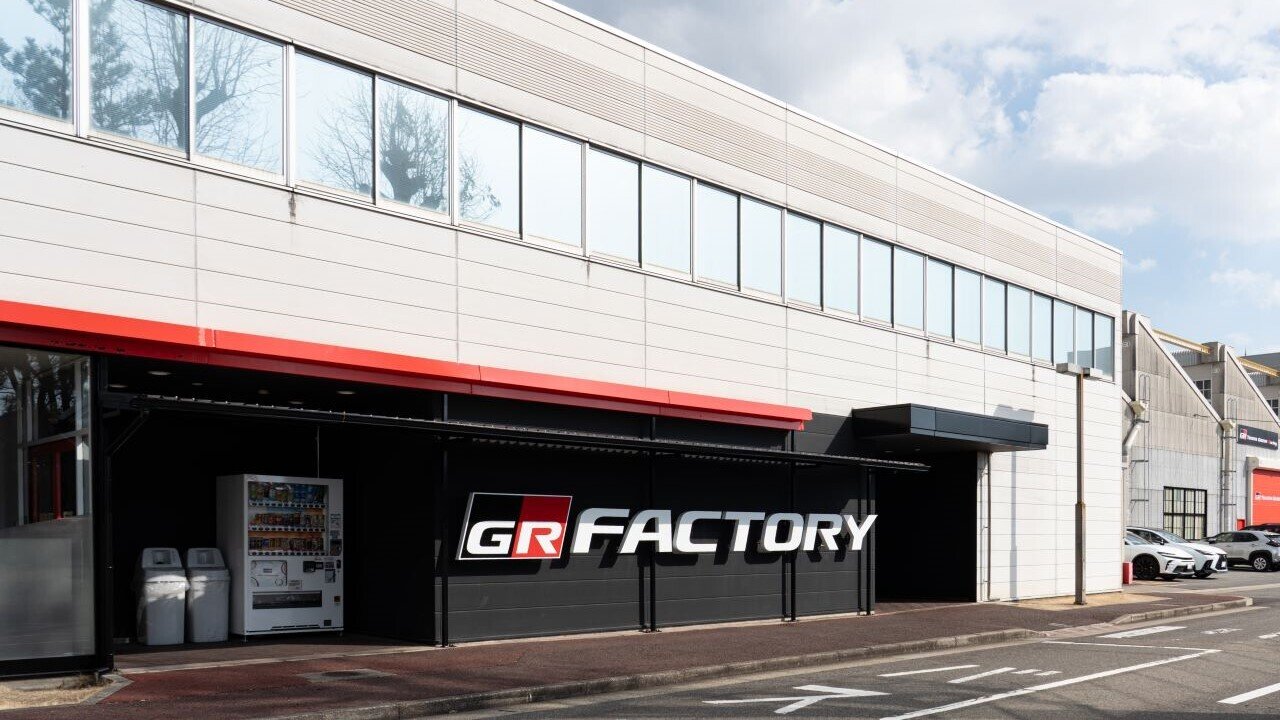
モータースポーツを起点としたもっといいクルマづくりを実現するGRファクトリー。"トヨタのスポーツカー"への想いとこだわりが詰まった、クルマづくりの一端を紹介する。
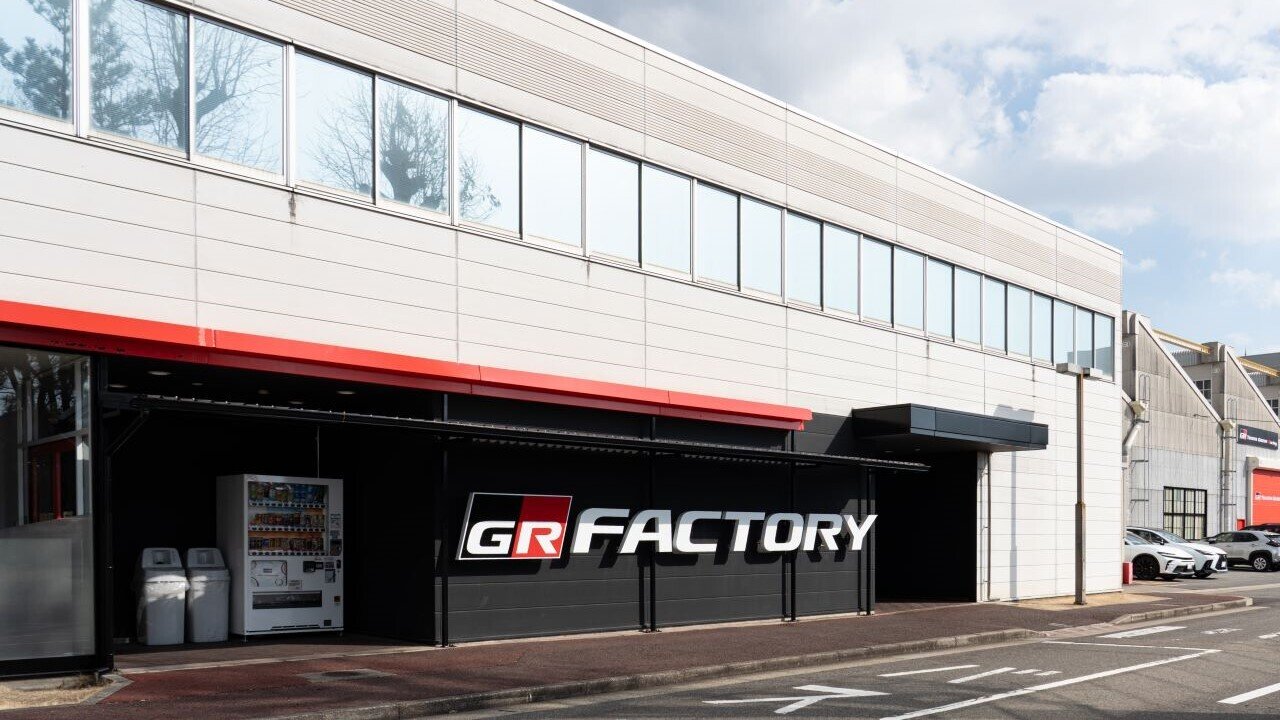
2020年のGRヤリスの立ち上げに合わせて稼働を開始したGRファクトリー。モータースポーツの現場で得た知見によって進化する車両に合わせ、アジャイルに生産工程に反映するラインだ。
2025年1月には生産ラインがリニューアル。トヨタイムズでは、このGRファクトリーのモノづくりの一端を紹介する。
“トヨタのスポーツカー”を取り戻したい
GRヤリスはモリゾウこと、豊田章男会長の悲願のスポーツカーだ。
2000年代、トヨタのスポーツカーは生産終了が相次いでいた。4代目スープラが2002年、アルテッツァが2005年、MR-Sが2007年に終了。
当時のトヨタは、海外を中心に販売台数を伸ばし、規模の拡大を追求する中で、「売れるクルマ」「儲かるクルマ」を軸とした戦略を立てており、「一部のクルマ好きのためのクルマ」と位置付けられたスポーツカーは、商品計画から遠ざけられてしまっていた。
