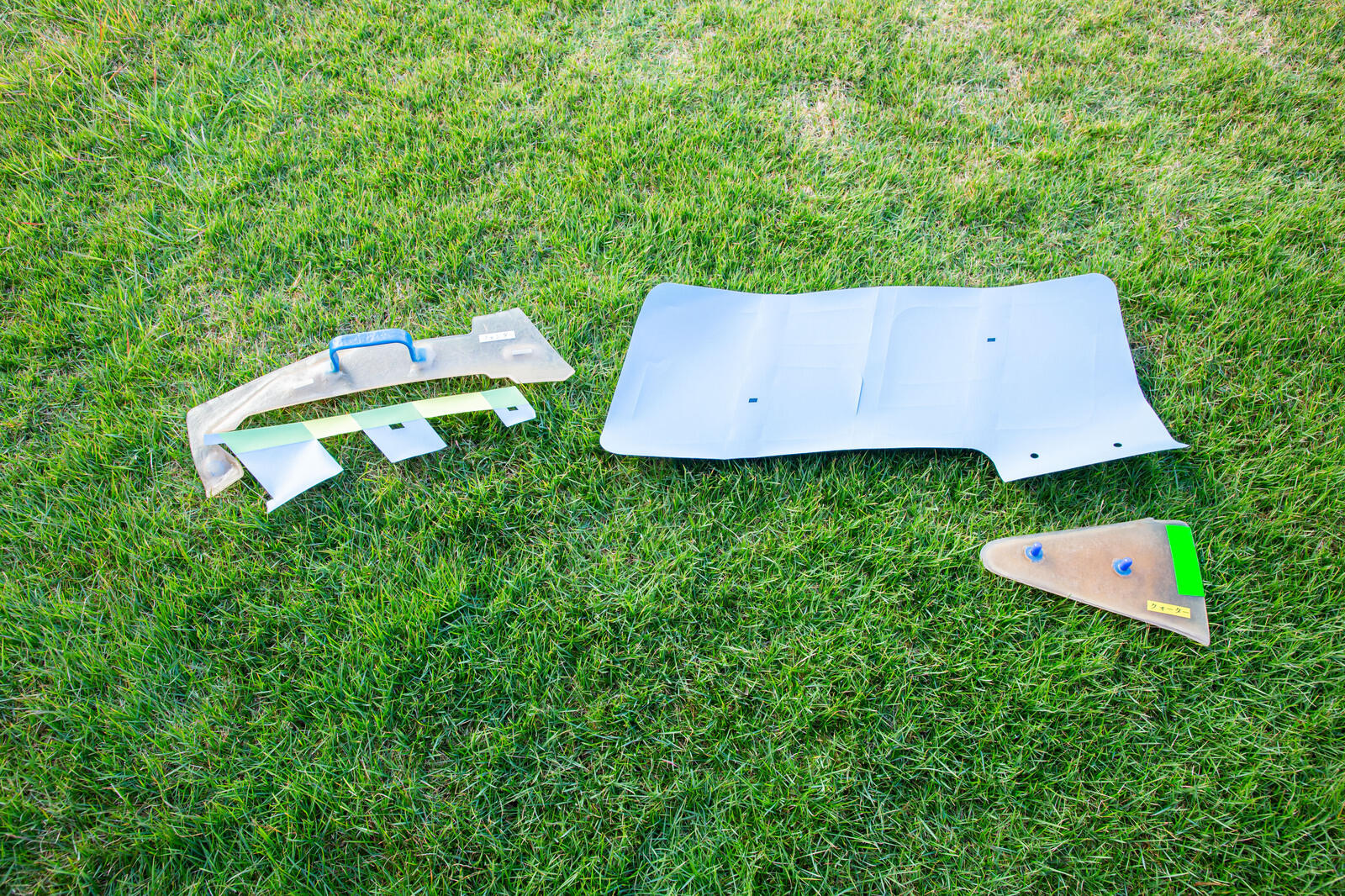
しかも、車体とバンパーの塗装は別々につくった上で、最後に組み合わせるため、模様にズレが生じないようそれぞれの工程で密に連携し、ミリ単位での調整を行ったという。
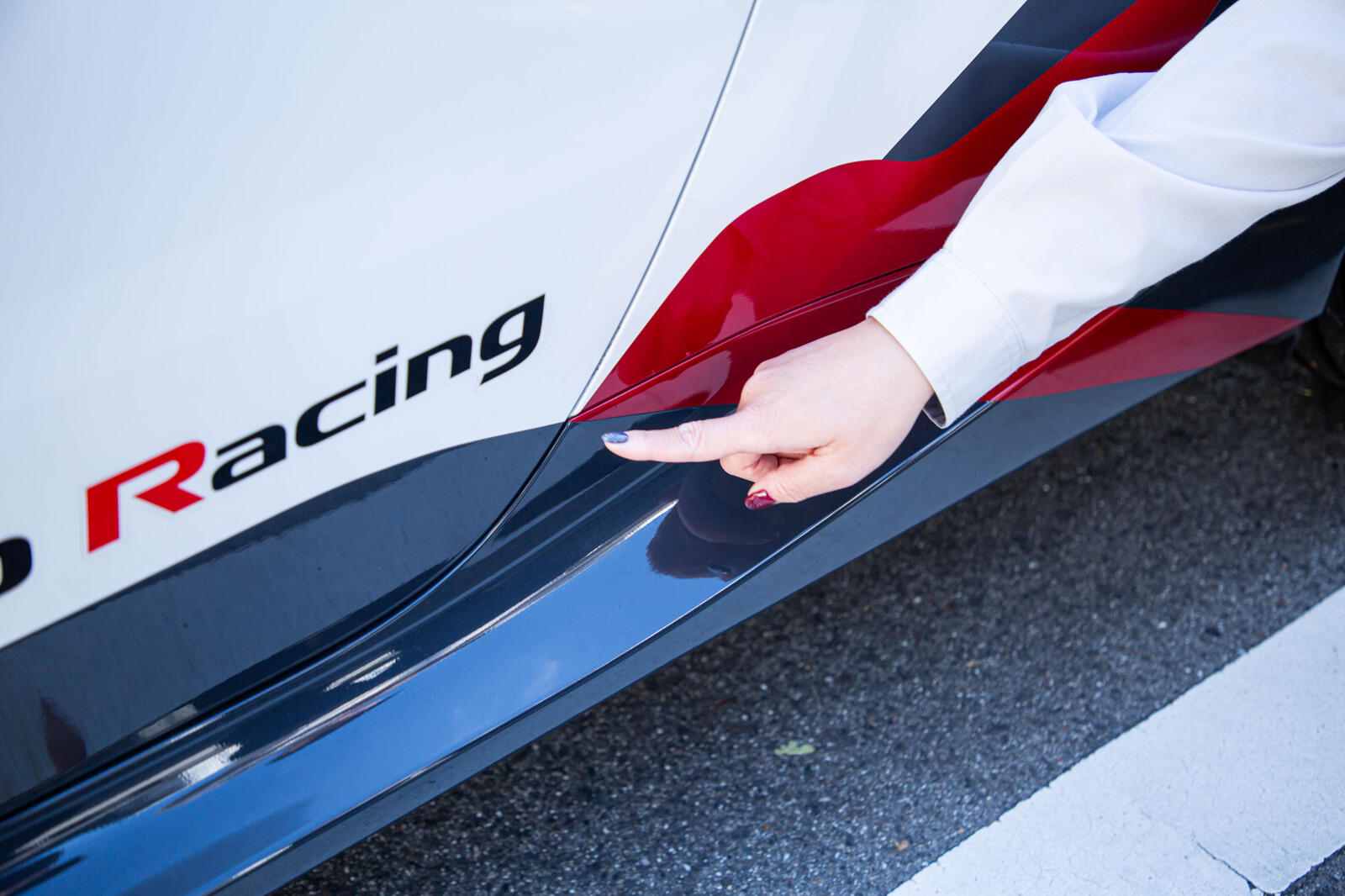
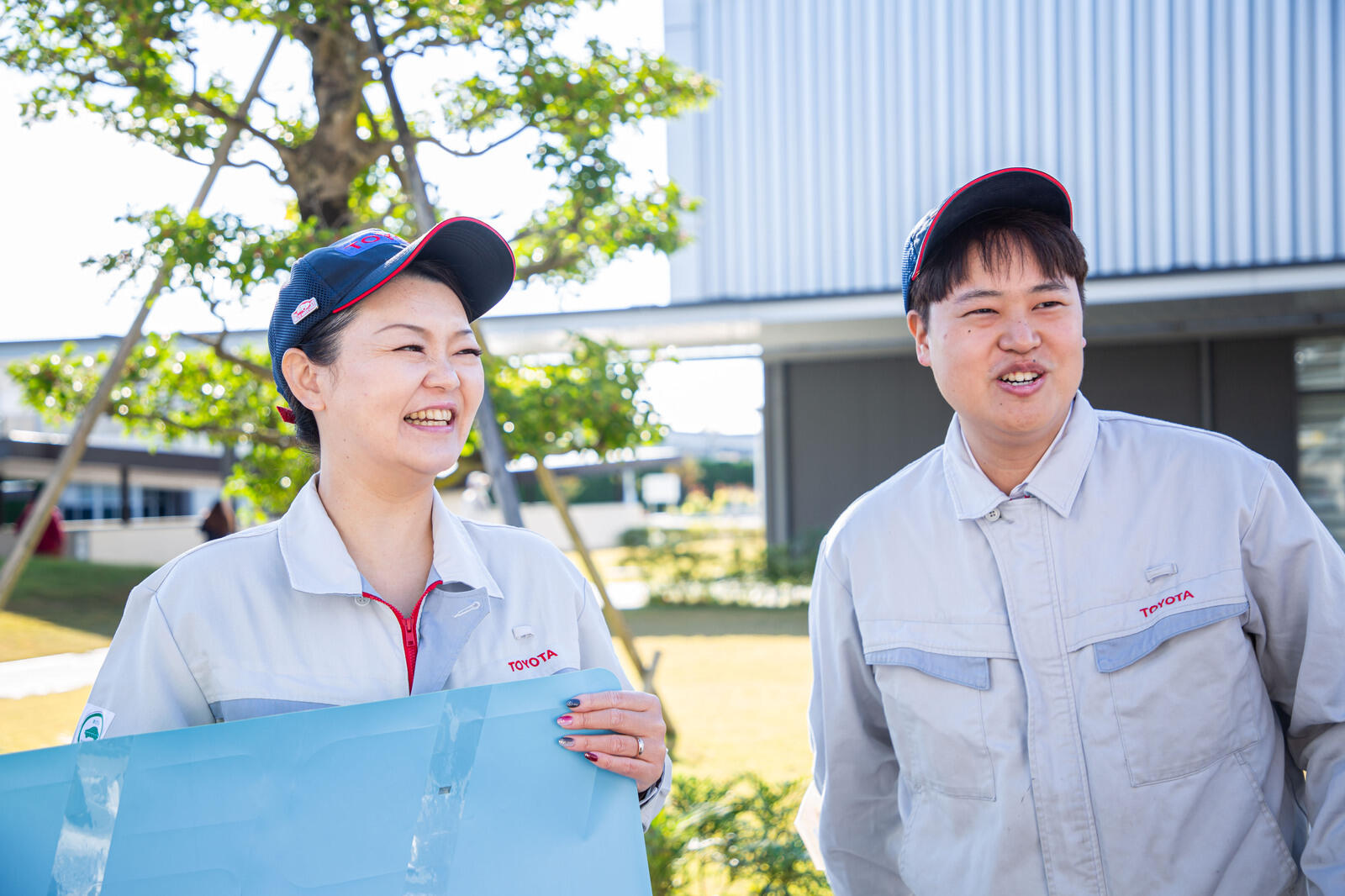
元町工場ではパトカーやツートンカラーのクルマの工法を扱ってきた中で培った知見や技能があったからこそ、このような高度な塗装を実現できた。
今回話を聞かせてくれた2人の表情は、未知の挑戦を経て技能を更新した今、さらなる進化へ自信に満ち溢れているように見えた。
変化をつくりだすための挑戦は、継承編で触れた溶接の現場でも。ここでは鉄からアルミへと新
境地に足を踏み入れている。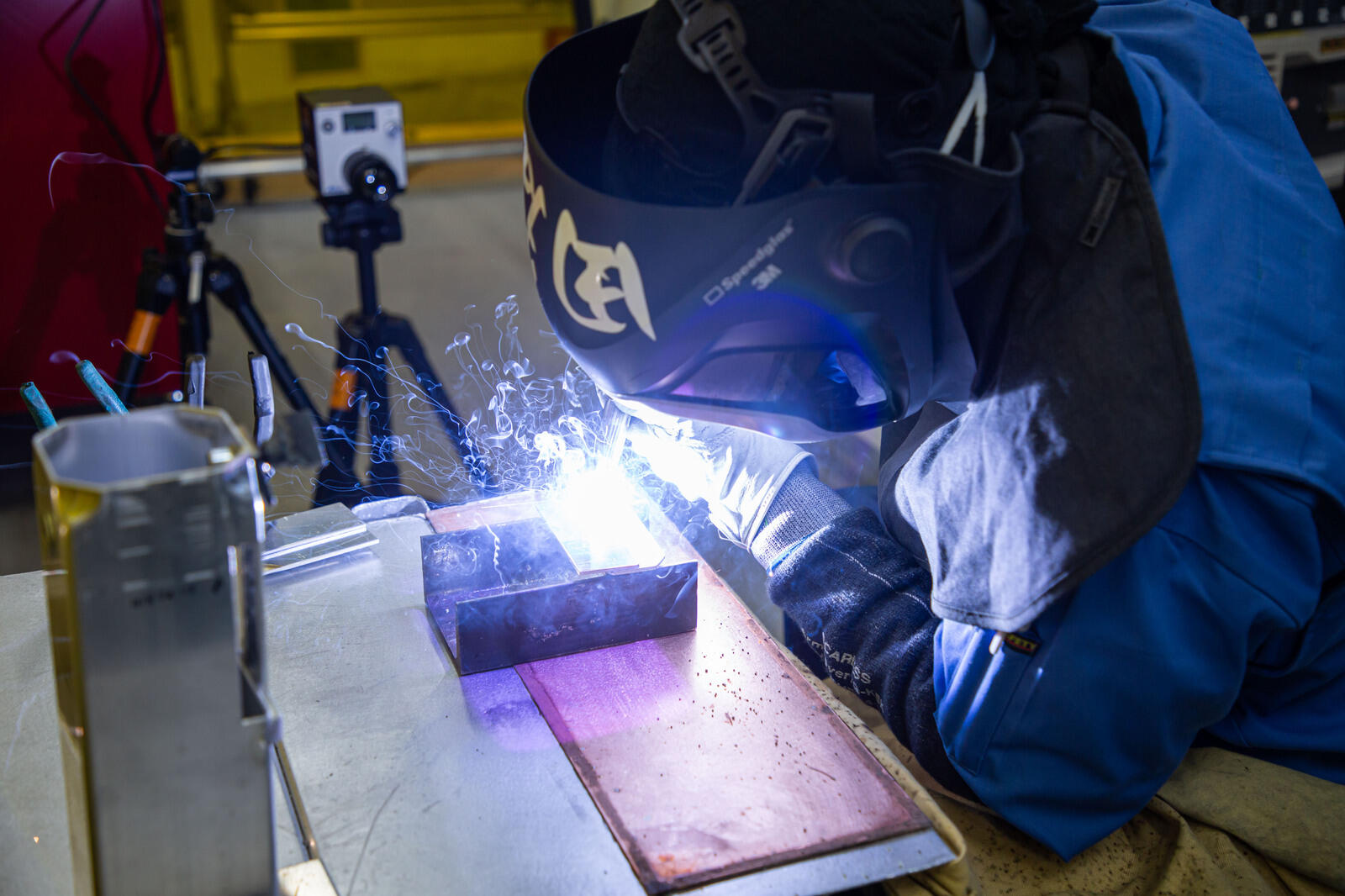
アルミは軽量で錆びにくいという特性から、自動車のボンネットやドアなどへの採用が広がっているが、溶接の難易度が高い金属とされている。
中でも、溶接の邪魔になる酸化被膜ができやすいという特性に対応するため、アルミでは(右利きの作業者の場合)溶接機を右から左に動かすようにして、作業しなければならない。
