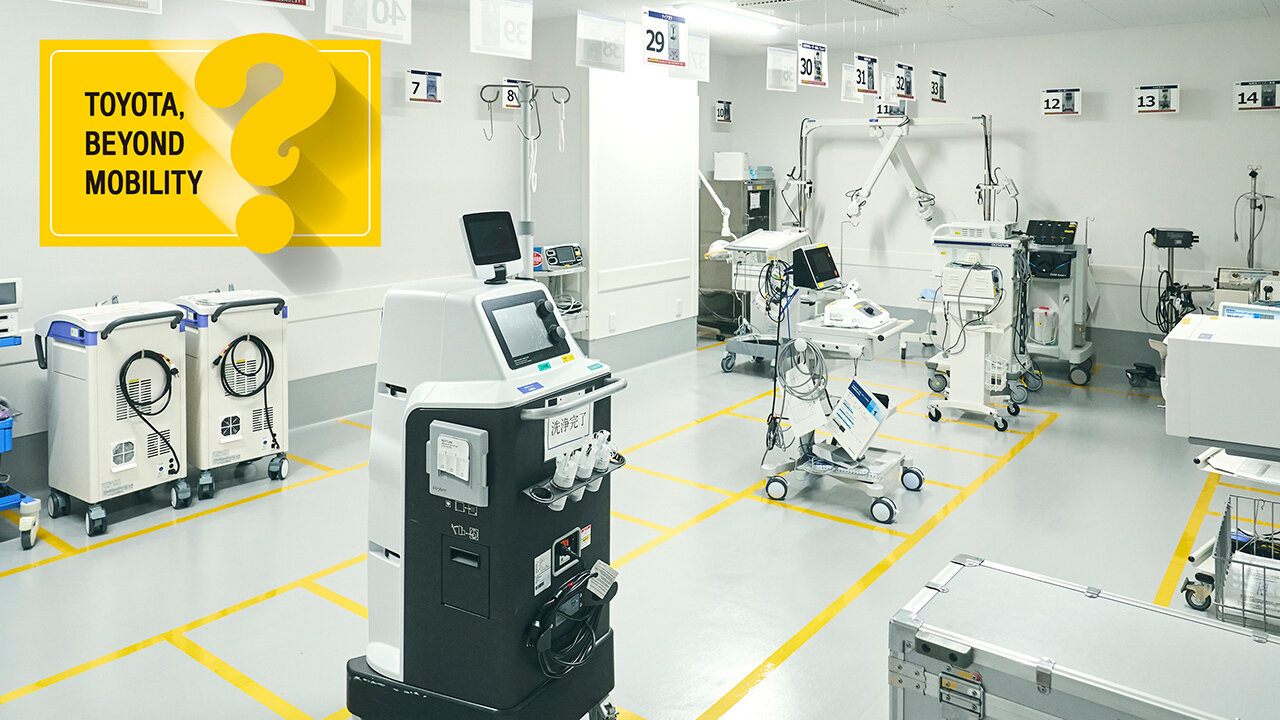
This is part of a series showcasing Toyota's activities in non-automotive fields. This time, we find out why the company operates an enormous hospital.
No more time-wasting robots
The hospital’s hallways are home to 24 Potaro robots, which autonomously transport medical equipment. They are another example of the Toyota difference.
These robots handle simple tasks that require no human input, such as delivering medicines and specimens.
