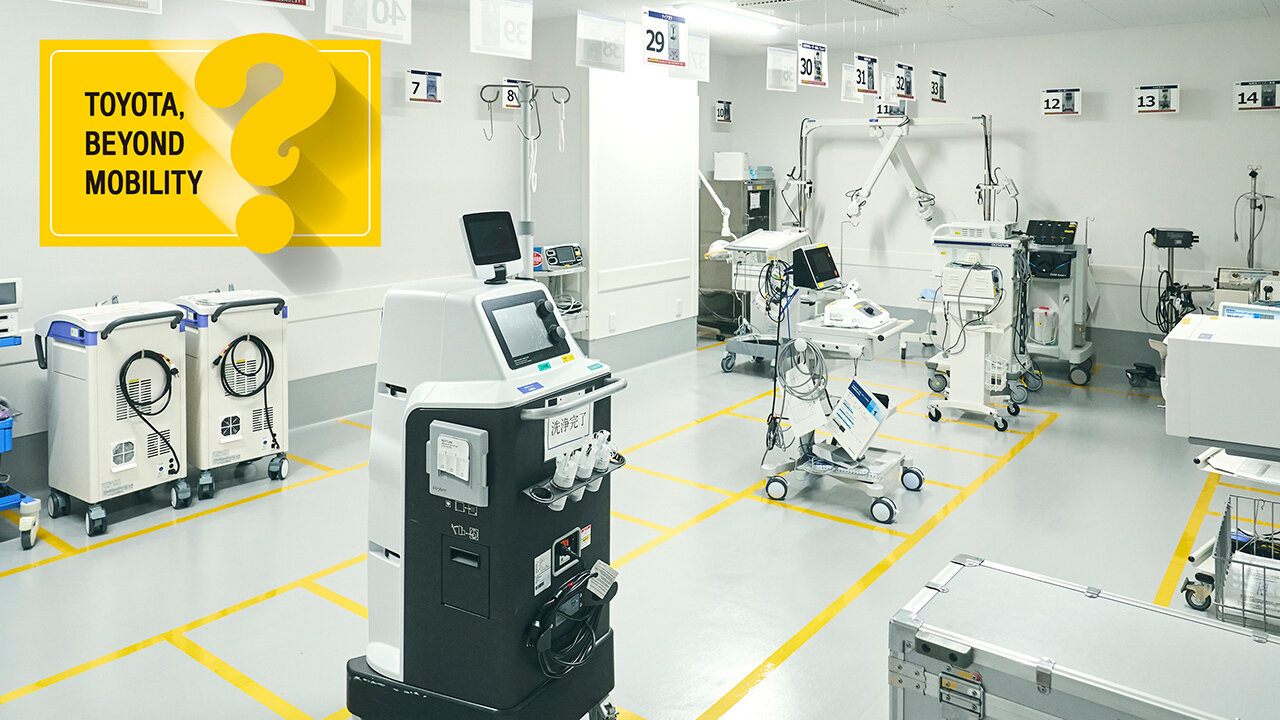
This is part of a series showcasing Toyota's activities in non-automotive fields. This time, we find out why the company operates an enormous hospital.
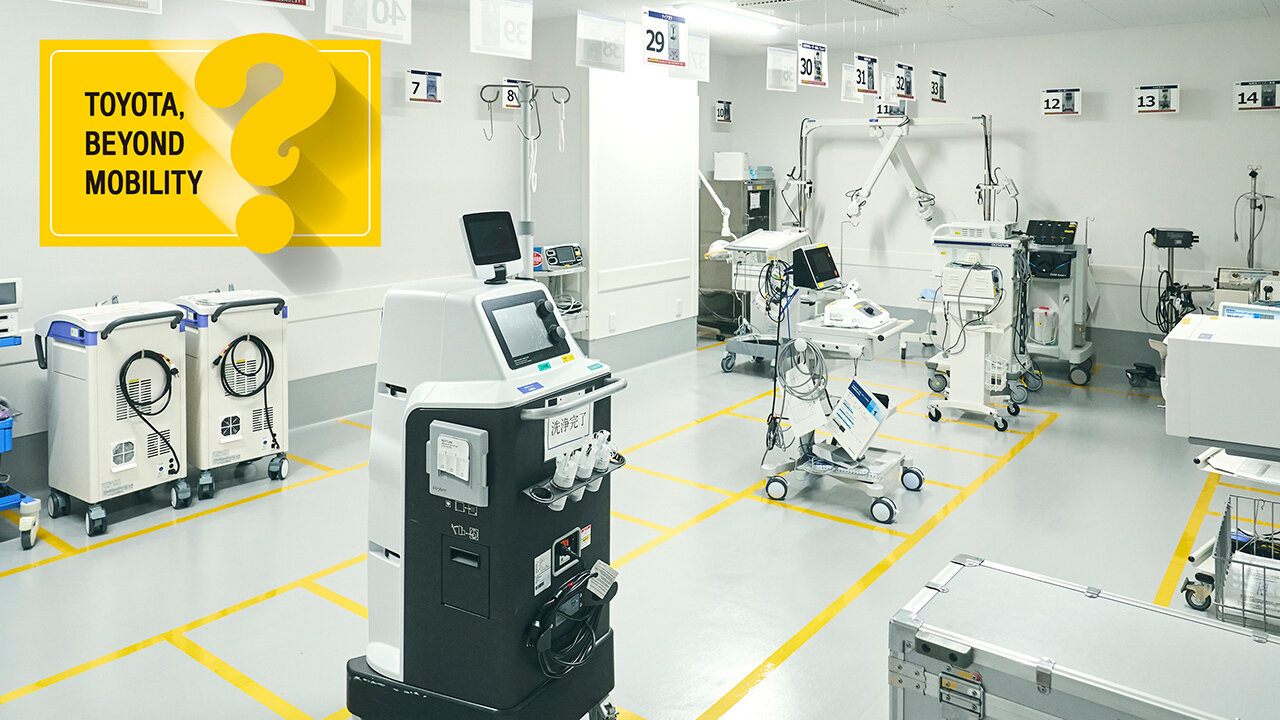
Hammers, electric screwdrivers, even a supersized ruler... any guesses what this place might be?