しかし、これだと、溶接個所が手や溶接機などで死角になってしまう。
車体部カーボン課 高崎恭暢チーフエキスパート
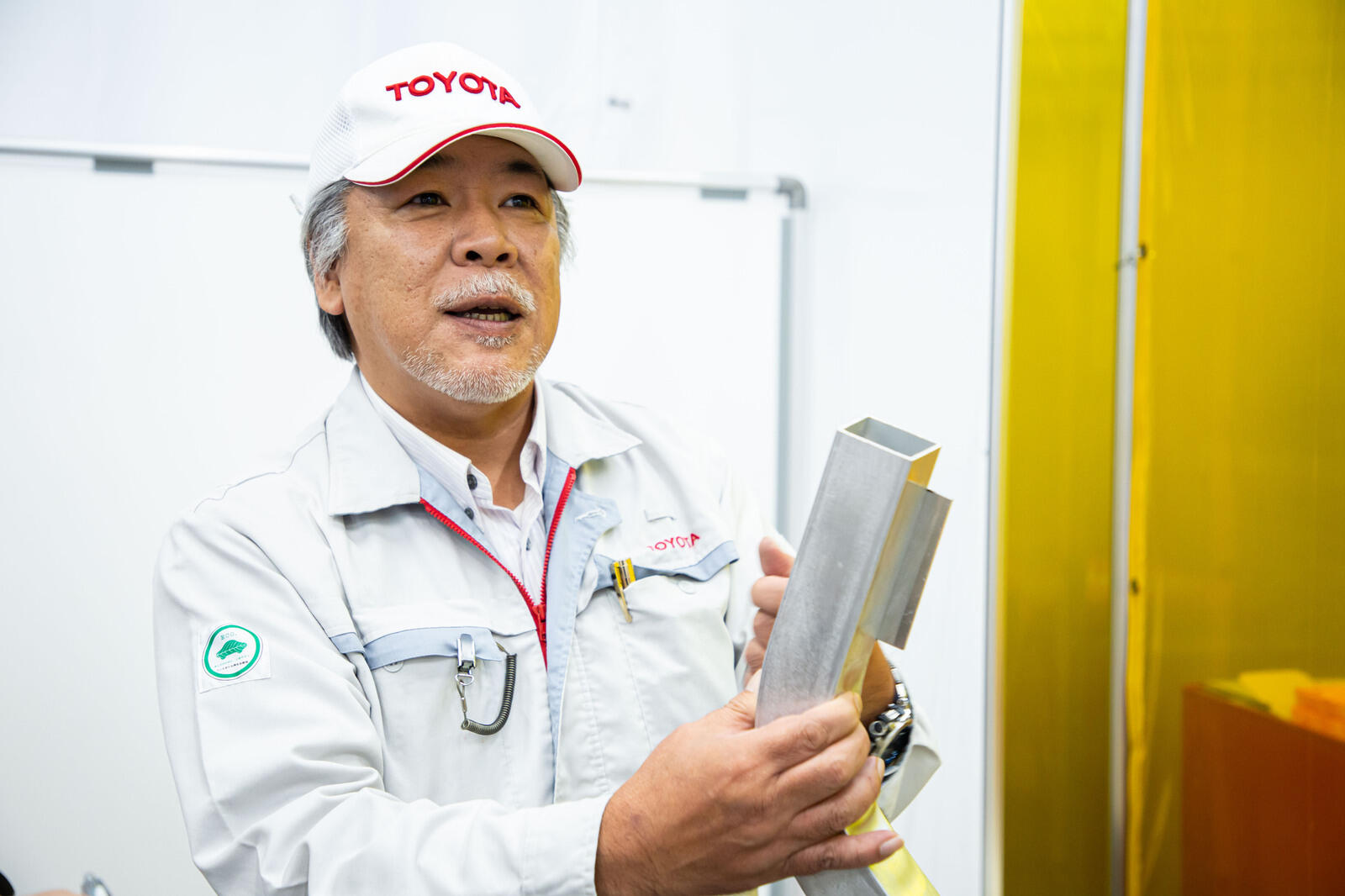
鉄との大きな違いは作業が終わるまでビードの状態が見にくいことです。仕上がりが目視で確認できなくとも、しっかり溶接ができるカンコツが必要とされます。
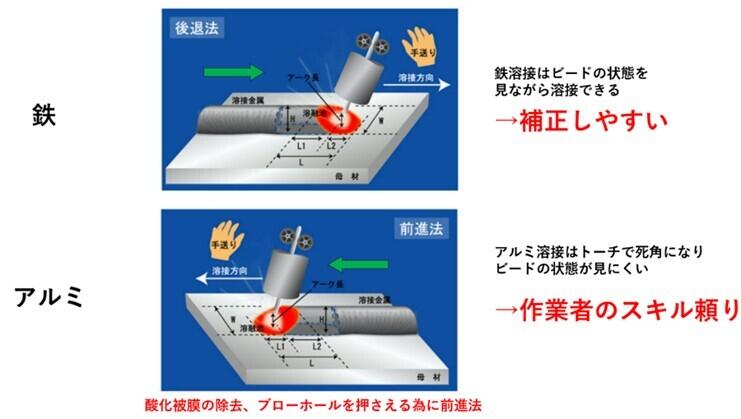
この技能の習得に一役買っているのがモーションキャプチャーである。
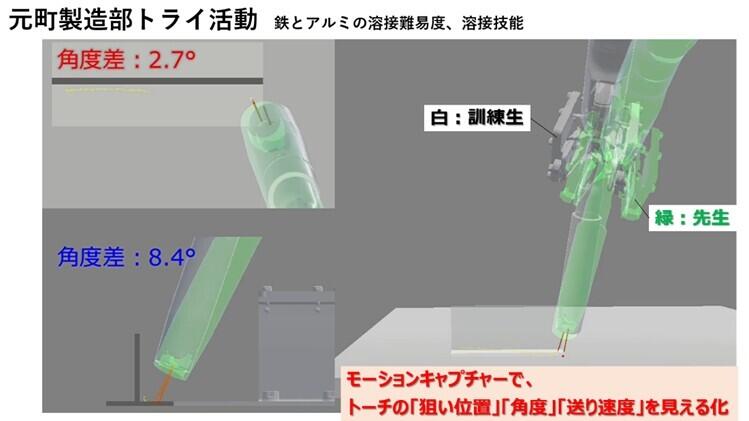
先生と生徒、それぞれの溶接の様子を撮影し、3D図面で再現することで、角度や狙い位置など、細かい動きの違いを立体的かつ視覚的に確認することができる。
これにより、4カ月かけていた技能の習得が、2カ月で可能に。できあがったもので違いを比較するしかなかったものが、デジタルの力を借りることで進化を遂げている。
軽量化を目的としGR ヤリスのルーフなどで採用が進むカーボンでも、変化をつくりだす挑戦が行われている。
軽くて頑丈なカーボン素材は3,000本から12,000本のカーボン繊維を織り込んだシートを超硬刃でカットし、必要な厚みに合わせて人の手で型に貼り付け、樹脂で固めてつくる。