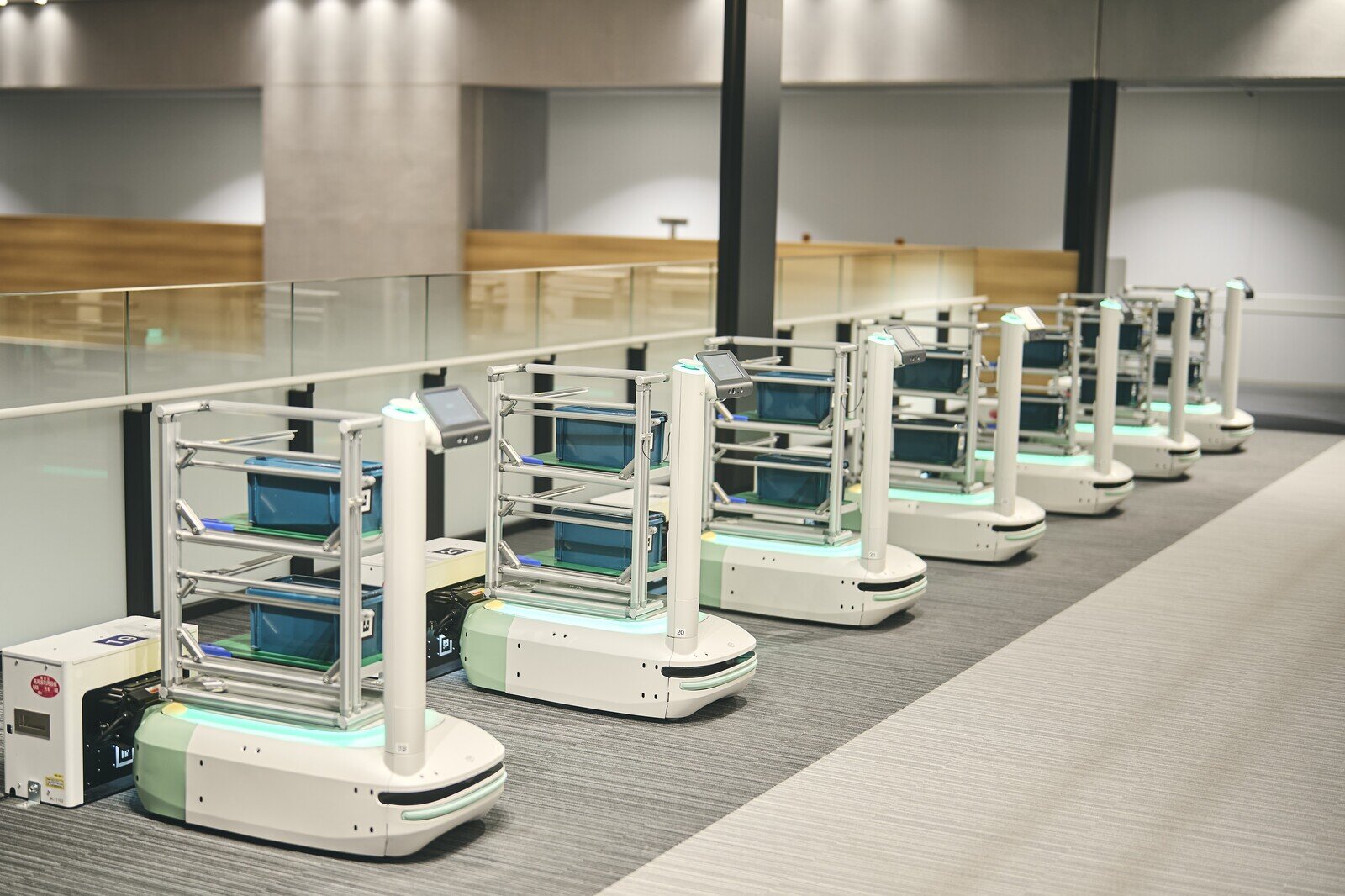
They have come a long way since our last report in 2022. Back then, the cart for carrying goods was integrated into the robot, meaning that nurses had to manually transfer the items that were transported.
Now, the robots have been redesigned to pick up carts and their cargo, then automatically drop them off at their destination. After unloading, the robot can immediately head to its next job.
This upgrade eliminates wasted time, not only for humans but also for the robots themselves. And one other thing: these robots also ride elevators by themselves, a sight that may startle first-time visitors to the hospital. Make sure to check out the video link at the end of this article.
The hospital has also devised other ways to increase time spent with patients.