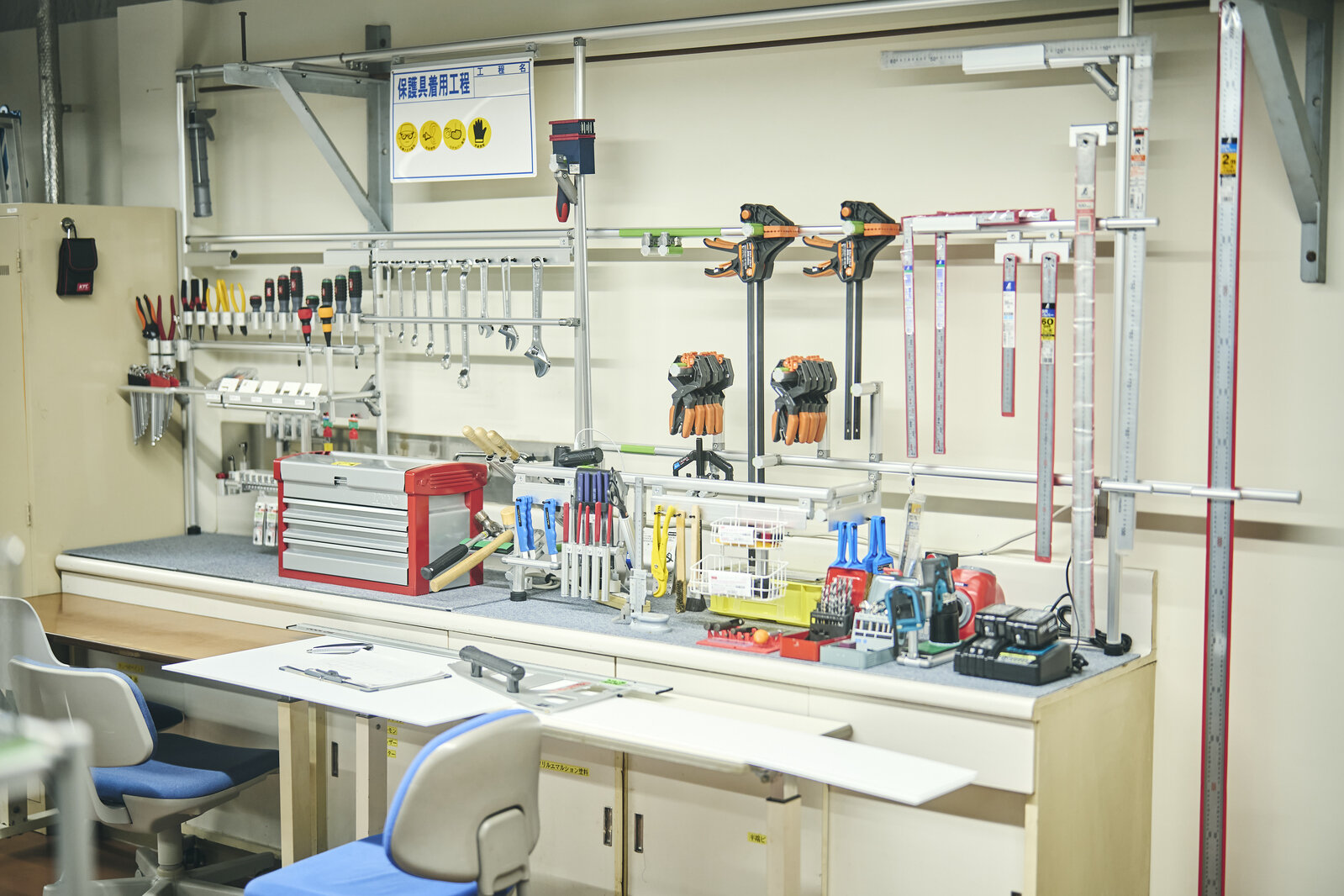
Though the scene looks more like one of Toyota’s production plants, this is in fact a room at a hospital. Why would a hospital be set up with tools for monozukuri? The reasons will soon become clear.
Just another company department
We recently visited Toyota Memorial Hospital in Toyota City. With 1,256 employees and 527 beds, this vast facility supports the region’s healthcare services by looking after patients from the local community.
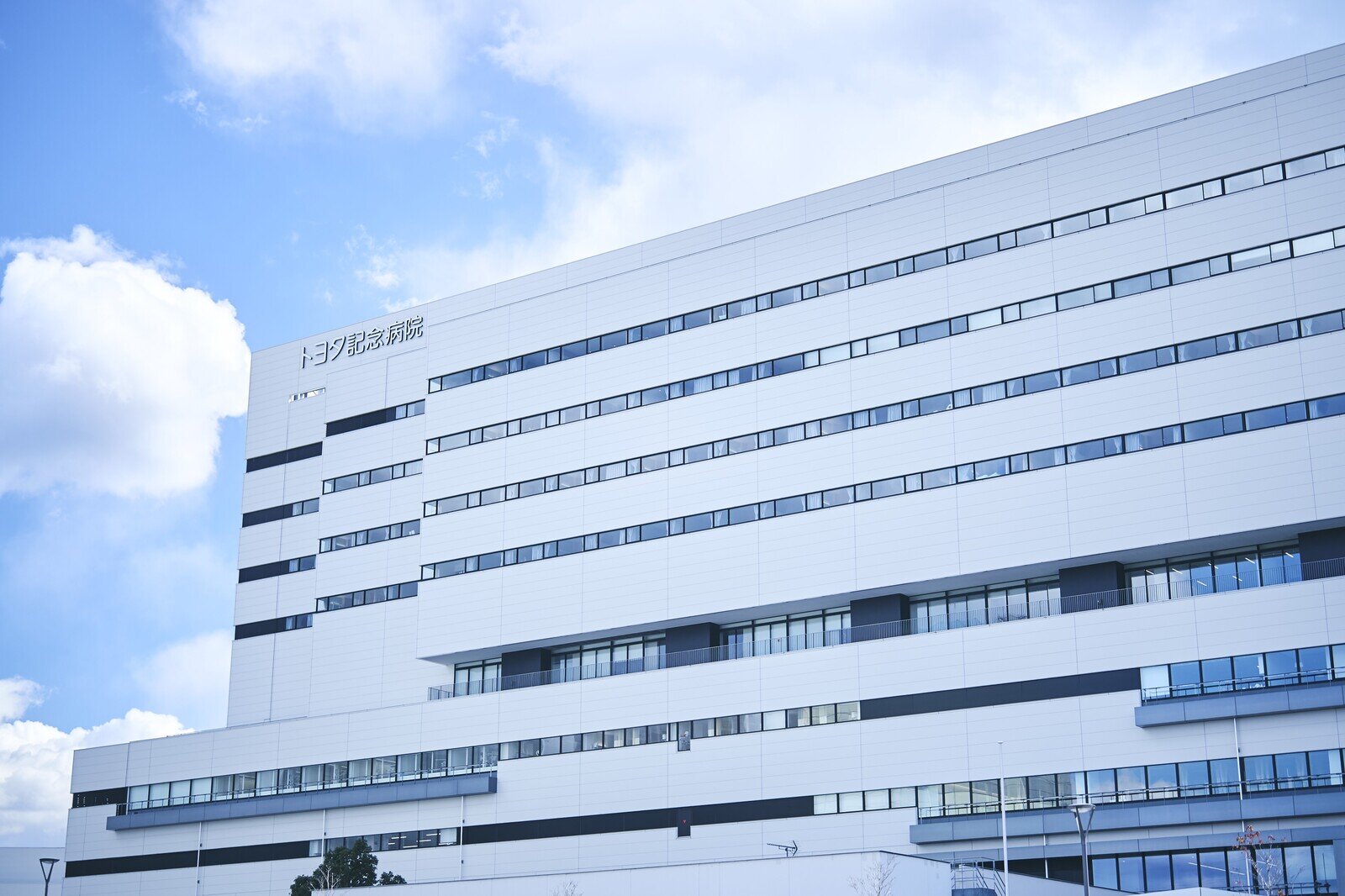
All of the doctors and nurses working here are actually Toyota employees, and the hospital itself is a department within the company. That explains why nursing uniforms can be seen at Toyota Motor Corporation’s annual entrance ceremonies.