この工程では、樹脂を含浸したシートを複雑な型に合わせて貼り付ける。機械ではなかなか届かない深さや細かい凹凸に対応できるのは人の手であり、職人技が受け継がれている。
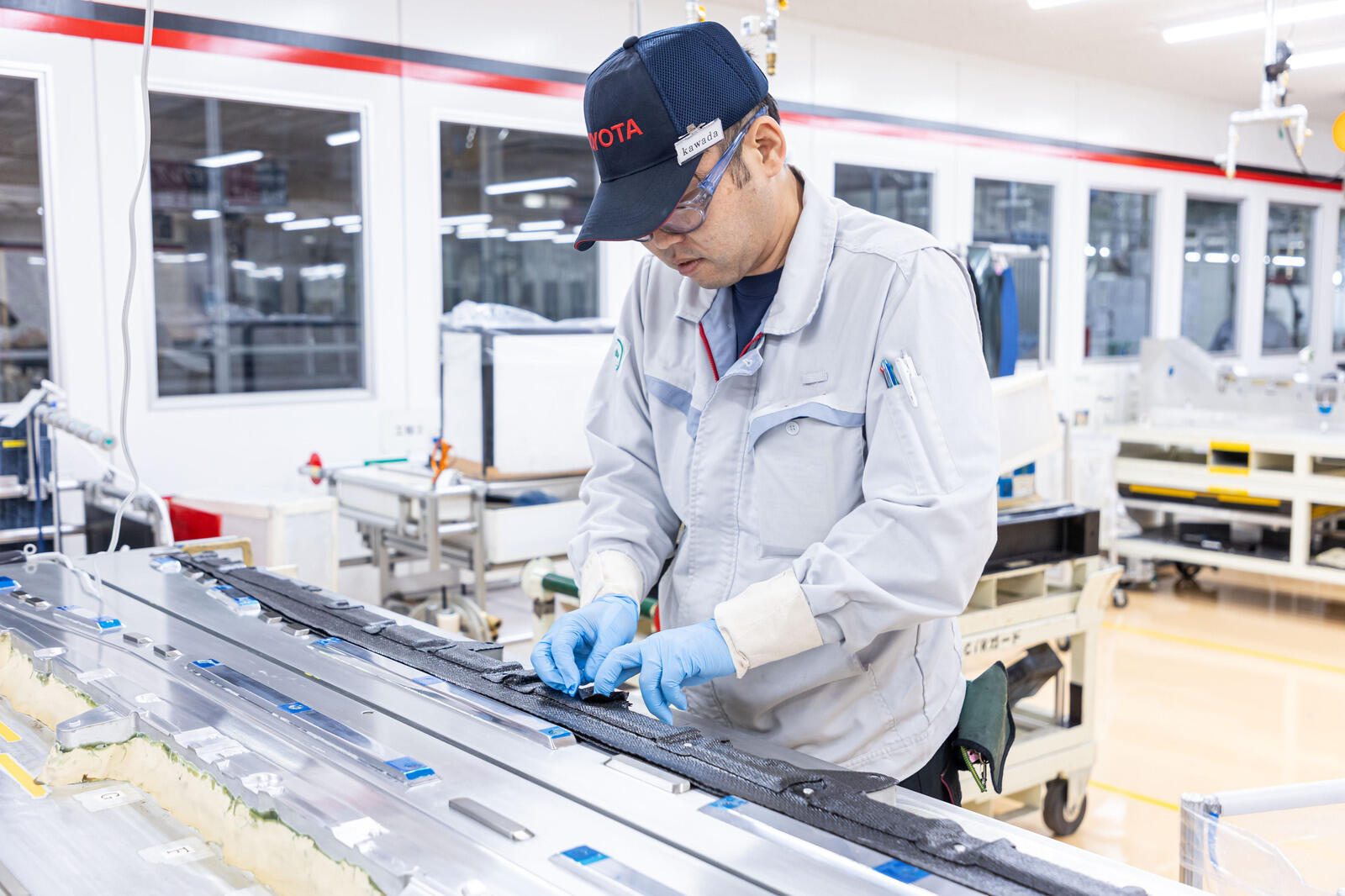
なお、外装品としてカーボンを扱っているのは元町工場だけで、クルマのほか、車いすレーサーや船などにも使われている。
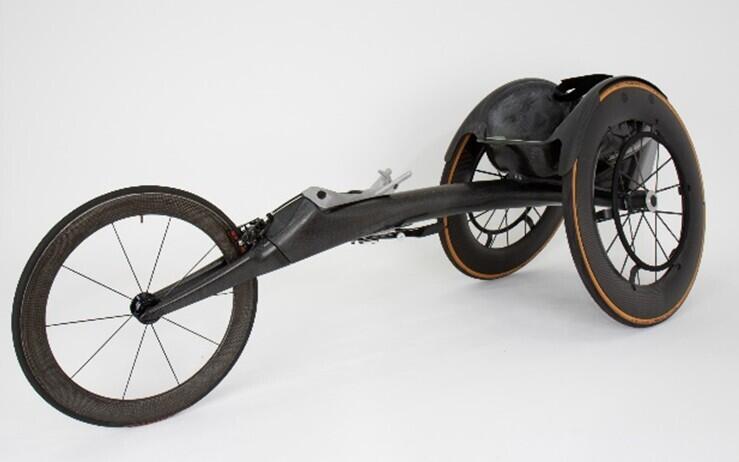
さまざまなモビリティに適する素材として進化していけるようさらなる軽量化を追求。シートを貼り付けた型の中にバッグを仕込み、空気で膨らませてつくる中空製品など、複雑な技法も取り入れ、モビリティの可能性を広げる挑戦を続けている。
車体部 カーボン課 平田京課長(現 高岡工場塗装成形製造技術部 外装部品技術室 カーボン部品G)
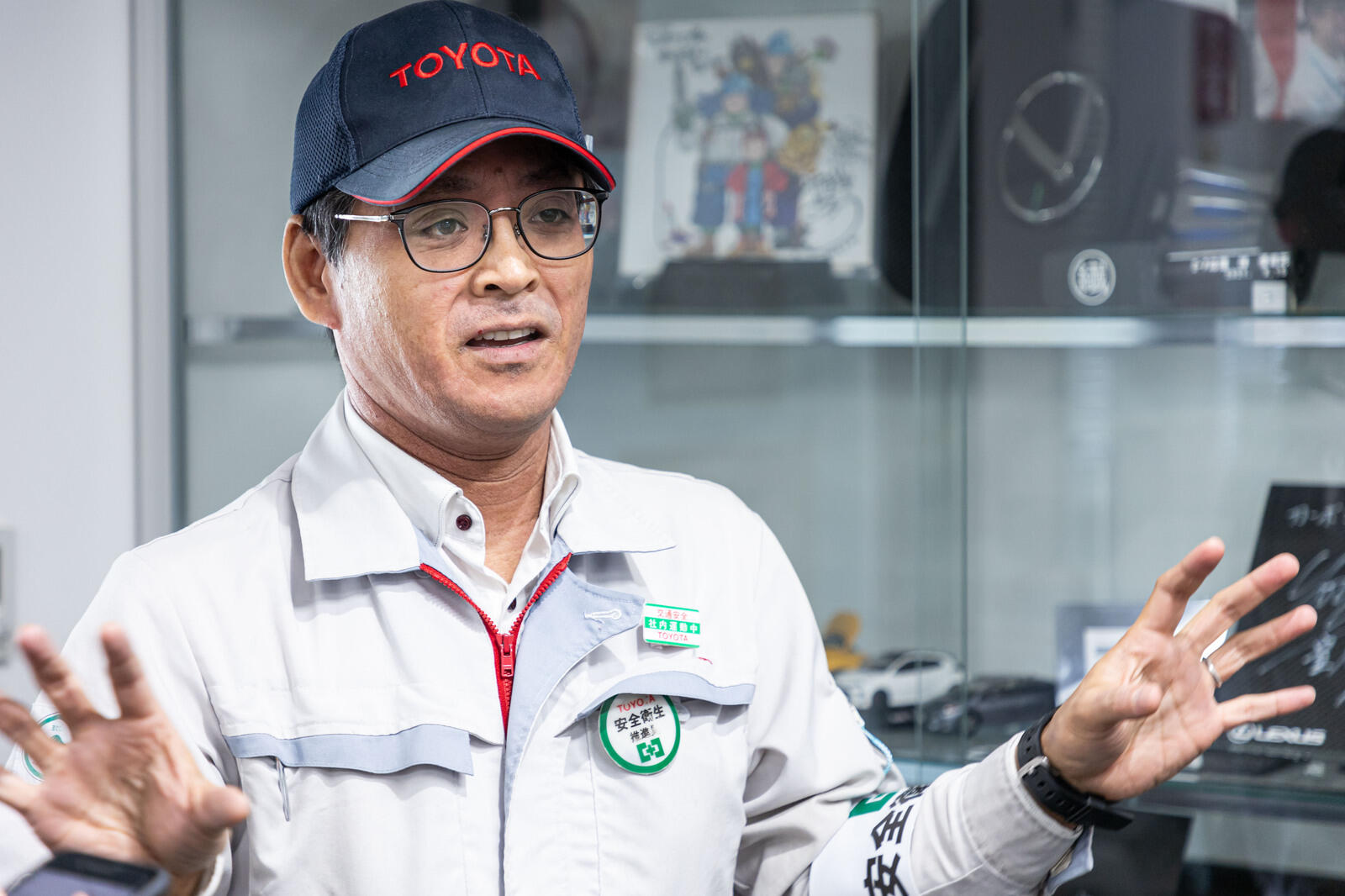
カーボン繊維を開発したのは日本です。しかし、量産の事業をやっているところがほとんどなく、後工程が圧倒的に少ない。ここで音を上げたら、日本の技術力の優位性がなくなってしまう、意地でも日本のモノづくりを守るという想いでやっています。
脱炭素へ技術で変化をつくりだす
トヨタ生産方式の考え方にのっとって、日頃から知恵と工夫でリードタイムの短縮や原価改善に取り組むモノづくりの現場。