Mitsunori Iwase, Director (MD)
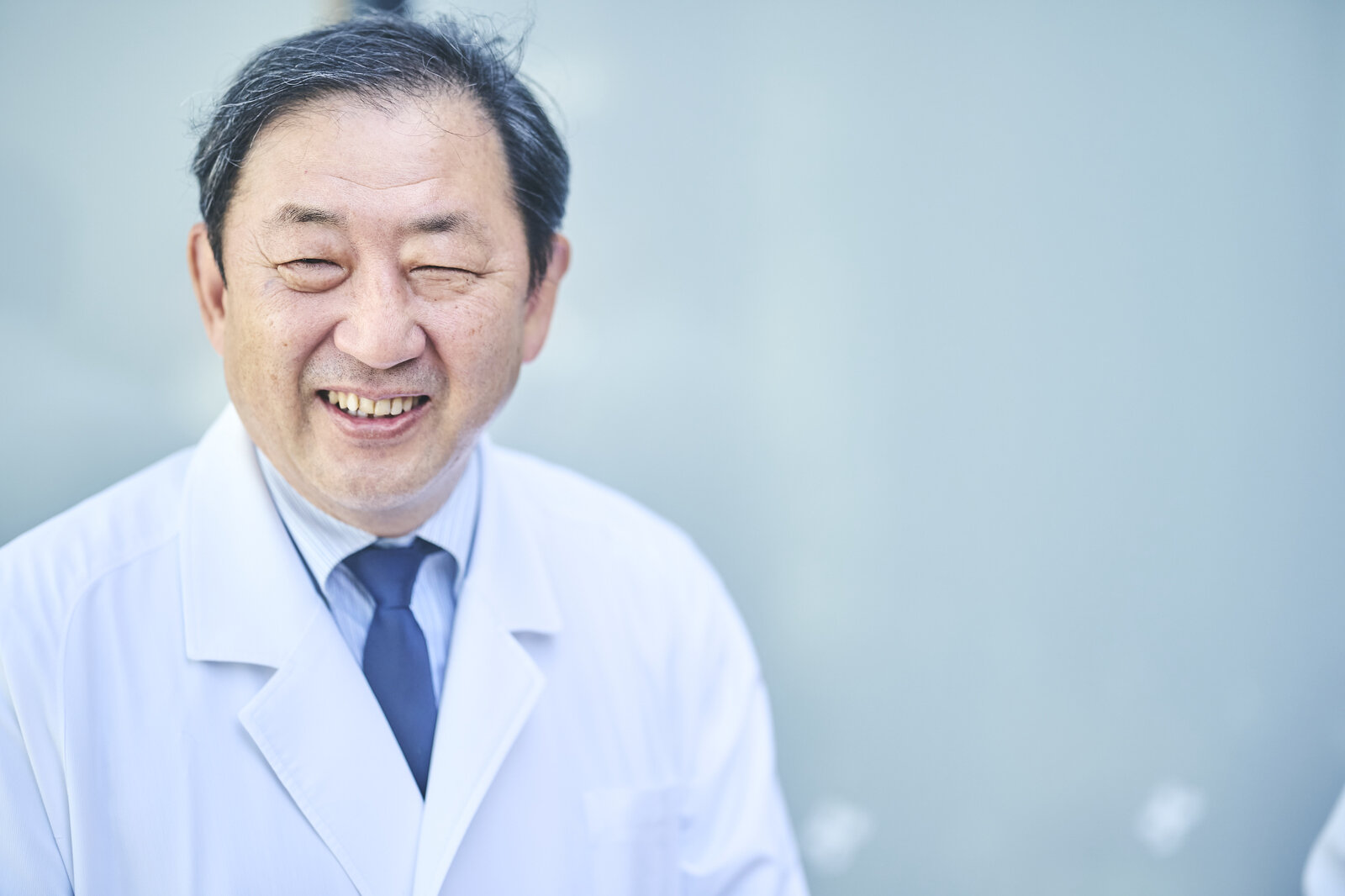
Normally, nurses work in staff stations until they are summoned by a patient.
In our hospital, however, we have many “mini nursing stations” in every wing, consisting of a chair and cart with electronic medical records. This arrangement allows staff to attend more closely to patients’ needs.
The idea was adopted by a hospital in Seattle that studied TPS and brought back to Japan by Iizuka Hospital in Fukuoka Prefecture. We also immediately borrowed it.
While this episode highlights the typical way that Toyota swiftly spreads good practices across organizations, it is still astonishing to see ideas making the round trip across the Pacific Ocean.