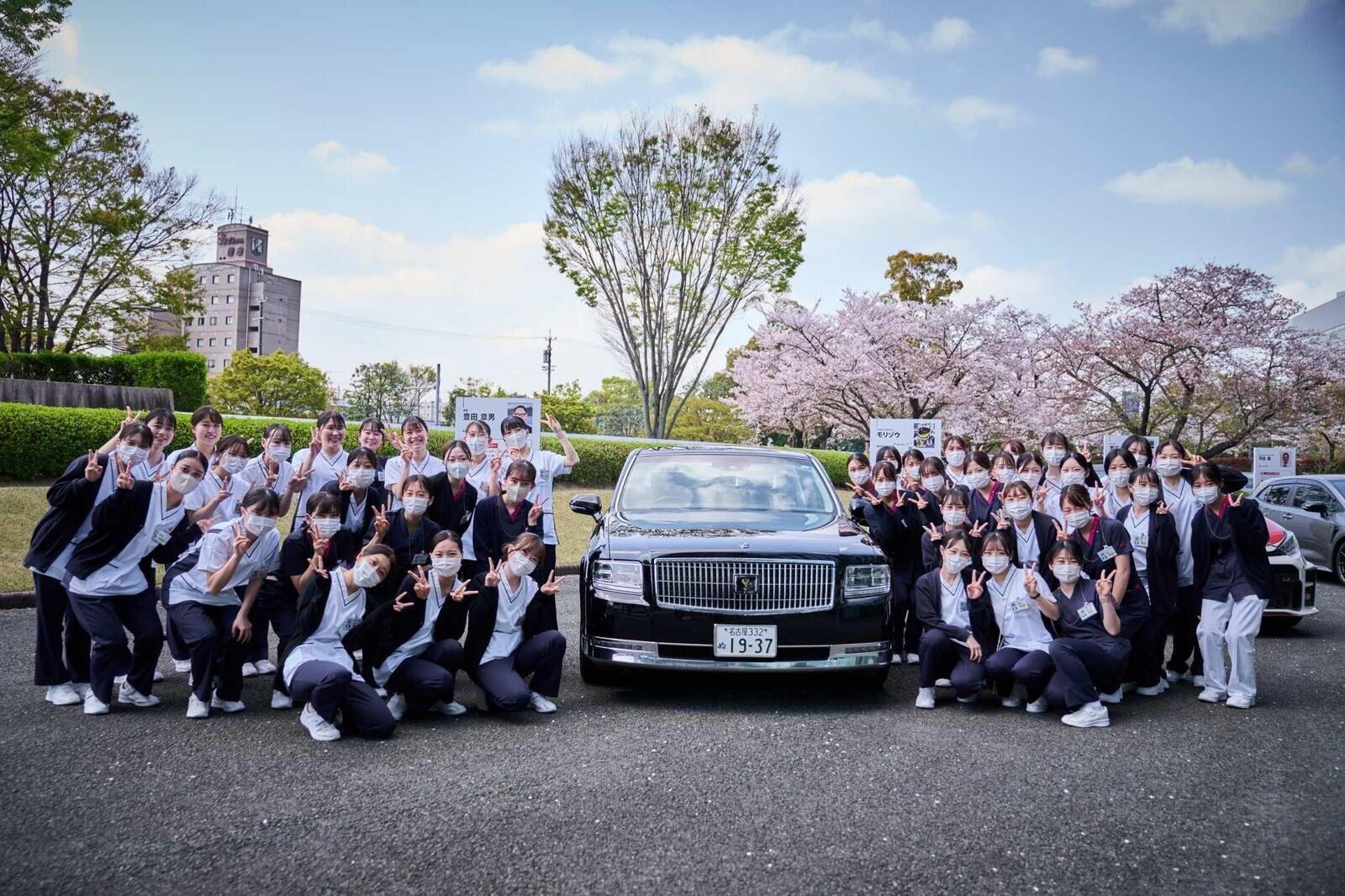
One of our past stories showcased how the hospital used robots to eliminate more than 200 hours of unnecessary night shift work per year.
There was some initial backlash verging on acrimony as carmakers tried to tell medical professionals how they should be doing things. But now the kaizen mentality has taken root, and with a new ward also completed, staff say several astonishing improvements are underway.
Even having a workshop like the one above is rare among Japanese hospitals.
Yoji Akiba, GM, TPS/Kaizen Promotion Group, Administrative Management Department, Toyota Memorial Hospital
With the hospital being so large, just going to fetch things takes up much of the nurses’ time. Through the Toyota Production System (TPS), we are working on improvements to eliminate such waste wherever possible.
Less waste means more time spent with patients.
When someone says, “It would save us time if we had shelves here,” for example, we always listen to genba needs. Be it shelves or anything else that makes work easier, we design and make it ourselves. That’s why we need a workshop inside the hospital (laughs).
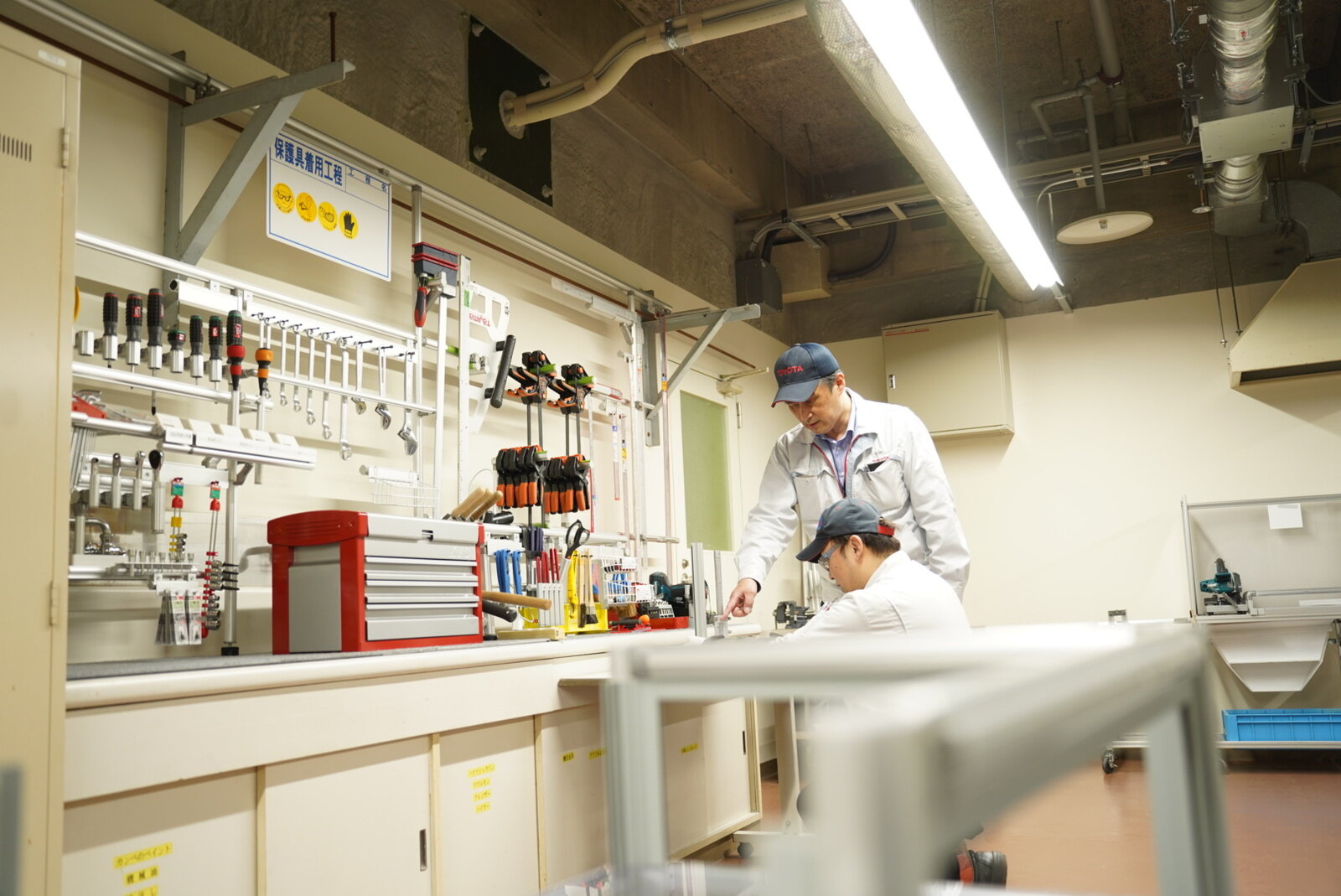
Making equipment ourselves also means we can shorten lead times, which is vital in the medical field, where people’s lives are at stake.