電動化の波に対応するだけでなく、従来の仕事のやり方や組織の在り方を大きく変え、自ら変化をつくりだすチャレンジも行われている。
機械部 設備課 浅野伸二課長
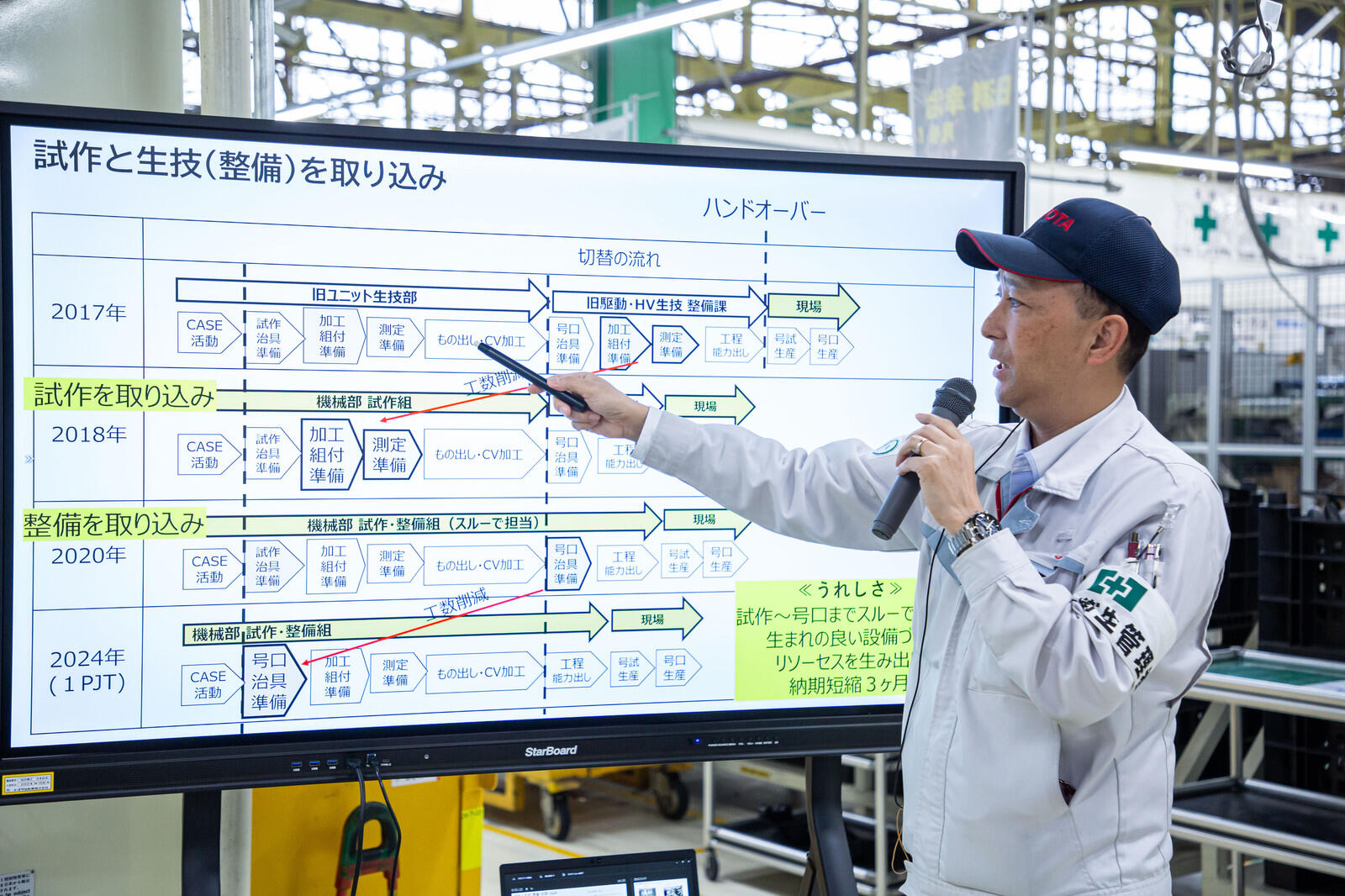
これまでの足回り部品の生産では、製品の開発段階を試作部、生産ラインの工程計画を製造技術部、量産ラインができてからは機械部と役割をすみ分けていました。しかし、2018年以降、機械部へ試作業務を取り込み、製造技術部からは約20名が機械部へ異動。試作段階から量産まで一貫して担える組織へ変革しました。
業務領域の拡大により人材育成と効率化が進み、人工を減らすことで確保したリソーセスを、電動化に充てている。
こうした背景のもと、機械部では2022年にトヨタ初の本格BEV用の電池パック生産ラインを立ち上げた。担当する山田大円課長は現場の絶え間ないカイゼンを教えてくれた。
機械部 EVユニット課 山田大円課長
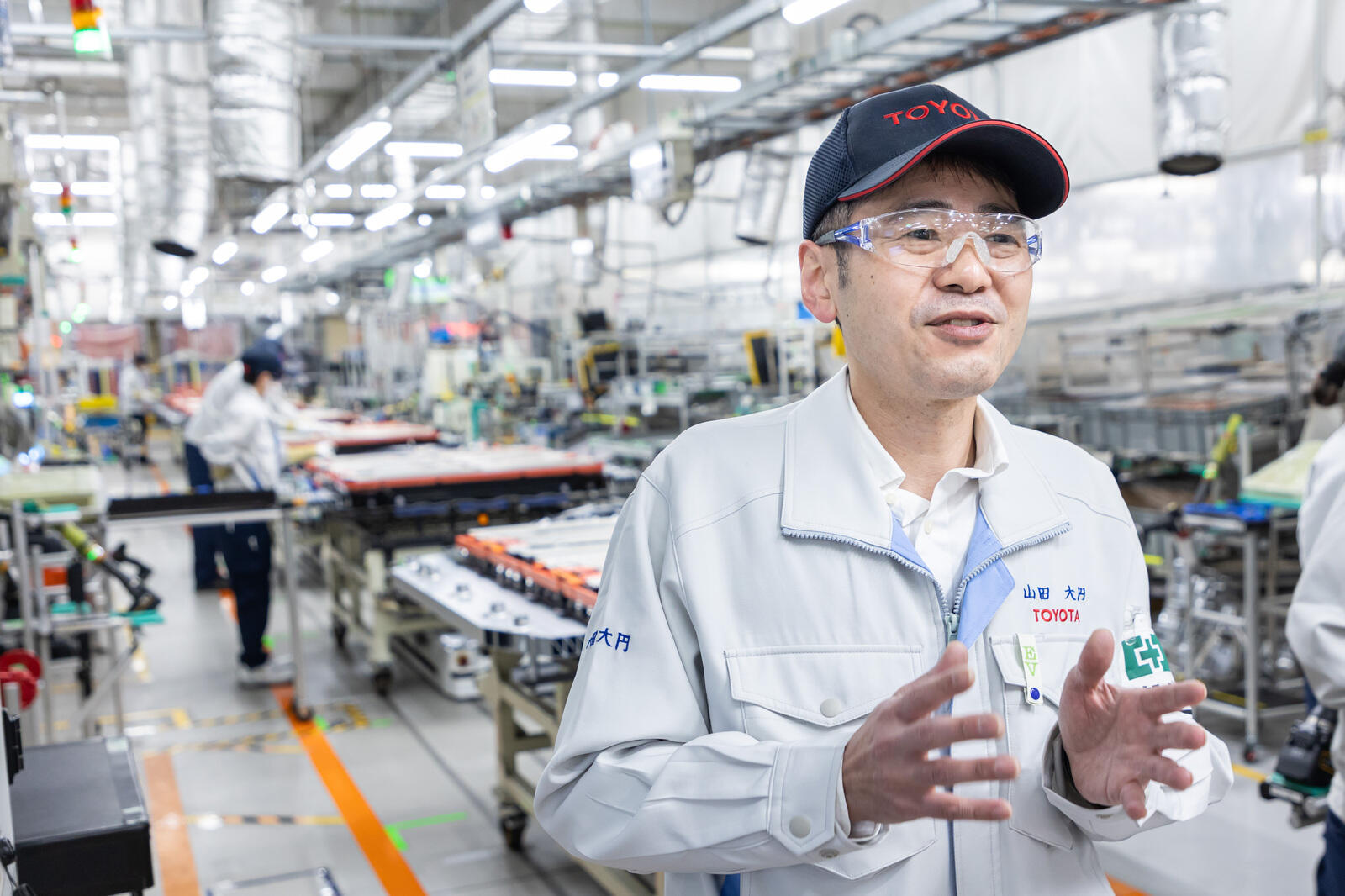
電池につながるコネクタの接続が甘いと、走っている間に外れ、クルマが動かなくなってしまう原因になる。これは検査でも簡単に見つけられず、後工程に流れてしまうことが課題でした。
これに終止符を打つため考案したのが、こちらの検査治具です。