Two of Toyota’s other initiatives have also been adopted by the hospital: the Creative Idea Suggestion System, which encourages employees to propose workplace improvements, and QC circles, kaizen activities undertaken in small groups.
In 2024, these QC circle activities tackled a record-high 29 different areas. Obstetrics and gynecology nurse Ayaka Yonezu shared her experience.
Ayaka Yonezu, Nurse, Obstetrics and Gynecology
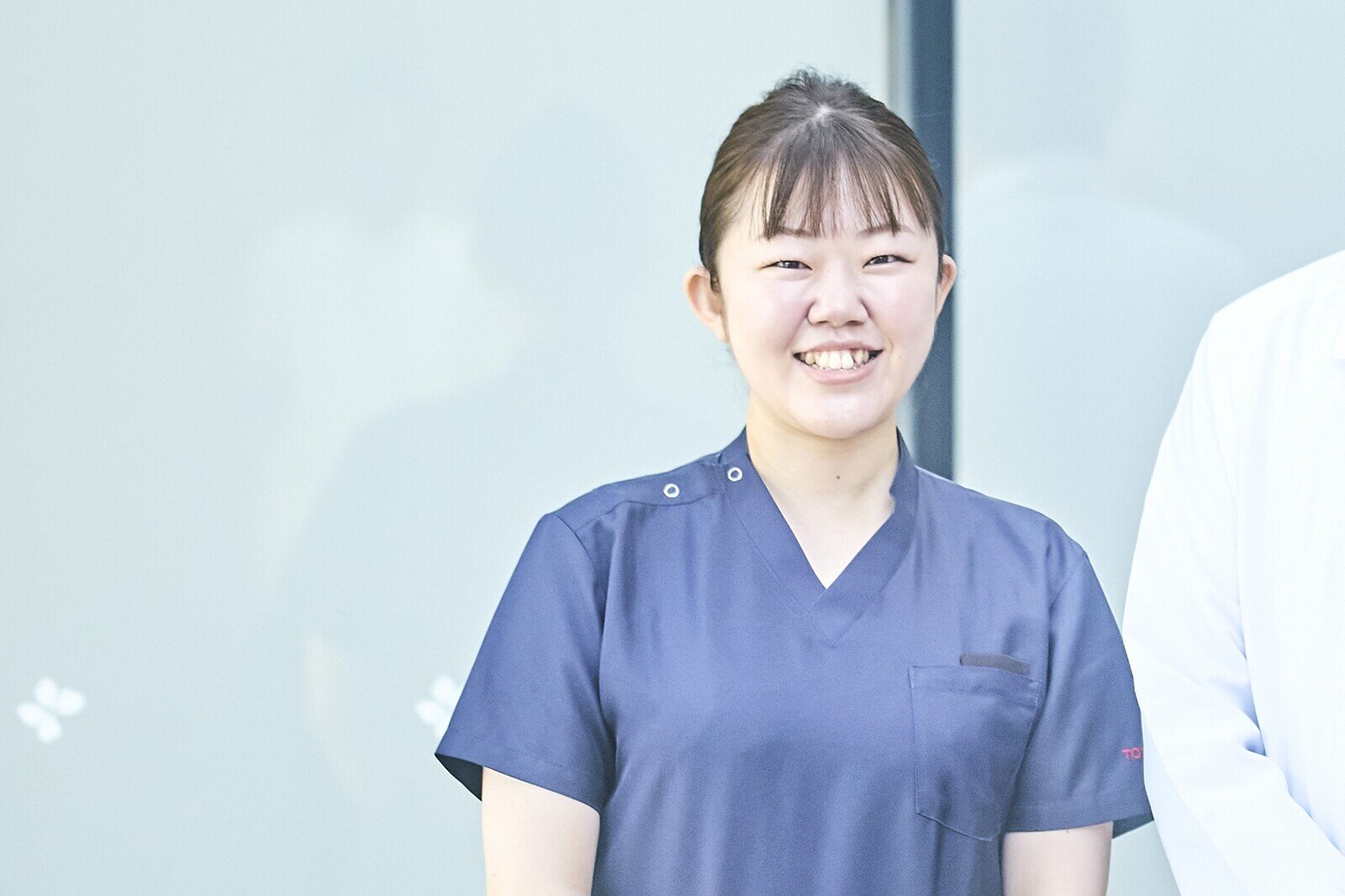
Childbirth, for example, requires not only the person who receives the baby, but also people to look after the newborn and care for the mother.