After joining Toyota in 1986, GM Akiba developed his skills and expertise in the carmaking genba, including engine parts. Then in 2018, he was transferred to Toyota Memorial Hospital. Taken by surprise, he found himself wondering, “Why me?”
Since then, his TPS/Kaizen Promotion Group has grown from a one-man operation to a team of eight. Here we take a look at some of the fascinating improvement measures the group has undertaken.
A catalog of kaizen!
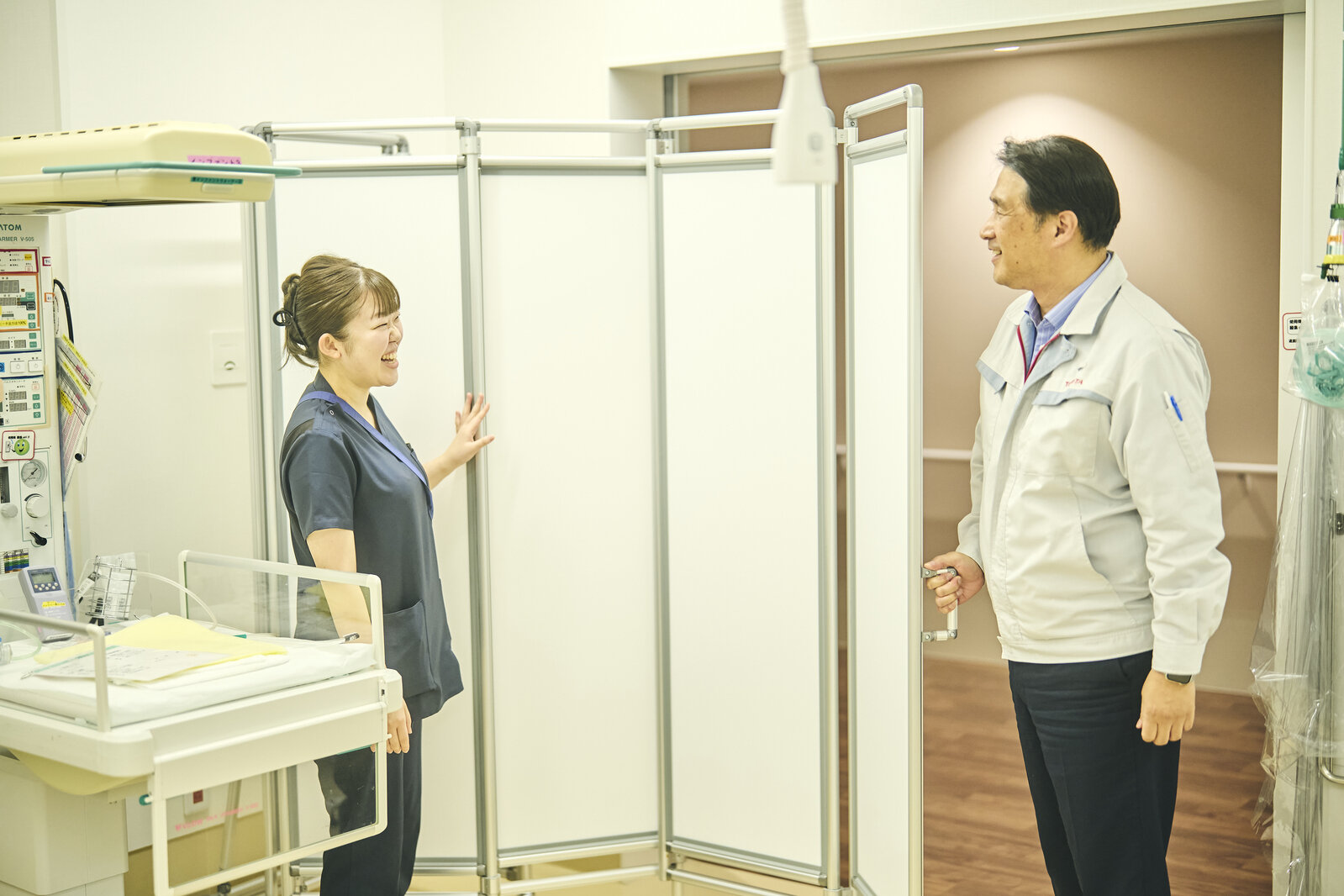
These delivery room screens were made with materials from Toyota’s workshop, based on ideas from midwives. Unlike off-the-shelf products, they are sized to partition the space precisely as needed.
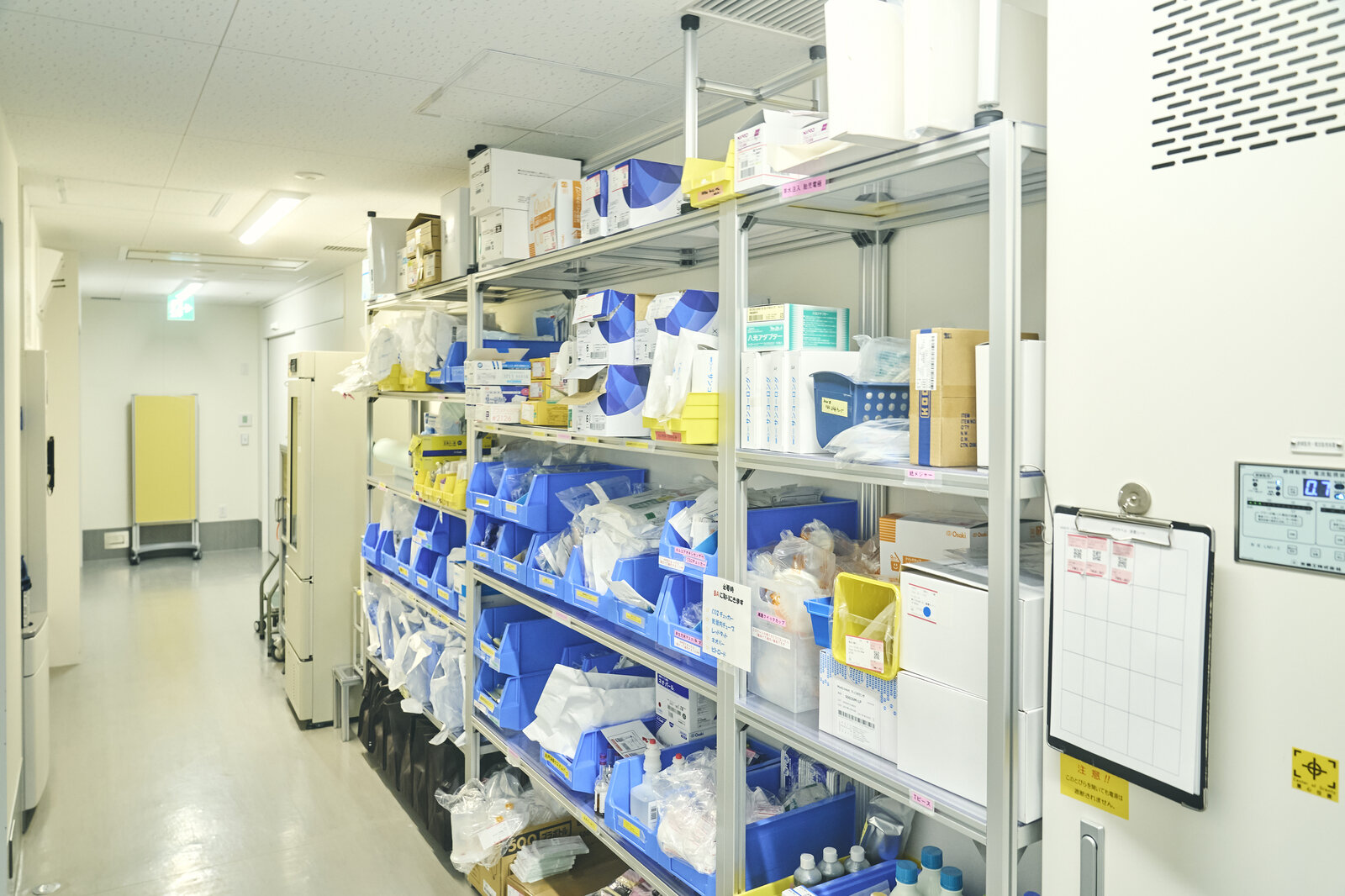
In the corridor behind the delivery room, these large shelves were also made in a snap. By reducing the time spent fetching items, they allow staff to remain by the side of anxious mothers-to-be. The shelves were custom-built to fit and are equipped with stoppers to prevent them from falling over in an earthquake.