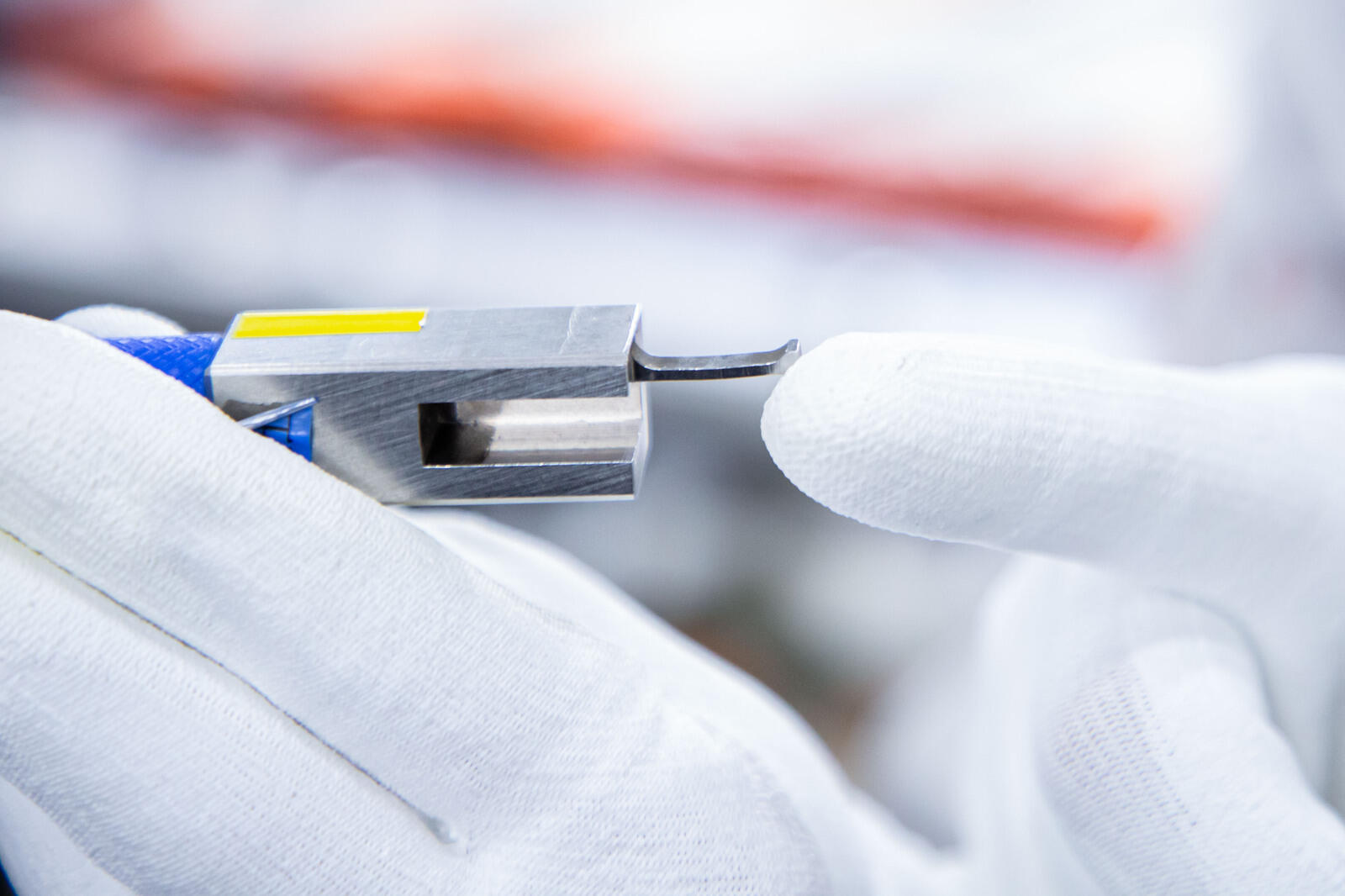
非常にシンプルな構造ながら、接続が甘いコネクタ部に差し込むと、引っ掛かって抜けなくなる仕組みになっています。
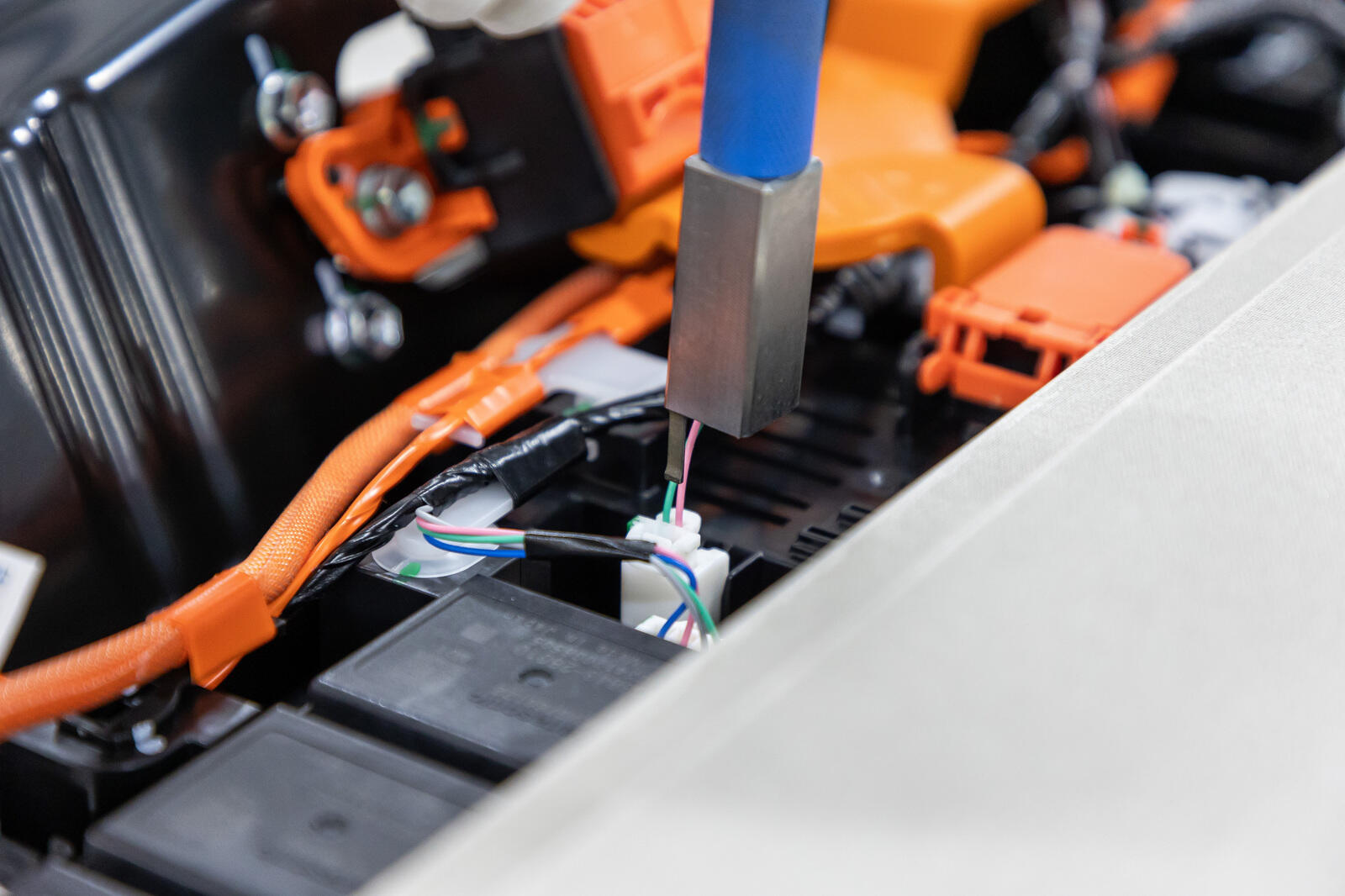
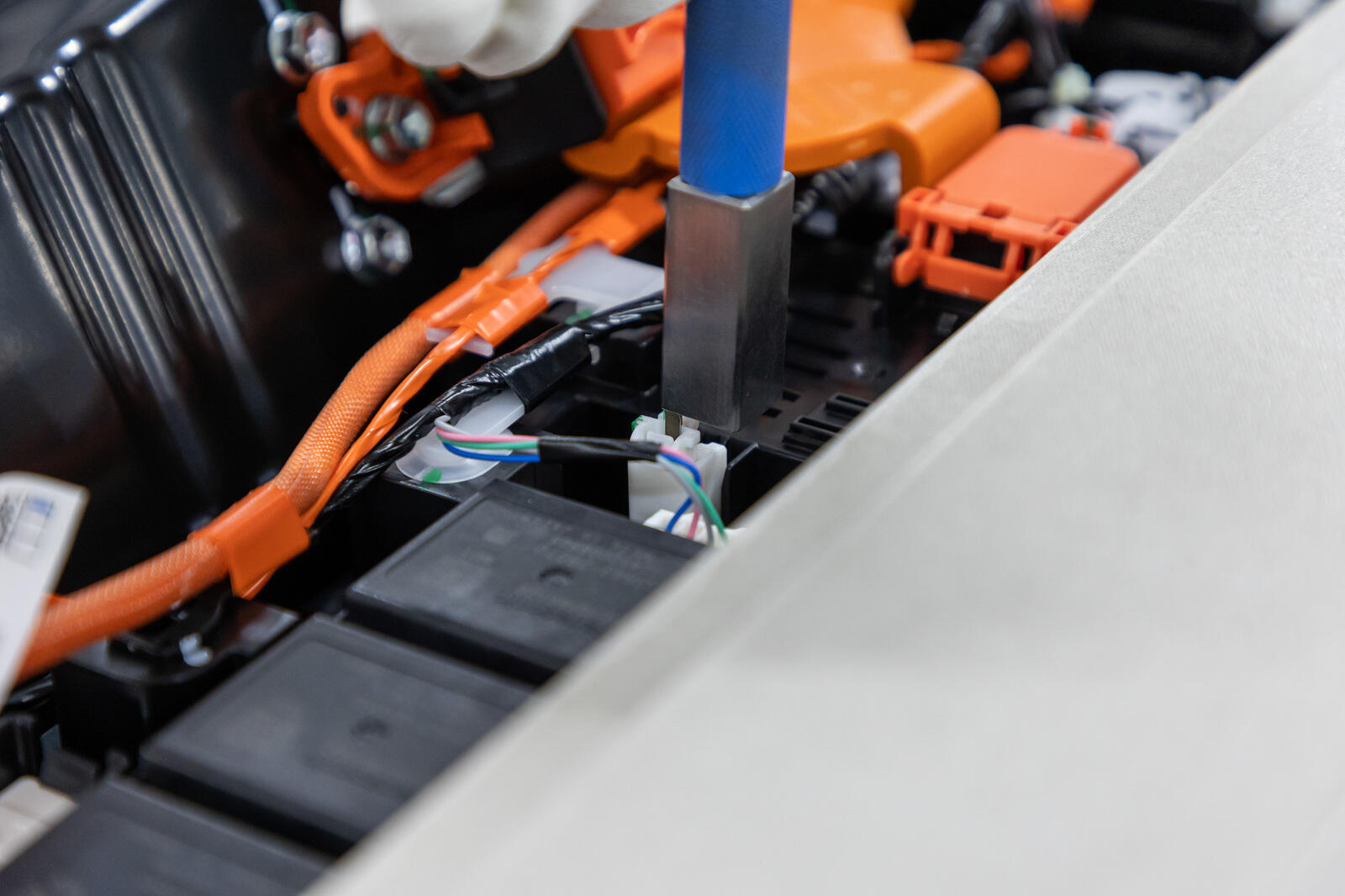
電動化時代の新たな挑戦も、ベースを支えるのは長年にわたって培ってきた現場の知恵と工夫。全社を挙げたモノづくりの力で「変化」をつくりだしていく。
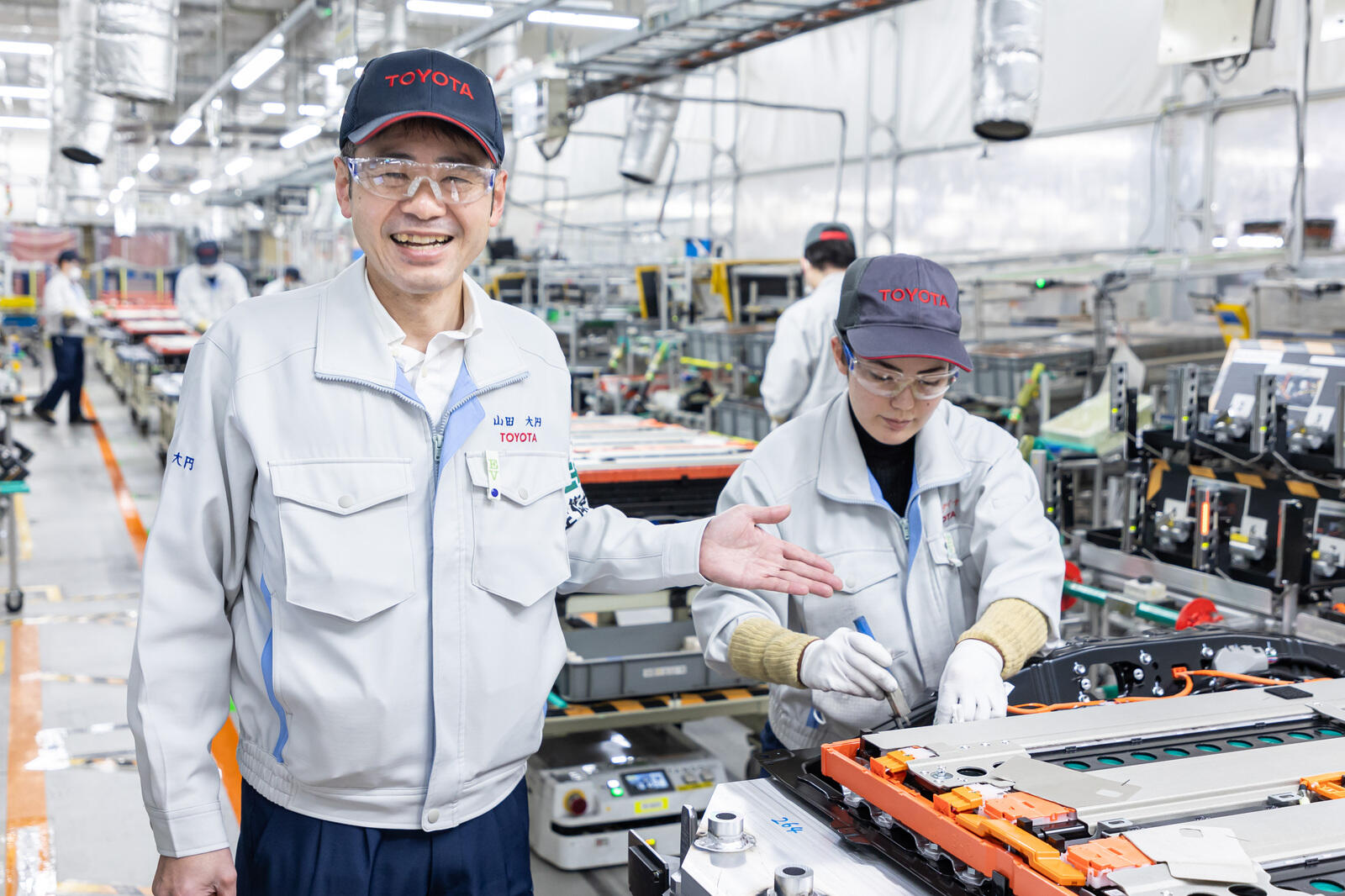
ここまで紹介してきたのは、元町工場の中で変化をつくりだす試みだったが、変化を工場の外へ広げるために挑む集団もいる。
工場のいたるところで活躍するフォークリフト。元々、ガソリン仕様だったものを、2016年から燃料電池(FC)へと切り替えはじめ、現在では167台、実に全体の42%が水素を燃料 * としている。
*燃料となる水素は、知多市や東邦ガスと連携して、バイオガス由来の都市ガスからつくっている。
他にも、水素を使った実証実験はあちらこちらで行われている。その1つが、先ほど紹介した電池パックラインの乾燥炉への活用だ。