豊田社長の就任以降、86(2012年)、GRスープラ(2019年)とスポーツカーを復活させていったが、いずれも、他社との共同開発で、トヨタが生産するモデルでもなかった。
「トヨタのスポーツカーを取り戻したい」
これが、豊田章男が心に持ち続けた強い想いだった。
「走る・曲がる・止まる」を意のままに
市販車を改造してレース用の車両をつくる。そんな、トヨタで定着していたスポーツカーへの考え方を、モリゾウは変えた。
レースで勝てるクルマをつくり、市販車へ還元する。この逆転の発想で開発が始まり、生まれたのがGRヤリス。それを量産していくための工場がGRファクトリーだ。
ここでは、一般的なクルマの量産ラインで見かけるベルトコンベアやハンガー(吊り具)の姿はない。
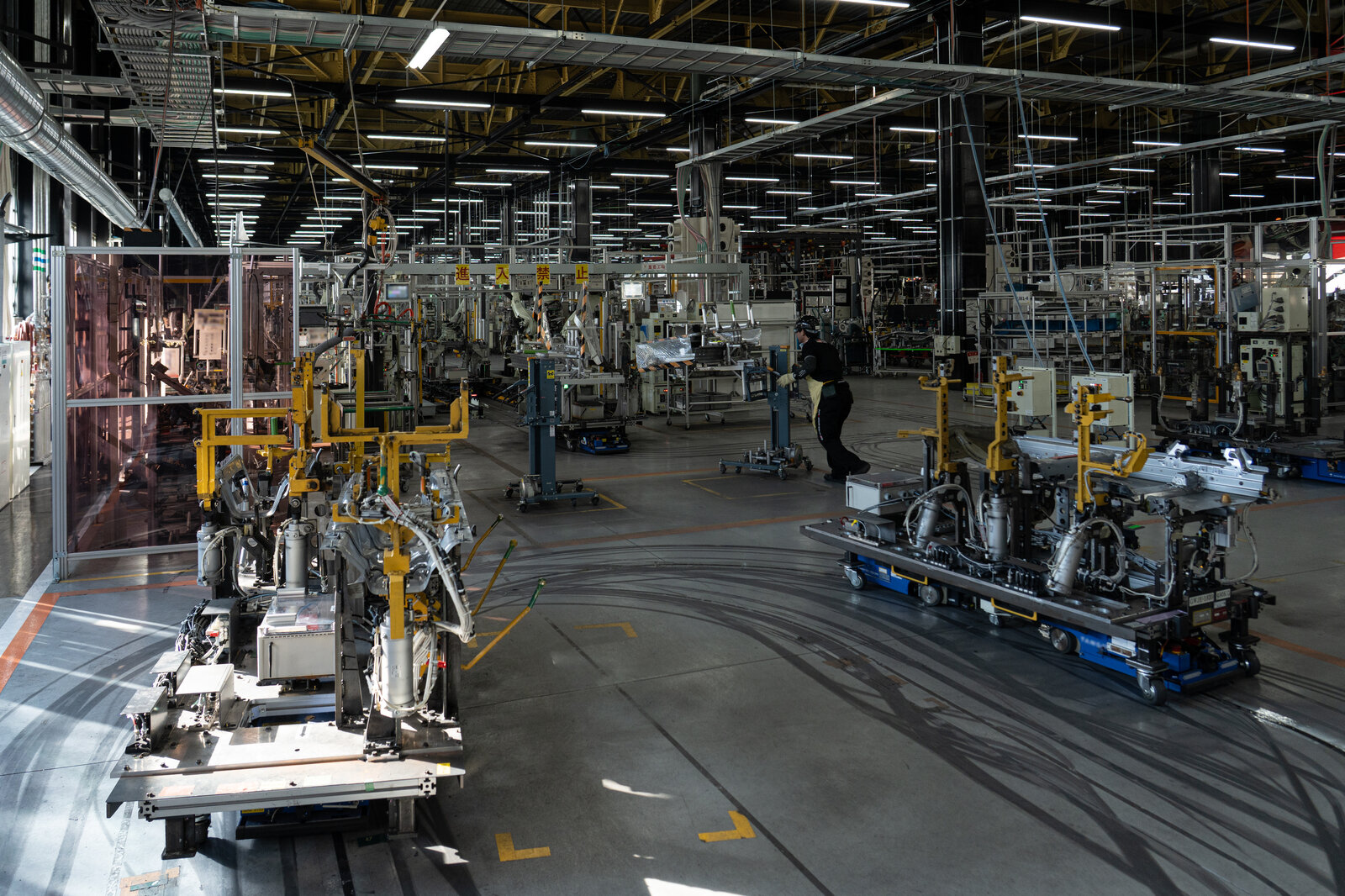
一人、または少人数のチームで、複数の工程をまとめて担当する「セル生産」の形式をとっており、セルとセルの間は、AGV(無人搬送機)で移動。これにより最新技術の導入や変種、変量への柔軟な対応が可能に。