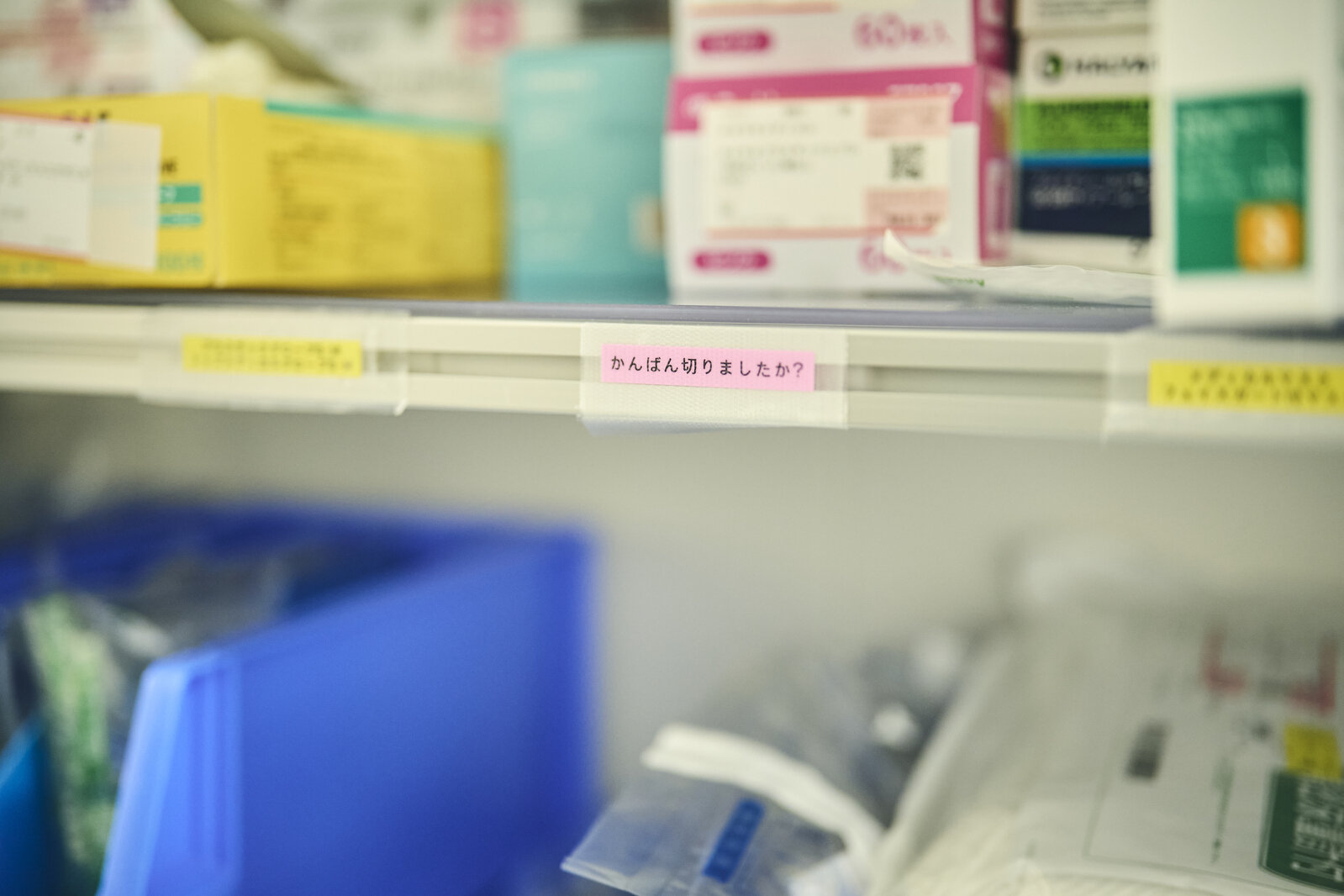
Just as in Toyota’s plants, supplies are accompanied by kanban cards that make it easy to find items or see which stocks need replenishing.