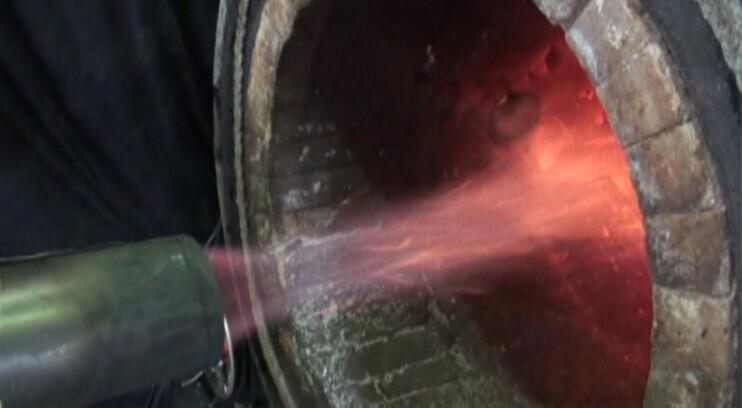
バーナーの燃料として、量産工程で初めて水素を使用。太陽光で水を電気分解してつくっており、水素の供給が十分でないときには不足分を都市ガスで補う。安定した水素供給を実現すべく、模索しながら生産工程のカーボンニュートラル化を進めている。
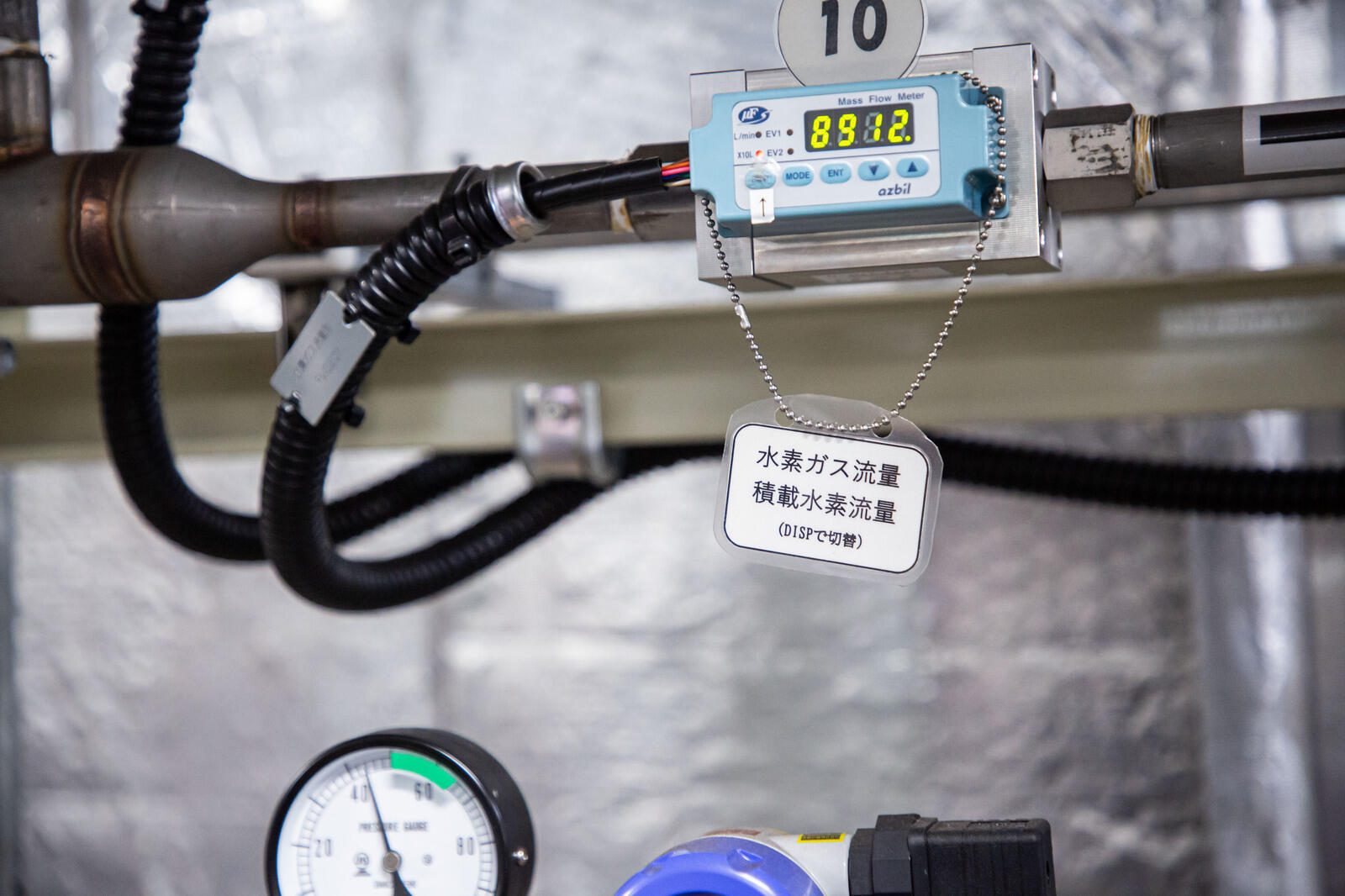
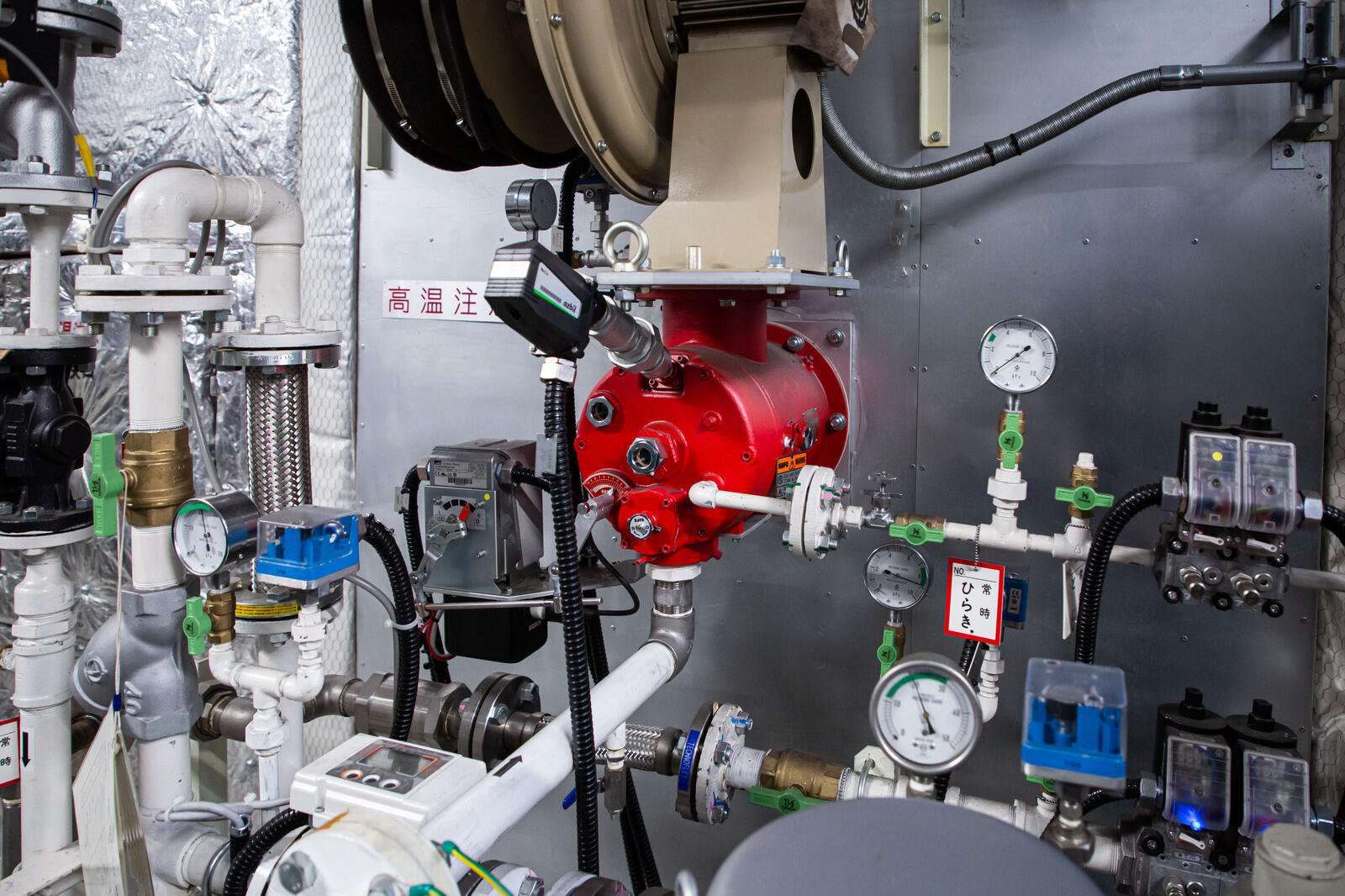
また、水素ステーションの運営コストを下げるための活動も積極的に進められている。
水素の充填設備の中でも、ノズルやホースといった部品は消耗品にあたる。ある一定の期間や使用回数に応じて交換することが推奨されているが、その頻度が少なくなれば、当然コストにも効いてくる。
元町工場では、実際どこまで使用に耐えうるのか、リアルな使用環境の中で検証を進め、データを収集。部品一つひとつに対して、交換基準を更新できる余地はないか、どうすれば長く使うことができるか、探り続けている。
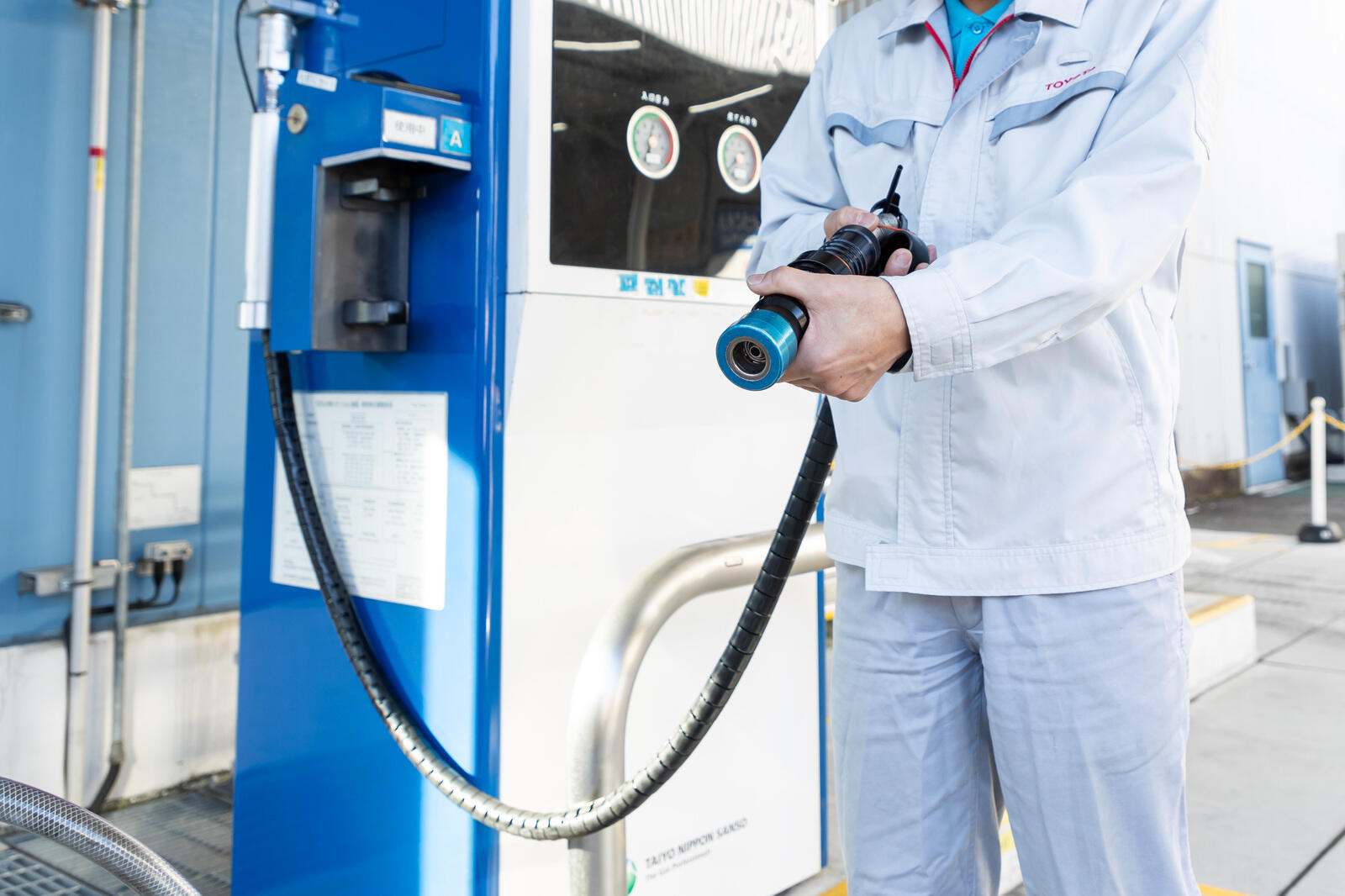
このような実験を行う理由について、プラント・環境技術部 原動力技術室 第1保全管理Gの北辰彰吾グループ長は次のように語る。
プラント・環境技術部 原動力技術室 第1保全管理G 北辰彰吾グループ長