スポーツカーに求められる少量生産において、モータースポーツの現場と工場の現場がクルマづくりで連携し、アジャイルな生産を実現している。
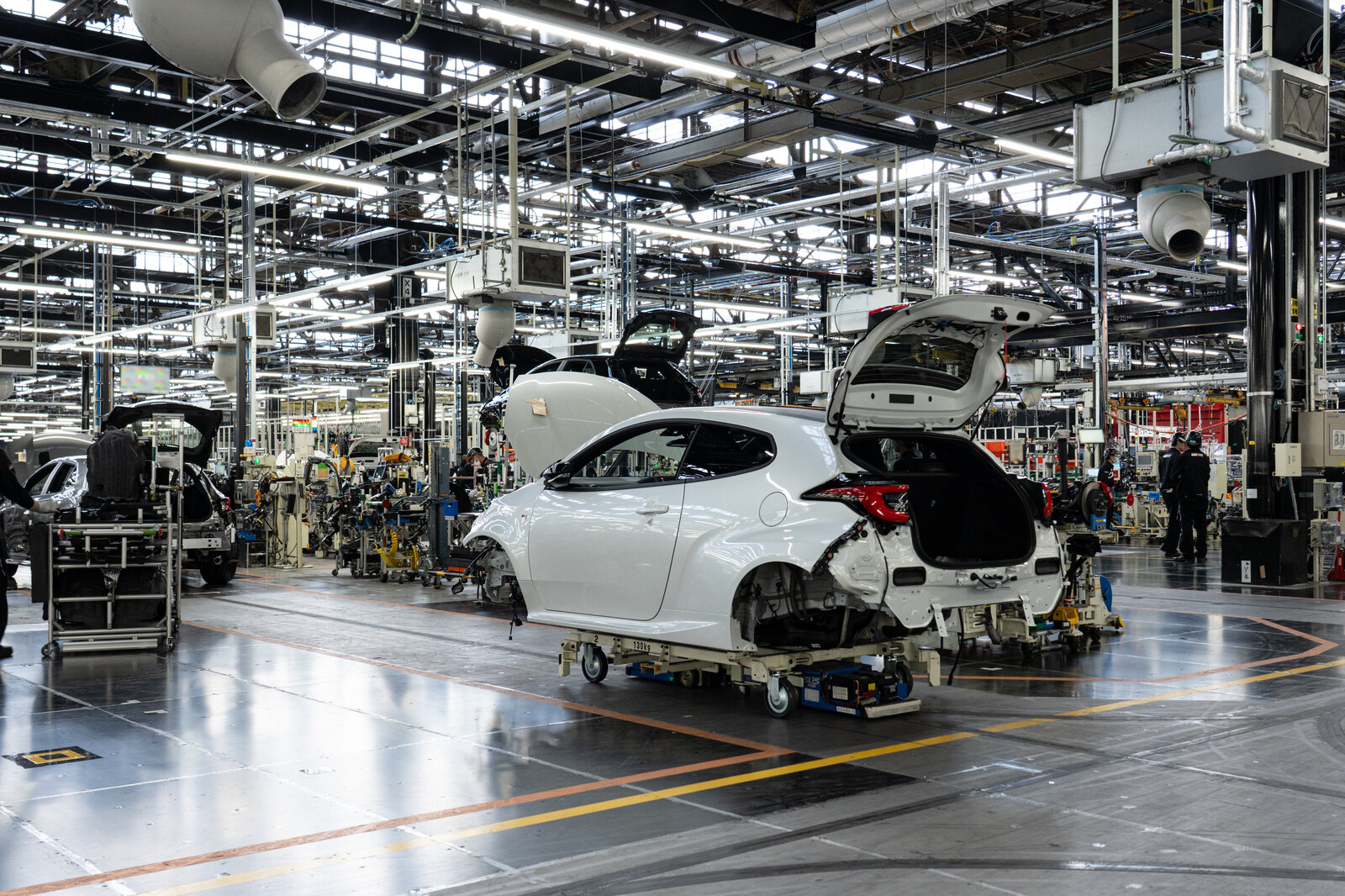
GRファクトリーが特異なのは、ラインオフしたクルマをそのままサーキットに持ち込んでも全開走行できるクオリティに仕上げている点だ。
例えば、バランスを崩すことなく、曲がりたい方向に、曲がりたいタイミングで曲がる。これを実現するためには、力が加わっても変形しにくい高剛性なボデーが求められる。
具体的には、ボデーの最初の工程であるアンダーボデー*溶接で、全長3.995mのGRヤリスに対して、約35m分の構造用接着剤を使用。これは通常のヤリスより10m以上長い。
*アンダーボデー:前部のフレームワークからトランクのフロアまでを含むクルマの下部構造
続いて、各部品を正確な位置で組み付けるため、メインボデー*をスポット溶接*で仮付けし、その後増し打ちを行うが、ここでもGRファクトリーならではのこだわりが。
*メインボデー:クルマの基本骨格である上部構造