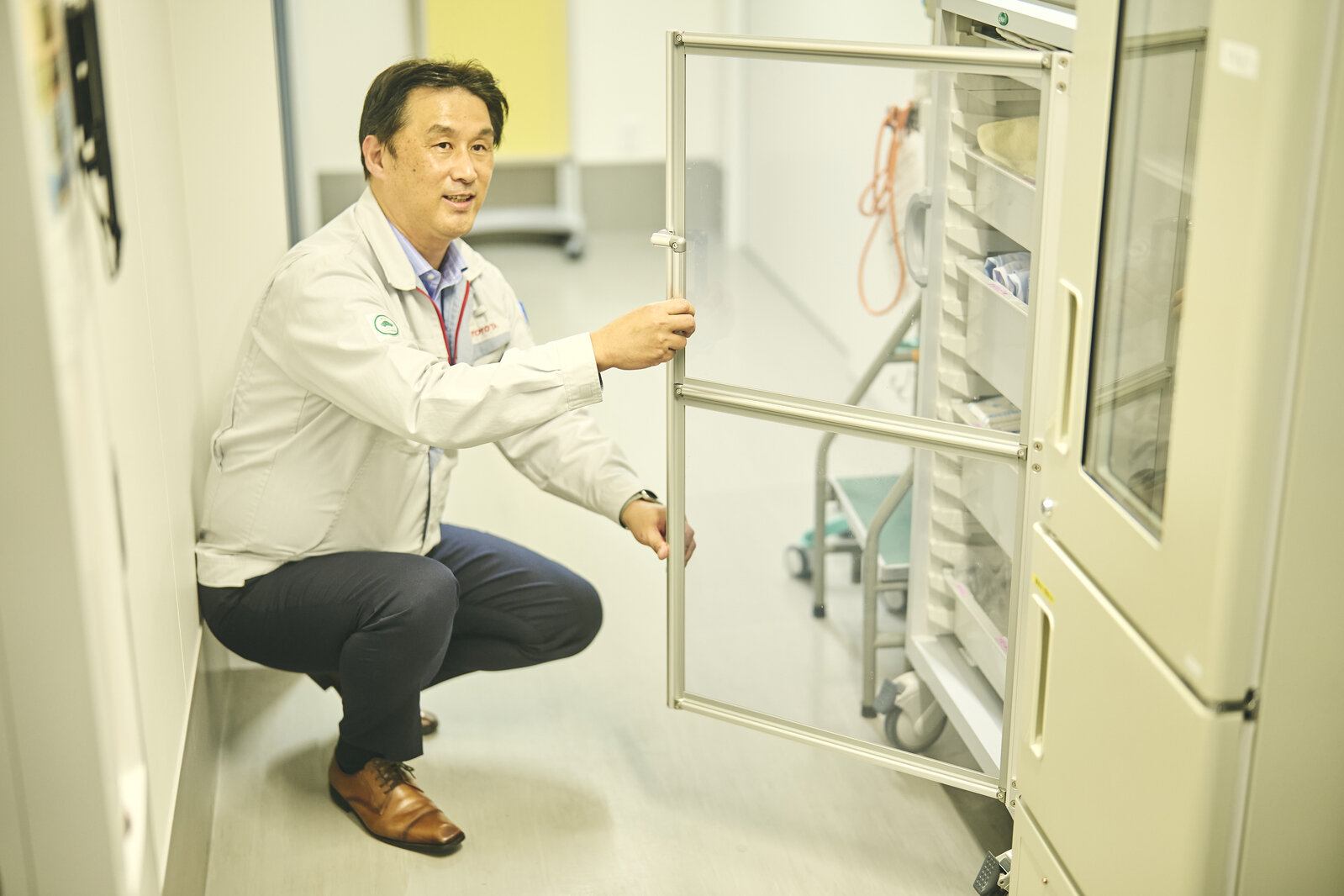
Doors were mounted on certain shelves to hygienically store sanitary items. This significantly reduces expenses compared to buying new.
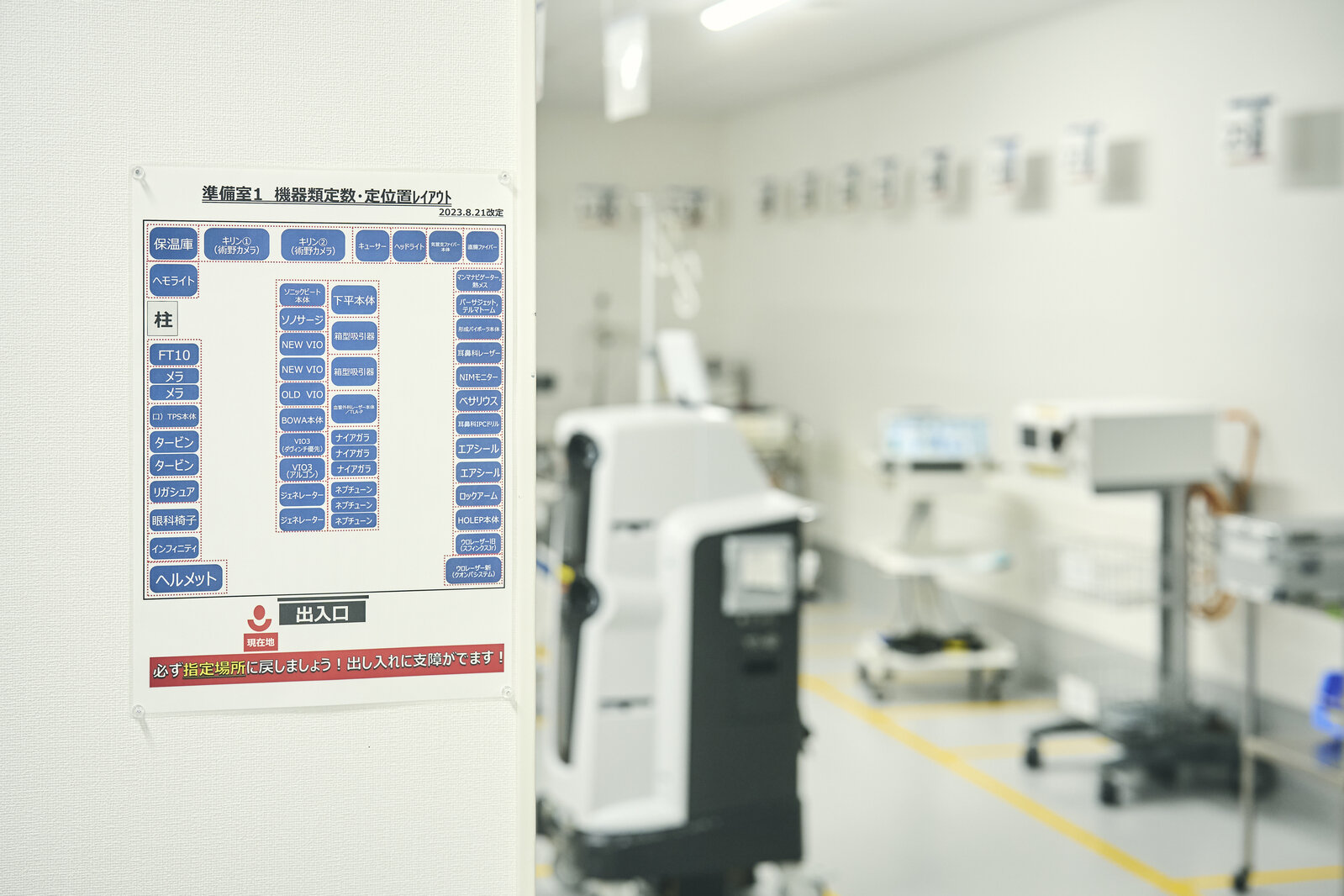
Medical equipment storage locations have been optimized based on the frequency and order of use. Anyone can quickly find what they need, eliminating wasted time before and after surgeries.