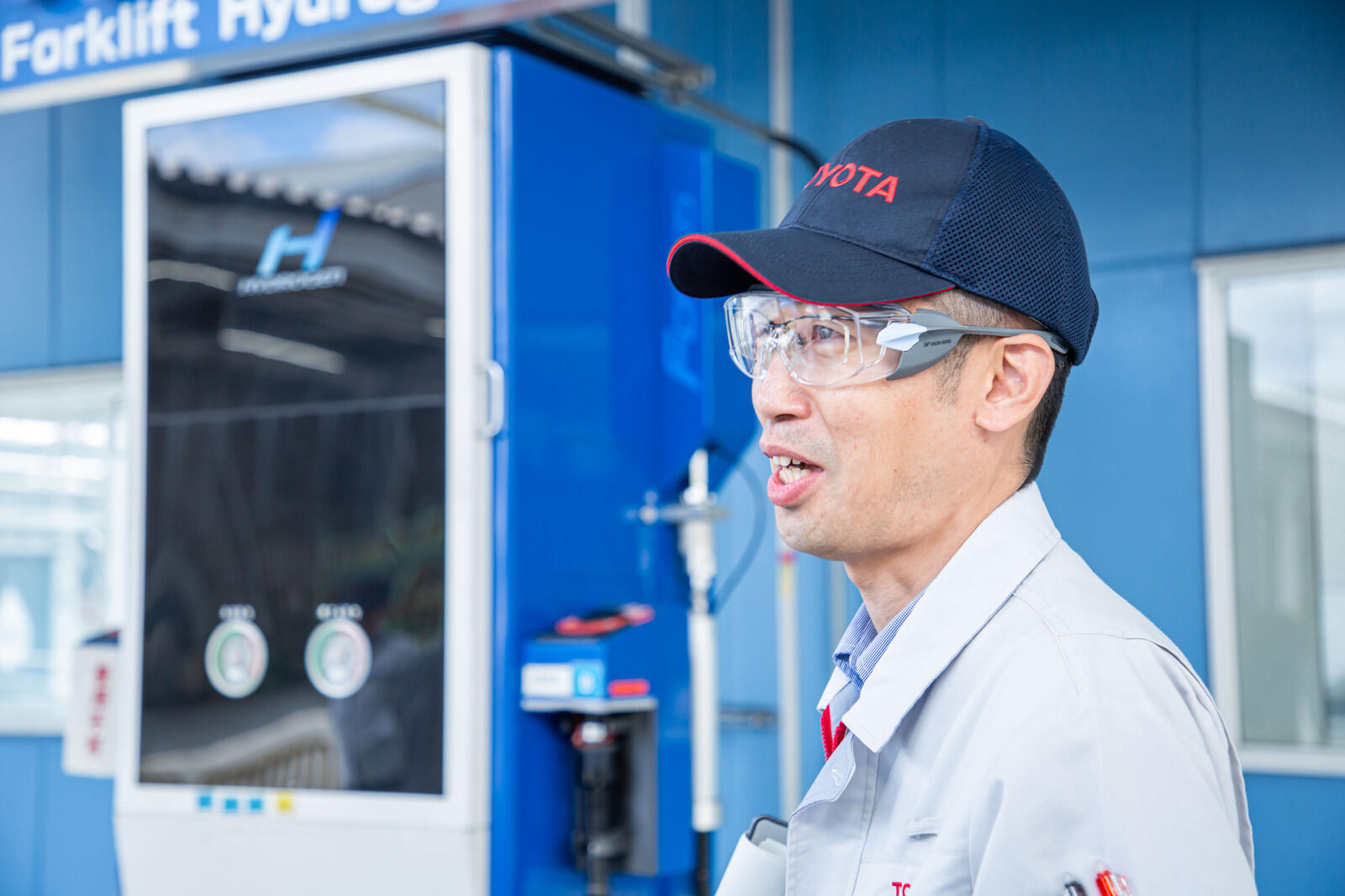
トヨタの工場の中だけで、いくら設備の信頼性を高めても、水素社会は実現できません。
市中の水素ステーションも「なかなか原価が下がらない」と苦しんでおられます。ここで我々が得た知見をフィードバックすることによって、運営費低減につなげられないかと考えています。
トヨタだけで終わらせず、他の企業とも手を取り合って、水素の普及、カーボンニュートラルに向けた取り組みを加速させていきたいと思います。
「感謝」皆さんとともに
建設から65年。いつの時代も変化に飲まれまいと歩みを進めながら、現在まで流れ続ける想いを、宮部工場長に聞いた。
宮部工場長
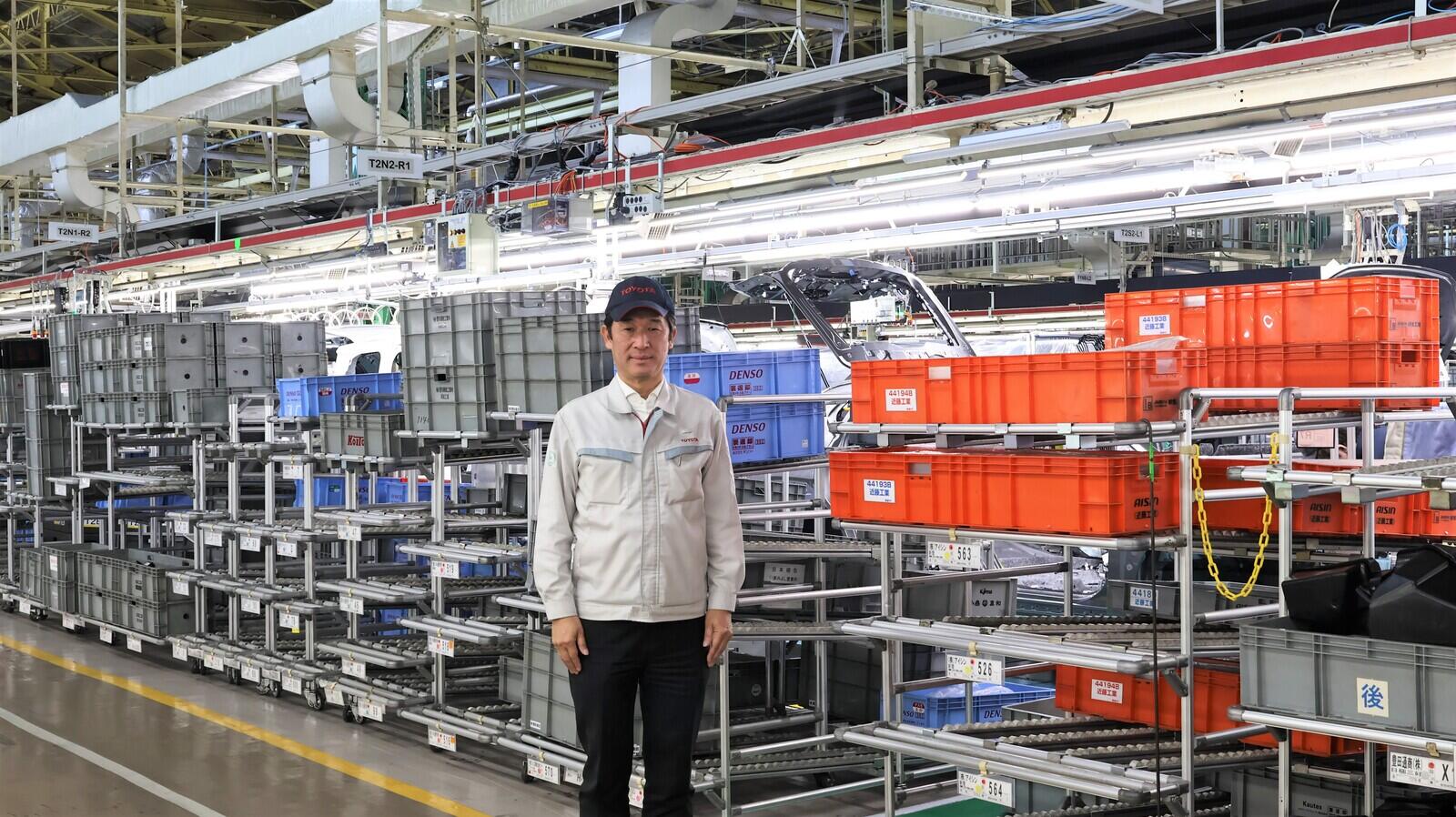
組立工場には、ボルトとかナットとかも含めて、1車種で3,000品番ぐらいの部品が入ってきます。
長年トヨタで働いていますが、いまも、部品の入った通い箱には初めて知る仕入先様の名前が書かれていることがあります。
そうした仕入先様から、必要な種類の部品を、必要なタイミングで、必要な量、途切れることなく納入いただいている。
こうした事実に、やっぱり自動車産業550万人に支えていただいているなと感じます。