*スポット溶接:接合したい金属に対し、ポイントを定め電流を流すことで溶接する方法
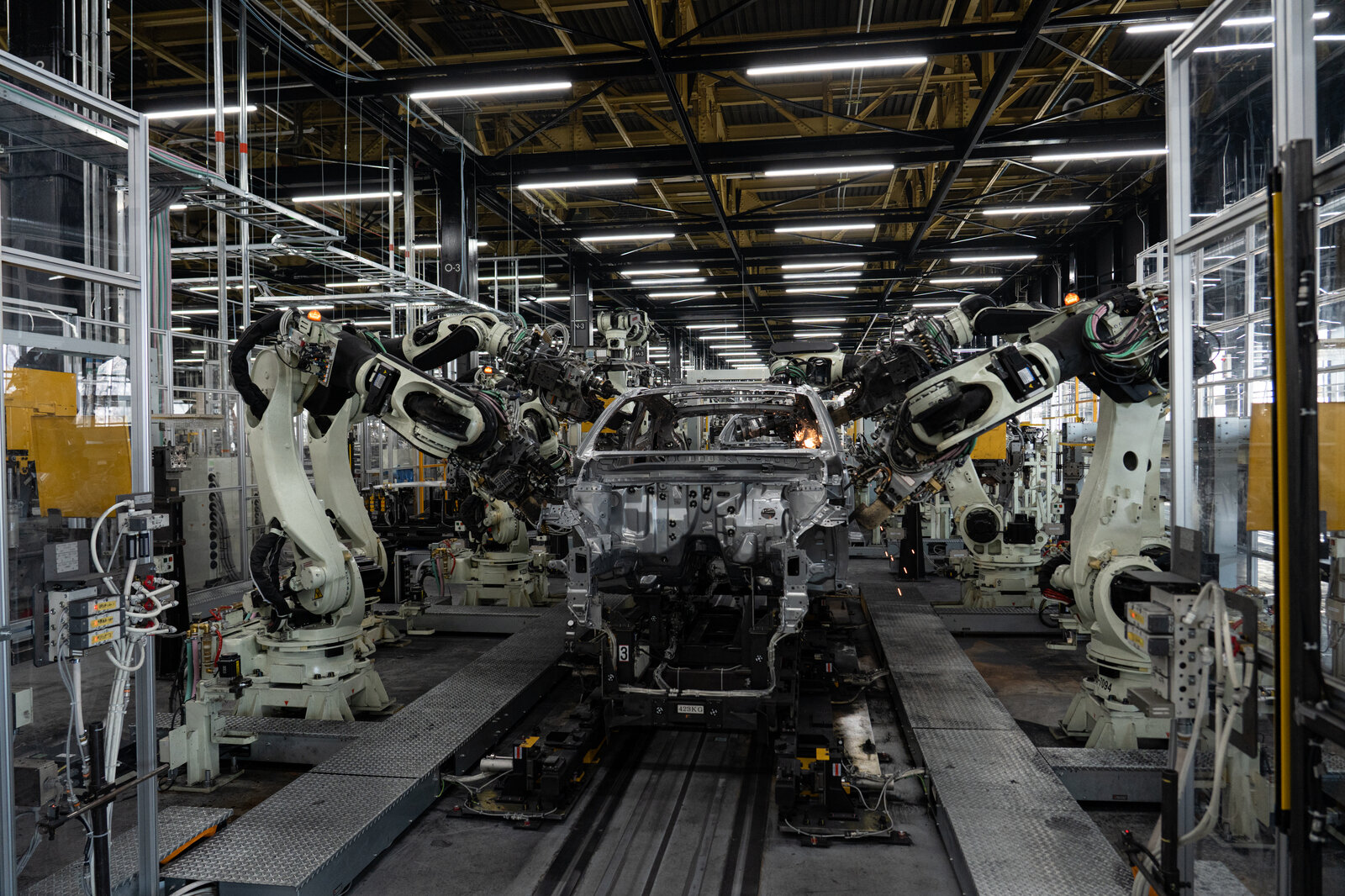
サーキット走行を可能にする高剛性なボデーを実現するため、打点数は通常ヤリスの約3,700点に対し、GRヤリスでは約4,500点。プロドライバーからのフィードバックで、より強固な結合が必要と判断された箇所を選定し、打点を増やしている。
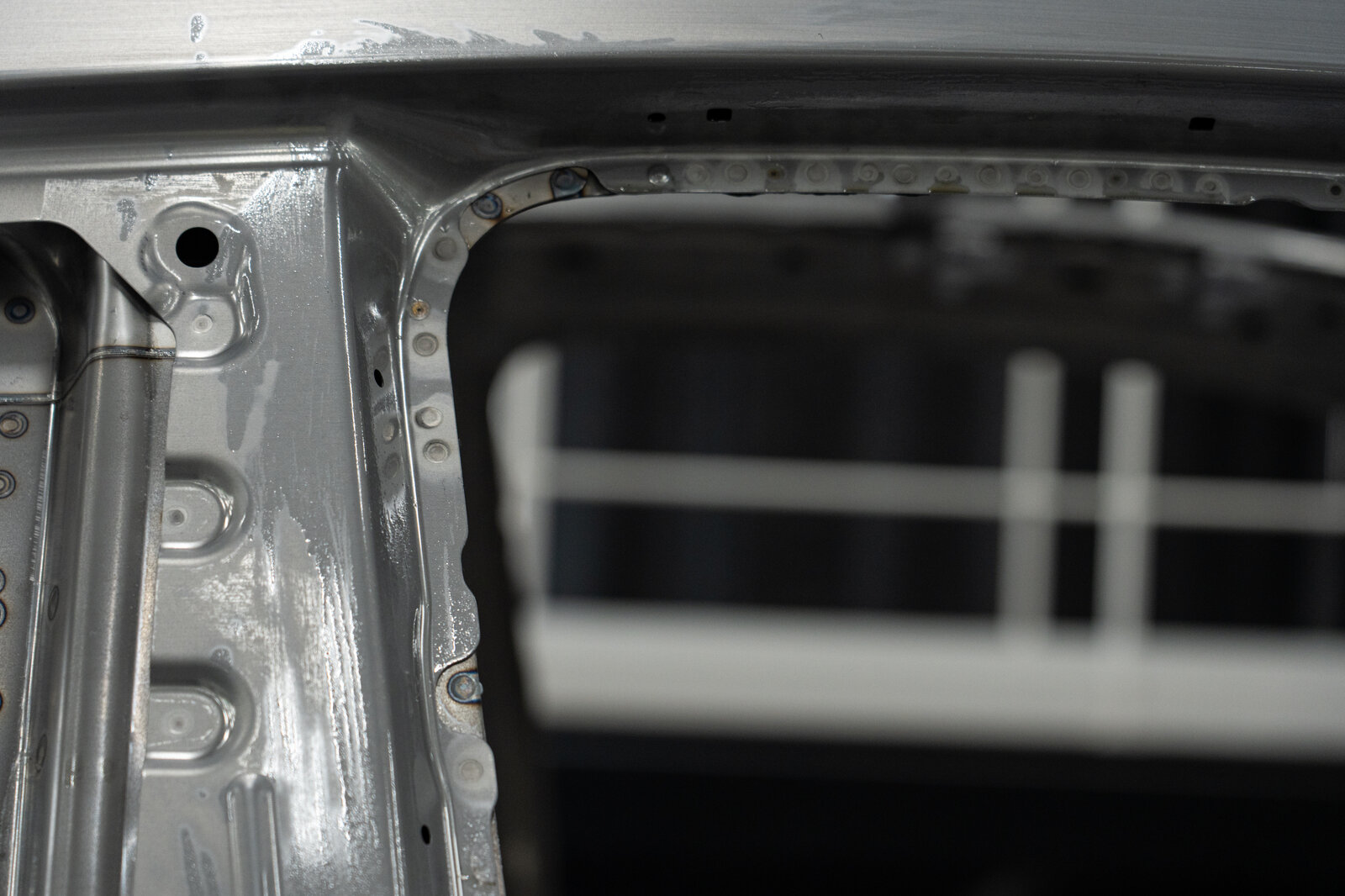
なお、これらの工程を踏んだGRヤリスのボデーは、さび止めを行いフィンランドへ送られRally2車両としても使われている。GRヤリスの骨格がRally2とほとんど同じ素性をもつことは、まさにレースで勝てる車両を市販車にするという逆転の発想の表れだ。
ボデー工程の最後は、設計図と実際の車体の状態を比較、確認する精度検査。こだわりが詰まったGRファクトリーの中でも、特に注目したい工程だ。
どんな工業製品にも一定の基準値内で製造誤差がある。市販車ではまったく問題ないわずかなばらつきも、クルマを限界性能で走らせるサーキットでは大きな差となって結果に表れる。