Since there are fewer midwives on the night shift, we worked across different sections and made it possible to obtain advice from nurses in the NICU (Neonatal Intensive Care Unit), who are qualified in neonatal resuscitation. This improvement gives patients peace of mind while also allowing staff to put their skills to use.
Another focal area for kaizen activities was reducing wait times, a common issue in large hospitals.
No doubt most readers have experienced a long stint in a hospital waiting room. At Toyota, revising every step of the process is steadily yielding results, offering much hope for the future.
Why Toyota remains committed to its hospital
This hospital is not only steeped in Toyota’s unique character but also has a long history.
Director Iwase
It was originally established in 1938, at the same time as the Honsha (then Koromo) Plant, as an on-site clinic. Instead of simply building a production plant, from the outset the company seems to have been conscious of protecting employee health.
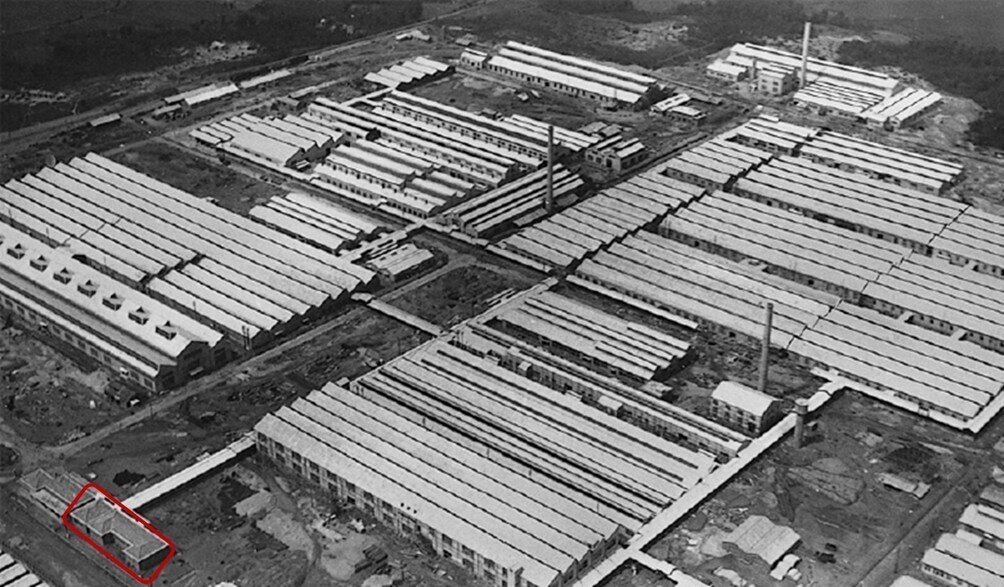
In the past, many hospitals in Japan were run by corporations. Recently, however, that number has declined, as operating hospitals increasingly became a loss-making enterprise, due to factors such as medical fee revisions, hefty capital investments, and the impact of working condition reforms.
Despite this, for Toyota, the hospital remains an important way of contributing to the local community. It has also set a goal of never declining treatment, accepting 9,212 ambulance visits last year.
Handling such high volumes sounds like a challenge, to say the least. We asked Director Iwase how the hospital manages it.