元町工場の初代工場長は、豊田章一郎名誉会長。2023年2月、亡くなった数日後には、名誉会長の棺を乗せたクルマが元町工場にも訪れ、多くの従業員が別れを惜しんだ。
そんな章一郎名誉会長の色紙が事務棟に飾られている。そこには、直筆で「感謝」としたためられている。
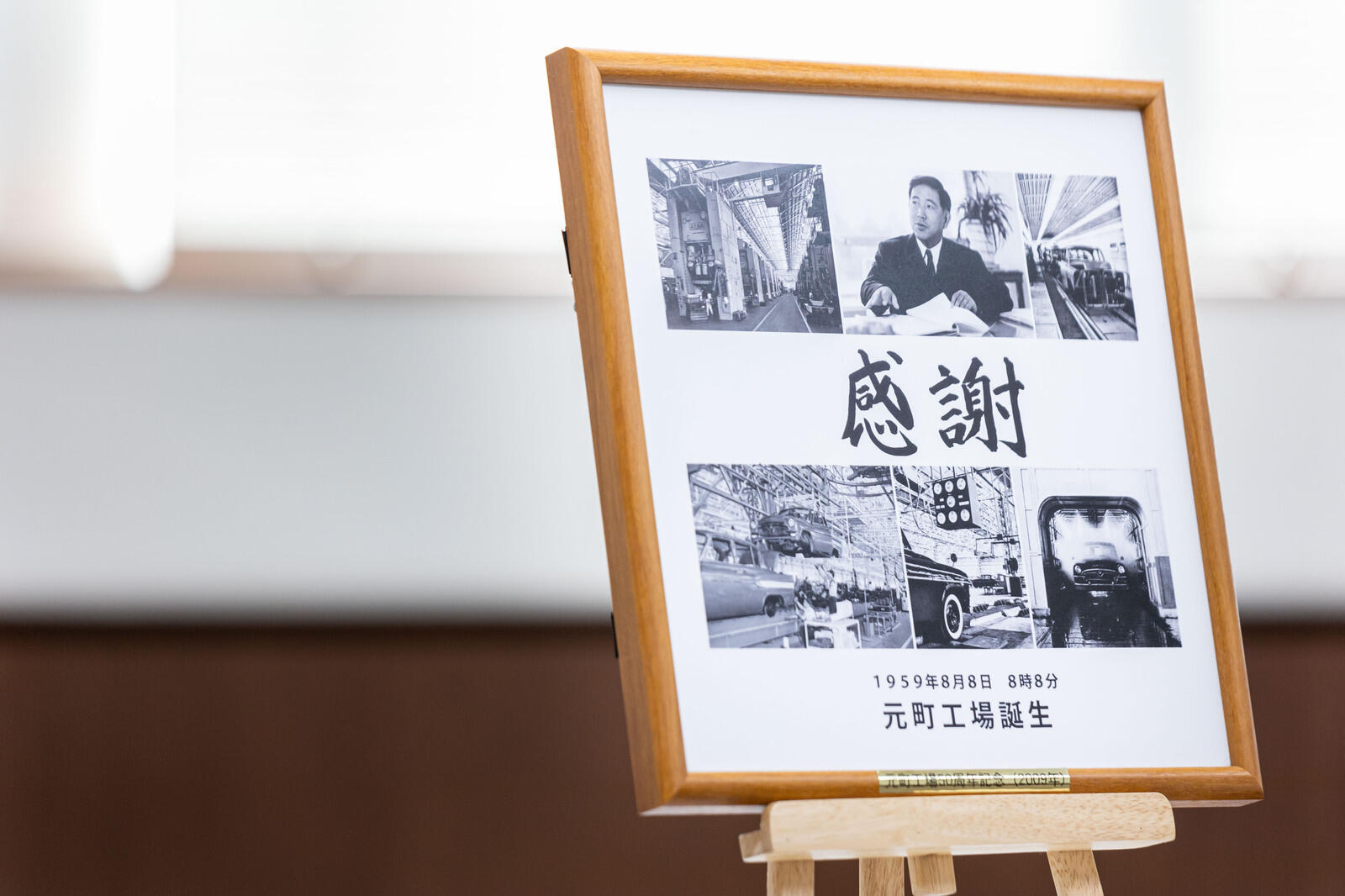
元町工場は着工から量産開始までわずか11カ月という異例のスピードで立ち上がった。
しかし、この背景には、昼夜を問わず、工事を進めてくれた協力会社、土地の工面に速やかに動いてくれた自治体の支えなど、たくさんのステークホルダーのサポートがあったという。
建設委員長として、それを誰よりも感じていたのが章一郎名誉会長だったのかもしれない。飾られた額縁を眺め、65年の歩みの先に見据える未来への想いを続けた。
宮部工場長
(豊田)章一郎さんが遺された「感謝」という言葉。社内の従業員だけでなく、すべてのステークホルダーの方々に「感謝」。
元町工場はこの気持ちを素直に胸に抱き続け、スピード感を大切に、チャレンジする集団であり続けなければならない。先人の決断の重みを僕らの世代でもしっかり背負わなきゃいけないと思います。
元町工場に生き続けるチャレンジスピリットを継承していかなければならない。工場を興し、発展させてきた先人たちに想いを馳せた宮部工場長の言葉に、そんな決意が見えた。