こうしたばらつきを極限まで抑え込むため、足回り部品をボデーに結合するボルトの穴の位置のずれをコンマ数mmで三次元計測。
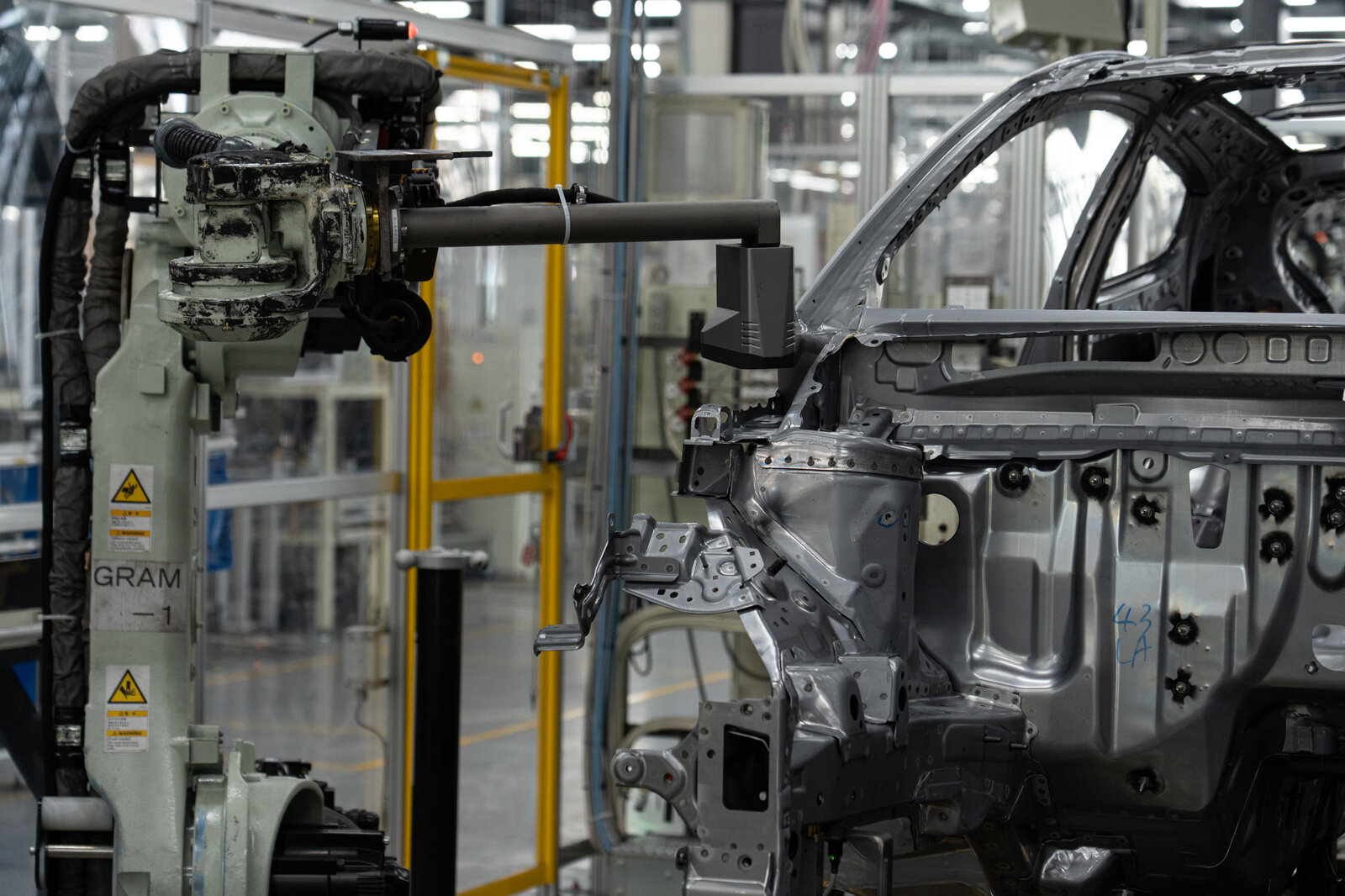
測定データは専用の解析システムへと送られ、設計時に想定していた数値に最も近い仕上がりになるよう、組み付ける部品はずれを最も補完するものが選定される。
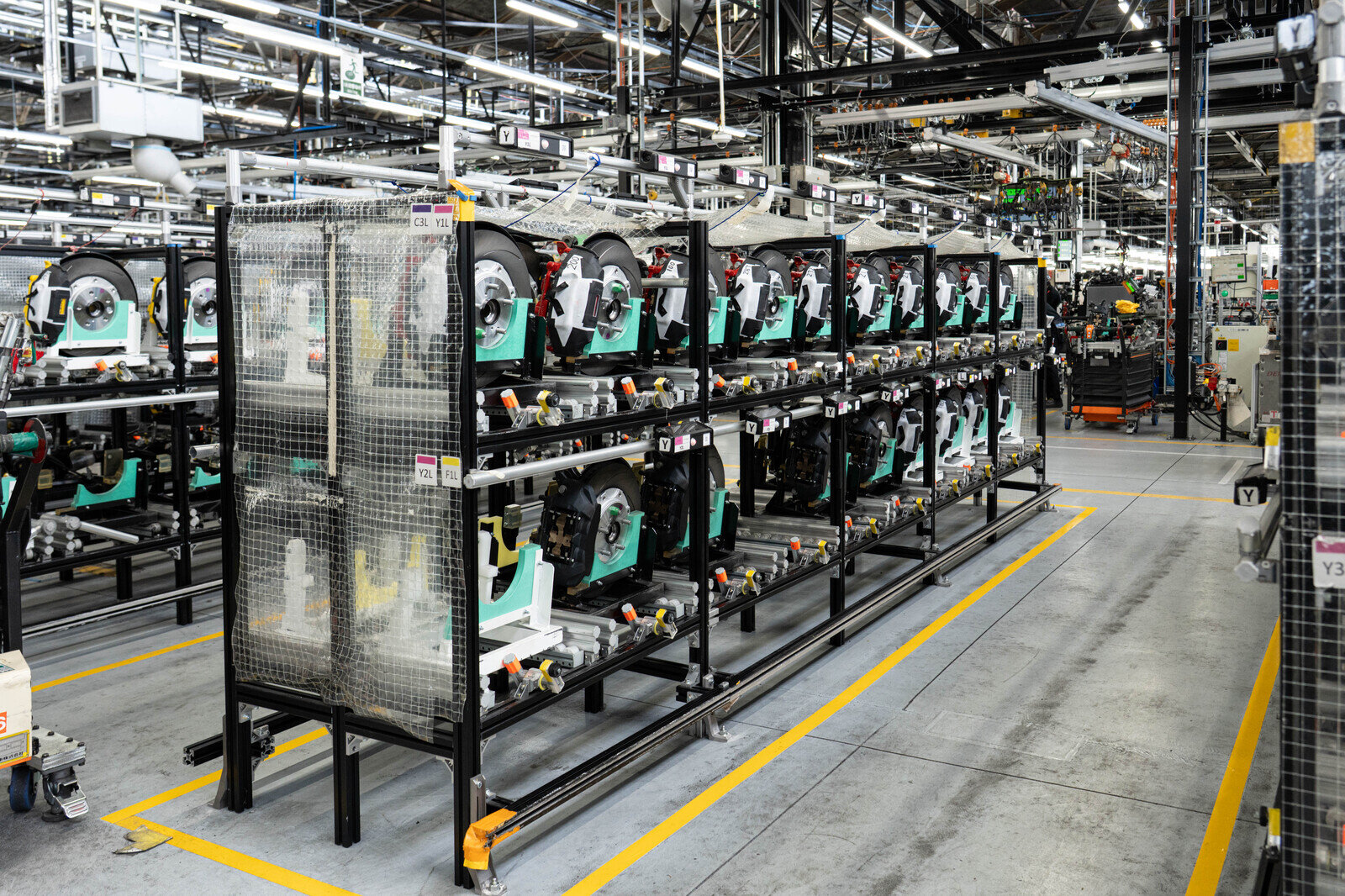
また、一般的な量産ラインでは、吊り下げられた状態で流れていくボデーに対し、作業者は下から持ち上げるようにして足回り部品を搭載する。
しかし、GRファクトリーではモータースポーツの現場同様、水平な床の上に正確に足回り部品をセットし、ボデーを上からかぶせるようにして組み付ける。
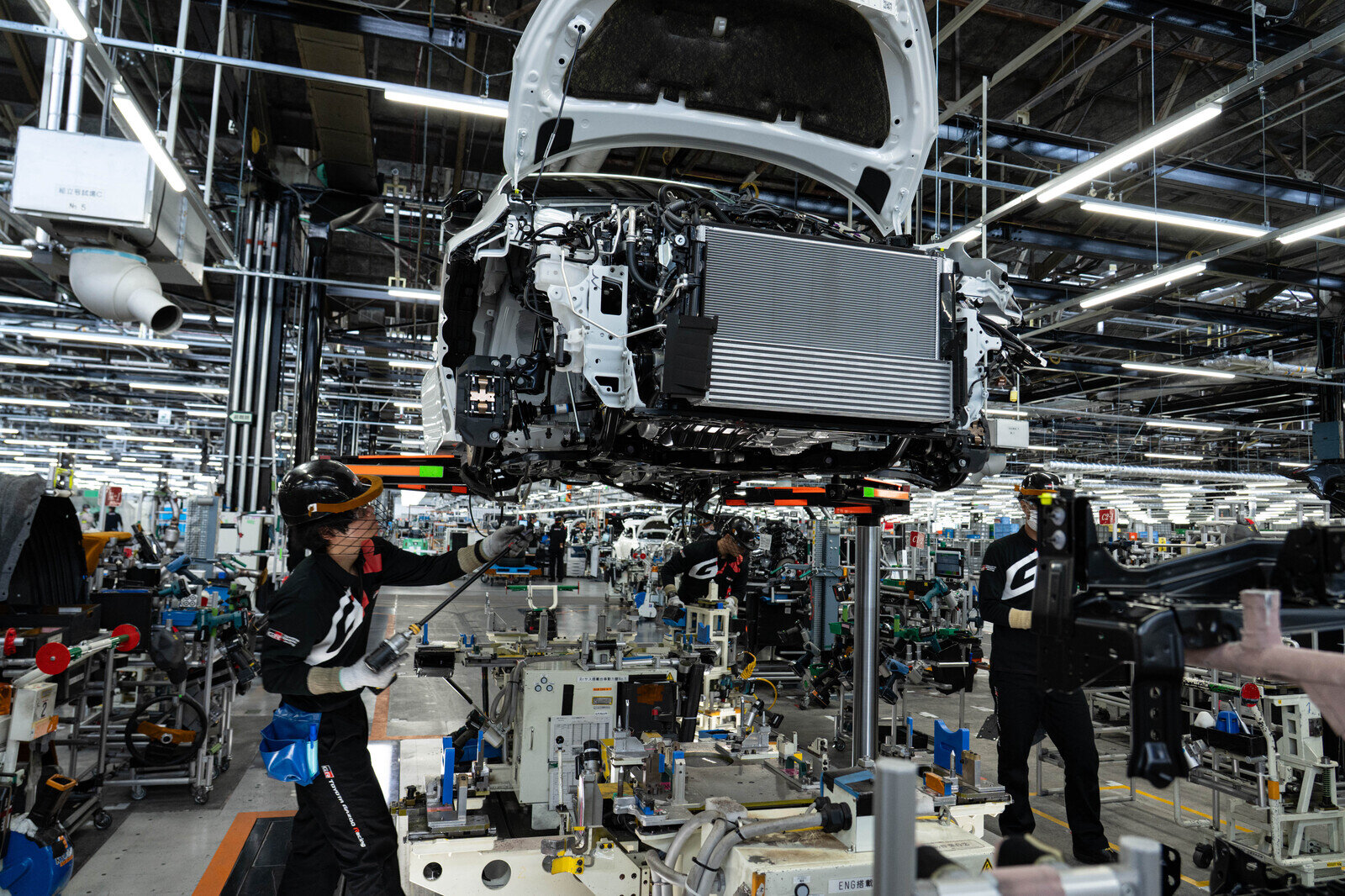
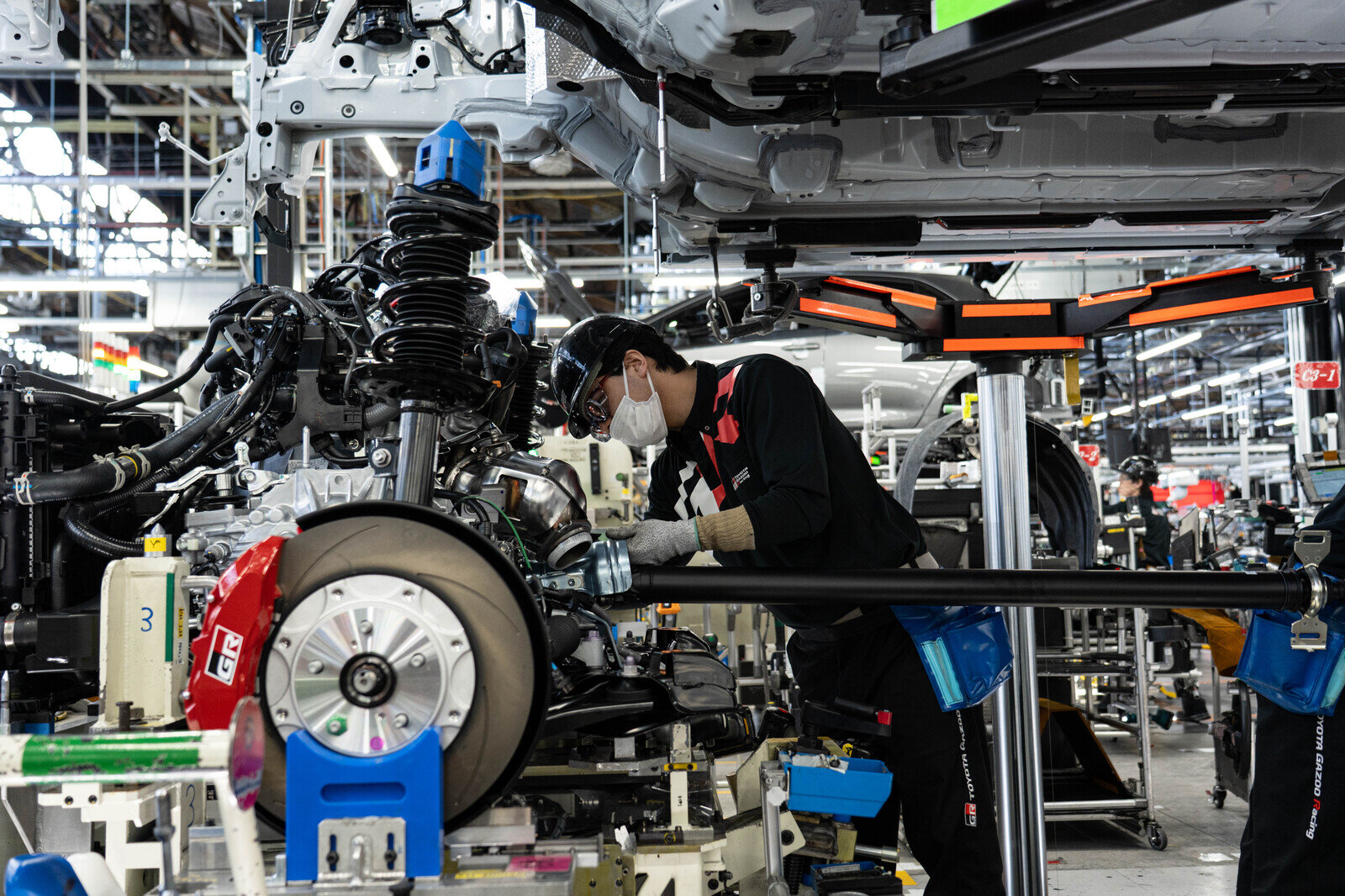
ボデーが静止した状態で行われるため、作業環境が安定。また、ボデーの重みのかかった状態で作業することで、よりしっかりと組み付けられ、精度も高まる。