Director Iwase
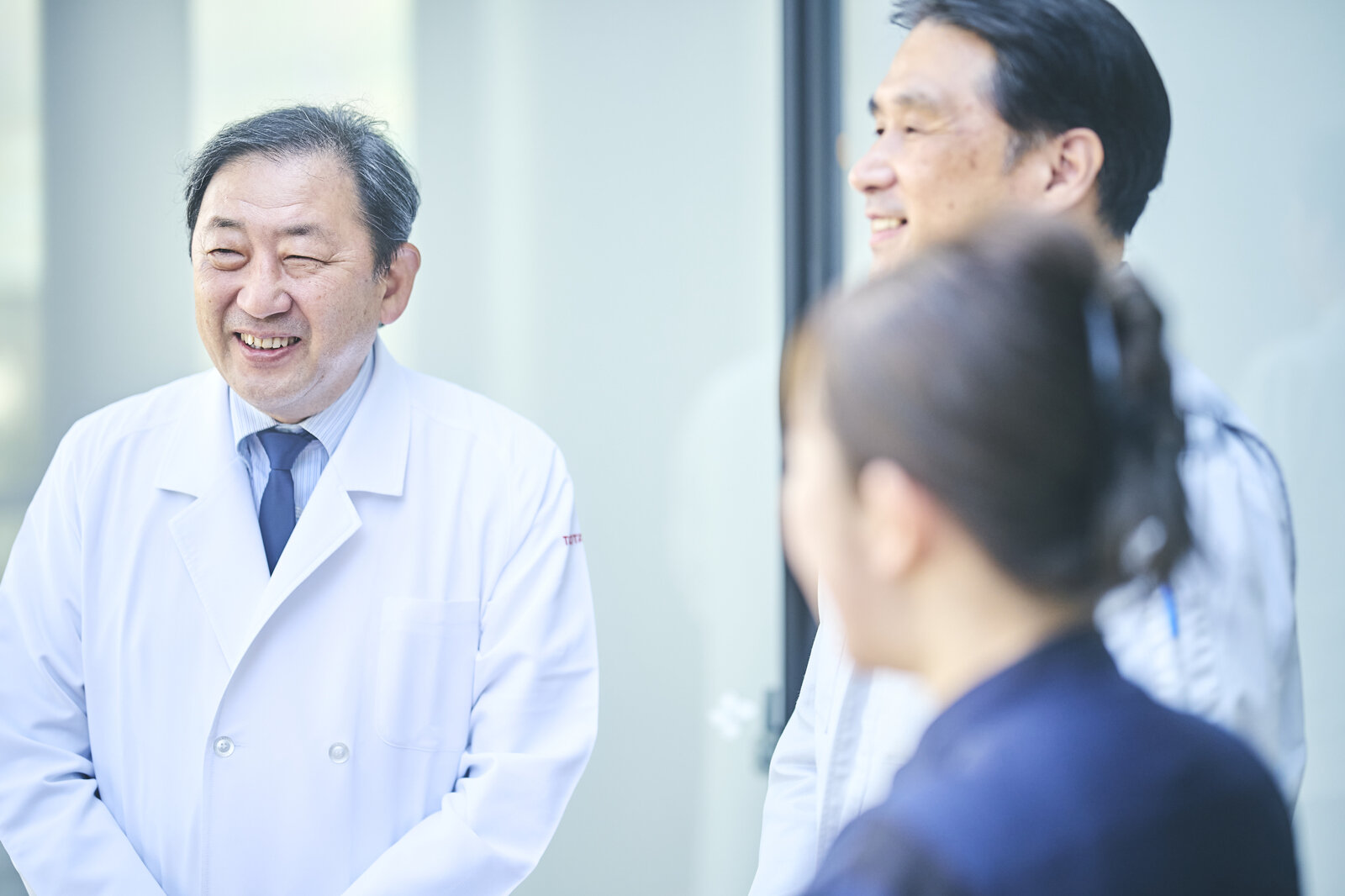
Our hospital is part of the region’s healthcare services, which means we coordinate with local medical facilities to try and maintain the health of the community.
We exchange information on availability and share expensive medical equipment. It’s about collaboration, not competition, which includes things like dividing up medical examinations. We are not rivals but rather partners with a shared vision.
The starting point of medical care is making patients happy. If we refuse to accept patients, their conditions will worsen, and they will lose trust in us. Although it becomes difficult at times of full capacity, we will keep striving to deliver a high level of care without turning anyone away.
Iwase says that his future goal for the hospital is “to help extend healthy lifespans by providing guidance in areas such as exercise and eating habits.”
There was one last question we really wanted to ask Akiba, the person who had led the hospital’s kaizen efforts: among all the white medical gowns and nursing uniforms, why did he continue to dress like a production plant worker?