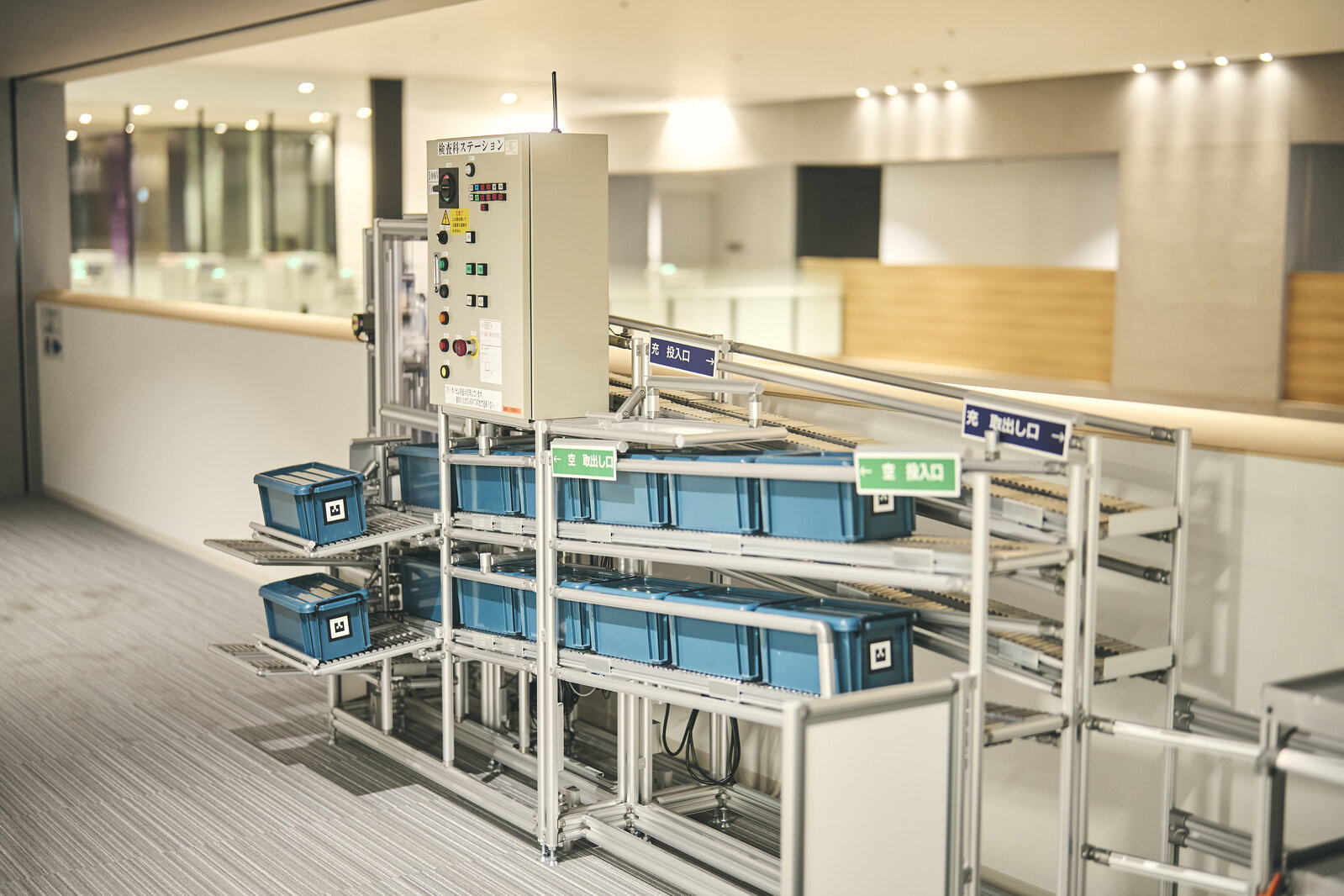
Karakuri devices that use slopes to make moving heavy objects easier have also been incorporated throughout the facility.
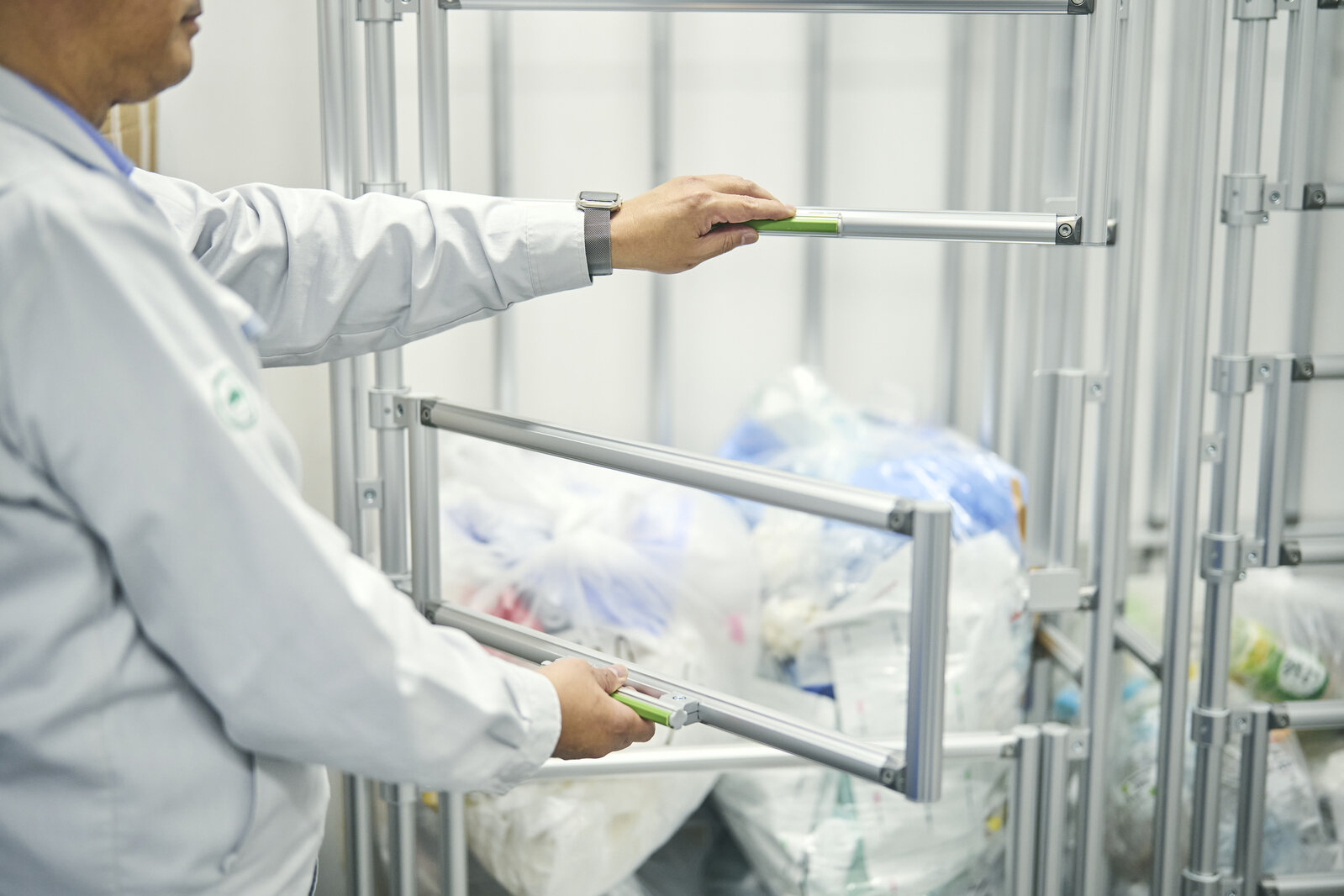
To solve the problem of garbage bag piles tipping over, the workshop also created carts that allow trash to be placed in at different heights, eliminating not only waste, but also stress.
“Whatever we ask for, they make it right away,” the doctors and nurses tell us happily.