車両の企画段階から議論に参画し、率直なフィードバックでGRのクルマづくりを支える石浦宏明選手は「普段レースのガレージで僕らが見ている作業と、同じようなことをやっているように見えました。開発段階ではミリ単位で調整してもらいますが、生産段階でもそれを再現しないとお客様に同じ精度でクルマをお届けできないので、本当に感謝です」と語る。
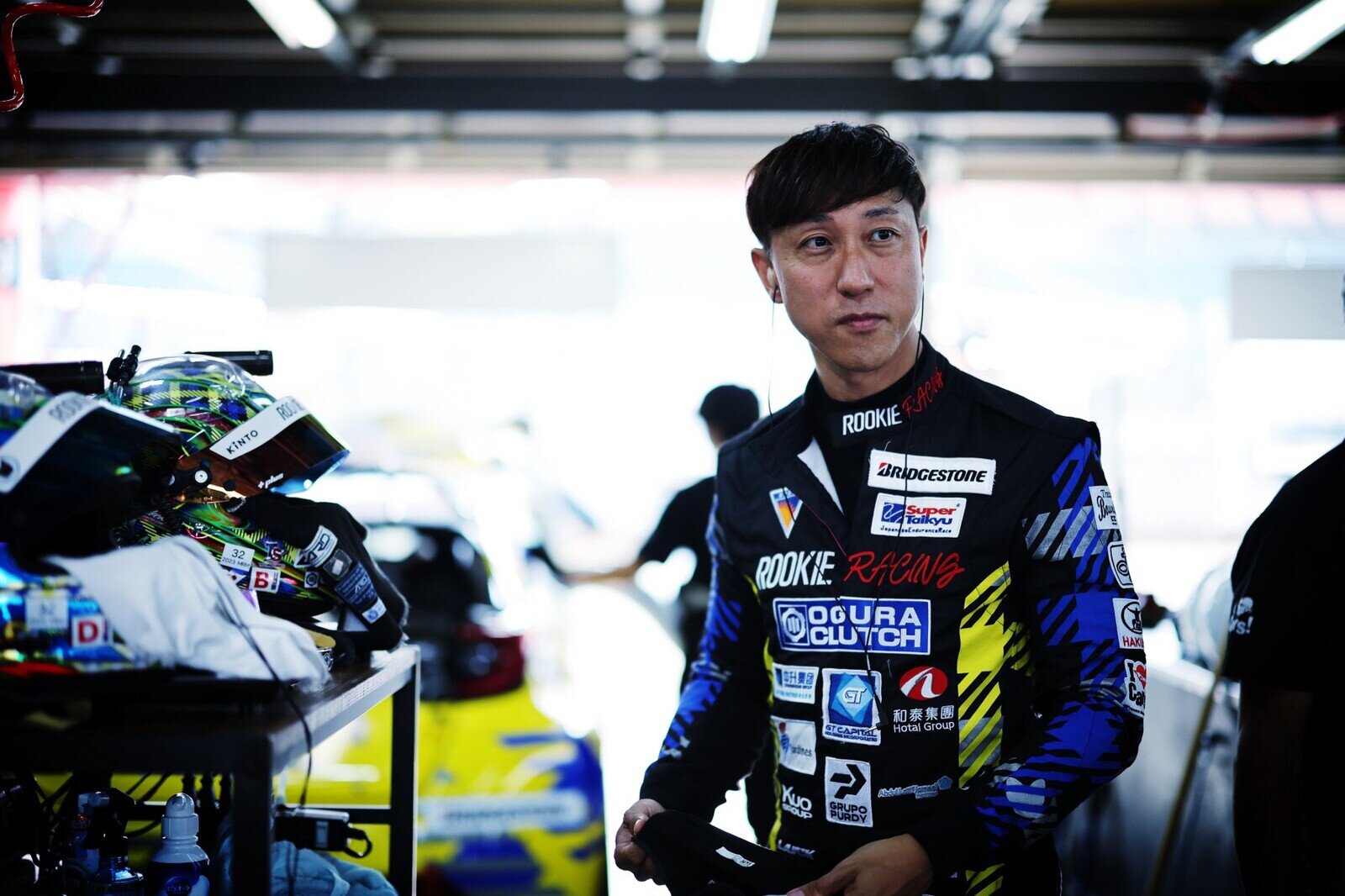
さらに、GRファクトリーを出たすべての車両は、テストコースでの走行試験が行われる。運転評価技能の訓練を受け、認定試験を通過した16名の検査員が感性評価を行う。
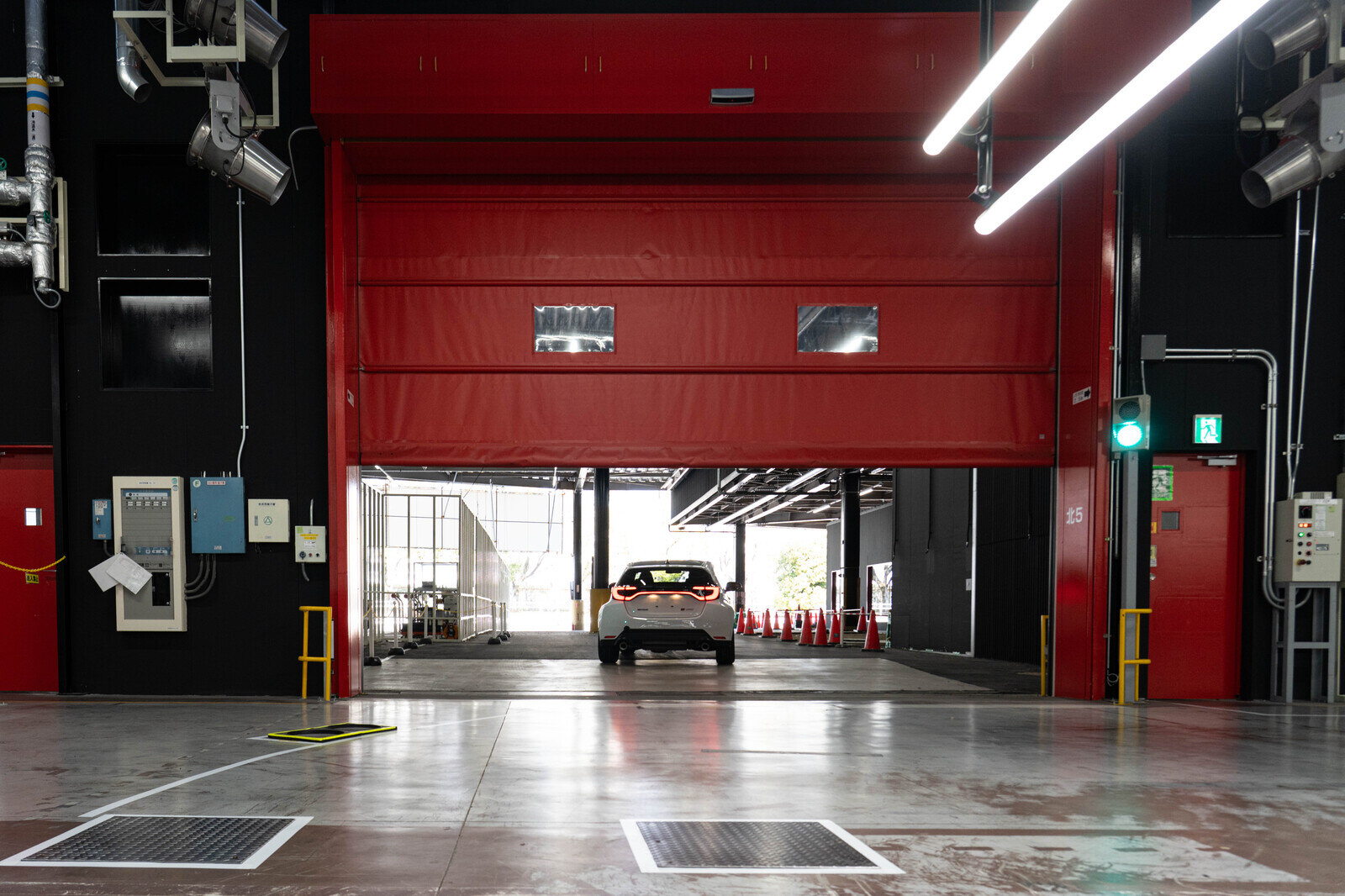
評価項目もまた石浦選手が監修しており、「120kmでの直進安定性」や「レーンチェンジによる操安性*」「ブレーキ時の挙動や騒音」など14項目。結果はすべて保管され、開発や生産へフィードバックされる。
*操安性:操縦安定性。車両が安定して走行、停止、旋回できる能力
こうした最終チェックを経たクルマが、晴れてお客様の元へ届けられる。