“At Toyota, we have this idea of ‘continuous kaizen’—as long as I am working to make the job easier for my colleagues and improve healthcare in the community, I will keep wearing this uniform.”
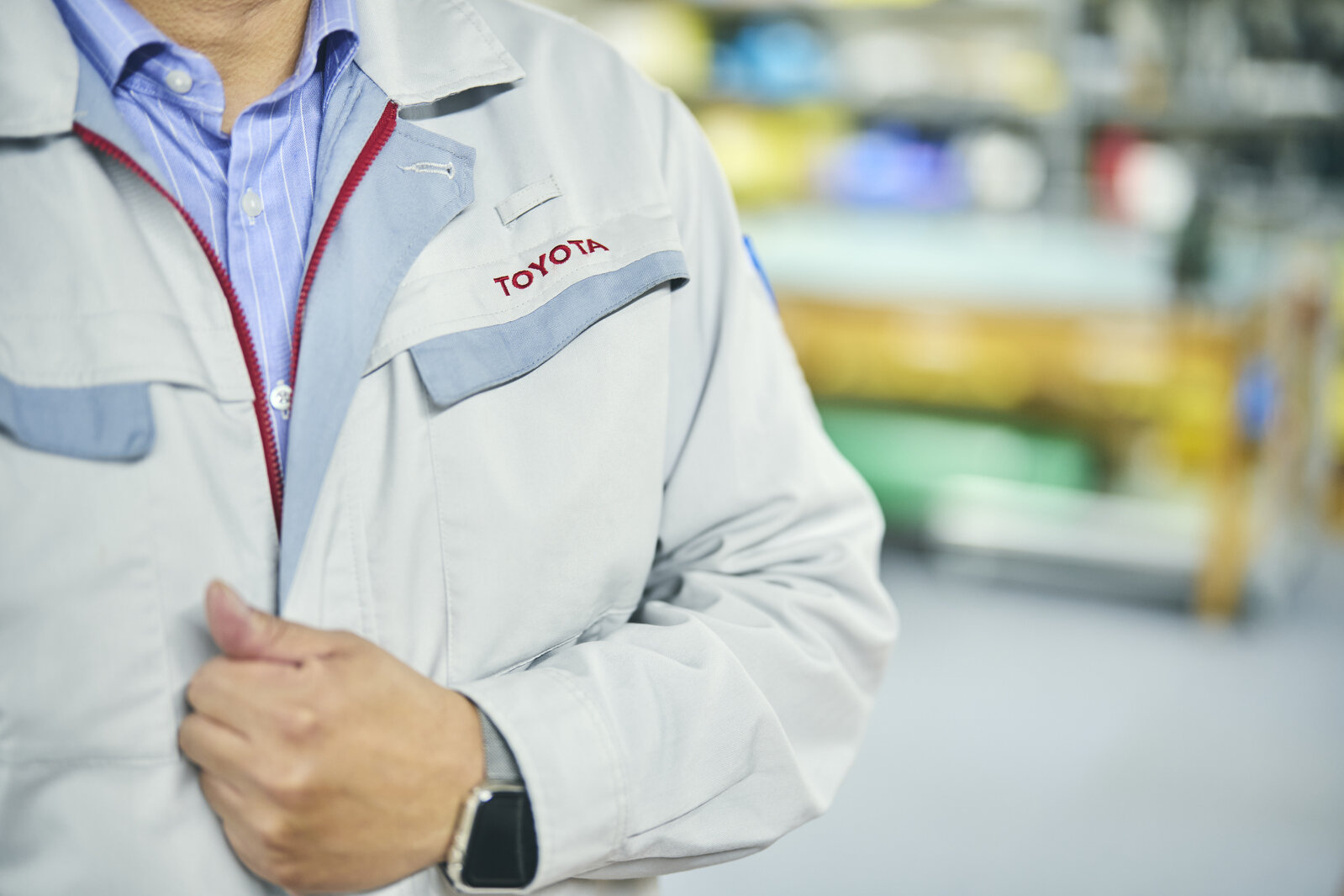
Visiting this hospital, you can sense a commitment to pursuing improvements for the benefit of others. Perhaps this, more than anything else, is what makes it a part of Toyota.