GM Yoji Akiba
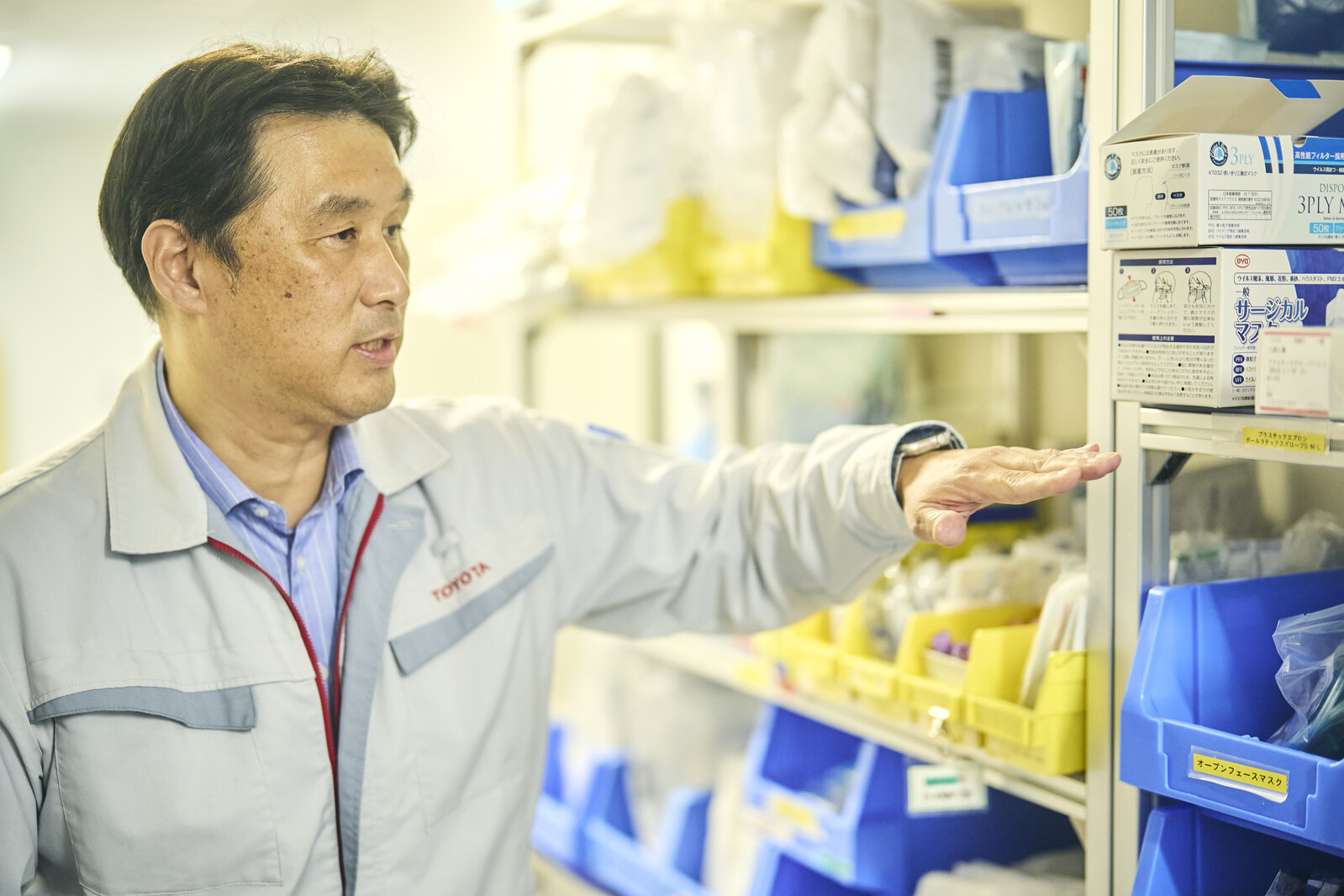
You could just buy existing products, but instead we can make them ourselves at a fifth or tenth of the cost. On top of that, we can instantly rebuild something that doesn’t work in practice.
Since moving to the new ward about a year and a half ago, we have already made more than 600 items, which adds up to around 15 million yen in cost savings.
Because we make their work easier, the doctors and nurses come to ask for help time and again. This cycle ultimately leads to better healthcare services. I am glad that, even as someone who is not a medical worker, I can contribute to local healthcare.
Having spent many years honing his skills in the carmaking genba, GM Akiba showed a carmaker’s pride when he spoke of contributing to the local community.
On the next page, we look at this unusual mobility device, an advanced solution found in no other hospital. What could it be?
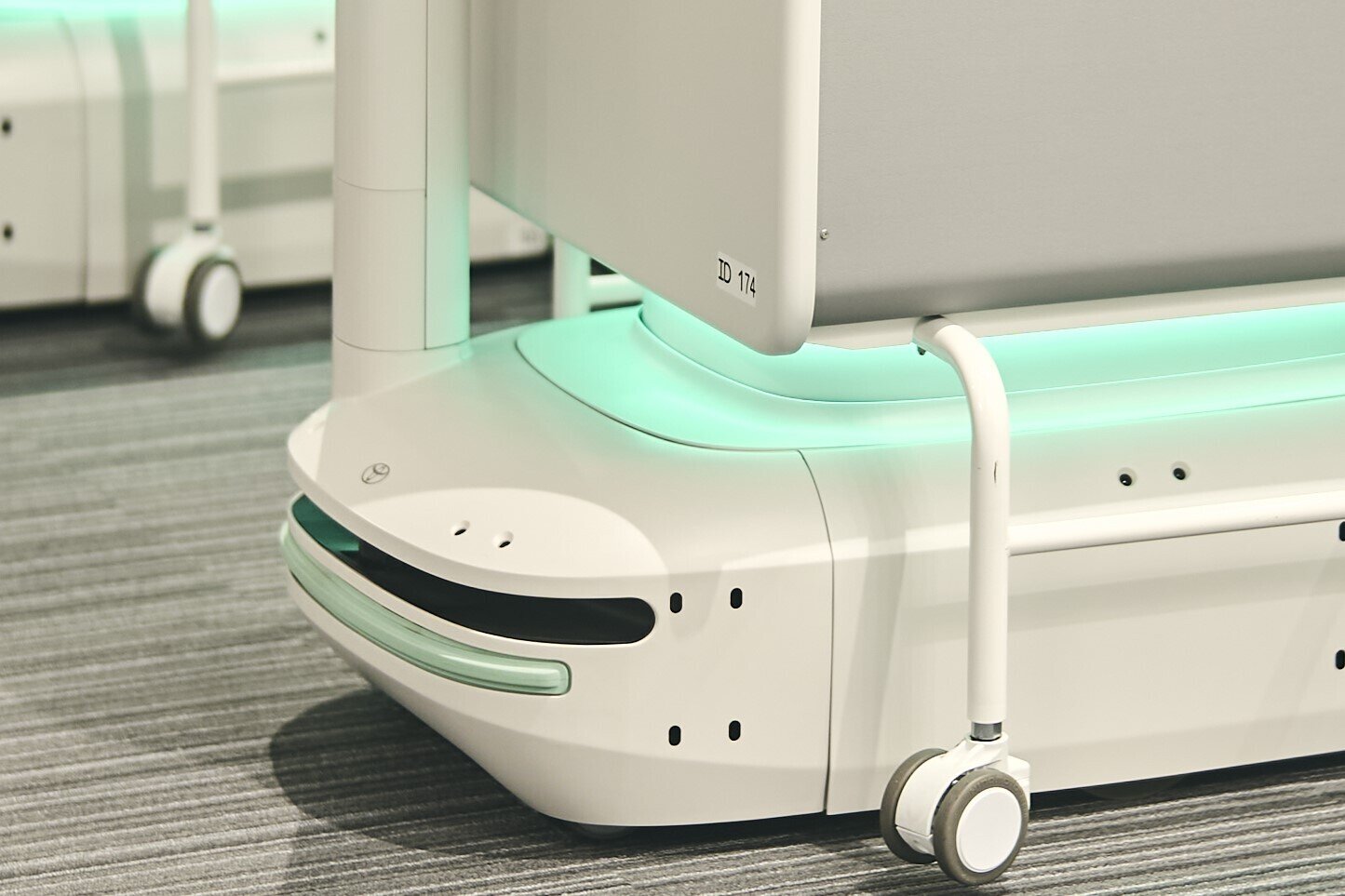