ラインの中においても、一台一台に徹底的に向き合ったモノづくりを行うことで「走る・曲がる・止まる」に違いを感じられるGRならではのクルマがつくられる。
GRヤリス開発責任者・齋藤尚彦チーフエンジニアは次のように語る。
齋藤チーフエンジニア
マスタードライバーであるモリゾウさん、プロドライバーの石浦宏明さん、大嶋和也さんたちがつくったクルマと寸分たがわず、同じ性能でお客様に乗っていただきたいという想いを実現できる。ドライバーのフィードバックを受けて常に改善を続けていける。
(GRファクトリーは)これまでのトヨタにはあまりなかったような特徴をもった場所だと思います。
終わりなきGRの挑戦
一般的な量産ラインとは異なるGRファクトリーでのモノづくりは、「人づくり」にも大きく貢献するという。
元町工場の宮部義久工場長は従業員の日々の成長についてこう述べている。
宮部工場長
私たち製造はモータースポーツからのフィードバックによる進化だけでなく、毎日1台1台のクルマのデータを蓄積しています。
例えば、選択組付では、左右バランスに加え、前後バランスを加えたアルゴリズムの変化を確認。工業製品における“ばらつき”に対する解が存在しない中で、今よりもっと“ばらつき”を小さくする方法を探す。現場だからこそ得られる大量の情報を基に、もっといい走りにつながる改善、進化を、皆さんには日々続けていただいています。
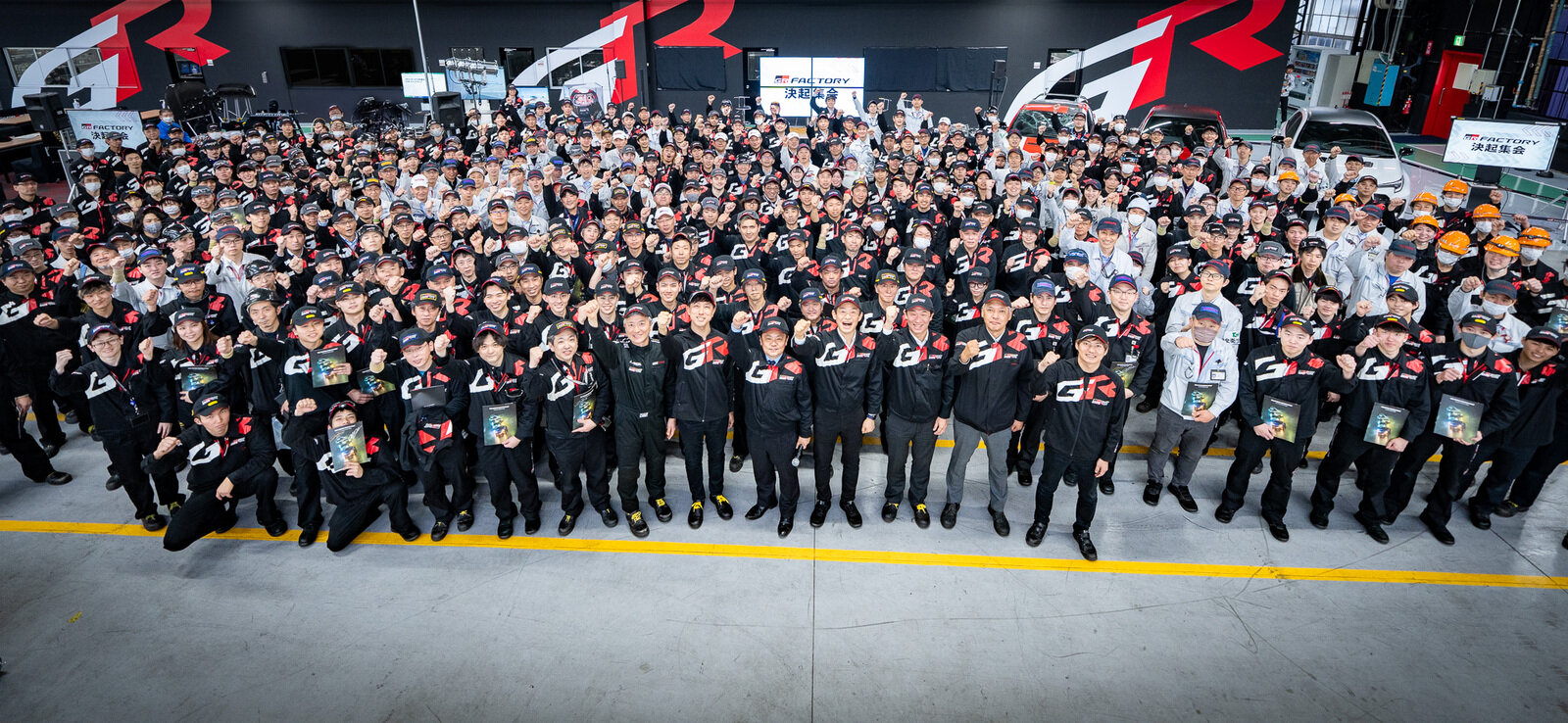
これまで私たちは、安全、品質、生産性を日々改善、進化させていくことは得意でした。
しかし、このGRファクトリーでは、クルマの進化だけでなく、もっといい走り、もっといいクルマに向けて、私たちの技能を日々進化させていただいています。
なお、GRファクトリーは2025年4月18日より、GRヤリス、GRカローラのオーナー向けに工場見学を開始。
MyTOYOTA(WEB)、MyTOYOTA+(アプリ)にて、該当するアカウントへ案内が配信されている。
GAZOO Racing Companyの高橋智也プレジデントが「これからどう改善させていくのか、もっといいクルマづくりのために工場をどう変えていくのかという全社に先駆けた挑戦ができる場所」と語るGRファクトリー。
モリゾウの悲願を形にする、唯一無二のラインを見に来ていただきたい。
